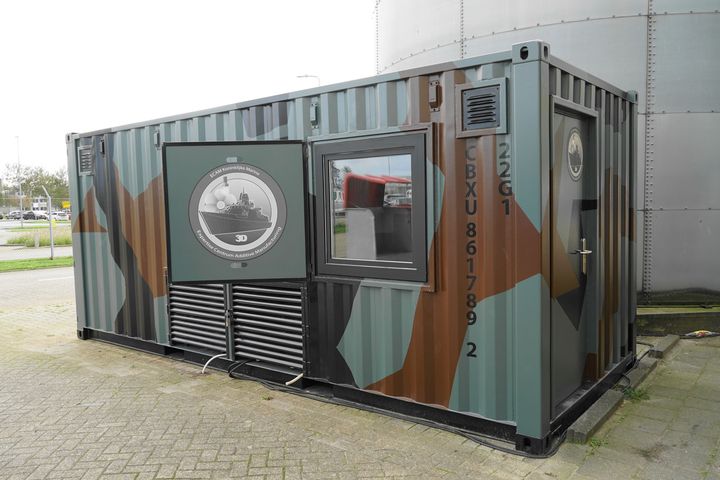
SPONSORED CONTENT
There was a time when high-temperature 3D printing was considered an experimental exercise, but that doesn’t seem to be the case anymore.
I’ve learned of a fascinating example of how high-temperature 3D printing has become so straightforward that’s it’s now being used in a mobile setting.
Let me explain how this has been done.
The Royal Dutch Navy’s fleet, like any ships, have a problem: spare parts are almost always required. In order to keep the fleet at sea for the maximum duration, each ship will carry large quantities of parts for components that could fail during operations. Apparently this can be a stock as large as 30,000 parts on a single ship.
That’s an enormous inventory of parts that, as you can imagine, requires significant management, storage and processing. If there was anything that could be done to reduce the complexity, the Royal Dutch Navy was interested.
AMCOD
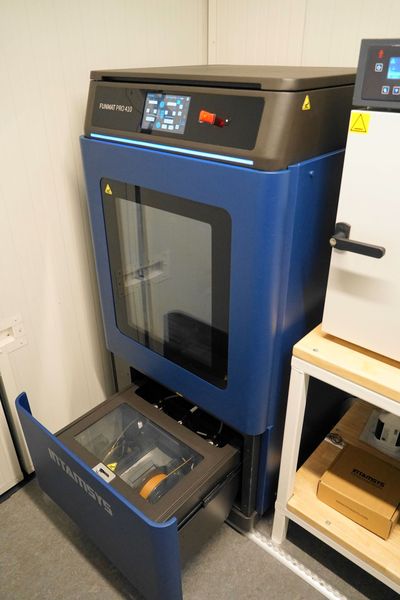
Their answer was something they call “AMCOD”, which stands for “Additive Manufacturing Container for Defence”. It’s a mobile 3D printing platform, essentially a workshop in a shipping container, as you can see in the accompanying images. From this platform workers can begin producing new parts within an hour of installation.
This type of installation has been done previously, even in the Royal Dutch Navy. However, the parts produced by those experiments were in PLA. That’s an easy material to 3D print, but it is far from the most durable material. This meant that spare parts produced onsite could not be used in mechanically or thermally stressful situations.
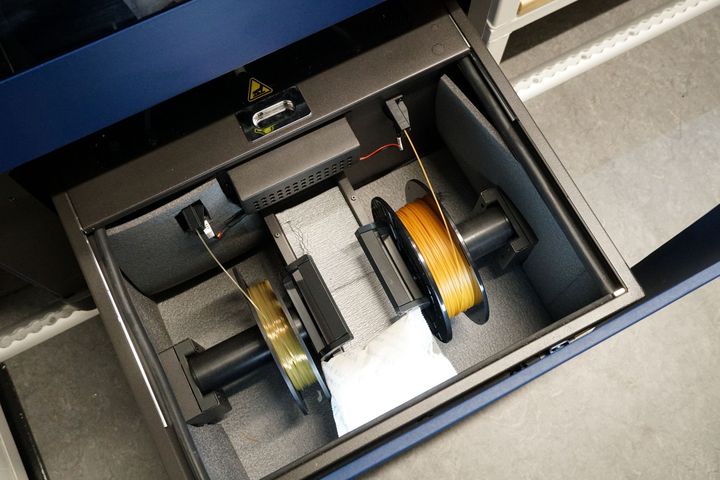
The Royal Dutch Navy sought to increase the breadth of possible spare parts usable with the AMCOD concept, and modified the unit to include three high-temperature 3D printers. For their experiment the Navy selected one FUNMAT HT and two FUNMAT Pro 410s. The FUNMAT 410 is an industrial model that can print up to 5000C in a chamber heated to 90C. It’s capable of 3D printing almost any 3D printable material, including PEEK, PEKK, PC and more, in a volume as large as 305 x 305 x 406 mm.
While there are now several capable high-temperature 3D printers currently on the market, the reason why the Royal Dutch Navy selected INTAMSYS’ devices is quite interesting.
3D Printing Spare Parts On Ships
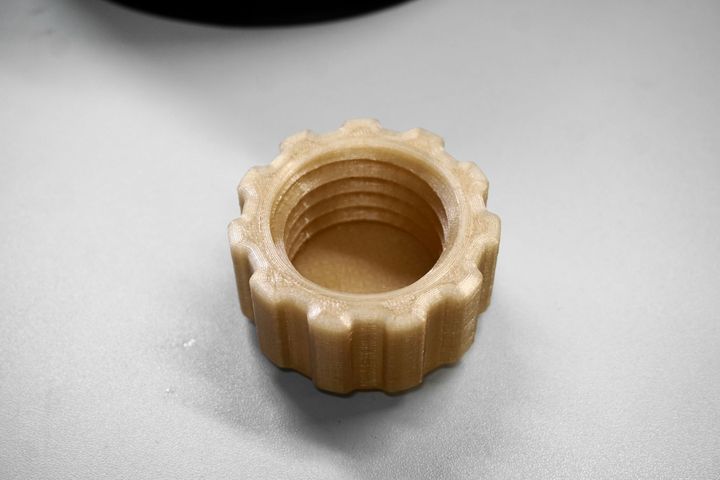
Onboard a ship there may be a need for spare parts at any moment. AMCOD workers are able to access a “Thingiverse for the Navy” repository of 3D models, which contains some of the required parts. They are also trained to reverse engineer parts if necessary to create their own 3D models.
The problem is that some of the parts require specific certifications before they can be used. Certifications usually require production in a certain way using very specific materials. In other words, they must use known 3D print parameters with a particular material.
That’s easily possible with the INTAMSYS equipment because it is a fully open-materials device. This means it is possible to use materials from any vendor, and having the ability to specify any 3D print parameter configuration required. Some competitive high-temperature 3D printers require proprietary or vendor-limited materials that might not meet the certifications.
The certifications mean the ship carries specific high-temperature materials that can then easily reproduce the required parts if the correct print profile is used. The AMCOD high-temperature configuration essentially becomes a certified mobile part factory.
This new capability will allow the Royal Dutch Navy to take another chunk out of their spare parts inventory on each ship. I’m not sure of the cost benefit analysis here, but it’s likely they could be saving a considerable amount of money, since the navy would not have to pay for hundreds of manufactured spare parts that, for the most part, would sit idle in ship stores.
Combining mobile 3D printing factories with high-temperature materials seems like a natural step that could be extended far beyond just this naval application. Ships are ships, whether in a navy or not. It’s possible the same kind of savings might be available to commercial shipping.
But only if they have a mobile high-temperature 3D print factory onboard.
Via INTAMSYS