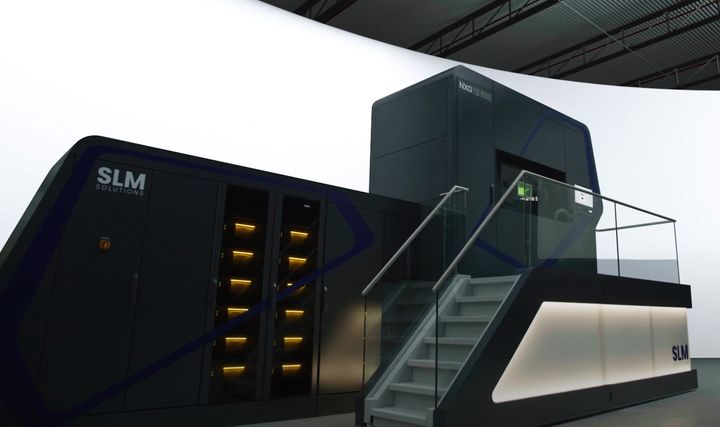
SLM Solutions has released a breakthrough metal 3D printer, the massive NXG XII 600.
I’m not quite sure where to start on this device, as it includes so many revolutionary features it’s almost like a new class of device. Meddah Hadjar, CEO of SLM Solutions, said:
“We have unveiled a miracle.”
He may be correct.
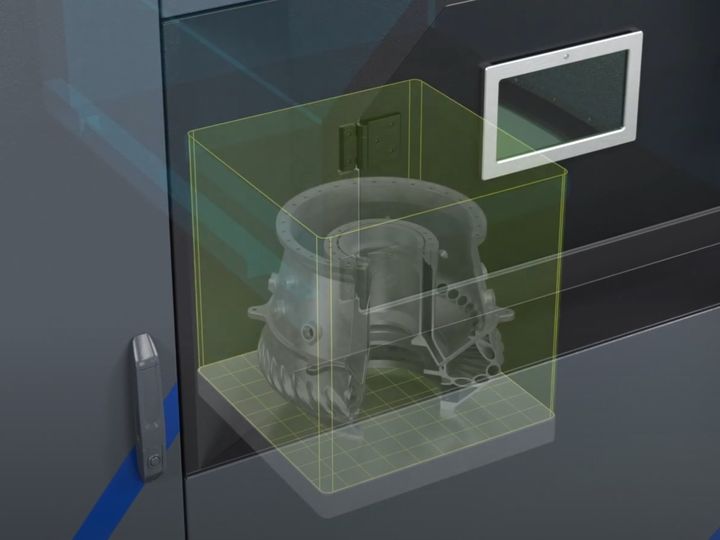
At its core, the NXG XII 600 is a metal 3D printer with a very generous build volume of 600 x 600 x 600 mm. That alone is notable, as it’s one of the largest build volumes you can get for a proper PBF metal 3D printer.
But it turns out the NXG XII 600 has multiple other astounding features that will no doubt place it in applications never seen previously in additive manufacturing.
12 Lasers
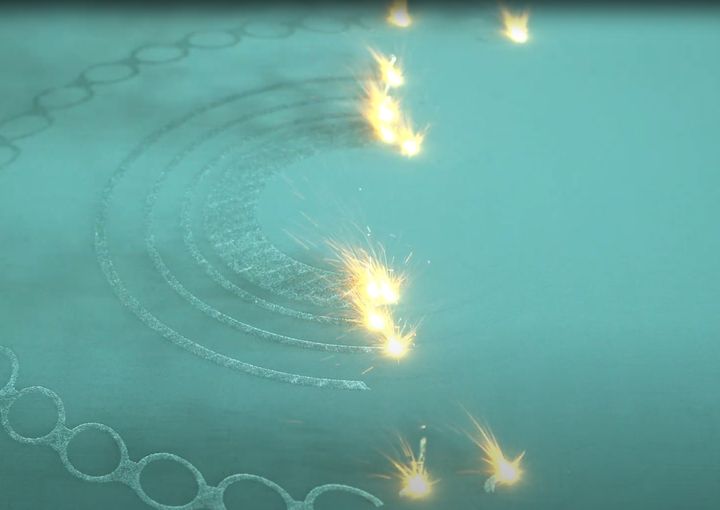
There’s a bit of a giveaway in the product’s name, “NXG XII 600”. The “600” obviously refers to the build volume dimension, but the “XII” refers to the TWELVE 1kW lasers in this system.
Yes, twelve. Not two. Not four. TWELVE.
Other companies had previously sought to speed up 3D printing operations by using multiple lasers, but the maximum seen in any other system up to this moment has been “only” four. In a sense you could approximate the speed increase by dividing the build time by the number of lasers. Four lasers gets you 25% of the build time.
Now the divisor is twelve, not four. This means that the number of lasers alone will dramatically speed up long-running builds.
But that’s not all. SLM Solutions did not merely add eight lasers to the system and the rest of the day off. No, they included a number of optimization features to make those lasers work even more efficiently. They’ve doubled the jump speed and reduced skywriting time significantly.
They say the machine can 3D print material at the rate of up to 10,000kg per year, or 20X faster than a typical single-laser PBF machine.
NXG XII 600 Tuning
There’s an indicator that SLM Solutions is stepping into new territory, as they encountered some previously unseen issues with the introduction of so many lasers.
One is the issue of laser coordination. An easy approach would have been to assign each laser to a region of the print plane. In this way they would not interfere with each other.
However, that approach would also mean the machine could not leverage all lasers optimally. A small part in only one region, for example, would use only one laser.
SLM Solutions did not use that approach in the NXG XII 600. Instead, each of the twelve lasers can reach the entire build plane, and thus can work on all object(s) simultaneously.
That sounds good in concept, but it causes another issue: coordination. You don’t want laser 5 walking on top of laser 8’s path, for example. You also don’t want laser 3 to complete its work and be idle while the other lasers continue working.
Therefore SLM Solutions found a way to equally divide the work between all twelve lasers so that all would work at the most efficient level.
But it’s more complex than that, as each laser necessarily produces spatter and smoke. Should a laser attempt to fire through some smoke, it would disturb the laser energy and reduce quality for that portion of the layer. SLM Solutions has solved that issue by developing a brand new air flow system.
The new air flow system, designed using fluid dynamics, allows for a coordination of laser firing and smoke removal that doesn’t disturb laser activities.
Coincidentally, the air flow system also is designed to work optimally with the new bi-directional recoating mechanism that places a new flat layer of powder on the bed. While some other systems have used the twice-as-fast bi-directional recoating approach, now SLM Solutions does as well.
NXG XII 600 Thermals
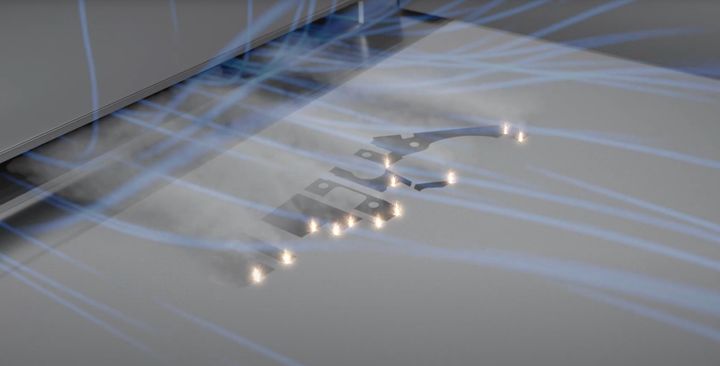
There was another challenge for SLM Solutions: thermal control.
To produce optimal 3D prints, the system must maintain a highly consistent temperature of the material and atmosphere during printing. This is challenging at the best of times, but it’s vastly more complex with the NXG XII 600.
Why? It’s because the system is beaming 12 X 1kW laser energy into the build chamber. Let’s say that again: a 600 x 600 x 600 mm region is being subjected to TWELVE KILOWATTS of energy. As you might guess, this causes a bit of heating.
Well, maybe a lot of heating.
Again, the new air flow system is designed to accommodate this, but there’s also more thermal features. SLM Solutions has developed some unusual kind of new coating on the inside of the build chamber to better control heating. There are cooling features for each individual laser as well.
This results in what SLM Solutions describes as:
“Constant substrate plate temperature independent of the laser power input.”
Impressive!
NXG XII Laser
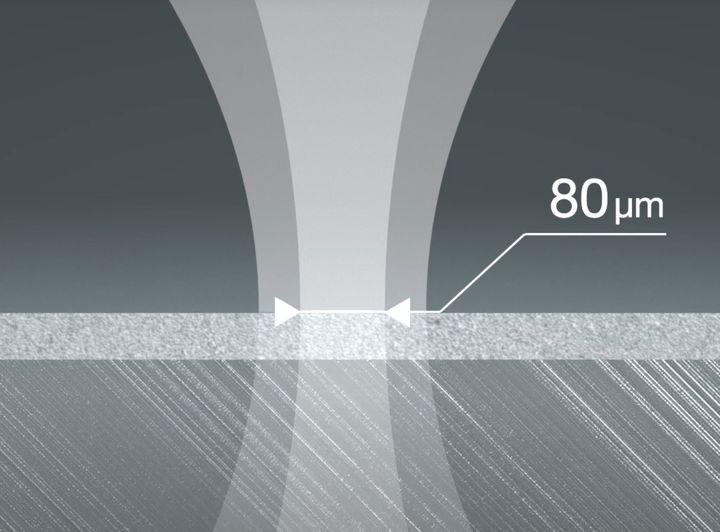
Another radical feature is the introduction of “zoom”. This is a way for the lasers to change the spot diameter, and it seems that SLM Solutions has leveraged this in several ways.
They can, for example, use a tighter spot for contours and surfaces, while using a wider spot for faster 3D printing of inner regions.
This capability also introduces changes to the ability to work with certain metals. They explain:
“Up to now it was not possible to build parts out of nickel-based alloys or steels with laser power of more than 350 Watts. The zoom functionality enables you to use increased laser power of up to 800 Watts. In these material groups we expect significant jumps in build-up rates compared to aluminum, where we already achieved very high built up rates in the past. For aluminum alloys, we expect higher build up rates, nonetheless, not only because of the use of 12 lasers.”
The results are astonishing. For example, the company showed a 15.5kg engine housing that was 3D printed in AlSi10Mg in only 21 hours!
Another example shown was an aerospace midframe weighing 120kg, produced in only 69 hours.
These are startling figures and vastly more speedy than alternative systems.
NXG XII 600 Support
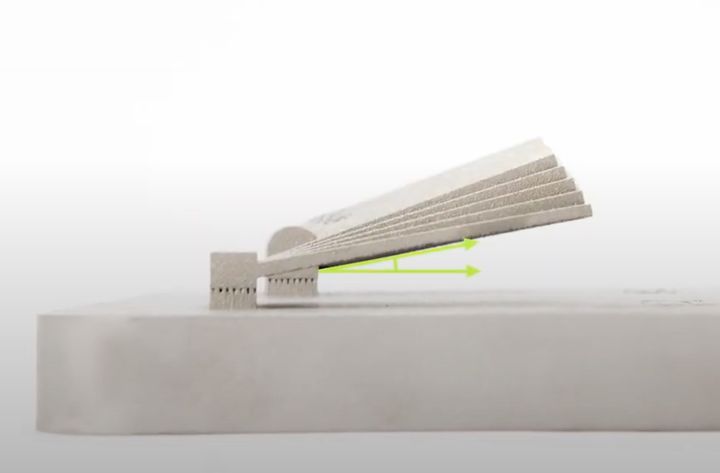
Wait, there’s even more, if you can believe it.
The precise tuning of the system has allowed SLM Solutions to perform amazing feats of overhang 3D printing. They say the NXG XII 600 can 3D print short overhangs with no support up to five degrees! That’s almost-but-not-quite-horizontal.
For longer overhangs they can handle ten degrees.
This means that objects produced on the machine will require vastly less post-processing to remove support material. This, along with the other changes above, should allow for far more economical production of parts on the machine.
In fact, SLM Solutions is billing the NXG XII 600 as a “high volume production machine”. That could be true, depending on how you define “high volume”. Nevertheless, this machine is definitely going to open up many new applications for metal 3D printing.
Here’s a video of the machine and its features:
We received no word on the price for this machine, but it will no doubt carry a six-figure price tag. Heh, to put it in perspective, if you want to fill the machine’s 216 liter powder reserve with around 980kg of titanium powder, you’ll be paying a staggering amount.
Via SLM