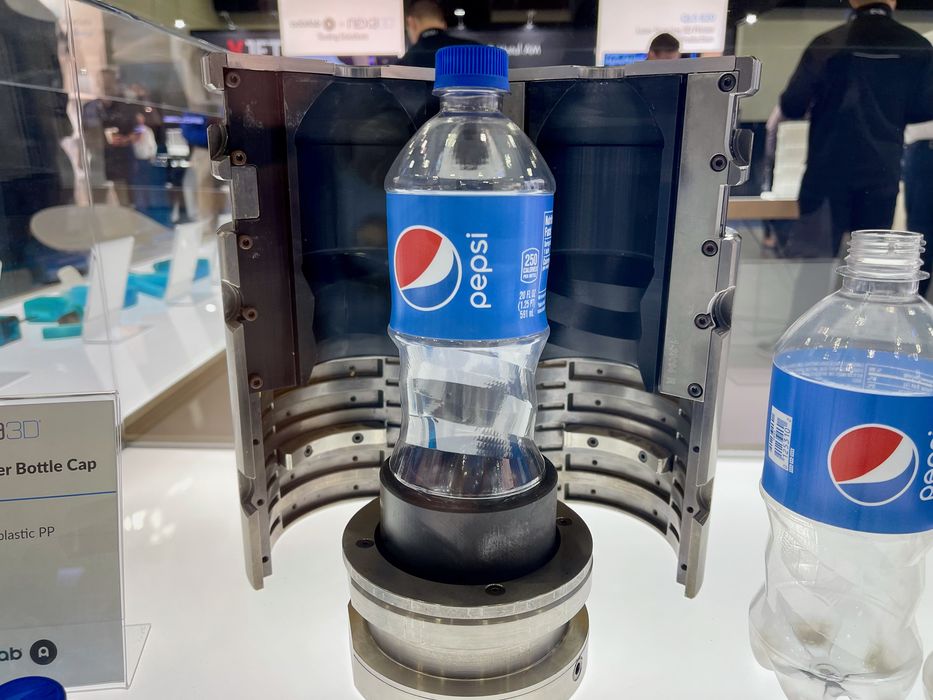
Charles R. Goulding and Preeti Sulibhavi examine how PepsiCo was able to leverage advanced 3D printing technology.
On July 28, 2022, Nexa3D hosted a webinar titled, “The Pepsi (3D Printing) Challenge.” It was hosted by former Fabbaloo editor, Sarah Goehrke (now Senior Director, Strategic Communications and Ecosystems, Nexa3D) and featured the following panelists and speakers:
- Max Rodriguez – Sr. Manager Global Packaging R&D, PepsiCo
- Thangtip Tekanil – R&D Packaging Engineer, PepsiCo
- Hratch Gasparyan – Director of Enterprise Solutions, Dynamism
- Sam Bail – Director of 3D Printing and Partnerships, Loctite / Henkel
We saw how 3D printing has helped improve the manufacturing processes at a large company such as PepsiCo, with so many brands and product lines. Questions came up during the discussion that included how Pepsi’s molding process has changed over time and how the current combination of Nexa3D NXE 400 with Henkel xPEEK147 compares with previous methods.
We learned that PepsiCo is automating CAD software to achieve new designs in only minutes. Using Lubricant Sublayer Photo-curing technology (LSPc 3D Printing) from Nexa3D, PepsiCo is able to complete high-speed resin printing. PepsiCo is 3D printing plastic inserts for their blow molding technique that can be used multiple times. The Nexa3D NXE 400 and PepsiCo’s partner, Dynamism, helped achieve this success.
Henkel Loctite is their go-to for materials and resins. xPEEK147 (Polyether Ether Keytone), used by PepsiCo, is a high HDT230 resin that was selected because it had excellent dimensional stability, good surface finish, and of course, high heat resistance. It is a tooling and molding application that allows end-users, such as PepsiCo, to achieve high-resolution print definition and detail. xPEEK147 also has chemical compatibility with industrial chemicals such as traditional ABS plastics, motor oils, acetones, and APAs, among others.
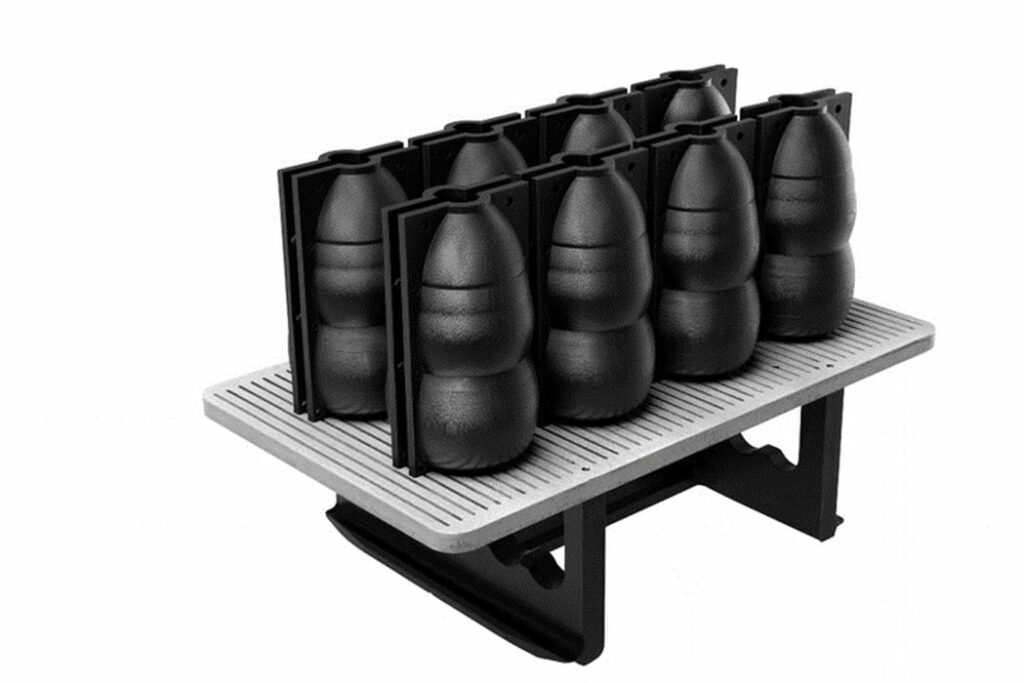
The R&D team at PepsiCo discussed how prototyping toolset costs had been reduced by 96% (US$350 versus US$10,000 for mold sets) since using Nexa3D for its printers. In addition, there was a time reduction of 93% (mold sets are ready in 48 hours as opposed to 4 weeks). These metrics were derived from comparing metal blow mold tool sets of 10,000 samples to the Nexa-Henkel combination discussed.
Max Rodriguez, Senior Manager, R&D, Global Packaging at PepsiCo, stated that “AM allows PepsiCo to improve on internal processes….to modify iterative processes….so that manufacturing processes can achieve better results..” with fewer errors and costs. He also indicated it improves their global supply chains as well.
PepsiCo had spent the last five to six years developing blow-molds. In the beginning, they had been using FDM 3D printers with carbon-enforced filament. Prior to that, they were machining their mold sets. In the last 3 years, Henkel started to support PepsiCo with materials and photopolymer technology advancements.
The Research & Development Tax Credit
The now permanent Research and Development (R&D) Tax Credit is available for companies developing new or improved products, processes and/or software.
3D printing can help boost a company’s R&D Tax Credits. Wages for technical employees creating, testing and revising 3D printed prototypes can be included as a percentage of eligible time spent for the R&D Tax Credit. Similarly, when used as a method of improving a process, time spent integrating 3D printing hardware and software counts as an eligible activity. Lastly, when used for modeling and preproduction, the costs of filaments consumed during the development process may also be recovered.
Whether it is used for creating and testing prototypes or for final production, 3D printing is a great indicator that R&D Credit eligible activities are taking place. Companies implementing this technology at any point should consider taking advantage of R&D Tax Credits.
Conclusion
What PepsiCo has accomplished with 3D printing is a lesson we can all learn from. PepsiCo has used a team from a host of different industries to see what processes would work best for PepsiCo as the end-user. As demonstrated during the insightful webinar, the results speak for themselves.