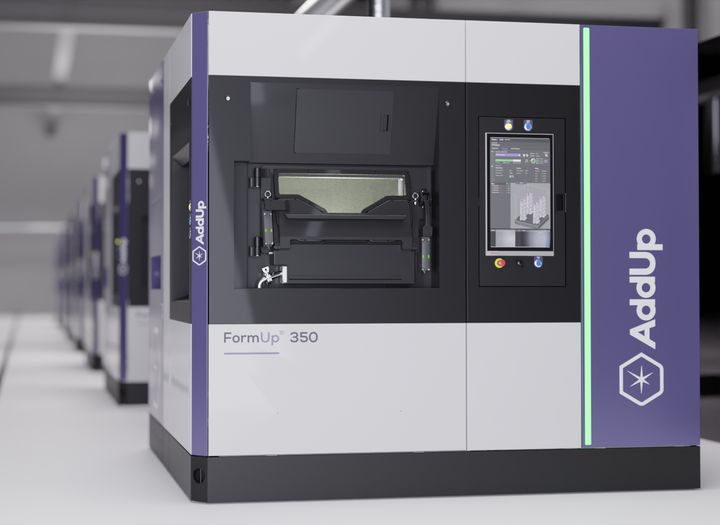
AddUp announced a new metal 3 printer, the FormUp 350, and it includes quite a number of unusual features.
AddUp is a joint venture of France-based Fives and Michelin, who have been using metal 3D printing in their operations for many years. In 2016, the two decided to create AddUp to design and deliver advanced AM technology to industry.
There are now many different metal 3D printers on the market, and most use the LPBF approach, in which a powerful laser selectively sinters fine metal powder, layer-by-layer. In concept this is straightforward, but in practice it is ever-so complex as there are many factors that must be correct to achieve successful 3D prints.
The new FormUp 350 includes quite a few very interesting and unusual features, perhaps more innovations I’ve seen on a LPBF machine for quite some time.
One of the most interesting, and perhaps the most important features from a safety standpoint, is a new “automatic passivation” filter system.
LPBF 3D printers often have a problem with condensate. This is formed as the inert gas in the build chamber is continually filtered, collecting metal particles. Eventually, a large amount of condensate will be produced and must be disposed of. However, the condensate can be flammable, creating a fire hazard. This makes it expensive to deal with, and unfortunately some AM shops simply store condensate in an unsafe manner.
The FormUp 350’s passivation filter seems to neutralize this effect. They explain:
“Exposure to fumes and smelting residues is controlled, using an automatic passivation filter system that ensures safe waste disposal. The passivation of soot and powders recovered during filtration is done by adding a calcium carbonate powder. This removes the risk of flammability from the waste and it can be processed safely.”
I don’t believe this approach has been done on other LPBF 3D printers, but I stand to be corrected. Nevertheless, this feature makes the 350 much safer to operate.
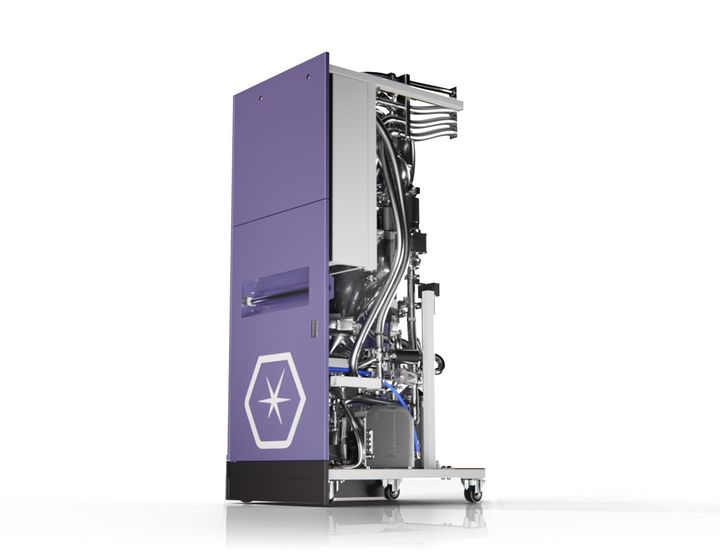
Like many other metal 3D printer manufacturers, FormUp has developed a seamless powder management system to be used with the 350. They said:
“Operators will be able to work in complete safety using an innovative autonomous powder module developed exclusively with the AZO company, ensuring the storage, conveying, recovery and sieving of the powder, with all operations being carried out automatically in a closed circuit in an inert atmosphere.”
Beyond safety concerns, AddUp has added several features to increase the quality and reliability of metal 3D printing on the 350.
One feature is an automated recoater check, in which each fresh layer of powder is optically inspected in less than a second. Should the system detect any deviations in the surface, it instructs the recoater to run a second time. That should eliminate recoater problems in a way that is not done on most LPBF systems.
The FormUp 350’s recoater is interesting in another way: it’s interchangeable. One of the difficult problems in LPBF 3D printing is that certain material powders tend to work best with certain types of recoater mechanisms. Unfortunately, most LPBF 3D printers usually have only one mechanism type permanently installed. However, the FormUp 350 allows you to use either a blade or roller to account for the best possible outcome.
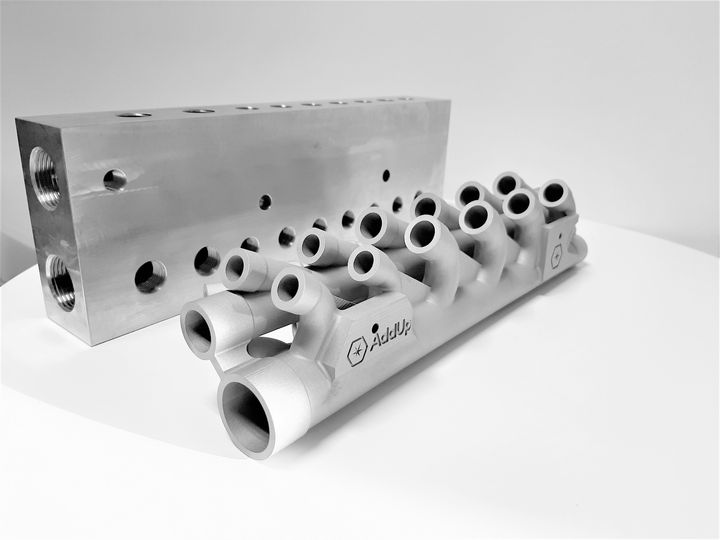
The FormUp 350 is also quite productive, as it includes four separate lasers, each 500W. These can each sweep the entirety of the build chamber, meaning they can work in parallel on even the smallest objects. This is unlike some other multi-laser systems in which lasers are dedicated to specific zones and cannot “help” on an object that is within a different zone.
AddUp has redesigned the sealing of the FormUp 350’s build chamber to ensure it can be purged to 500ppm of oxygen within only 15 minutes. This should speed up print start times.
The company has also beefed up the AddUp NCore software on the FormUp 350 substantially. The system can now compute 1.27M laser trajectories per second, which they say is “1000 times faster than real production”. This suggests that handling complex objects should never be an issue with the FormUp 350. They say they can process 80GB production files without issue, and that’s pretty impressive.
There’s plenty more innovative features on this very interesting metal LPBF 3D printer.
Via AddUp