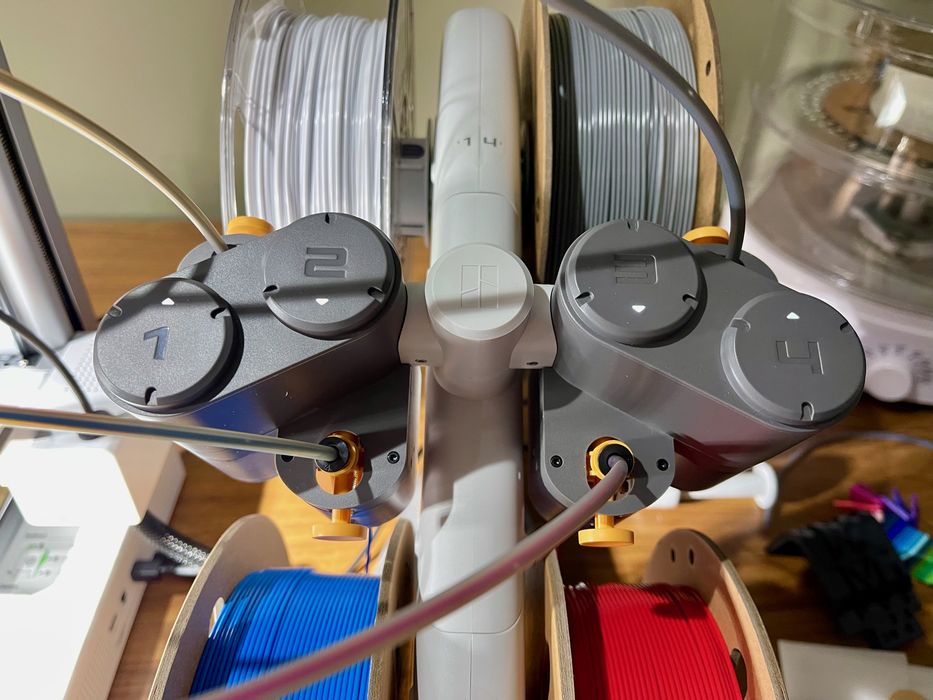
Our review of the Bambu Lab mini A1 continues with a look at operations.
This is part three of a four part series, please read parts one, two and four.
Bambu Lab A1 mini Operations
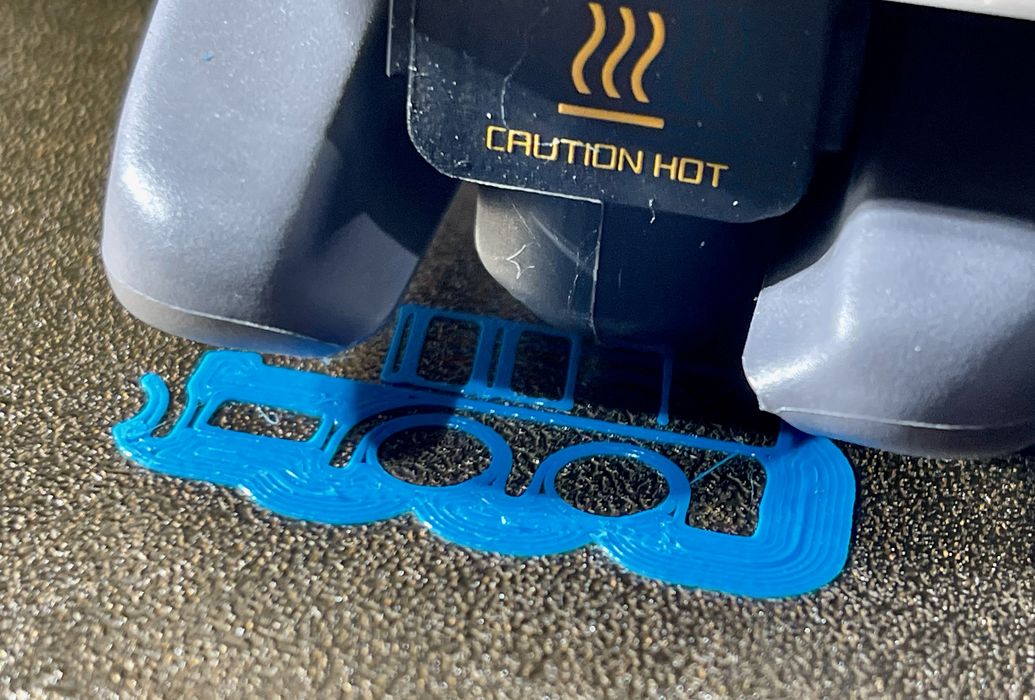
Operating the A1 mini is a huge pleasure; it’s so easy to perform almost every operation, even complex actions that involve multiple steps.
Printing can be done from the machine’s touchscreen, the mobile app, or the desktop app. I usually used the desktop app because it was convenient: slice and print from the desktop.
Once jobs are sent to the A1 mini, they stay in the machine’s memory and can be easily reprinted from the touchscreen. I’m not sure what happens when that storage gets full, but I’m nowhere near that yet.
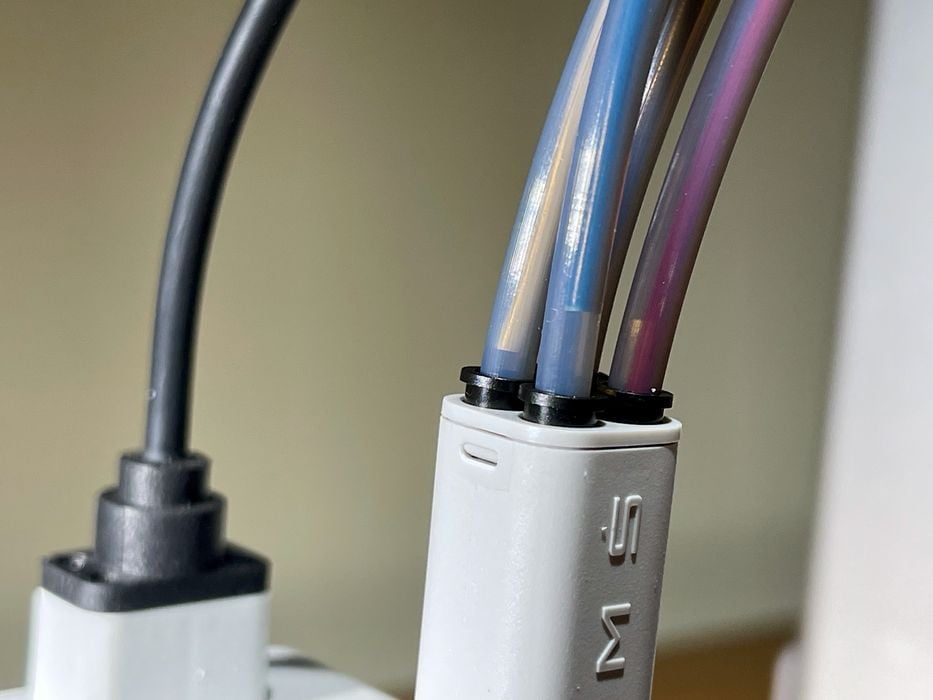
Here we see how the A1 mini positions the filaments. The AMS motor positions the filament ends just outside of the input ports. When activated, it’s pushed into the extruder, where the extruder motor grabs it and pushes it into the hot end.
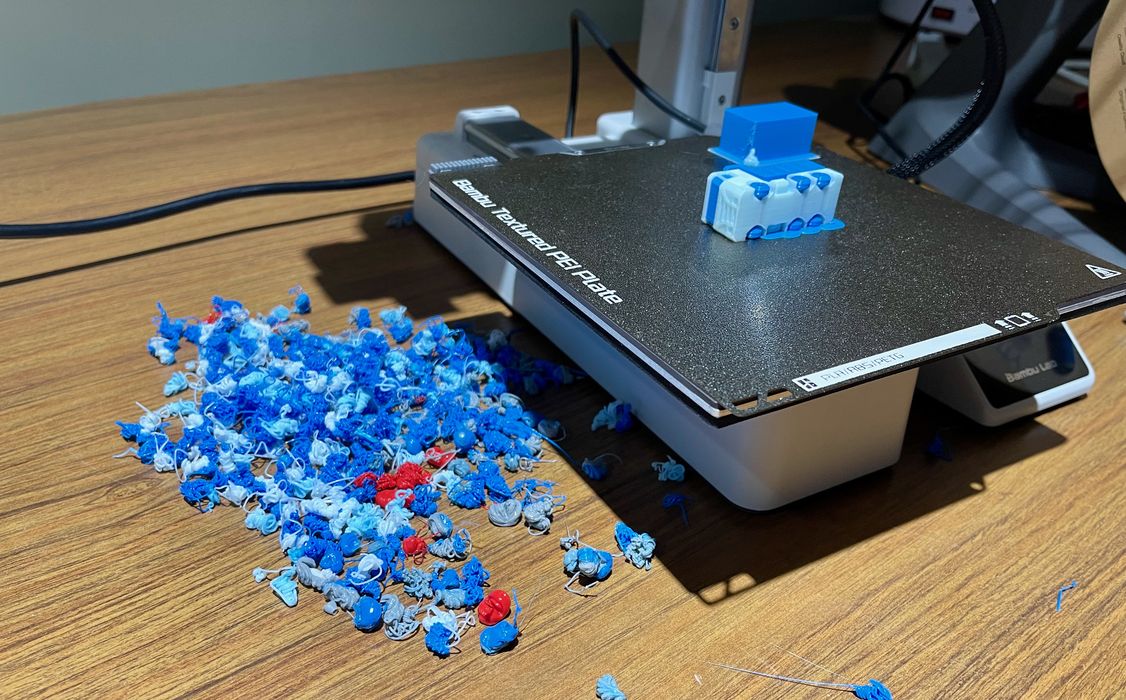
It’s time to talk about the “poop”. When the material is changed, the nozzle must be purged of the previous color, otherwise you get weird color mixes. While other systems perform a lengthy extrusion into a purge block, the A1 mini does something quite different.
The swap sequence involves sliding the X-axis to the right, which pushes a blade that cuts the filament! This allows the AMS to pull back the first filament to the position above.
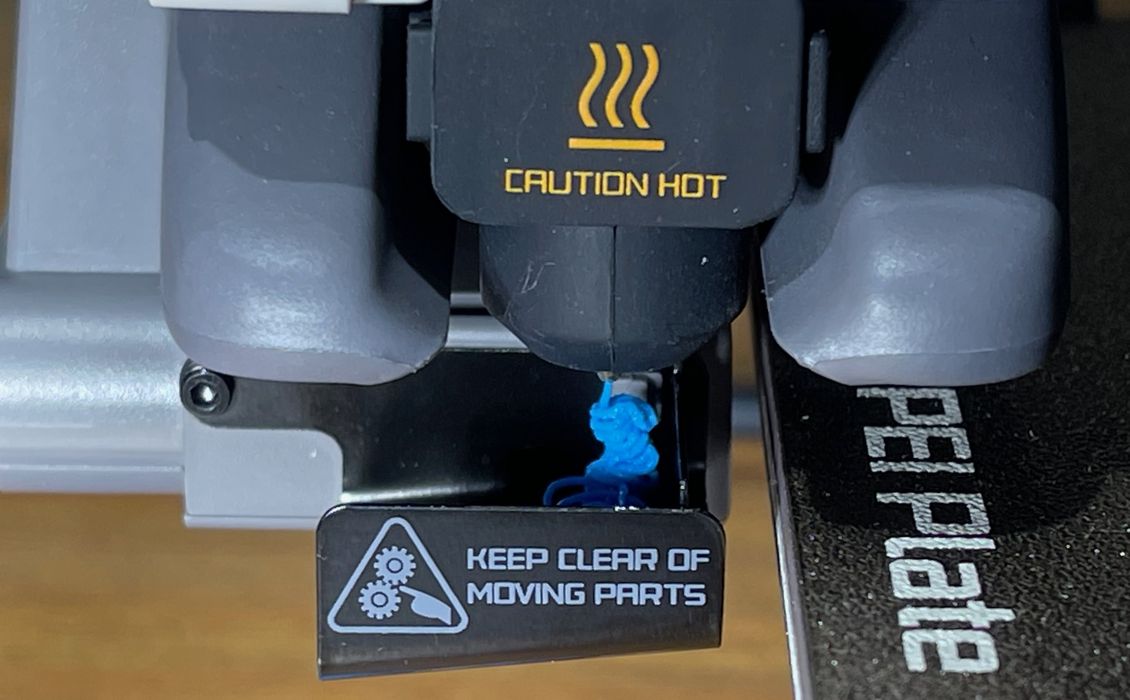
Then the AMS pushes the new filament into the extruder, where it performs a purge. This lands in the ejector, as seen here. Once complete, the sweeper pushes it out to the side.

For a job using multiple colors, you quickly end up with a pile of filament “poop”. After several jobs the poop can really pile up. You could consider this approach being wasteful, but other systems use about the same amount but it is put into a purge block instead. Note that the A1 mini can also use purge blocks, but they’re not as big. I guess this is the cost of making multimaterial prints.
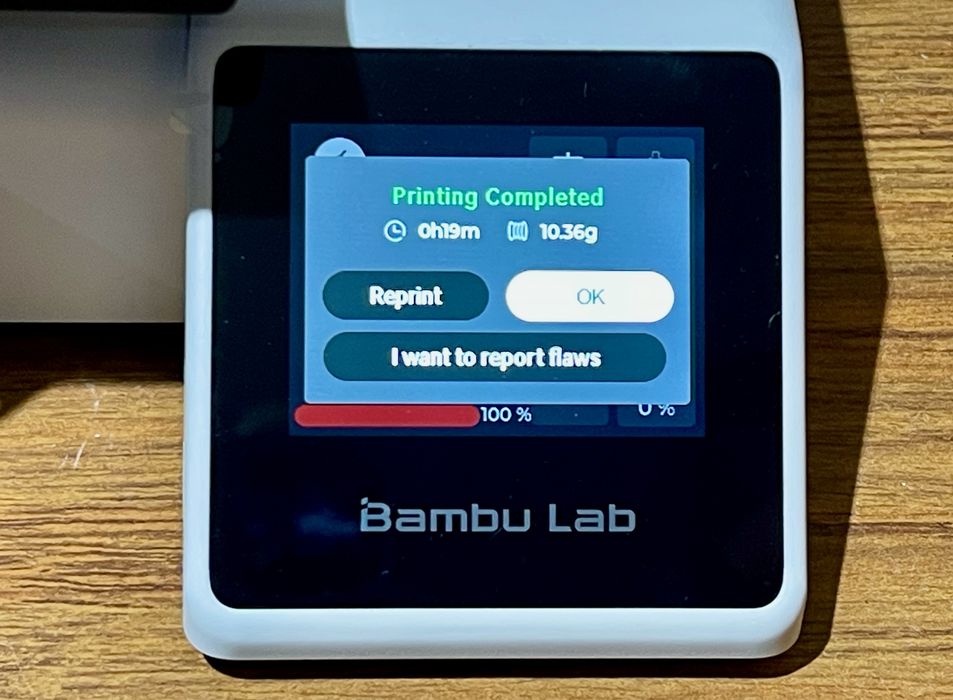
When jobs are complete, the machine asks for feedback, always a good thing. If there’s a problem it can be reported and the job can be reprinted.
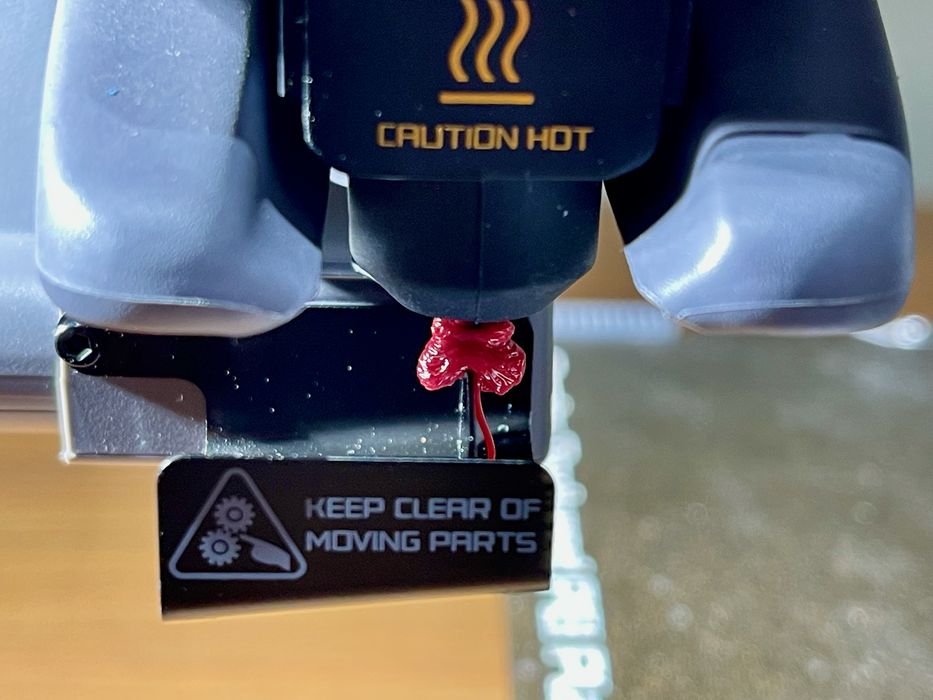
I had one problem with the poop process. Here you can see that the purging is being deposited on top of the sweeper instead of to the left. This was quite a problem because it meant the poop would land randomly about the print area. Sometimes I would find them attached to a print, left beside the printer, on the floor or sometimes even where they were supposed to go.
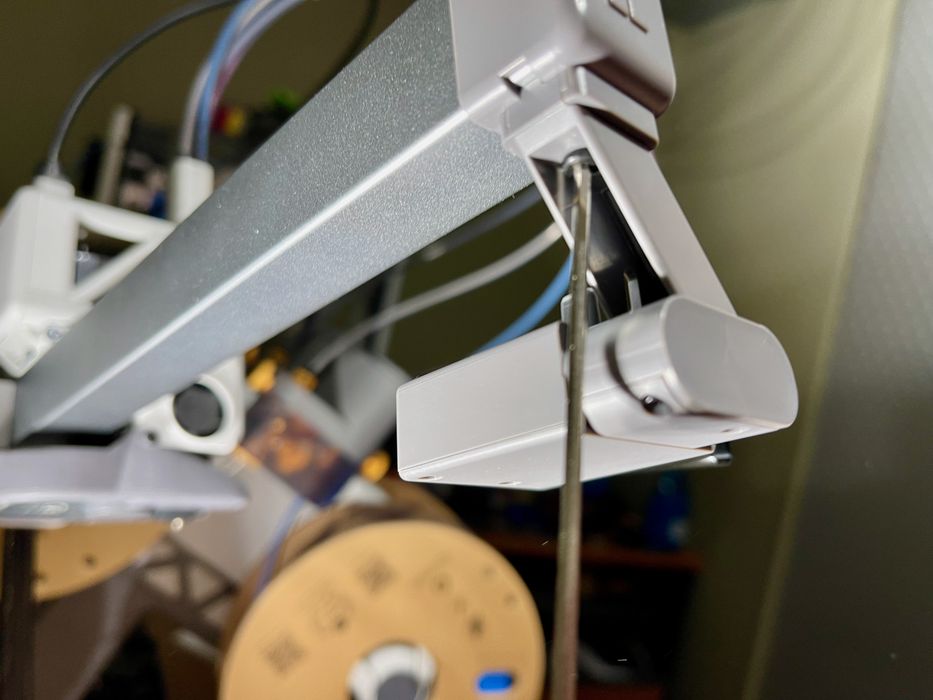
After discussion with Bambu Labs, the recommendation was to adjust the ejector mounting, which I did here.
This partially corrected the problem, but in the end I actually bent the sweeper arm slightly to ensure it caught the purges properly each time. After that there were no ejection issues.
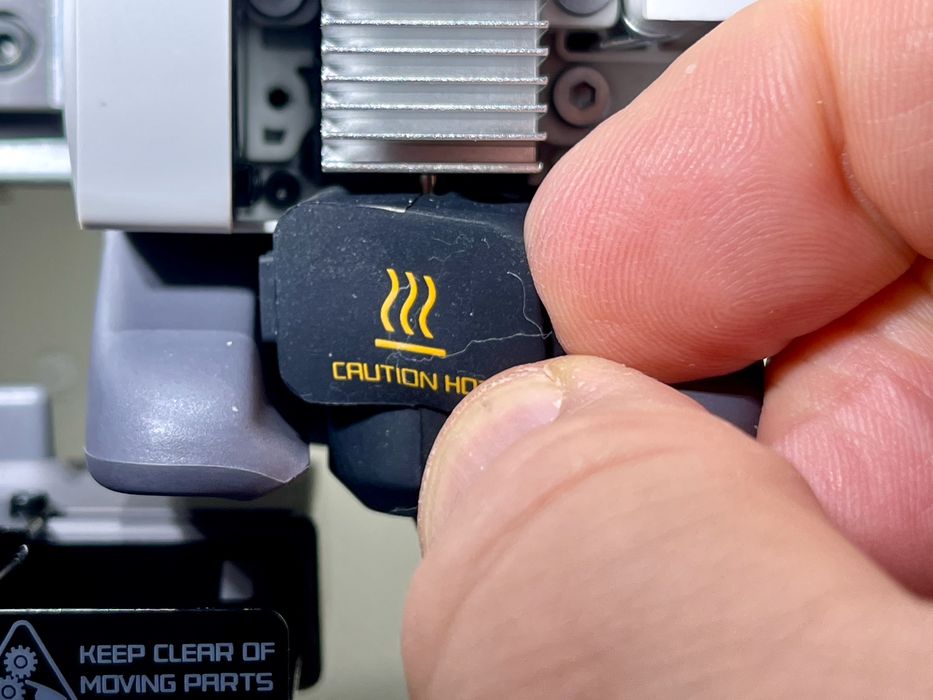
Quick nozzle swaps were the next thing to test, and I was interested to see how this works. The first step is to remove the silicone insulating cover off the in-place nozzle.
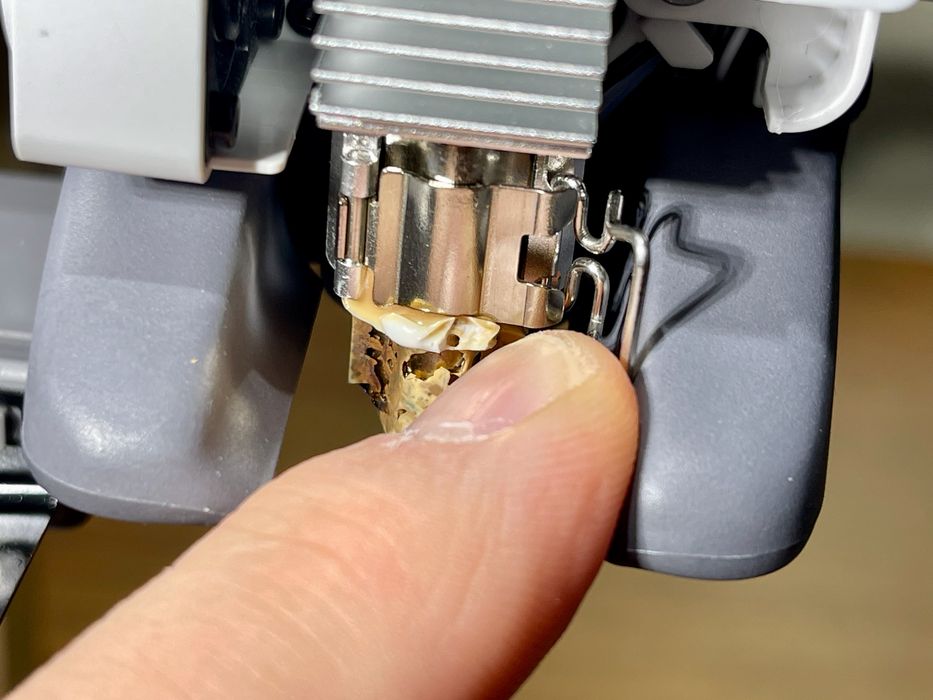
Then there’s a metal latch that must be flipped. Note that it could be pretty hot, so use a screwdriver just in case.
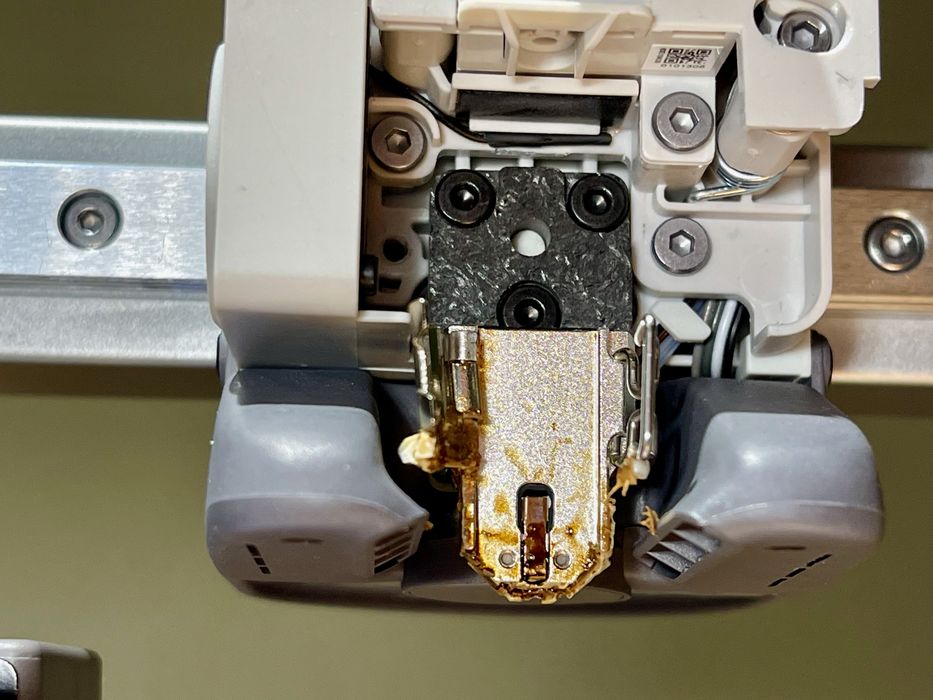
After nozzle removal, I noticed that there was quite a bit of residue from previous prints. This didn’t seem to cause any issues. Similar junk was found on the nozzle that came out.
Multimaterial prints were astonishingly reliable. As someone experienced with the challenging Prusa MMU2S, I can say that the AMS is light years more reliable than the Prusa approach.
One issue I found with the nozzle swaps was that the nozzle would not come out, even after being released. This was because a filament was in place inside. To solve the problem I simply heated up the nozzle to soften the filament, and then the nozzle came out easily. Bambu Lab suggested using the filament cutter manually by sliding the toolhead to the right. However, that didn’t work and I had to stay with the “hot” method.
I encountered one more interesting issue that I am sure most A1 mini operators will eventually bump into: broken filament.
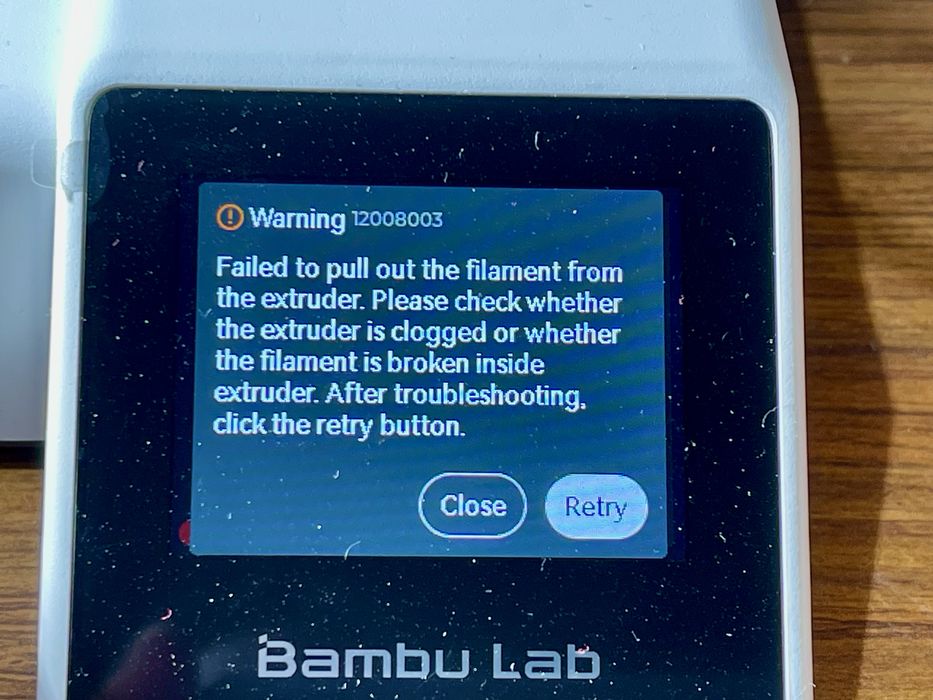
What happens is that if you leave a filament unused in the AMS for a while, it may degrade and crack. Certain brands are more likely for this to occur. Then, when starting a job the AMS pulls the filament out, but it doesn’t actually come out of the extruder because a segment is left behind in the tube.
To solve the problem you must pop off the specific AMS PTFE tube and remove the broken pieces.
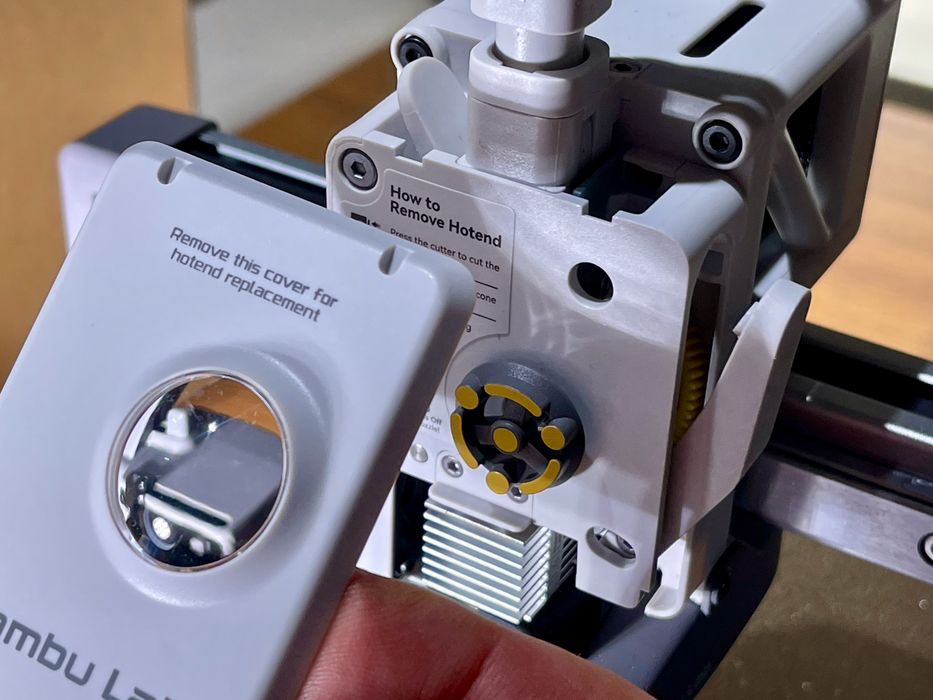
Usually there’s a piece in the extruder, so you may have to pop off the toolhead cover and get deeper inside. It’s pretty straightforward to do so, just follow the instructions in the Bambu Lab wiki.
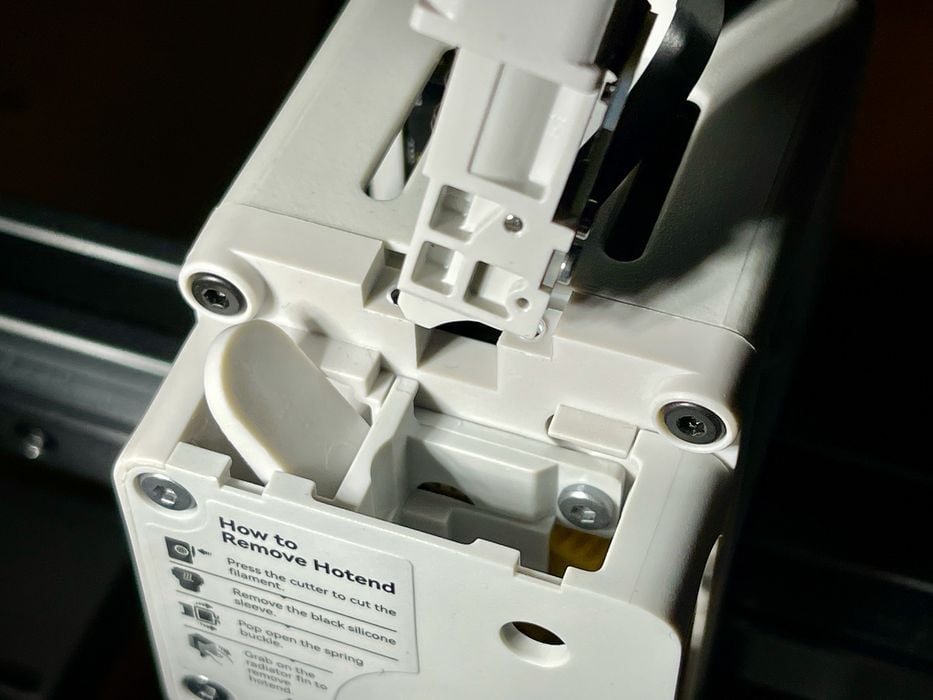
Sometimes you may have to remove the four-way filament connector at the top, and that’s also easy to do. However, be extremely careful because there’s a short ribbon cable attached, and you don’t want to break it.
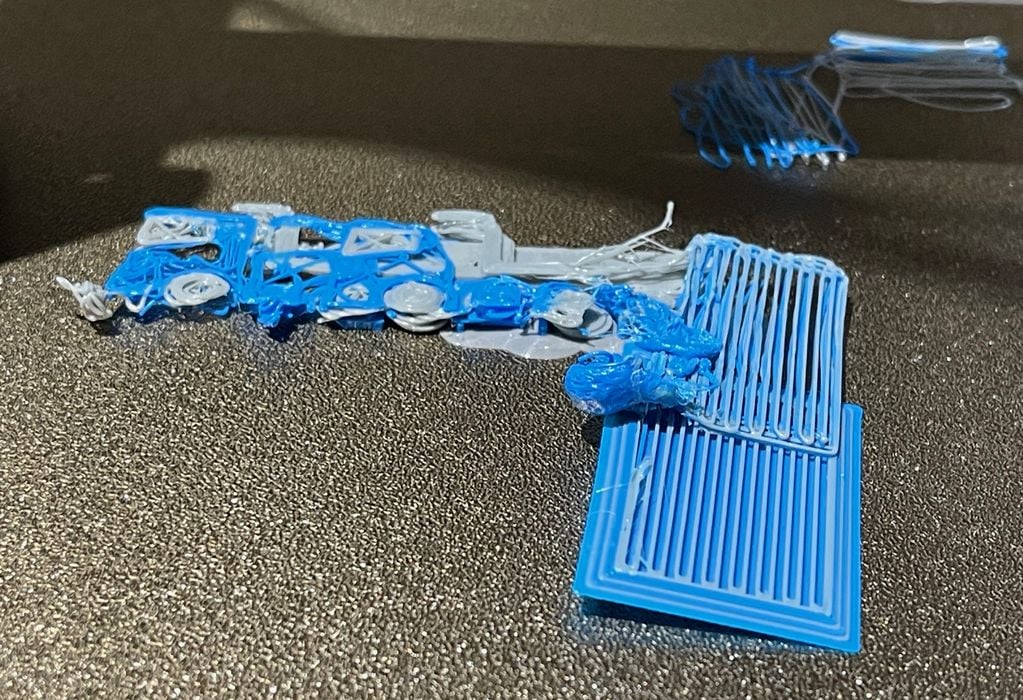
Several times I encountered problems with first layer adhesion. In each occurrence it turned out to be my problem! I had mistakenly selected the wrong profile for the job, which can happen when you’re swapping nozzles. For example, using the 0.2mm nozzle profile when you’re actually using the 0.4mm nozzle on the machine. Don’t do this!
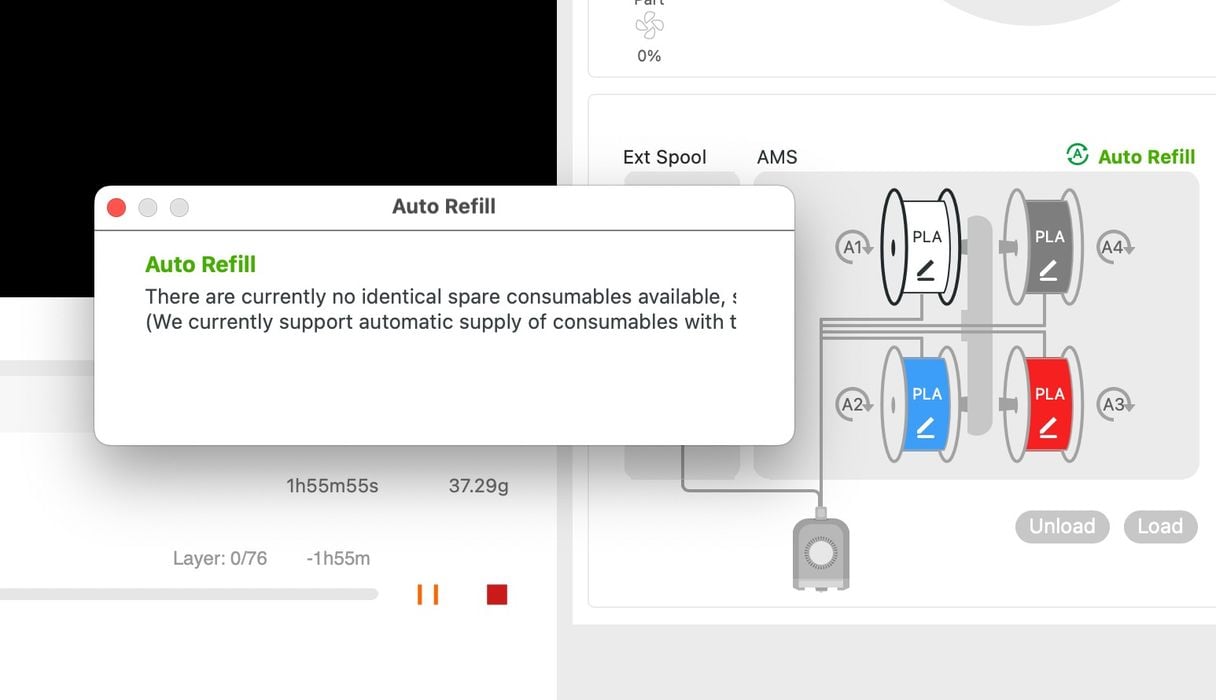
I didn’t try this, but the AMS is capable of automatically switching spools to an identical material on another slot, should you run out. This means you can have very long print jobs using the same material. However, I’m not sure how useful that is given the small build volume and very fast print speed.
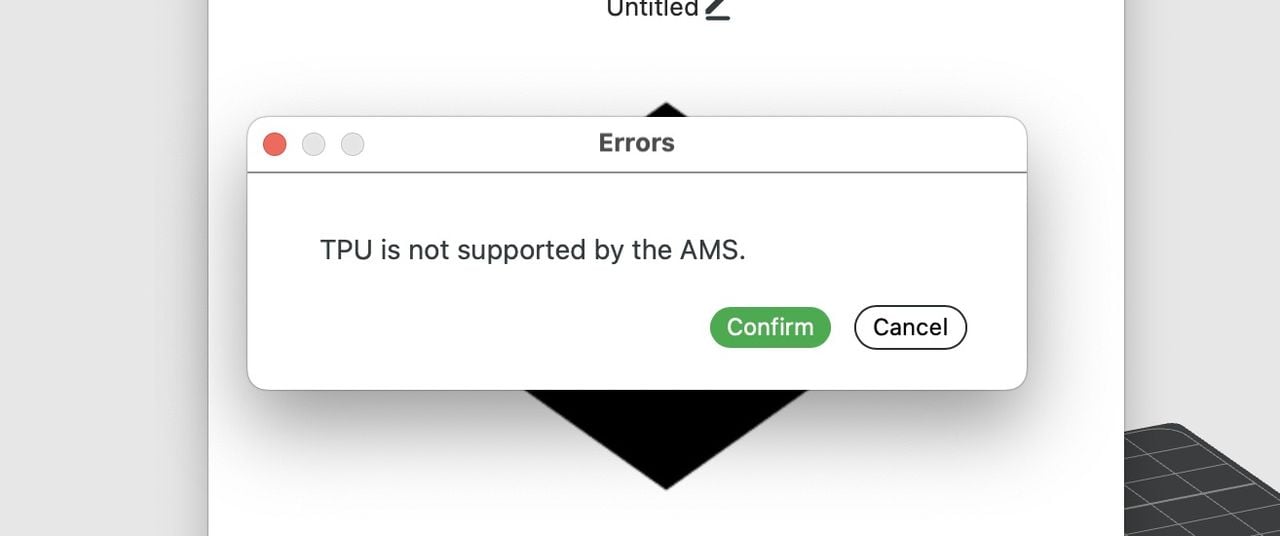
I tested PETG and TPU as well as high speed PLA, and it all worked. However, TPU is not supported by the AMS because it can’t push the spaghetti-like material up the tubes.
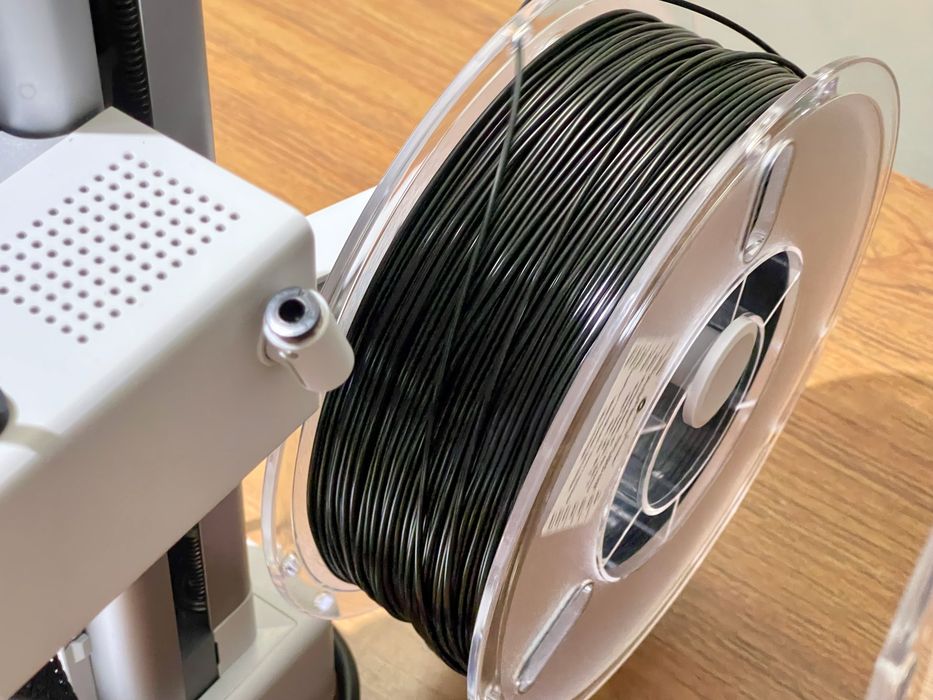
Instead you have to mount the TPU spool on the standard mount point on the base unit.
I did learn at this point that it is quite critical to ensure you properly match all the material configurations: the print profile, the AMS configuration and your color selections must all align, otherwise it’s an error or misplaced colors. Be very methodical when swapping spools!
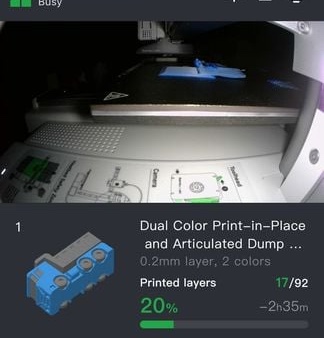
There is an onboard camera for capturing timelapse videos, and also for real time monitoring.
I’d say the camera isn’t exactly in the best position, as it’s off to the side, but there’s few mounting options for Bambu Lab here. The poorly lit view does show you whether the print has failed, and that’s useful enough. Timelapses are pretty basic and not the “smooth” type seen elsewhere.
I did occasionally have trouble connecting to the cloud for remote video view. Sometimes it would take quite a while to connect, so perhaps Bambu Lab needs to scale their cloud system with all the machines they’ve sold?
This is part three of a four part series, please read parts one, two and four.
Via Bambu Lab