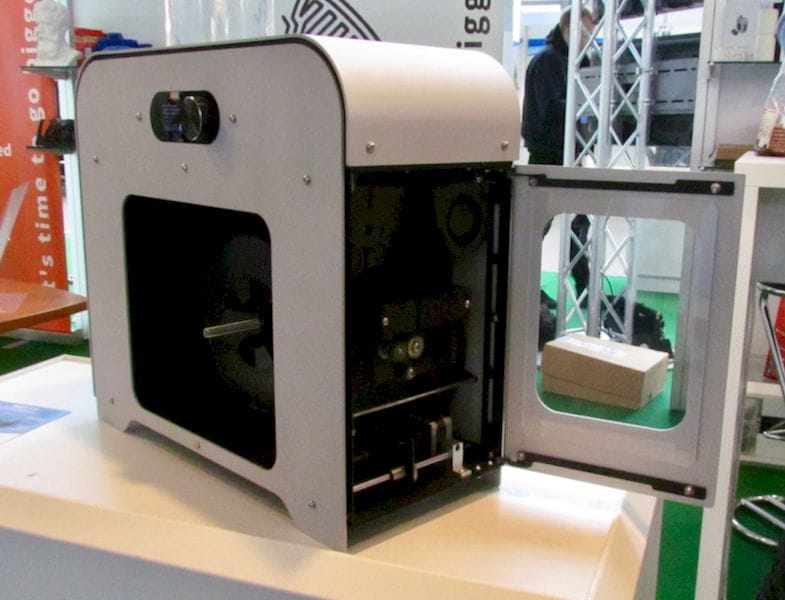
This week’s question relates to the idea of making your own 3D printer filament.
Fabbaloo reader James asks:
“The extrusion bot. Is this still available somewhere if so where? Plus by chance do you know of any shredders that are priced decently for a 3d printing hobbyists?”
To start, let’s discuss the ExtrusionBot project. It was launched as a Kickstarter way back in 2014, and the idea was to grind up your old 3D prints and recycle them into fresh filament for use in your 3D printer.
It’s a good idea, but vastly more challenging than anyone then imagined.
ExtrusionBot failed, and today their website looks like this:
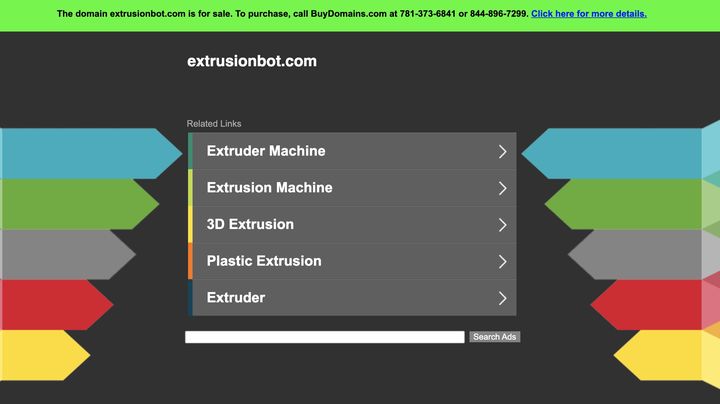
They discovered, as did several other eager entrepreneurs, that making truly printable filament is far more challenging than simply squirting out wet plastic.
The problem is that the filament produced must be of sufficient quality to 3D print. This means that it must be:
- Of consistent diameter
- Of consistent round shape
- Made from the same chemistry
- Free of moisture or other pollutants
- Neatly wound on a spool for use
And as a bonus, it might have a consistent color, but that may not affect printability.
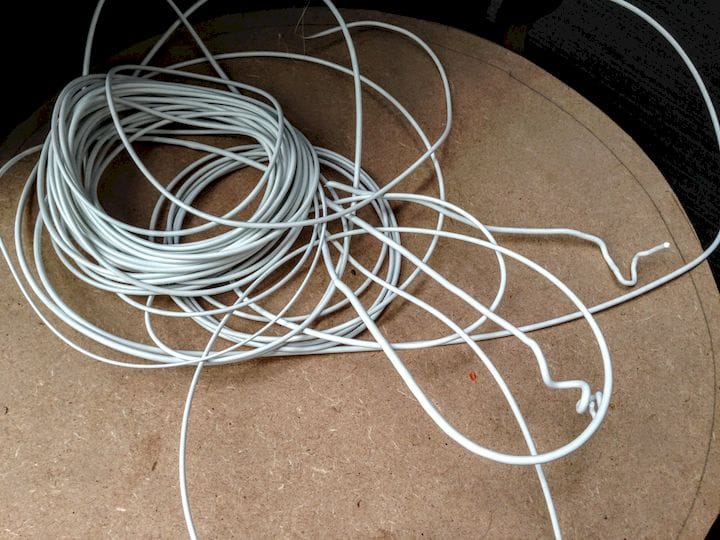
Early filament makers such as the ExtrusionBot didn’t account for these factors. One example I witnessed at an early 3D print tradeshow was simply spilling freshly extruded filament onto the floor in a spaghetti-like pile. Sure, there was filament there, but it was literally unusable. I never saw that company again, and one can guess why.
True filament production requires extraordinarily precise methods. In order to achieve the correct diameter and shape, the speed of extrusion must be carefully determined through real time measurement and parameter adjustment. Modern machines use laser-powered sensors to determine filament diameter and geometry. Once these parameters are locked in, the filament must be quickly, but gently cooled otherwise it will loose its precise shape and dimensions.
In a production line this is most often done with a long water bath that’s at a precise temperature. As the new filament passes through this bath it cools at the correct rate. When it emerges it can be spooled up, but it’s also full of moisture. This means you have to dry the filament using yet another step in the process.
Now the big question: how do you achieve all this in a simple desktop extrusion device?
There’s many steps involved, including:
- Sourcing consistent input material
- Shredding input material to a consistent size
- Feeding into the filament extruder
- Heating and extrusion
- Measurement and feedback
- Cooling
- Drying
- Spooling
- Storage
Note that shredding is an explicit step in this process, and it has its own special requirements. The shredder must produce bits that have a maximum size in order to fit through whatever recycling system you’re using. In other words, the shredder must match the filament extruder.
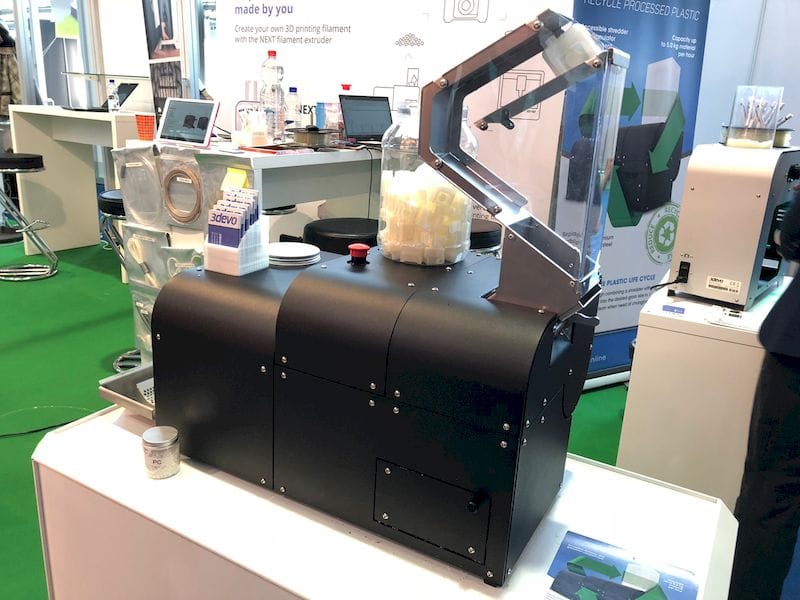
The need for precision 3D printer filament is now higher than ever. As today’s 3D printers strive for the highest quality 3D prints, they can only achieve this through the use of precision input filament. In fact, many machines today use pre-made print profiles that match the machine with a specific filament product from a specific manufacturer. That’s the only way to truly optimize the quality.
This is one of many reasons I’ve seen almost all of the desktop filament machines fall to the side. That and an uncanny preponderance to completely ignore the issue of spooling, as described above.
These days I know of only one practically useful desktop 3D printer filament production system that attempts to solve all of the required issues, and that’s the equipment from 3DEVO. At top you can see an image of their machine.
The company has been around for many years, and thus it’s quite true they’ve solved most of the problems. They have solutions for shredding, measurement, spooling and more, and it works. I’ve seen it with my own eyes. We wrote about the 3DEVO NEXT machine here, and also about their expansion to North America.
Some may find the price of their equipment to be high, but that is actually the cost of doing the job properly.
If the 3DEVO option is too pricey, then we have to ask the question: what are we trying to achieve by recycling 3D prints?
If we’re trying to lower the environmental cost of 3D printing, then one must consider the entire eco-cost of the operation, including energy used to recycle, cost of recycling equipment, etc., and I suspect in the end there’s really not much to be saved, unfortunately.
On the other hand, if we’re trying to save money, that’s not really possible. The cost of properly recycling filament is near the same as buying inexpensive new filament after all is accounted for.
When speaking with 3DEVO, it turns out that most of their clients use the system not to save money, but in fact to produce unusual and new filament combinations that aren’t on the market. With that equipment you can play with colors, additives and composites. It’s not to save money on filament.
The best way to save money on filament is to find the lowest cost product, it turns out.