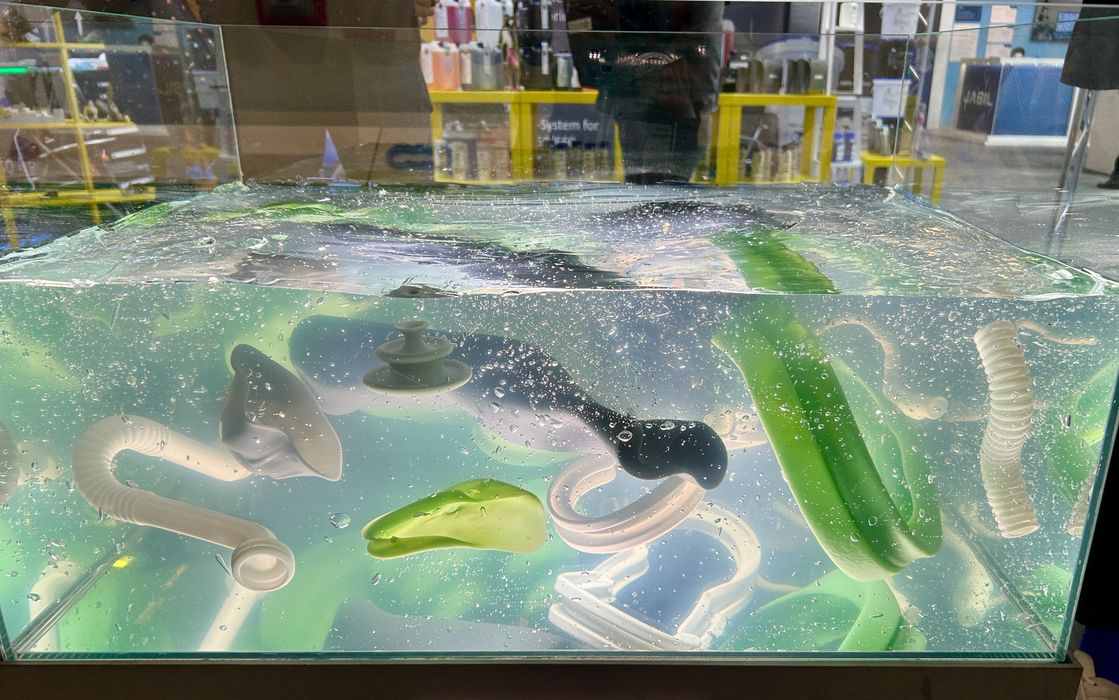
I had the chance to see RLP’s amazing liquid 3D prints.
RLP, a Boston-based company, is an acronym for “Rapid Liquid Printing”, and that’s exactly what they do. Their process involves 3D printing within a large vat of transparent gel.
They started work on this technology at MIT in 2015, and then left the institution in 2020 to go “full time” on the project.
The process involves moving a slender syringe through the gel in three dimensions while extruding material. As the syringe moves, the gel parts and then closes together afterwards. However, the gel is thick enough to hold stationary any extrusions from the nozzle.
The extrusion system somewhat resembles a common FFF desktop 3D printer in that there is a cartesian gantry to move the syringe through the gel. Like FFF, both the speed of toolhead movement and amount of extrusion can be controlled. This means they can produce thin extrusions, or thicker if slowed down and pressure increased.
The material used in the RLP process is basically epoxy resins. The toolhead has a mixing nozzle that exposes the two components, which then slowly cure after extrusion.
The resin we saw was said to cure completely in about 90 minutes after extrusion.
The interesting part is the gel medium. It’s completely transparent so you can see what’s going on, just like a desktop FFF 3D printer. However, the nozzle does not need to operate in horizontal layers and has complete freedom of movement of movement.
RLP told us it was even possible to have multi-material prints by using two toolheads within the same print job, each with a different resin.
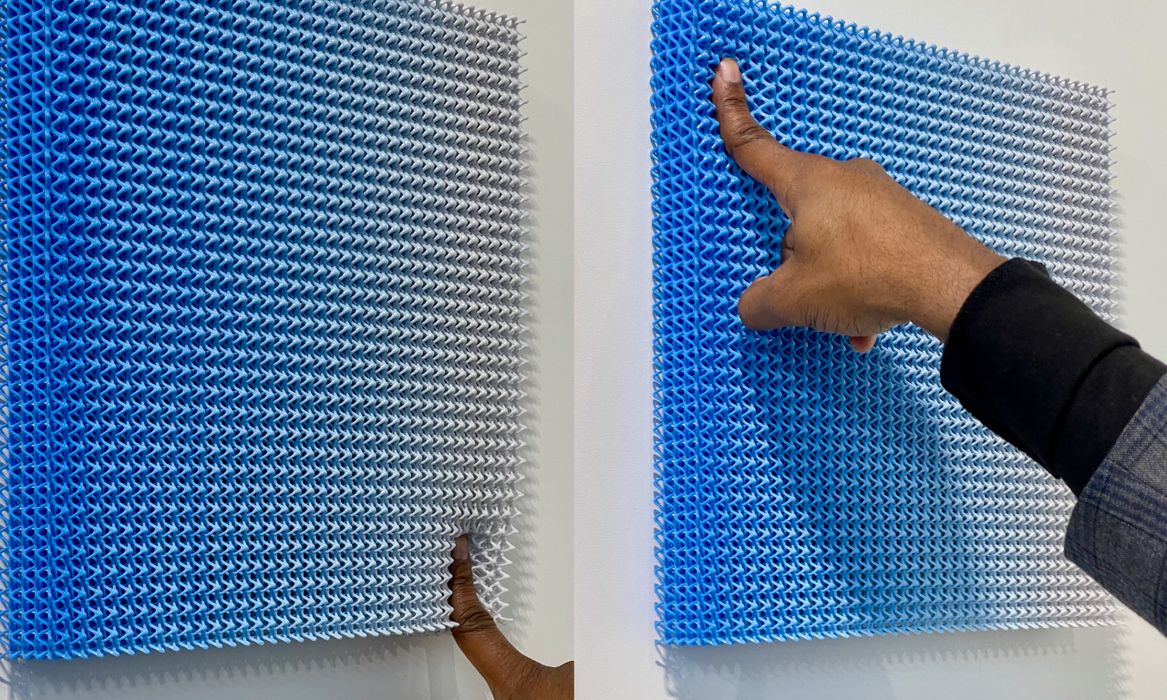
By varying the extrusion thickness, it’s easiy possible to generate shapes with a gradient of hard to soft regions. Here we see a lattice structure printed with hard areas at the top and software at the bottom.
Support material is non-existent in the RLP process: the gel simply holds up the print, and provides a perfectly smooth surface for doing so. There are absolutely no “support bumps” that mess up surface quality on these prints.
When jobs are complete the post processing steps are perhaps the easiest I’ve ever seen with 3D printing: you reach into the gel and pull out the print. The print will have a bit of gel left on its surface crevices, so you just wash it off with plain water. The waste water is perfectly safe, and can go down the drain normally — no need for toxic disposal here.
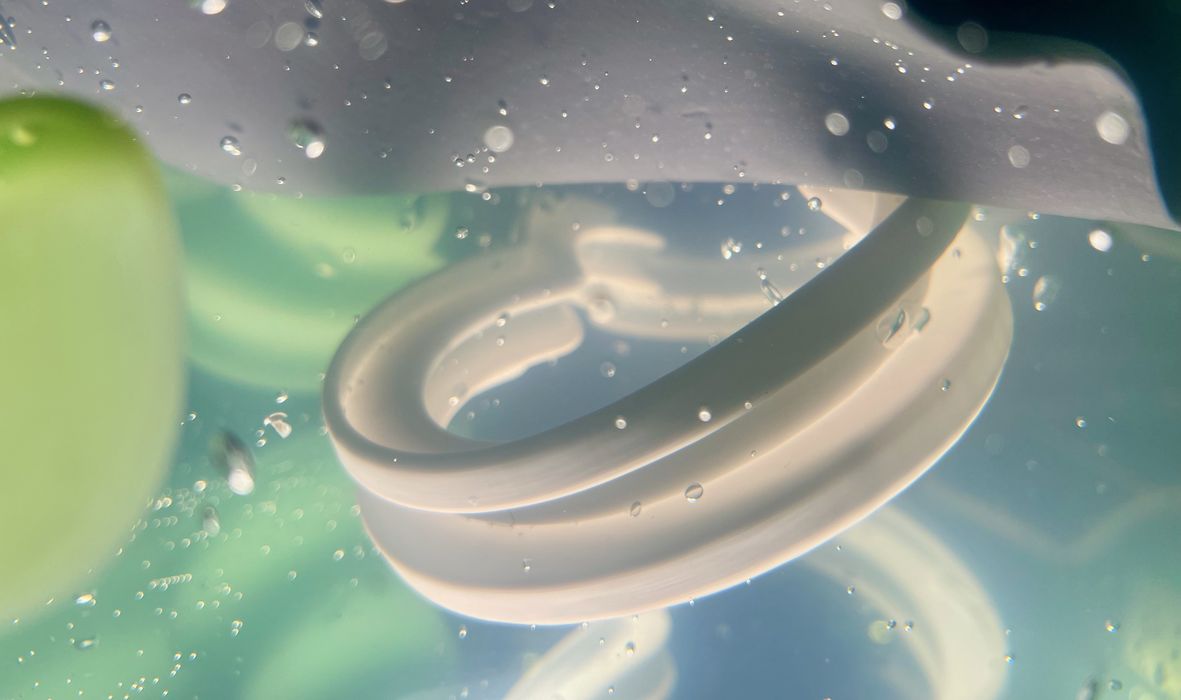
The results are pretty amazing. We saw multiple prints, mostly flexible materials, each having outstanding surface quality. RLP was also able to manage color swaps during printing, but I’m not sure how they did that.
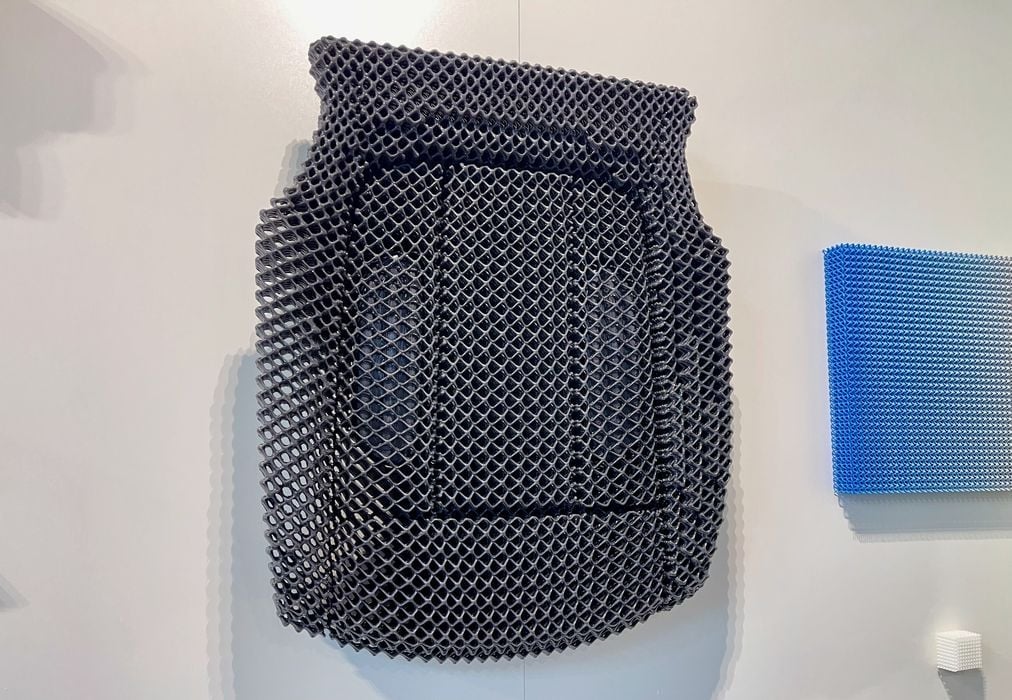
The process can be relatively quick. This life-size car seat was apparently completely printed — including post processing — in only five hours. That is surely competitive with some of the other industrial 3D printers we’ve seen elsewhere, but this one require basically no post processing.
For now RLP is operating the technology as a service. They’re so new it’s not yet clear which industrial application will make the most benefit, so they’re observing the orders to learn more about how people will use this amazing 3D printing process.
Via RLP