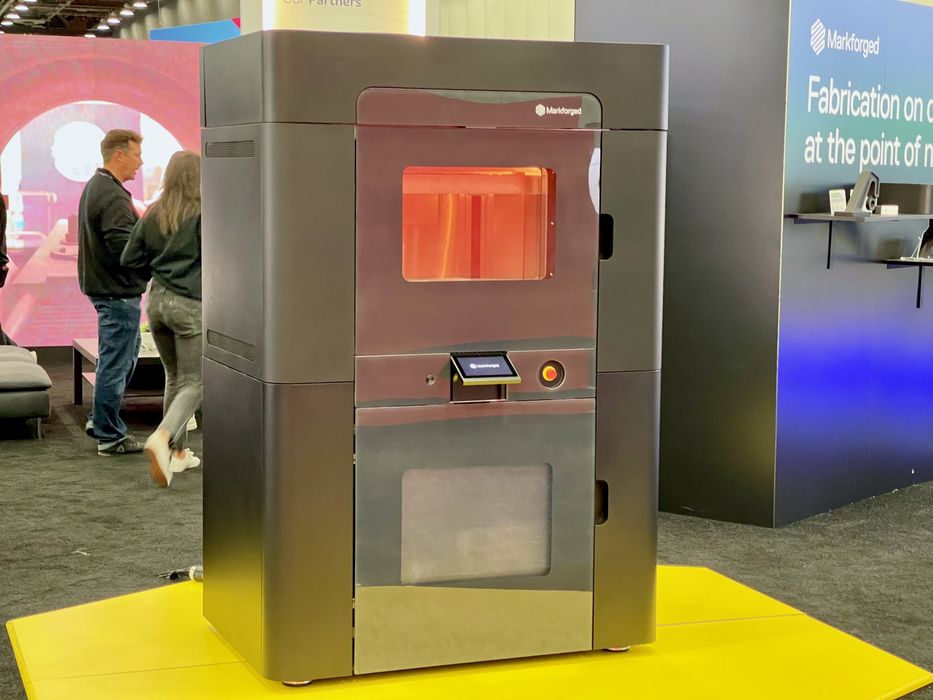
Markforged’s FX20 3D printer is quite impressive.
The company has come a very long way from its early days marketing a unique continuous carbon fiber 3D printer. That device paved the way for many companies to produce equipment that could make parts with sufficient strength for many new applications.
Since then Markforged has added plenty of new equipment, including a line of devices capable of producing metal parts using a relatively inexpensive process.
Their most recent innovation is the FX20 3D printer, and it’s quite different from the rest of their gear in that it’s clearly a device for the factory floor.
For starters, it’s not a desktop device at all: as you can see in the top image, it’s a large standalone unit that weighs in at 450kg.
The reason for this size is that the FX20 has a rather larger build volume, the largest in Markforged’s fleet: 525 x 400 x 400 mm, almost placing it in the “large format” category.
Similar to Markforged’s prior devices, the FX20 is able to 3D print with continuous carbon fiber, along with selected polymer materials. The continuous carbon fiber adds considerable strength to printed parts, far more than one gets from using chopped carbon fiber filament. Here the filament is literally continuous, and threads through parts that are both strong and lightweight.
The parts can be as strong as some metals, yet very lightweight, and that’s quite attractive to the aerospace industry: every gram saved is another gram of payload on an aircraft or rocket.
However, the aerospace industry is also filled with regulations and qualifications, as one would expect for such a life-critical function. Because of this there are certain materials certified for use in that industry. One of them is ULTEM.
ULTEM is a high-temperature material that’s strong and lightweight. It’s been used in aerospace 3D printing for some years, but now Markforged has combined ULTEM and continuous carbon fiber in the FX20.
The FX20 is able to 3D print continuous fibers (carbon, fiberglass, Kevlar, etc.) with their normal strong Onyx material as well as nylon, but also with high temperature ULTEM 9085.
ULTEM 9085 can be 3D printed due to the presence of a high temperature nozzle and an actively heated build chamber temperature of 200C. This is another reason for the large size of this machine: it has to handle extreme heat. Actually, there are three direct drive nozzles on the FX20: two for polymers, and one for the fiber.
The presence of two polymer nozzles suggests that at some point in the future Markforged might enable the use of high temperature soluble support on the machine. However, as of this writing they don’t mention this possibility.
There are a number of features for the FX20 that should be amenable to manufacturers. One is Eiger, Markforged’s cloud-based digital library and online job preparation tool. This provides 2FA security, team administration features, encryption and much more, all of which should help qualify the FX20 for use in sensitive or critical applications.
The FX20 is able to 3D print details as fine as 0.05mm, which is quite impressive for a high temperature machine of this volume.
Markforged said the FX20 is their “most sophisticated” 3D printer yet, and it appears to be so. One omission may be “Blacksmith”, the company’s “autopilot” for quality control. This system, which is available for X7 machines, monitors prints to ensure they are within design tolerances with an AI-powered inspection system. As far as I can tell, Blacksmith is not yet available for the FX20, but it would certainly be a welcome feature for manufacturers.
Nevertheless, the FX20 appears to be a unique option for aerospace applications: large build volume, continuous fiber and high temperature materials.
Via Markforged