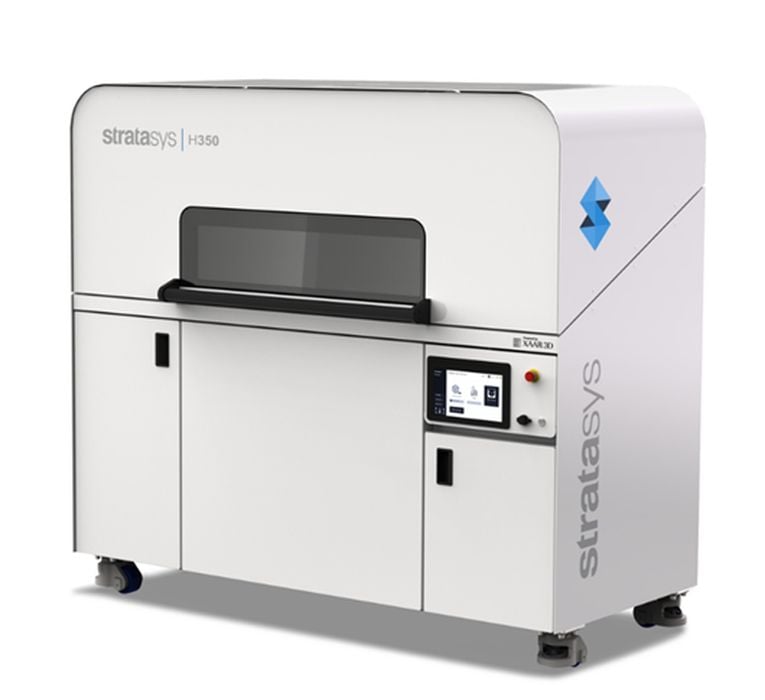
Charles R. Goulding and Preeti Sulibhavi examine Stratasys’ capabilities to match injection molding technology.
Injection molding is long proven technology for making large quantities of high-quality molded products cost-effectively. Injection molding processes have continually improved with top of molder unit robot integrations that pull in raw materials pre-production and also pick and package finished goods for shipping. With conveyors robotized connecting molders, the molding process essentially becomes fully automated. It is difficult for new technology to disrupt and displace an already efficient process.
On June 21st, 2023, Stratasys held a webinar titled, “Injection Molding versus 3D Printing with SAF.” The webinar detailed all the ways in which its SAF H350 FDM printer is reliable, consistent and produces replicable and repeatable high-quality results when compared to injection molding.
Injection molding involves all-at-once production processes, whereas 3D printing uses layer-by-layer techniques. It can reduce a company’s on-demand inventory and makes it less physical and more digital.
In addition, there are very little design limitations as opposed to the many that are encountered with injection molds.
SAF H350 uses a proprietary powder resin that can be reused to a certain extent.
Companies like Onulis and Purple Platypus are using Stratasys workflows to reduce costs, inventory, increase design complexity, and reduce lead times.
The Stratasys technology raises breakeven volumes compared to traditional 3D printers, which have lower breakeven volumes when compared to injection molding. The breakeven for SAF H350 printers versus injection molding is approximately 1 million parts (where the larger volume is more amenable to injection molding). 3D printing offers better results with smaller more complex parts and reduces lead times for most project workflows.
Onulis

This company’s mission is to solve critical gaps between 3D printing workflows and sustainability. The company has an extensive background in product development and bringing to market intuitive products that solve current industrial issues.
Much resin waste is considered hazardous. Onulis is taking sustainable steps to minimize the harmful effects that such workflows pose to the environment.
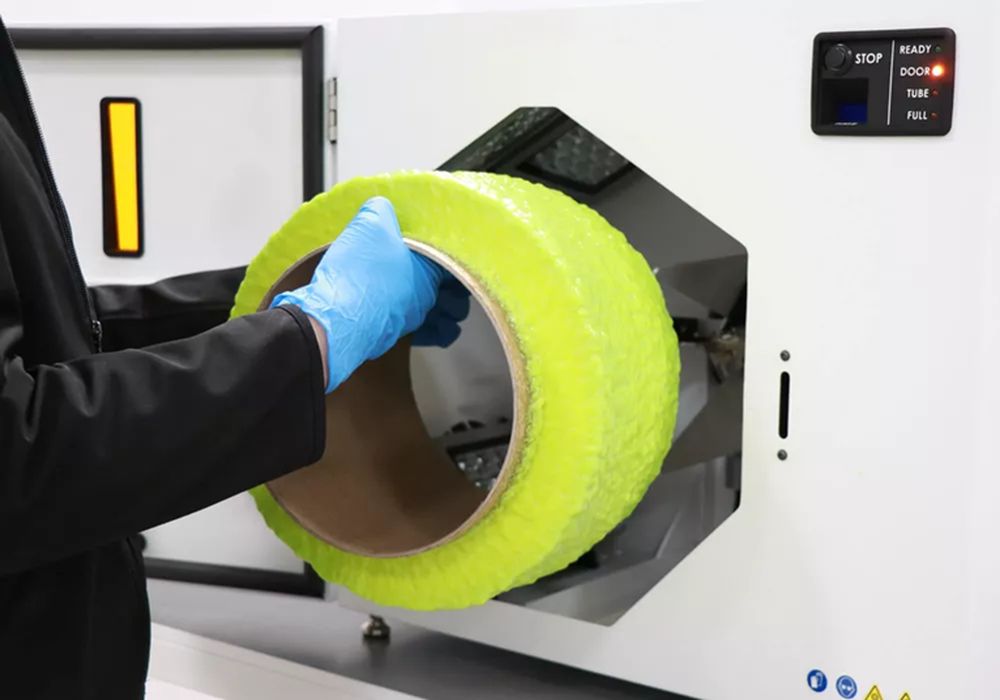
The WRAP W7500 printer creates solid plastic stock for a wide variety of uses, including low-cost media for prototype machining, raw material to produce colorful products, or unique organic shapes to create artwork projects. Leveraging the patent-pending WRAP (Waste Resin Axial Printing) technology, which prints with previously used or expired UV resin, the W7500 operates at virtually zero cost. Once the waste resin is printed, it can also be disposed of as standard household waste.
Purple Platypus
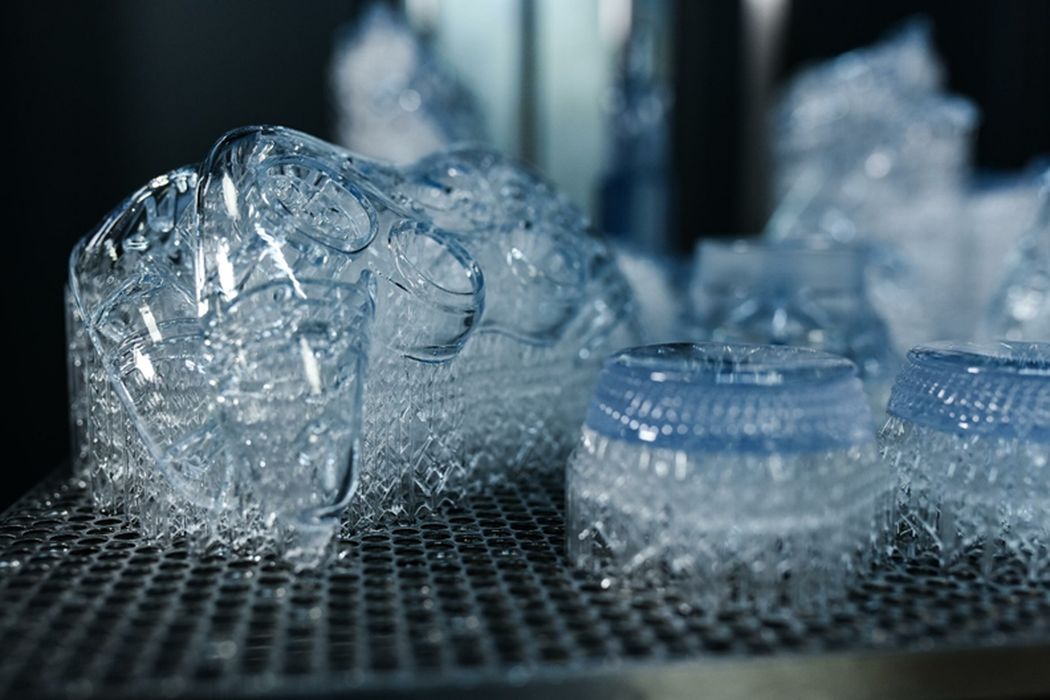
A Diamond-level Stratasys reseller, Purple’s team is specialized in 3D printer technology and materials. It hosts a blog where experts post weekly and cover topics ranging from milled buckles to determining if a PolyJet printer is the right choice for a customer’s needs. All useful and relevant topics. All add value to 3D printing technology.
One topic of particular interest to us was the piece on Advancing Automotive Production & Development, as we have covered this topic extensively on Fabbaloo. But there were other topics including air turbines and football helmets that piqued our interest as well. We have covered turbines and football injuries on Fabbaloo so the relevance was not missed by our team.
The Research & Development Tax Credit
The now permanent Research and Development (R&D) Tax Credit is available for companies developing new or improved products, processes and/or software.
3D printing can help boost a company’s R&D Tax Credits. Wages for technical employees creating, testing and revising 3D printed prototypes can be included as a percentage of eligible time spent for the R&D Tax Credit. Similarly, when used as a method of improving a process, time spent integrating 3D printing hardware and software counts as an eligible activity. Lastly, when used for modeling and preproduction, the costs of filaments consumed during the development process may also be recovered.
Whether it is used for creating and testing prototypes or for final production, 3D printing is a great indicator that R&D Credit eligible activities are taking place. Companies implementing this technology at any point should consider taking advantage of R&D Tax Credits.
Conclusion
The webinar provided great insight into the technology behind the Stratasys SAF H350 FDM printer as well as the benefits of using the technology when compared to injection molding.
Specifically, this webinar was informative in noting the scaling requirements to break even using the 3D printing technology and the point at which injection molding proves more cost-effective to use in daily manufacturing processes. We are excited to see this innovative technology expand into various industries.