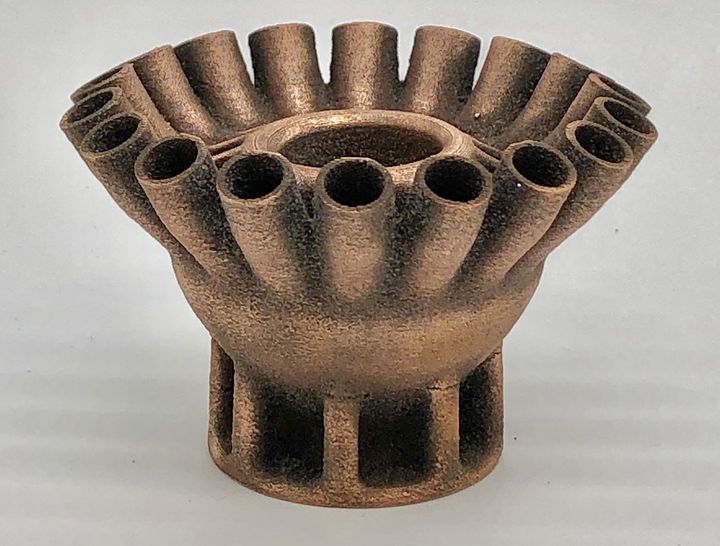
I spoke with The Virtual Foundry to find out more about their unusual metal 3D printing approach.
The company produces an extensive line of metal filaments for 3D printing they call “Filamet”. Their products currently include a range of materials from aluminum to titanium.
Hold on, I know what you’re thinking: how do you 3D print metal with filament? Is not filament exclusively for thermoplastics? The answer is a combination of chemistry and process.
The idea here is to 3D print an object using a thermoplastic filament that is mixed with a high ratio of finely-powdered metal. The resulting 3D print is a heavy object made of the two materials. This “green” object is then heat processed to first remove the thermoplastic resin, and then again to sinter the remaining metal particles together into a fully dense metal object.
This is a process used by some other metal 3D printer manufacturers, notably Desktop Metal and Markforged, but The Virtual Foundry’s process does not involve chemical debinding. Instead, their process only involves non-toxic heat.
The Virtual Foundry Origin
Bradley Woods, the founder of The Virtual Foundry, was originally developing methods of producing artistic metal sculptures, but when exposed to a 3D printer realized the two could be combined into a real business. After a successful Kickstarter launch in 2014, in 2017 the company hired their current CEO, Tricia Suess, who reorganized the company for growth.
The Virtual Foundry Advantage
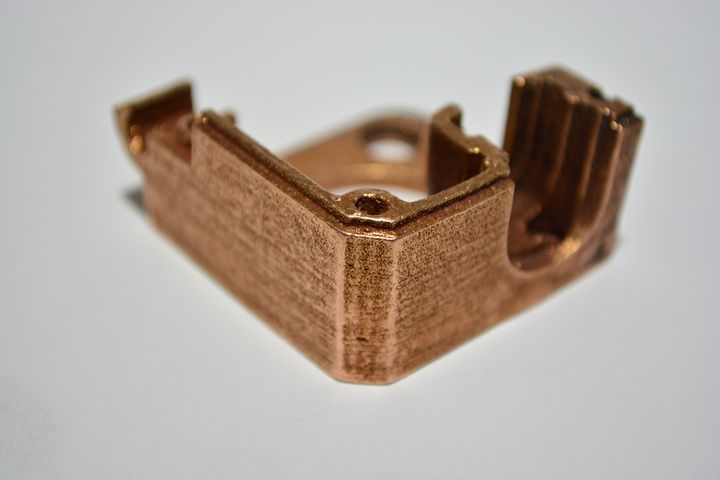
While it’s entirely possible to purchase excellent metal 3D printing systems from a number of providers, The Virtual Foundry has a notable advantage: low cost.
Alternative providers require significant sums to both acquire 3D printers and associated equipment for full operation. Meanwhile, The Virtual Foundry concept can be as simple as purchasing a spool of filament and using an existing FFF 3D printer.
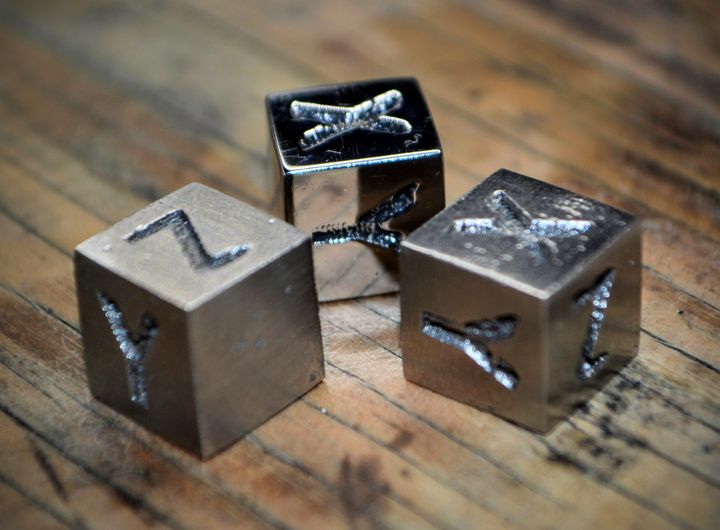
Of course, there are the debinding and sintering steps. That can take place in a sintering furnace, which can be obtained for anything between US$1,000-100,000 depending on size and features, or by using a sintering service. The Virtual Foundry has partnered with Sapphire3D to perform sintering services at low cost. Thus, the cost of entry to The Virtual Foundry’s approach is vastly less than using any other metal 3D printing option.
The Dog Bone Problem
If this sounds like it would be easy to sell these products, there’s actually a barrier in the way that The Virtual Foundry calls “The Dog Bone Problem”.
It turns out that their clientele — which is composed of a wide variety of industries ranging from the arts, aerospace, research labs and more — required a lot of convincing to proceed.
This is not unexpected, as most new 3D print technologies require much explanation and education in order to persuade them to proceed.
One issue is that The Virtual Foundry’s materials are often confused with “novelty” 3D printer filaments that were first seen years ago. Those materials would typically mix PLA with an unusual powdered substance like wood, coffee, algae, coconut, and yes, metal powders. These filaments were essentially for making decorative objects and were not mechanically functional in any true sense.
After getting past that barrier, The Virtual Foundry’s clients realized they could produce serious metal mechanical parts using the approach. However, they would inevitably be interested in the strength of the resulting parts.
Strength analysis is commonly done in almost all 3D printing processes. Typically this is done by producing a series of standard sample parts and pushing them through tests to gauge their strength. The most frequently-seen test part is the standard “dog bone” object: a flat length with some tabs on the ends.
Usually clients would print dog bones and then test them in the standard way they would do with any other 3D printing process. However, it turns out this doesn’t work with The Virtual Foundry’s process.
The reason is that parts produced with sintering tend to shrink up to 20% in size. While this must be accounted for when the parts are designed, it doesn’t account for the mechanical tensions that occur during shrinkage. In the case of the dog bone, the end-tabs tend to pull too much on the center portion, causing it to weaken. The standard strength testing does not reflect actual results.
Thus The Virtual Foundry has to explain this to clients and ensure they test in other geometries that are more appropriate for the process.
The Virtual Foundry Partnerships
This effect has led The Virtual Foundry to provide robust support for clients, as it really is a very different way to produce metal parts. They tell clients that they cannot directly replace machining or casting processes, and instead have to think about things quite differently.
It turns out that the geometries typically produced by generative CAD software tend to sinter very well, so The Virtual Foundry helps clients get into that design space. It also provides a way for clients to more easily leverage the advantages of 3D printing technology, as “impossible” objects can be produced.
They work closely with clients, some of whom are notable US national laboratories. They also can produce custom metal filaments on demand from clients. I asked about who would do such a thing, and was told a story of how NASA sent them “jugs of stuff” and they made filament from it, without even knowing what it was.
Another client used their tungsten filament to produce an object for a radiation application that, even without debinding and sintering, was sufficient for use in the application. The tungsten green parts were apparently 8g/cc density, which almost matches lead.
Yet another client used Filamet to print an in-situ Peltier cooling system on a circuit board by doping one side positive and another negative.
In a way, The Virtual Foundry materials system is more like a development platform than a straightforward set of metal filaments. It’s a far more complex space than you might imagine.
If you’re interested in experimenting with professionnl-level metal 3D printing at a very low entry cost, you might want to check out The Virtual Foundry.