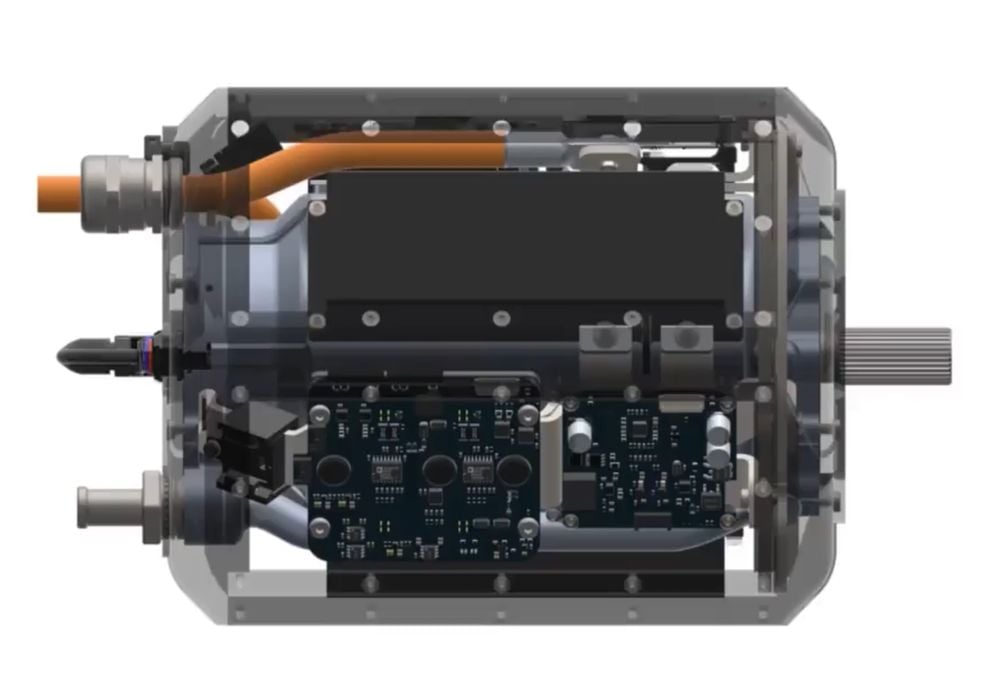
A startup company has leveraged copper 3D printing technology to produce a much more powerful electric engine.
H3X, based in Denver, the company develops advanced electric propulsion systems for aircraft. This is a monstrous challenge for science and industry, as we will have to switch aircraft from polluting fossil fuels to electric alternatives at some point in the relatively near future.
Unfortunately today’s technology isn’t suitable. The combination of battery and motor weight simply don’t allow for the production of even medium-range commuter aircraft. The more range required, the more batteries must be on board, and that increases the weight. At some point it’s essentially impractical to consider electric propulsion in this scenario.
There are two solutions, of course. One could increase battery energy density, and that would mean fewer batteries need be carried, reducing weight. There are a ton of companies working on this issue, and several are using 3D print technology to do so, including Sakuú.
The other solution is to make the motor more efficient, and that’s the strategy of H3X.
The key to efficiency in an electric motor is heat management. As energy levels increase, so does heat, and if thresholds are exceeded, the motor can fail and be permanently damaged.
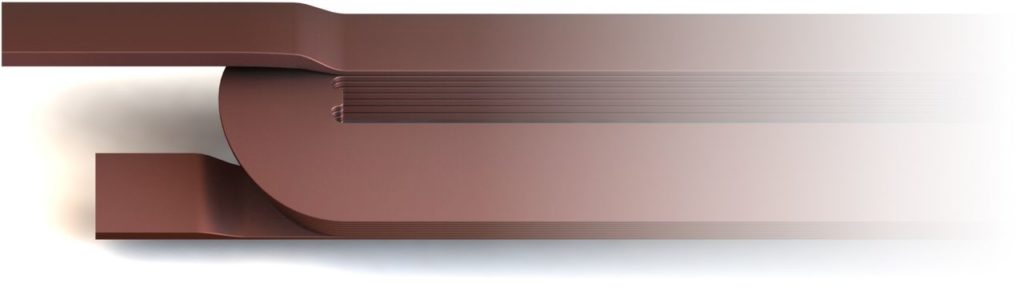
H3X took this up as a design challenge and realized they could 3D print internal motor components in copper with complex designs. These structures were able to pull heat out of the motor at a far greater efficiency than using conventionally designed and manufactured parts.
H3X explains the design:
“H3X has developed a new kind of stator coil that is additively manufactured using pure copper with >93% IACS conductivity. Our AMcoils achieve >70% copper fill factor in the HPDM-250 and offer a 40% improvement over conventional windings in terms of maximum continuous current density.”
This allows the motor to handle higher power levels, and thus be more efficient.
The result is a motor that is apparently 3X more efficient than competing electric motors when measuring the power to weight ratio. While today’s “best in class” motors achieve 3-4 kW/kg, H3X’s HPDM-250 motor can achieve 13 kW/kg — continuously!
H3X explains:
“The HPDM-250 is optimized entirely for power density and efficiency. It features the highest level of integration on the market, made possible by our holistic design methodologies rooted in first principles and multidisciplinary expertise in power electronics and electric machines.”
The specific efficiency of the HPDM-250 is notable, because it could enable the production of true, electric airliners. H3X explains:
“At 13 kW/kg continuous, the HPDM-250 exceeds ARPA-E’s requirements and is at least 3X better than current systems. It is a step change in electric propulsion technology and removes one of the main barriers blocking widespread commercialization of electric aircraft.”
H3X expects their motor to be used in any application requiring lightweight electric motors. This ranges well beyond aircraft, and could also considered for UAVs, boating, automotive and even military applications. They expect the HPDM-250 to be used specifically for “Large commercial electrified aircraft for short-haul flights less than 1000 miles (1600km).”
This is an incredible development that could shape our future in many ways, if successfully commercialized by H3X.
It is also an example of how 3D print technology can dramatically change a design that’s been most the same for decades. In many ways our engineers and designers have long been prisoners in the jail of traditional design tools and techniques.
Additive techniques are the jailbreak.
Via H3X