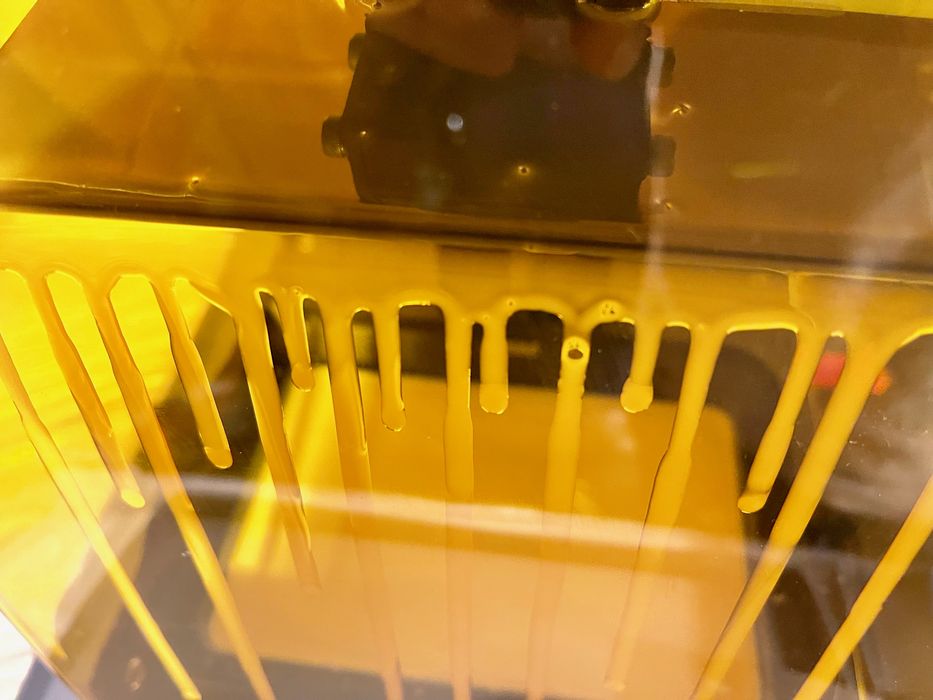
Here are my thoughts on seven completely new features I’d like to see on desktop resin 3D printers.
I’ve been doing a lot of resin 3D printing lately for some reason, and I’ve got my own process nailed down for doing it without making too much of a toxic mess, but along the way I keep thinking of ways to make the experience a lot easier.
Resin 3D printing, while providing outstanding results, is more complicated operationally than typical FFF 3D printing, and adds in the risks of handling toxic material at the same time. For this reason individual desktop 3D printer operators typically start with the easier FFF systems, and then move on to the resin equipment.
If there was a way to simplify things for resin 3D printer operators, I’m all for it. But what could help? Here are seven ideas that might do so.
Resin Tuner
Some believe you turn on the resin 3D printer, pour in some random resin, use the settings on the resin bottle and you’re good to go.
That will almost certainly not work. Resins must almost always be tuned to the machine. While some resin systems use proprietary materials that are “known” to the system, the vast majority of inexpensive desktop resin systems are “open materials” and there is no way for the printer to know what’s been poured into its vat.
The result is that you must “tune” the parameters to match that specific resin to the that specific 3D printer. This is done by repeatedly 3D printing a test object and inspecting the results. If you do so, you will be almost guaranteed to get fantastic results.
But how many resin 3D printers really do this? Many certainly do, but I have a suspicion a lot of people just use the specs on the bottle. This is usually ok for a starting point, but those parameters are necessarily set to be highly conservative by the manufacturer. It’s best to tune your own parameters.
The idea is to embed the 3D printer with a “resin tuner”. This would be a kind of “wizard” system that would guide the operator through a sequence of quick prints to dial in the resin parameters. The test object could be stored internally on the machine, and the touchscreen could show what to look for in the results. It could even ask yes or no questions and automatically set up for the next test. When done the machine could present the tuned parameters to the operator for use in the software slicing system.
Weight Sensor
How much resin is left in that vat? Normally you have have absolutely no idea at all. Even on machines with level-lines on the side of vat it’s almost impossible to tell. This is critical information because a print might run out in mid-job, causing a print failure and wasting expensive resin.
The idea here would be to implement a weight sensor on the vat that could tell very precisely the amount of material remaining in the vat.
Because the vats are typically tightened down with bolts, this idea may require a magnetic attachment so that the weight sensor could properly gauge the amount of resin remaining.
Print Plate Housing
It’s almost always a sloppy, toxic job to extricate a finished resin print from the printer. I’ve noticed, however, that most of the drips are not from the model, but instead from the top of the build plate, which often is submerged in the deep resin vat during printing. Some equipment has lots of nooks and crannies that hold resin, only to let it loose when you tip the plate. The better plate designs have smooth sloping sides to at least make it a bit easier to paddle off the resin.
My idea is to redesign the plate housing so that there are steep walls that are at least the height of the resin vat. This would prevent resin from washing over the top of the plate and making a mess after printing. This should be a relatively easy change.
Integrated Pouring Funnel
When a resin 3D printer has to change material there is almost always some resin left in the vat that must be poured out. This is another step where toxic messes can easily occur. The better vats have a slight indentation in one corner that is intended to use for pouring. This makes it somewhat easier, but I think a better design could be made.
Why not adapt the vat design to fit more easily into a funnel system? Why not include a universal funnel with each resin 3D printer that fits properly on the vat and avoids drips entirely?
Automated Plate Tipper
After a resin print job completes the plate is raised for removal. Inevitably, the print and plate are coated with leftover liquid resin. If you leave the print job alone for a sufficient time, much of this resin will drip off automatically.
But the only resin that drips off is that which is not horizontal. Resin on horizontal surfaces simply waits for you to accidentally drip it on the floor.
The idea here is to have a system to automatically tip the plate a couple of directions after printing to allow for drips to occur from different sides. The degree of tip does not have to be much, and this would likely require another motor in the system to make it a bit more expensive.
But it would be far less messy.
Total Wipe Industrial Design
Every desktop resin 3D printer I’ve used is soiled by accidental drips. Sometimes these drips fall on smooth surface, where they are easy to wipe off with an IPA-soaked cloth. However, in many systems there are all kinds of crevices in which resin cannot be easily removed, should it fall in.
Why not design a desktop resin 3D printer with a “total wipe” design. This would include smooth surfaces everywhere so that cleaning could be far easier.
Filtration System
This is actually included on some more advanced systems, but should be on every system. Many desktop resin 3D printers include a cooling fan because the light engines tend to get warm and that heat can disturb the chemical reactions during printing. But that same fan also blows air and odors into the nearby area.
The idea here would be to include a proper filtration system on any desktop 3D printer equipped with a fan. This would not only smell a lot better, but reduce potential exposure to toxins.
That’s my list of seven hardware changes that I’d like to see on desktop resin 3D printers. Do you have ideas you’d like to see manufacturers implement? Let us know in a comment!