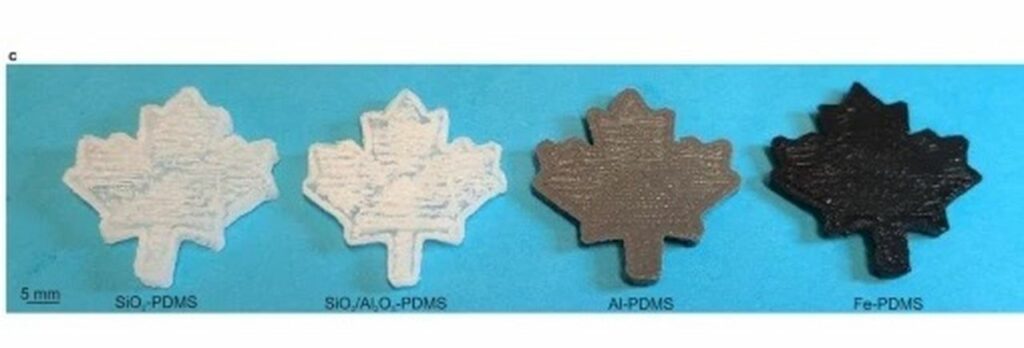
“Direct Sound Printing”, “DSP”, is an entirely new way to 3D print solid objects.
There are many 3D printing processes on the market, but all rely on these fundamental reactions:
- Thermal (FFF, PBF, EBM, etc.)
- Photoactivated (SLA, MSLA, DLP, Stereolithography, etc.)
- Kinetic (SPEE3D, friction, etc.)
There’s one more: sound.
As far as I know there is only one existing 3D printing process that uses sound (ultrasound, specifically), and that’s Fabrisonic. Their process uses ultrasonic waves to fuse metals together without the need for heat. However, that process is limited by the use of sheets and as a result is typically for making flat objects.
Now, researchers at Concordia University in Montreal have developed a sonochemical 3D printing process that has no equivalent. They call it “Direct Sound Printing”, or “DSP”.
The foundation of DSP is that it is possible to create a “cavitation” in a resin which can briefly experience tremendous thermal changes and pressures. The researchers state that temperatures can exceed 15,000K and 1000 bar, with cooling rates exceeding 10^12 K/s.
Let’s take a moment to think about what those figures mean. The temperature alone is incredibly hot. Consider that the surface of the sun is “only” 5778K. This is three times that heat! The pressure is 1000X that of atmospheric pressure, and the cooling rate indicates that these conditions would last only instantaneously.

The researchers built a sonic apparatus that creates an ultrasonic field, and within that field is a focal point that can generate such a cavitation. The mechanism was designed to precisely move the focal point of the ultrasonic field through 3D space within a vat of resin.
As the focal point passes through the resin, it solidifies the material through thermal and pressure effects. By starting at the bottom, it’s possible to gradually build up an object by solidifying material on top of previously solidified material, voxel by voxel.
They say the power required for the DSP system when printing is as low as only 20W, far less than that required by FFF systems, and even less than MSLA.
The researchers found they could control the resolution of the system to be able to create gaps in solid models of only 0.025mm, which matches the best typical resolution of today’s 3D printers. Minimum feature sizes were 0.280mm.
Control of the system is managed by manipulating the characteristics of the ultrasonic field, and researchers indicate they have an extremely wide range of possibilities available.
The implication here is that DSP could handle a much, much wider range of materials than can be used with conventional 3D printing processes. They explain:
“Despite recent significant developments in additive manufacturing (AM) technologies, from printing materials to processes, light and heat are still the only energy sources used in AM to drive chemical reactions or physical transformations of polymers. Therefore, materials in AM processes are limited to photo-sensitive resins, like in stereolithography (SLA) or direct laser writing (DLW), and thermoplastic filaments or powders, like in fused deposition modeling (FDM) or selective laser sintering (SLS). Parameters controlling the chemical interactions are defined by the amount of energy per molecule, interaction time and pressure. Existing AM energy sources, light and heat, do not utilize all the potential of the chemistry in terms of the control parameters while sonochemistry pushes these parameters to their limits.”
The point out one example as being heat-curing thermoset polymers, which cannot be 3D printed due to the inability of current processes to produce precise spots of high heat and rapid cooling.
Another interesting effect is that opaque resins can be 3D printed: sound waves travel through all, whereas they pose challenges for current optical printing processes. This could allow for many more complex resin mixes containing stronger composite materials.
This could be a significant breakthrough for the industry, as if DSP were commercialized, we could see entry of many more materials that are currently non-printable.
Via Nature