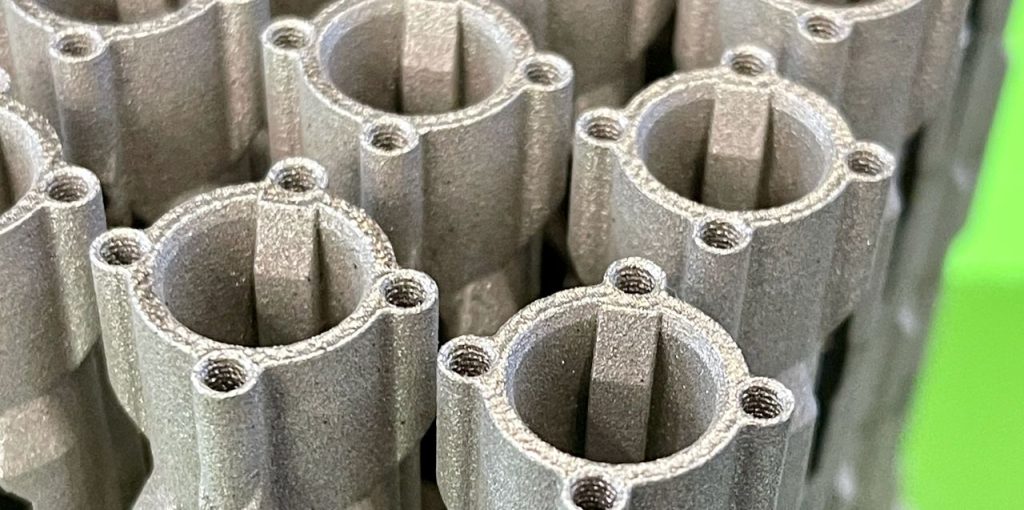
I spoke with the folks from One Click Metal and learned quite a bit about their mid-range metal 3D printer.
Somehow I had not seen their equipment, but that’s likely due to a combination of the pandemic and the fact that the company was formed only in 2019.
They’re a spin-off from Trumpf, a large manufacturer of industrial metal 3D printers. Translation: they make big metal 3D printers. One Click Metal, which currently has around 20 staff, makes much smaller machines that hit an entirely different market.
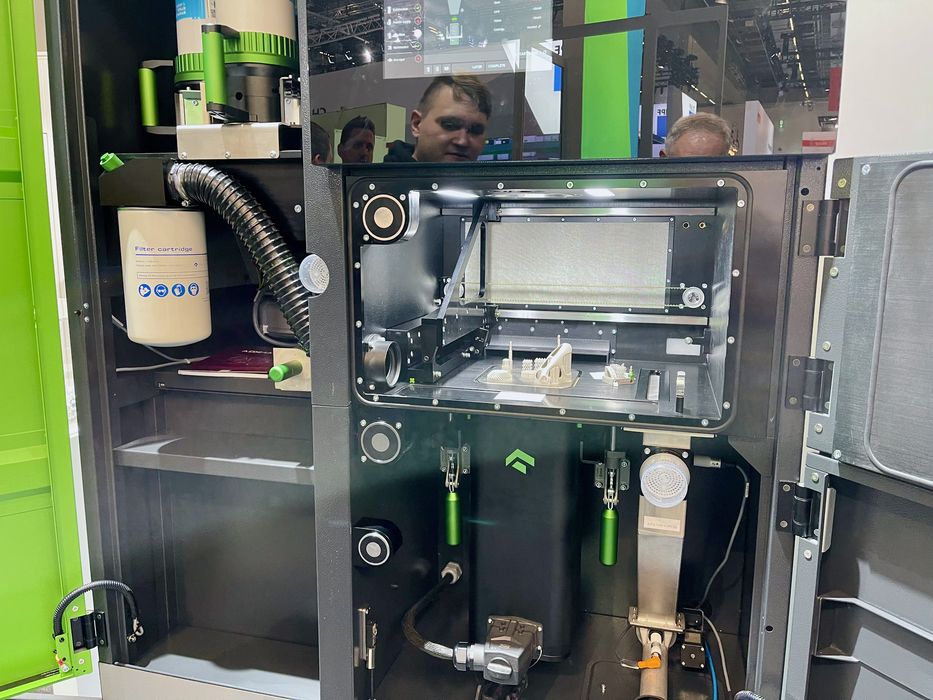
While their equipment has a smaller build volume, it also carries a smaller price tag: only €95K (US$101K), making it much more affordable for companies wishing to build smaller metal parts.
But there’s another factor here, and there’s a clue in the company’s name, “One Click Metal”. They’ve designed the system to be highly usable in every respect, from hardware to software. This is also attractive to the smaller-scale market they are trying to address.
Their MPRINT+ system uses the LPBF process, and employs a 200W fiber laser to melt the metal powder. The system sports a 150 x 150 x 150 mm build volume, which should be sufficient for many applications. This is larger than other small metal systems that target experimental applications.
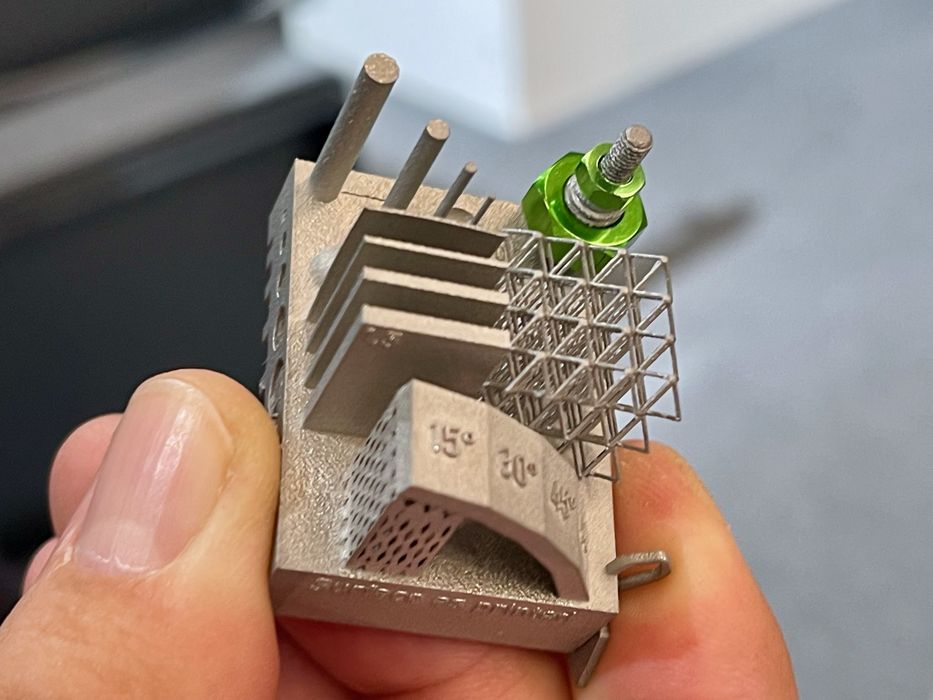
The laser is able to focus down to 0.07mm, making it possible to produce high resolution prints, as seen in the images here. The parts I examined appeared to be of excellent quality.
One of the biggest hassles that comes with the larger LPBF metal 3D printers is powder management. Metal powder can be toxic or even explosive, and exposing it to the oxygen in the air can destroy print quality. Therefore very sophisticated — and expensive — equipment, systems and procedures are used to manage the powder as it passes through the manufacturing process in those systems.
One Click Metal simplifies all that by using a cartridge system that is safe and clean. Operators don’t have to encounter the powder at all during or after printing.
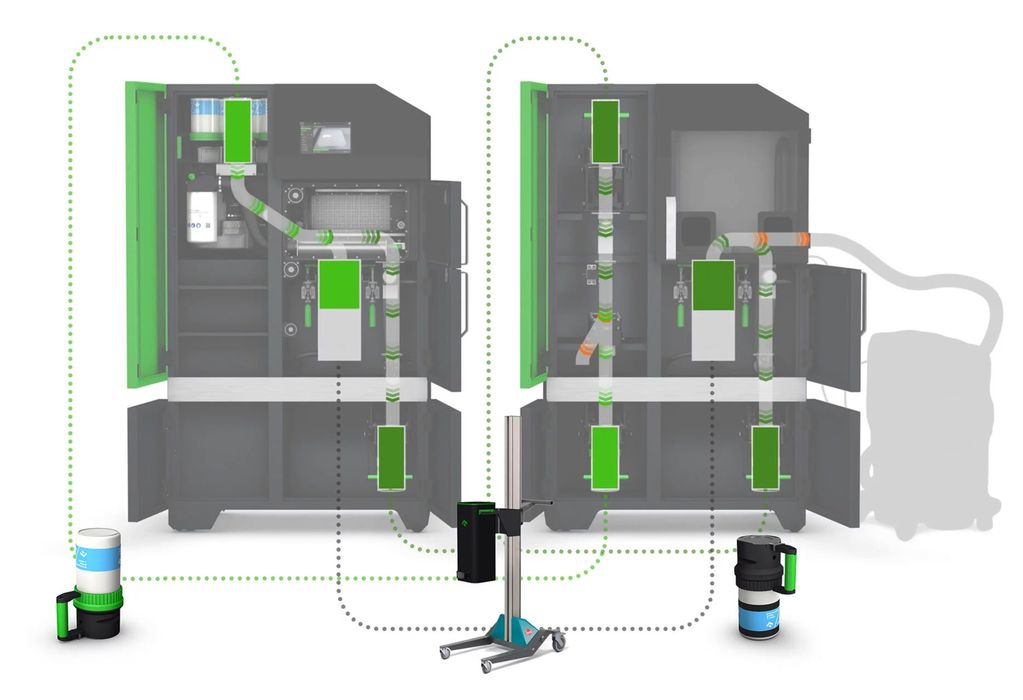
This diagram shows the flow of powder material through the MPRINT+ and the associated MPURE powder handling unit. The operator need only use a tool holder to move cartridges around between the machines, without exposing the powder.
The MPURE system is intelligent: the cartridges are tagged and the system knows their history, capacity and quantity of material. One Click Metal said the unused powder is “100% reusable”.
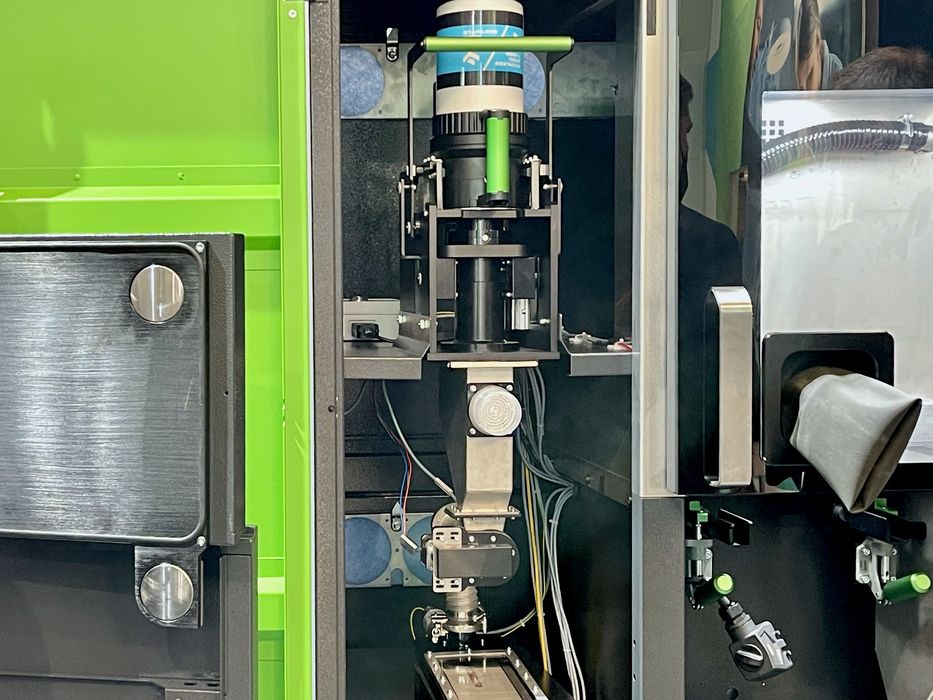
One interesting feature is the optional ability to pre-heat a print module to 200C. This dramatically relieves thermal stress during printing, and thus makes prints more accurate and reliable.
These print modules can be removed, so it’s possible to swap in a second print module to begin printing while you’re post processing the first one. That should increase throughput significantly.
I asked about the possibility of changing material, because many LPBF systems basically “commit” to a specific material once loaded. That’s because it’s basically impossible in many machines to clean out old powder; there will always be a residue. That’s totally unacceptable for many applications, particularly aerospace and healthcare.
It turns out that One Click Metal has an innovative solution for this, the “Lab Module”.
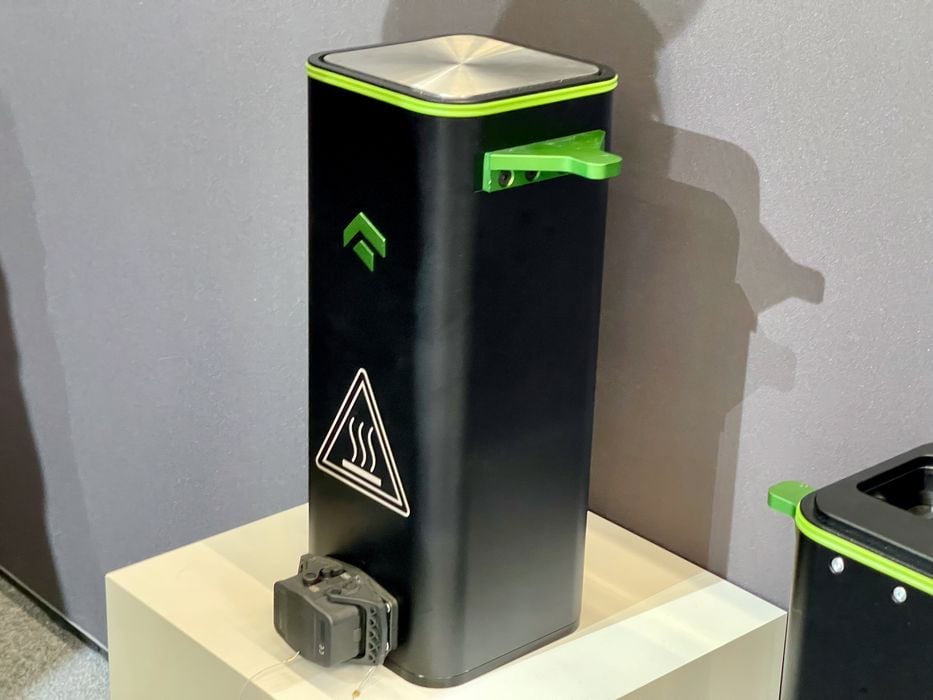
It appears to be another print module, like the ones that are normally used in the MPRINT+. However, there’s a difference here. The Lab Module includes the printing components, but also a totally enclosed powder system. This greatly decreases the build volume, but it enables the operator to change the machine’s material — in less than an hour — if required.
The scenario that I’d expect this to be used is one where a single material is normally used, but there is an occasional need for a different material. That is likely the case for many metal shops, and the Lab Module would be a lot cheaper than buying a second machine to dedicate to an infrequently used material.
Along with the hardware, One Click Metal offers a cloud-based system, MOne, that provides a complete remote print management solution.
The company seems to be quite successful, as they say they are “growing fast”, and “investors are happy”. For now they sell (through resellers) only in Europe, but “North America is coming”.
Via One Click Metal