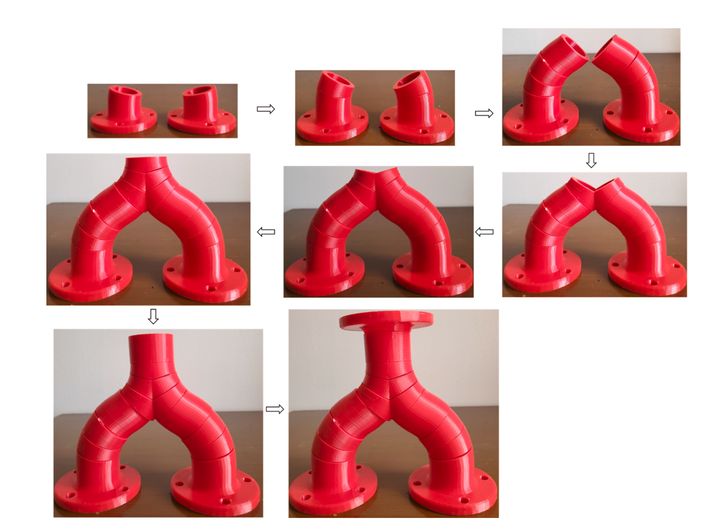
New research has uncovered ways to optimally use 5-axis 3D printing.
Most Fabbaloo readers will be familiar with the usual process of 3D printing: a 3D model is sliced into layers, and then each layer is produced sequentially to complete the object. The âproducingâ part could mean any of the many 3D printing processes, such as SLA, FFF, SLS, etc., but each uses this layered approach.
5-Axis 3D Printing
That paradigm changes with the introduction of 5-axis 3D printing. There are very few examples of this approach, currently available only from a couple of vendors including HAGE and VSHAPER. Those companies produce 3D printers that have not three axes of movement, but five!
The two âextraâ axes enable many more forms of movement and thus approaches other than the standard layer-by-layer approach could be attempted.
Why do this at all, with the inevitable complications of using 5-axis? There is a huge benefit that can become possible: 3D printing without any need for support material.
The idea is that as the print proceeds, it could be âtippedâ at an angle so that an overhang is no longer an overhang. If this concept were done for each overhang area, then a 3D print could be made without any support material.
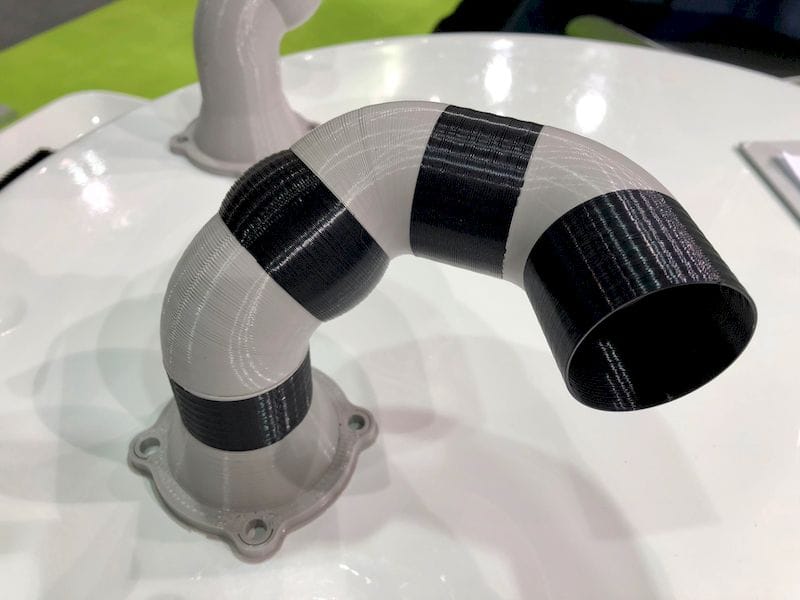
Eliminating support material would provide the enormous benefit of simplifying post-processing activities, which are typically done with expensive manual labor. Potentially this could both reduce costs of finished prints and speed up production. It would also reduce material costs, as there would be none required for supports.
How to Perform 5-Axis 3D Printing
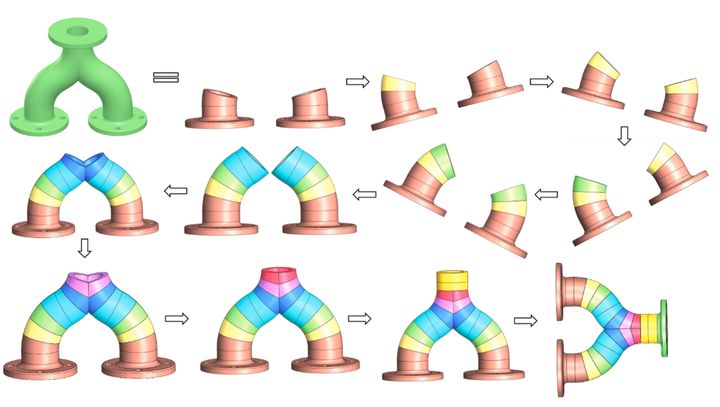
While this sounds terrific, achieving it is a lot more complex.
For example, if you were to pick up an object with complex geometry, how, exactly, would you proceed with these anti-overhang rotations? How many moves would you need? Where do they take place? How much angle is required? In what sequence should they occur? Is it even possible to do this with a given complex structure?
The more you think about it, the more complicated the answers become. This is not a trivial problem.
The answers to these questions now seem to be answered with new research by Xinyi Xiao of Miami University and Sanjay Joshi of Penn State. They explore this space in some detail in the paper âProcess planning for five-axis support free additive manufacturingâ.
They have managed to figure out the answers to all these questions. In the paper, they say:
âHowever, there is a lack of automated process planning software to support the full use of five-axis machines. This paper introduces an automated method that allows reorienting the part during the build using a five-axis machine. The reorientations still allow the part to be built using traditional planar deposition but without the use of supports. This requires that the part be decomposed into sub volumes, such that each sub volume has its build direction and can be built with planar layers without support structures. This paper presents algorithms to determine the sub-volumes, their orientations, and sequence, which form the major components of the process plan for manufacturing. The process plan is generated by sequencing the decomposed volumes while ensuring a lack of local collision with previously deposited volumes.â
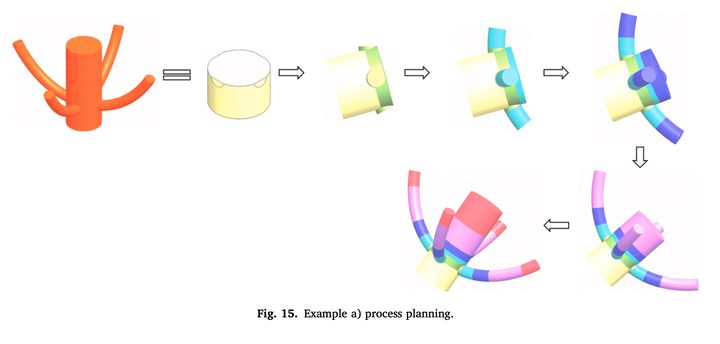
This is quite a complex problem to solve. If you think about the current simple layer approach, it is one that would work for any 3D model: at each Z-height, take a slice and compute the path of the perimeter. Thatâs it. With a fully three-dimensional 5-axis approach, where do you even start?
The researchers have identified algorithms that can analyze a 3D shape and decompose it into zones that have independently consistent orientation attributes. Then a sequence of operations is computed to allow the 5-axis printing to take place in a way that is practical.
It seems that not every geometry would be applicable to this process, but certainly the algorithm could quickly develop optimal tool paths for many objects.
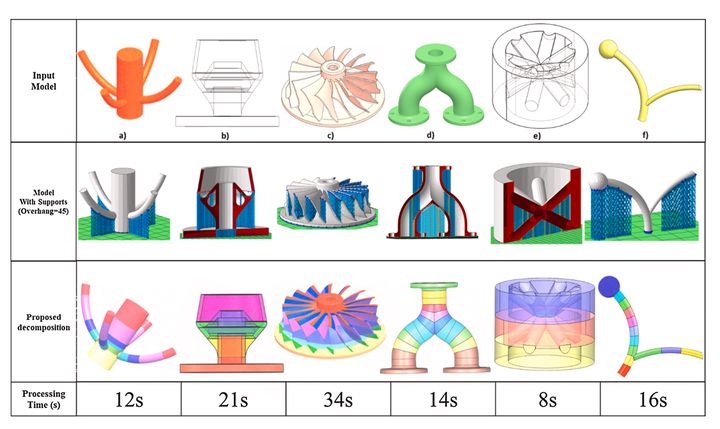
Due to the complexity of this problem, it is unlikely it has been solved previously. However, Iâve seen with my own eyes some of the aforementioned 5-axis machines in operation, but now I realize they must have composed toolpath solutions in a custom manner. Itâs very likely the existing 5-axis 3D printers could benefit greatly from use of Xiao and Joshiâs work.
Via Science Direct