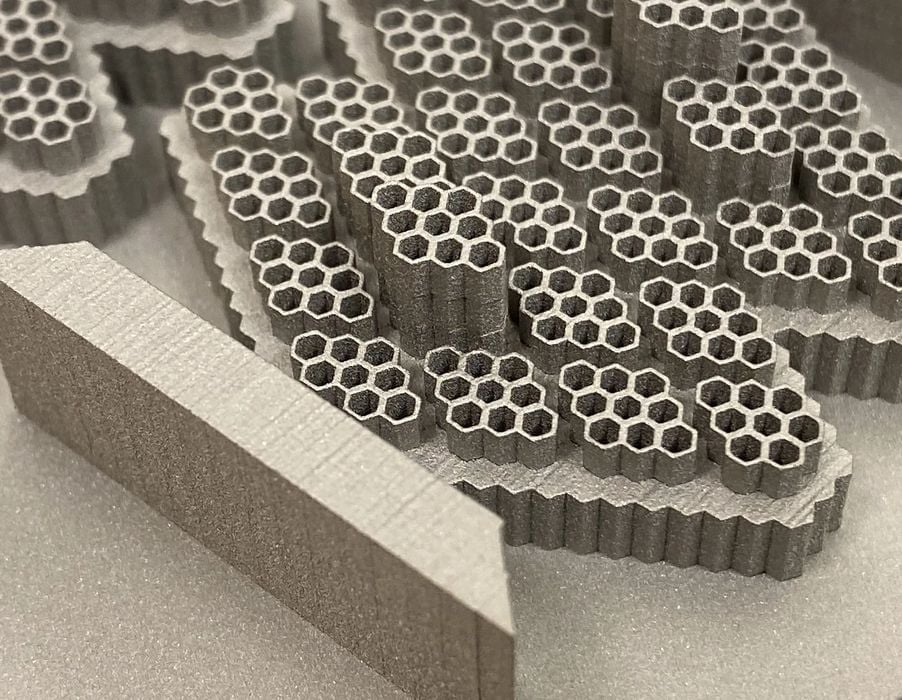
Seurat published a page explaining much more about their fascinating new “Area Printing” concept.
Actually, I shouldn’t call it a “concept”. In fact it is a real 3D printing process they have perfected and have built into products that are new being used on customer projects.
If you haven’t heard of Area Printing, it is an incredible concept that is far more powerful than traditional LPBF 3D printing. In LPBF approaches, a laser tediously sweeps across a flat bed of powder to gradually sinter solid portions of an object layer. This repeats, layer-by-layer until the object is built.
In Seurat’s Area Printing they have instead split the laser up into multiple beams and can process a large “area” simultaneously. This will dramatically speed up the printing process, to the point where it could become cost competitive to traditional metal working processes, such as casting.
In my previous interview with Seurat CEO James DeMuth, it was revealed that the inspiration for Area Printing was derived from his work on components for nuclear fusion experiments. In other words, very advanced stuff.
But how, exactly does this work? A new infographic on Seurat’s website explains the process in a lot more detail. Let’s take a look at the steps involved.
The first step is the laser source. Seurat uses a pulsed laser, which can produce intermittent higher energy levels. The beam is “shaped” to create a square illumination field.
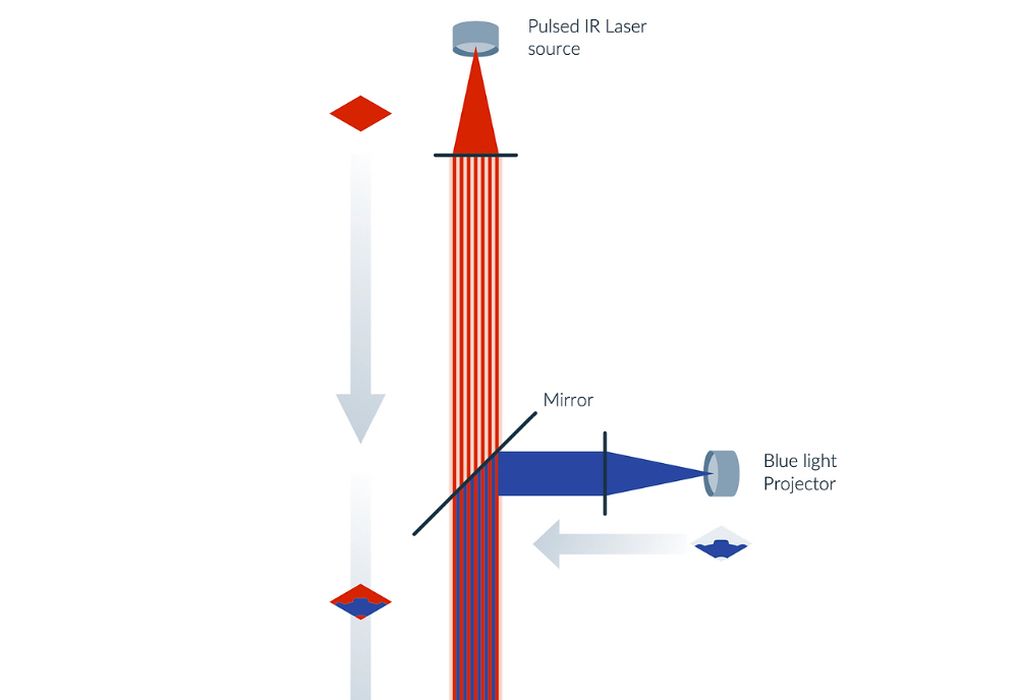
The second step adjusts the beam field by injecting a blue light image of identical dimensions with a mirror system. This image represents the area to be sintered.
The third step involves polarizing the mixed light beam through an optically addressable light valve. This polarizes the light where the two colors are not overlapping, creating the possibility for beam separation.
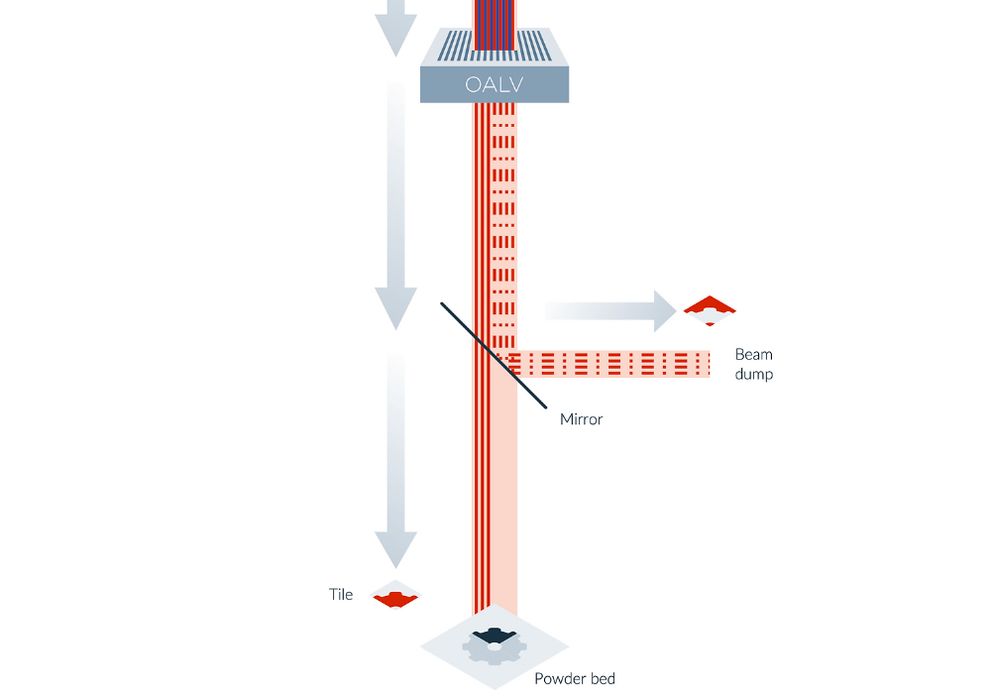
The final step is to split the beam with a polarized mirror: polarized goes one way, unpolarized goes the other way. This sends sintering light energy forward to the build layer, while shunting unnecessary sintering energy to the “beam dump”.
It’s a fascinating process where we can now all understand how this system works.
One obvious question is that if the energy is strong enough to sinter metal, why doesn’t it melt these mirrors and light valves? Shouldn’t the machine eat itself before it gets going?
The answer is in the quality of the components. DeMuth told me earlier that a large part of their process development was to source — or eventually make their own — high quality components. These are so near-perfect that almost no stray energy goes to where it should not, and the system works.
This “stack” produces a sinterable area about 100mm square. That’s not so big on its own, but imagine a system that can move the sinter area step by step. That would certainly enable production at a rapid pace. Another possibility is to develop a machine with multiple of these stacks.
The “dots” within the printable area are quite numerous, as the current Area Printing technology can achieve “10 features per mm”, but will eventually scale to 20 features per mm, and print up to 1700kg of material per HOUR. Amazing stuff!
Seurat also published this table showing the engineering characteristics of metal samples made with Area Printing. As you can see, it seems to do the job.
That’s the vision of Seurat: produce a 3D printer capable of incredible speed — and therefore able to produce low-cost parts. That’s the secret that could eventually enable them to take over the manufacturing market.
Via Seurat