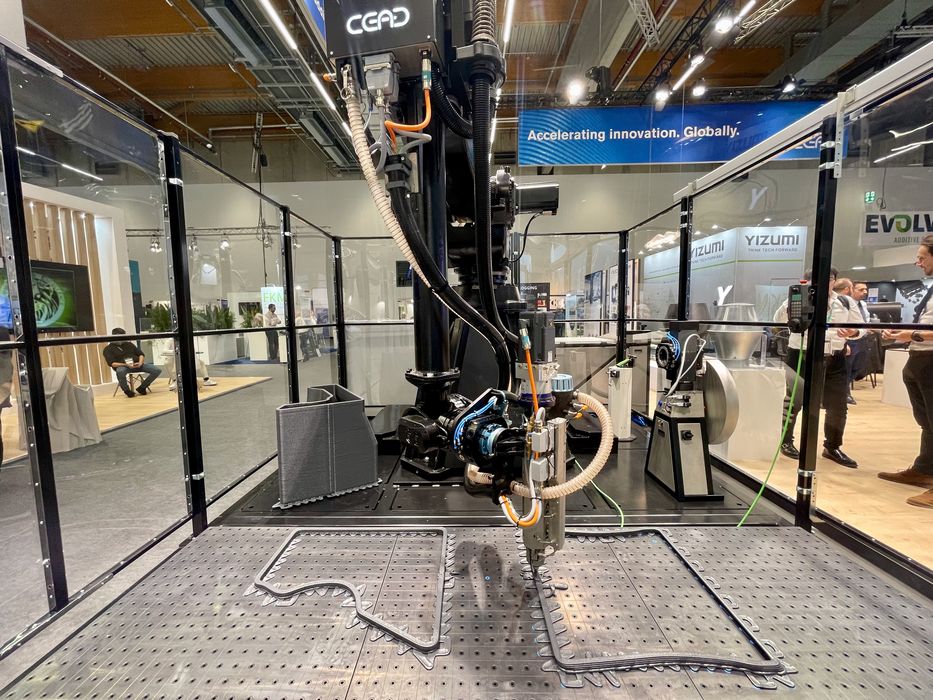
I had an interesting visit with CEAD to learn about their massive robotic 3D printing system.
The Netherlands-based company produces several large-scale extrusion-powered 3D printers, both robotic and gantry style. They’ve been in operation since 2014, and have produced many solutions for industry. Their largest deployments have build volumes in the several meter range, and one customer even 3D printed a 12m boat, which took two weeks to complete.
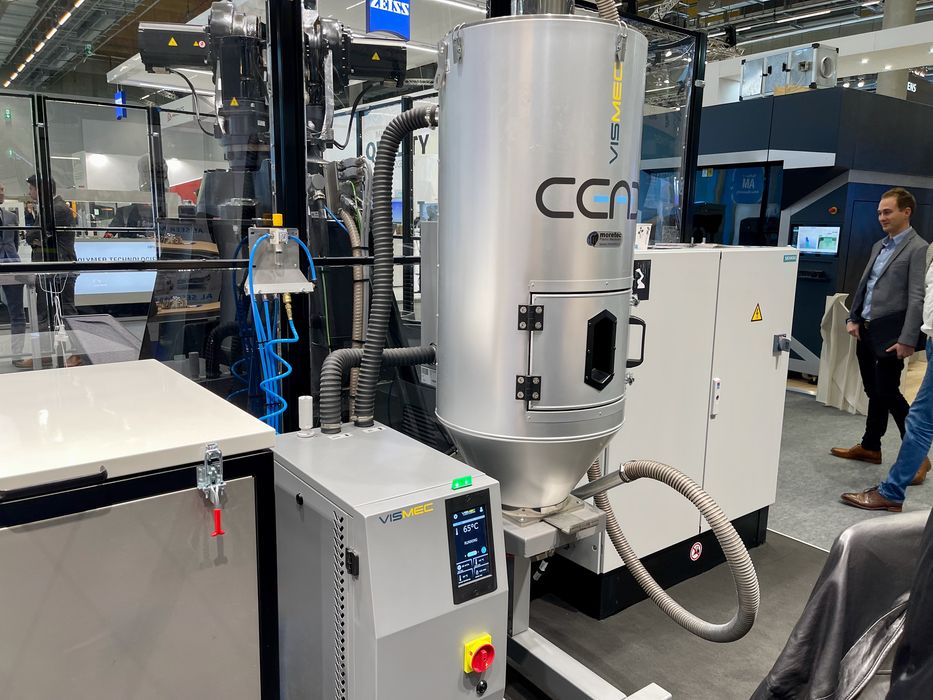
The machine uses inexpensive polymer pellets as material, which are stored and dried in the hopper system seen here.
You might think their technology is simply a pellet-fed polymer extruder on a robotic arm, but it’s actually far more complex than that.
For one thing, their robotic system can print with continuous carbon fiber, something very few 3D printers can do. How is it done? They have an ingenious solution: after a layer is printed, a robotic arm lays down a carbon fiber tape on top, as you can see in the above image. This enables their prints to be far stronger than mere polymer extrusions.
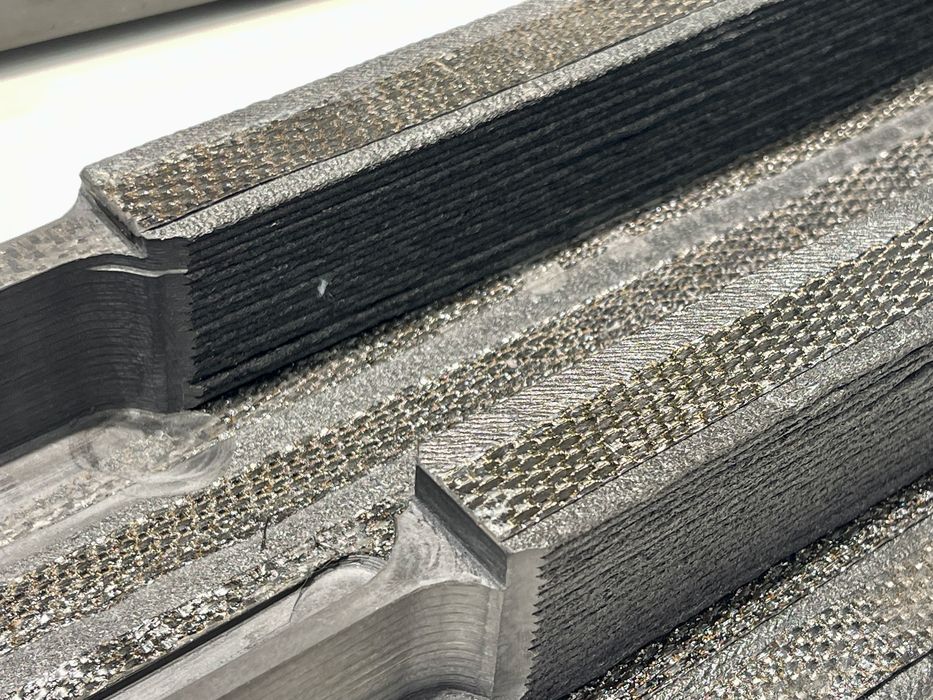
You’ll also notice in the image that some of the surfaces are quite smooth. That’s very different from the rather fat extrusion lines delivered by the toolhead. This is because their robotic solution allows for the use of multiple toolheads. It’s possible for the machine to use a CNC milling head to smooth out portions of the printed layers during jobs. This allows them to produce very smooth and strong “final” parts.
One of the big issues with large-format polymer 3D printing is bed adhesion. The warping forces amplify over longer lengths, and that’s exacerbated by the huge prints made in CEAD machines.
It turns out CEAD has an incredibly ingenious method of bed adhesion. Here’s the print surface, and you’ll note a number of regularly-spaced holes.
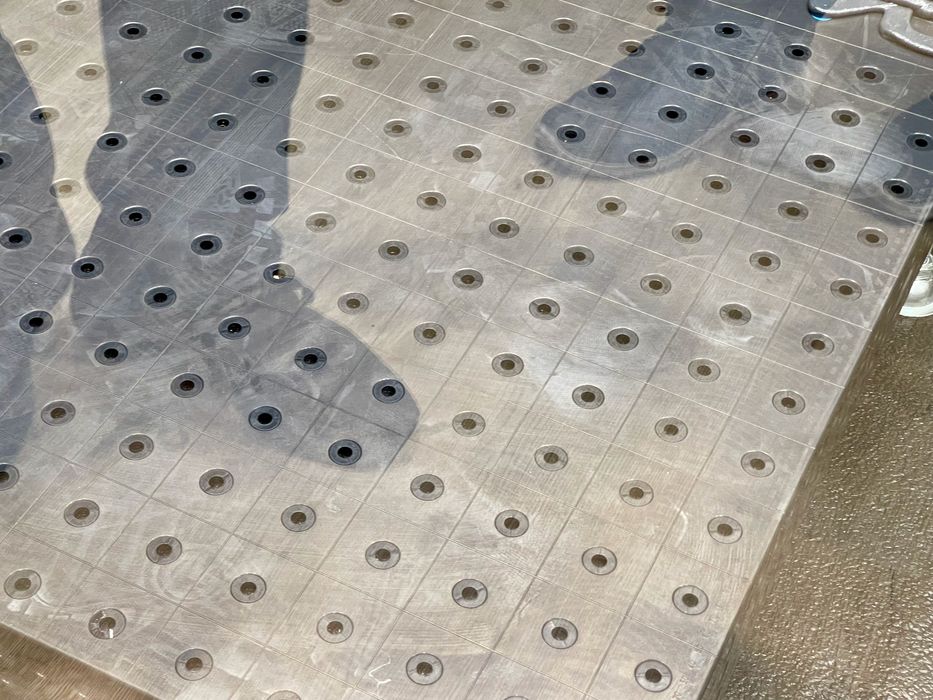
If you think about it, the fat extrusion would leak into these holes and fix the print to the plate. However, it would be very difficult to lift the print off the plate afterwards because those leakages would be solid.
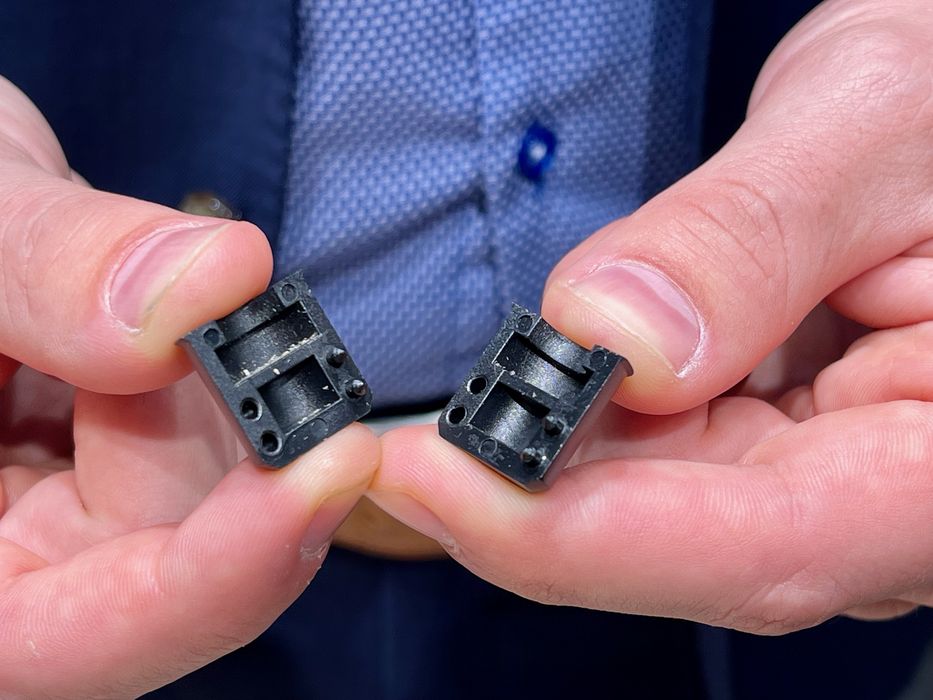
CEAD’s solution is to insert these split-plugs into each hole before the print job begins. The plug creates a cavity with a tight throat, and you can imagine how material would flow into that cavity to create a very secure linkage. Their software has a special raft generator for this purpose.
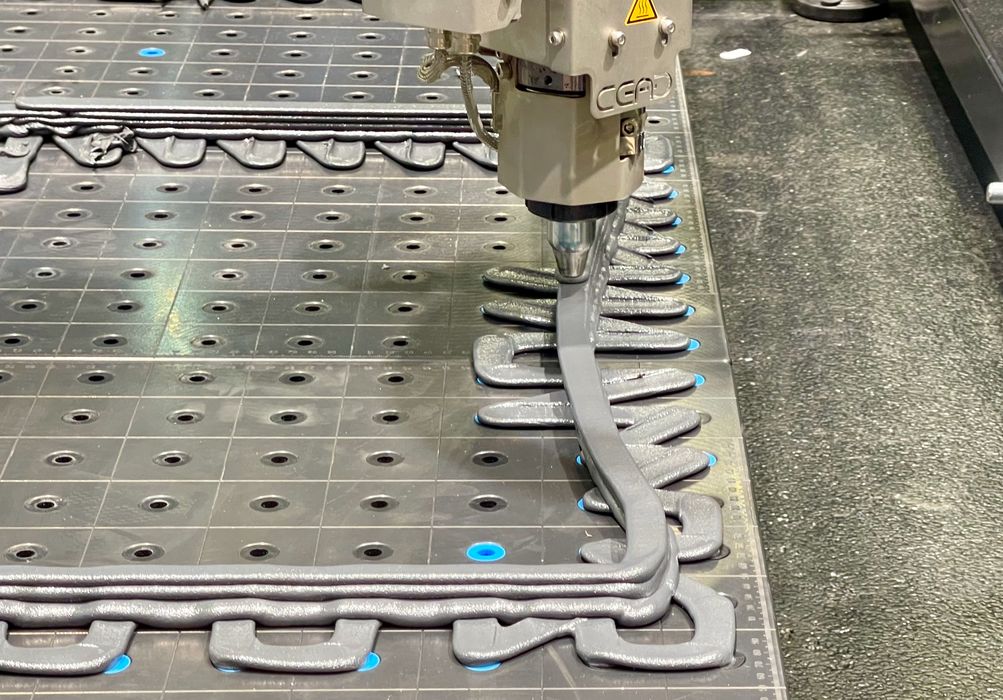
After the job completes, the print can be simply lifted up because the plugs are not attached to the plate: they just sit in the holes. Then the plugs fall off because there’s nothing holding the two halves together. The leftover pegs on the bottom can be milled or broken off. Ingenious!
One of the big concerns with larger prints is the cost of materials, but CEAD assured us that they have this under control. They explained that materials can be as cheap as €6 (US$8.75) per kg, which is quite a bit less expensive than filament. So far they have certified around 300 different materials for use in their equipment.
A new feature they’ve just unleashed is data logging. The idea is to collect a vast amount of sensor information during print jobs for later analysis. For example, the printed part might be compared to the original CAD design to ensure its within tolerances. Their plan is to eventually provide some type of certification for parts using this data.
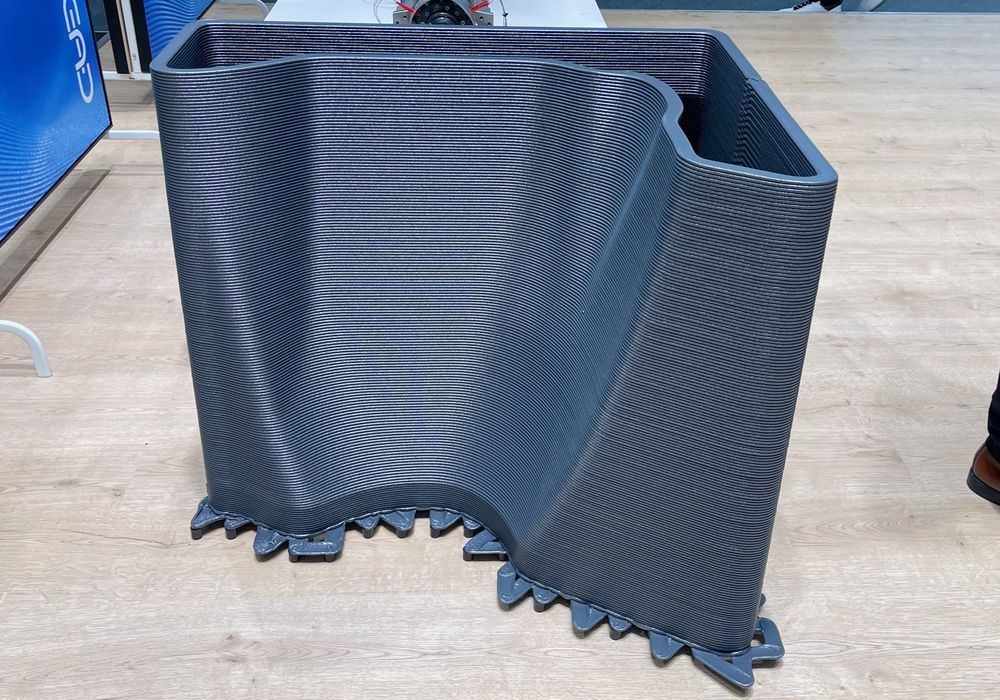
The CEAD technology seems to be quite advanced and growing in popularity. CEAD told us of several use cases, including the production of large molds. They even have a customer in Florida that’s 3D printing furniture with the system.
It seems that large format robotic 3D printing has matured considerably.
Via CEAD