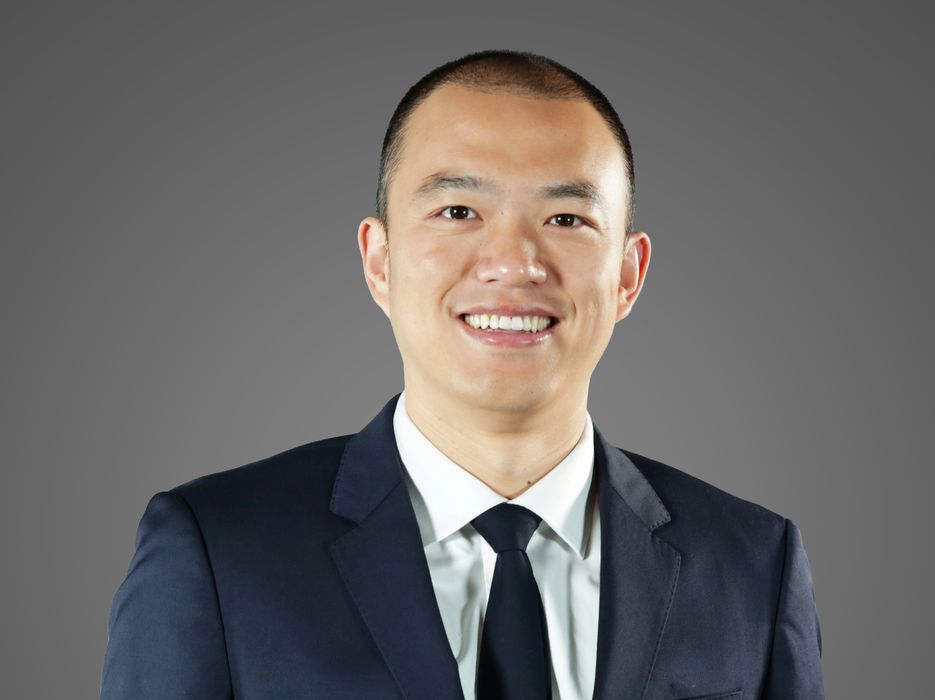
SPONSORED CONTENT
We had a chat with Raise3D CEO Edward Feng to find out more about their latest 3D printers, the E2CF and the Pro3 Series of professional 3D printers.
These new additions to the Raise3D portfolio offer significant functionality, and as you’ll see in the interview below there were many interesting challenges that Raise3D had to overcome to develop these devices in order to improve their customer experience.
Raise3D E2CF 3D Printer
Fabbaloo: Youāve added a new professional 3D printer, the E2CF, thatās capable of 3D printing parts with reinforcing carbon fiber. What is causing the demand for this type of material?
Carbon fiber and other fiber-reinforced composite filaments have been proven to be the best companion for engineers. Their excellent mechanical properties and high HDT both make them a perfect choice for mainstream engineering challenges. That’s a typical requirement for Raise3D customers, so it’s a perfect fit.
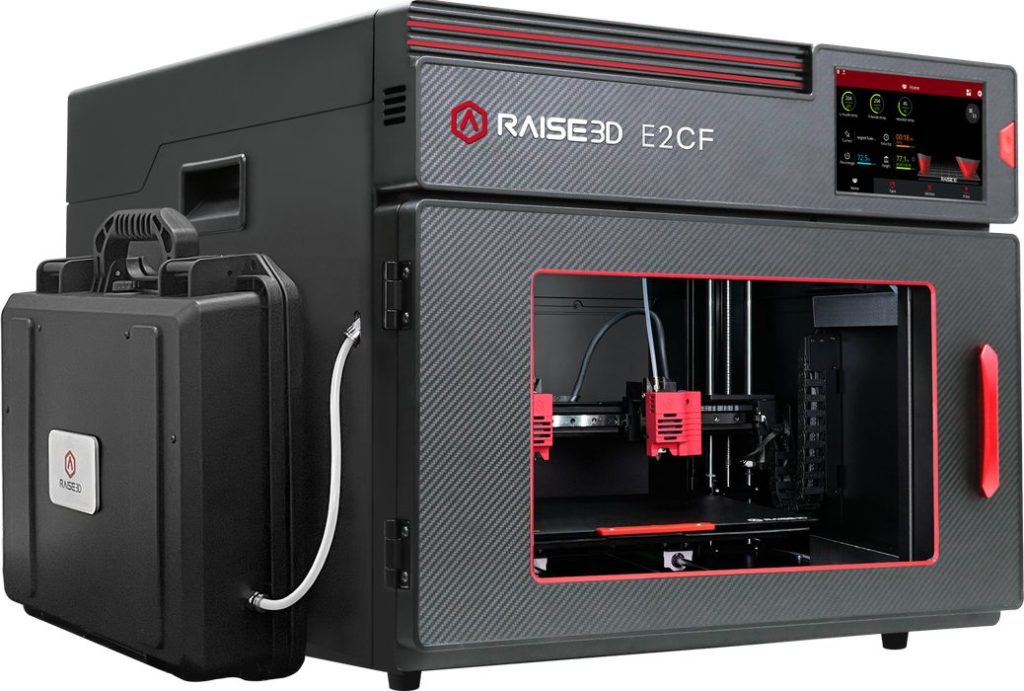
Fabbaloo: How challenging was it to adapt existing Raise3D technology to permit the use of CF materials in the E2CF?
The biggest challenge to deal with was the abrasion problem. When running a 3D printer on CF materials, abrasion is always the key issue. Additionally, our material scientist wanted to have better filament performance when compared to other CF reinforced materials available on the market, so the length of our chopped fiber within the filament is about 20% to 30% longer. That brings better mechanical performance, but the estimated lifetime for the nozzle is more than 50% shorter. So, finding a durable extrusion path is the first problem we solved, and thanks to the hard work of our engineers , we adapted the most advanced silicone carbide nozzles to the system , in order to offer customers a longer lifetime when using CF filaments.
The second biggest challenge for the system was the humidity control. Since nylon-type polymer is used as the main base resin for the reinforced material, this type of polymer can easily absorb moisture. The problem with having moist filament is not only a resulting visual appearance that is unappealing or a failed print, but even if the print is successful, the mechanical performance would be very different from that specified in the datasheet. Drying using hot air the preferable solution for humidity control, but the cost as well as the resulting noise and vibration prevent that solution from being used in an office environment. So, after validating different approaches, our final answer was to use a sealed dry box solution. This allows the the filament to remain with a humidity of under 20% for over 2 weeks with 100% relative humidity outside.
Fabbaloo: Would it be possible to perform low-volume CF end-use part production with the E2CF? Is it possible to organize groups of E2CF units together to increase throughput?
Sure, it’s a reasonable and economically friendly solution. Also, the mirror mode will easily double the production if you don’t have complex geometry that may need support material. The IDEX mechanics inherited from the E2 series make this printer very flexible, and printing with our breakaway support material could help with a situation where you need to create complex parts. And, as a Raise3D printer, it is always ready to connect. With the help of the RaiseCloud platform, you can easily manage a large-scale print farm for end-part production. We also recommend to have a mixed setup with our RMF500 industrial solution.
Fabbaloo: The E2CF release will coincide with a new PA12 CF material and a matching breakaway support material. Can you explain how the breakaway support works? What is the benefit of breakaway support?
Based on years of hard work, we finally found a sweet point for creating support filaments. The breakaway support filament has several key benefits when compared to water-soluble support materials:
- Very easy to remove, a medium size part can take less than 2 minutes to remove. This saves post-processing time;
- Works very well for large parts, as it won’t fail or break due to moisture absorption during the printing process;
- Environmentally friendly, as there is no waste water;
- Some of the nylon-reinforced material can undergo a performance and geometry change after being soaked in water. This solution avoids this;
- Much cheaper when compared with water-soluble support materials.
However, if the part is complex, you can still use our new PVA or BVOH support filaments from our OFP partners.
Fabbaloo: While many industries could make use of strong, lightweight 3D printed parts, which specific industries do you feel could immediately benefit by using the E2CF 3D printer?
The purpose of the E2CF 3D printer is to print complex and lightweight end-use components with fiber-reinforced thermoplastic filament. Such a solution creates instant benefits in several areas of application, including functional prototyping, jigs and fixtures and small batch production, without the usual limitations felt within industries. As such, the E2CF can immediately create advantages in almost all industries. However, among those that place a great value on large size, the ability to withstand harsh environments and fuel efficiency, the E2CF should deliver a distinctive ROI, in undustries such as automotive and aerospace.
Fabbaloo: What is the pricing and availability for the E2CF?
The E2CFās price is 3,999⬠in Europe and $4,499 in the US and rest of the World. Pre-sales started on the 1st of November, and deliveries are scheduled to start in December.
Raise 3D Pro3 Series
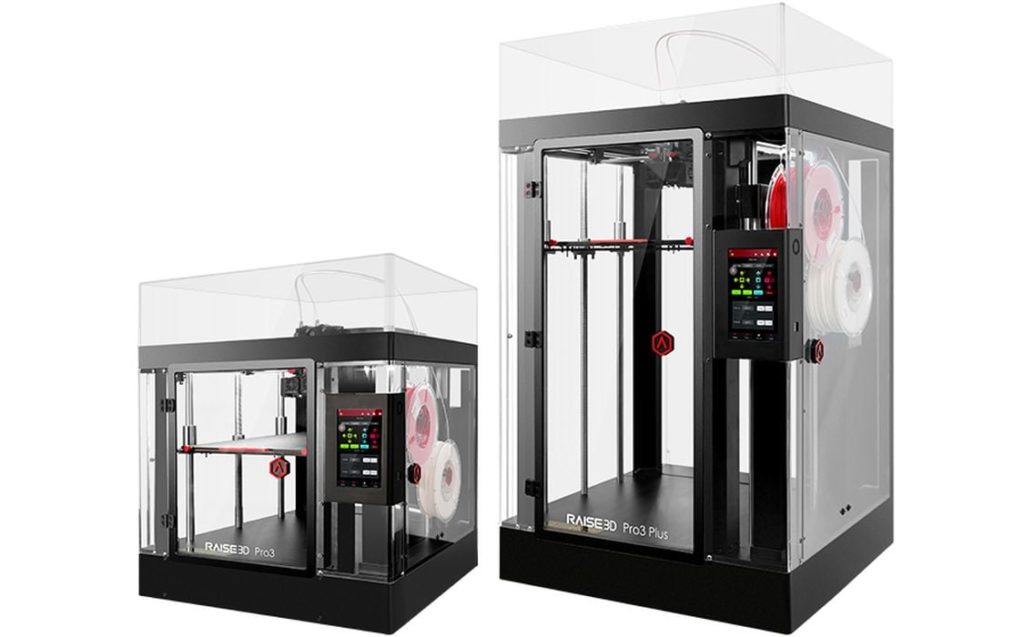
Fabbaloo: The Pro3 Series is also coming out, and it includes quite a number of changes from the previous Pro2 Series. What was the overall goal in the Pro3 redesign?
The market reaction to the Pro2 Series was very positive, but we had recurrent feedback about how it could better suit manufacturersā needs if usability were slightly improved in some areas. And thatās pretty much where we kept our focus. Usability is even better in the Pro3 series, by incorporating easily replaceable hotends, auto bed-levelling, and virtual smart assistant EVE, but also the overall printer hardware has been improved, thanks to a lighter extruder and cable chain system, and increased strength in the Z-axis.
Fabbaloo: How important is the software ecosystem around the Pro3 Series? What have customers and testers been telling you?
Since the beginning of Raise3D, our goal has been to develop a powerful and smooth software experience for our customers, and we have evolved and expanded both our expertise and the solutions we provide. As such, we can offer not only slicers and cloud platforms, but also make available additional tools to bring to our customers even more value. In addition to other innovative features such as remote operating, assisted calibration and power-loss resuming, our core software, ideaMaker, is constantly updated with improvements and new features. The on-board control system of each printer, RaiseTouch, is also an important component of our software ecosystem.
Most of our customers and testers find our software to be easy to use as well as quick to learn. As they use it more and more, they discover its advanced features and how they can do so much more within a single program, from dividing a model into parts to changing its geometry or adding a user-defined pattern to be the surface texture.
Fabbaloo: Is it possible to operate an array of Pro3 Series equipment with RaiseCloud? How difficult is that to set up?
Sure. We already have quite a few customer operating farms that have an array of our printers, and the Pro3 series won’t be any different. The setup is very easy, it’s just a matter of registering your account and then scanning the QR code on the printer’s cloud menu using our smartphone app. You are then ready to go. If you are not using a mobile device, you can download then encryption key file generated on your dashboard, copy it onto an USB drive and finally, insert it into your printer. That’s it.
Besides than that, we also have available an Octoprint plugin for RaiseCloud, meaning you can use it with printers from other manufacturers.
Fabbaloo: Other 3D printer manufacturers are building databases of print parameters for specific materials. Is this functionality also available in the Raise3D ecosystem? How does it work with third party materials?
We do believe to have a better system, because we are closely tied to our community. Our profile library site: ideaMaker.io, is where you can easily access printing profiles and textures. With the live access function from ideaMaker software, you can send any profile from your browser directly to the slicer. That means you don’t have to wait for the update from the slicer software to get access to a newer database, you can always stay up-to-date. It’s also a free and open platform, just like ideaMaker itself, meaning you can easily find profiles and settings for third-party materials and printers.
Fabbaloo: The Air Flow Manager is an interesting feature. Is it able to hold the entire build chamber to a specific temperature? How important is that to achieving high print quality?
A lot of our customers told us that they wanted the air flow manager to be able to heat the chamber, but unfortunately, the current manager doesn’t control the temperature accurately. We will keep listening to the market’s feedback, and we will definitely evaluate this feature when designing the second-gen Air Flow Manager. Its main jobs right now are to equalize the temperature inside the chamber, giving the user the option to introduce external cooling, and to filter particles and emissions during the printing stage. For some of the large technical material parts, especially on the Plus model, if the top and bottom have a big difference in temperature, this can lead to cracking. Also, to print filaments such as PLA in a fully enclosed chamber, extra cooling would be needed to get better printing quality. So this gives users the chance to change the heating state inside the chamber, whereas this was not possible before.
Fabbaloo: What is the pricing and availability for the Pro3 Series?
The Pro3 is 4,749⬠in Europe and $5,249 in the US and rest of the World, while the Pro3 Plusā price is 6,249⬠in Europe and $7,249 in the US and rest of the World.
Pre-sales started on the 1st of November, and deliveries are scheduled to start in December.