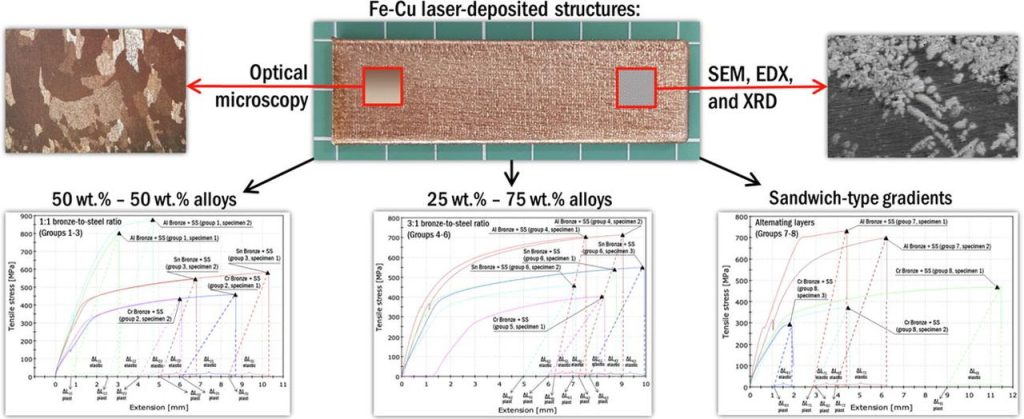
A new research paper describes a method of 3D printing copper and steel within the same job.
There are now many metal 3D printing options on the market, and several different 3D printing processes. One of them is DED, where material is sent through a printhead equipped with a laser to instantly melt the material. Sometimes this is done with metal wire, but it can also be done with metal powder, which is the form used by this research paper.
The paper, entitled, āMechanical characteristics of laser-deposited sandwich structures and quasi-homogeneous alloys of Fe-Cu systemā, examines methods of overcoming a persistent issue in metal 3D printing: alloys.
Alloys are incredibly important, because they allow the mixing of different properties to create new materials that best match an application. Most often the alloys are prepared ahead of a print job, and simply supplied to the 3D printer as a homogenous material.
But sometimes you canāt do that. For example, copper and iron donāt really mix well because they have drastically different melting temperatures, and the copper is highly reflective, whereas the iron is not. The researchers explain the problem:
āThe direct joining of Cu and Fe using the laser metal deposition (LMD) appears to be unrealizable because of a substantial positive enthalpy and significant difference between thermomechanical (melting point, laser radiation absorption coefficient, heat conductivity, thermal diffusivity, thermal expansion coefficient, elasticity modulus) and microstructural (crystal lattice parameter) characteristics of these materials. These factors lead to the limited miscibility of Cu and Fe and result in undesired effects such as embrittlement due to formation of the brittle phases, intense liquation and solidification cracking, overheating of the material with a lower melting point, formation of stress and strain concentrators and residual thermal stresses.ā
Here the researchers attempted to make āquasi-homogeneousā alloys by directly controlling the mix of input materials during printing.
This was accomplished by using two separate powder hoppers and independently controlling the flow of powder to the nozzle. In their experiments, the researchers used bronze and steel powders in each of the hoppers. They experimented with various approaches for modulating the ratio of materials to see what happened.
Specifically, they attempted:
- Creating an intermediate section of a supplementary material between the two misbehaving metals
- Alternating very thin layers of each material
- Creating a āgradientā of materials where the ratio would slowly change as layers increased
The researchers used a robotic setup with two powder feeders to produce three types of metal specimens using this approach with a variety of different printing parameter combinations and additives:
- Non-gradient sample with 50-50 material ratio
- Non-gradient sample with 75% bronze
- Gradient sample with alternating bronze and stainless steel layers
The results showed a variety of responses when mechanically testing the specimens. However, they definitely were able to produce usable structures that exhibited some of the predicted effects, such as increased ductility and strength.
Specimens tell only the beginning of the story, however, as there are significant potential uses for this approach. They explain:
āMoreover, not only gradient structures are our objects of interest. Bimetallic non-gradient Fe-Cu alloys also have a wide field of practical applications due to copperās significant influence on steelās mechanical properties. In particular, it is possible to increase the creep strength of low-carbon austenitic steel by including 4 wt% copper in its structure,along with reducing the materialās ductility. The temperature strength of austenitic steels in the area of ā¼ 650ā750 °C can also be improved by the addition of Cu. Additionally, binary Fe-Cu alloys are interesting in the light of improving an infrared laser radiation absorption coefficient (and, in addition to that, heat consumption) of bronze by alloying it with steel dopants.ā
Materials for 3D printing continue to improve.
Via ScienceDirect