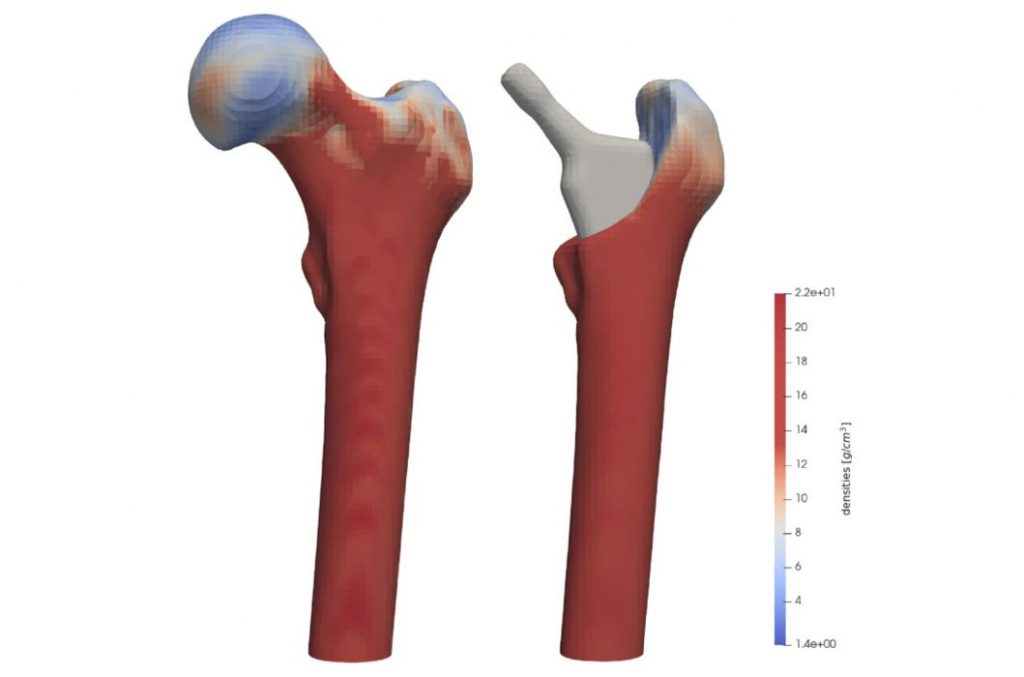
New research shows a way to optimize human 3D printed implants for more personalized microstructure.
The research, undertaken at TU Delft, examined a problem caused when implants are used: they generate different forces on surrounding bones. They explain the challenge and their solution:
“These devices, which are typically made from fully solid materials, significantly alter load transmission to the surrounding bone tissue, potentially leading to interface instability and bone resorption. In this work, we present computational methods to synthesize three dimensional (3D), patient-specific, implants with heterogeneous micro-architecture. Our method simultaneously minimizes the risks of load-induced interface fracture and peri-prosthetic bone remodelling, while taking into account functional and manufacturing constraints.”
The root of the problem is that the implants are typically made from 3D printed materials that are far harder than natural bones. Hip implants, for example, are typically made from titanium or similar metals that are more stiff than bone.
This causes new stresses within the bones near the implant, and this in turn causes the body to slowly deposit or absorb bone material in affected regions, which can lead to chronic conditions.
The solution, one would think, is to include software materials in the implant to form a buffer between the stiff metal and natural bone. However, that introduces other problems, and is the reason for the research.
The new approach involves a detailed FEA analysis of the bone / implant site and adjustments to the implant’s microstructure. The adjustments are intended to compensate for the change in forces, and thus reduces the risk of interface fractures.
They explain:
“In this work, we propose a gradient-based numerical optimization methodology to automatically synthesize 3D micro-architected implants that simultaneously minimize the risk of interface fracture and implant-induced bone remodelling. The procedure decouples the micro-scale unit-cell geometry from the macro-scale design problem, allowing for the efficient inclusion of manufacturing and/or application-related constraints, while significantly reducing the computational costs compared to concurrent multi-scale strategies.”
This is an interesting development that will clearly improve the welfare of implant patients. But it’s also a pattern we’ve previously seen with mechanical parts.
Today many production parts are manufactured with additive processes that do very much the same process: forces are analyzed and the part’s design is modified to account for those forces. The resulting part can be minimized to just what is needed to accomplish the part’s requirements.
Here we see that approach being used for implants, which for all intent and purposes become part of the patient’s body.
Looking from a higher level, this approach could be the way of the future for additive manufacturing: if each print job could produce a fully optimized part that is customized for the intended use, why don’t we do so?
Today’s 3D printer hardware is already capable of achieving this. The problem is that the software we use to design and create parts is not easily able to do so. Perhaps research of this type will trigger thought among software producers and 3D printer manufacturers to consider the idea of continuous customization.
Via Science Direct