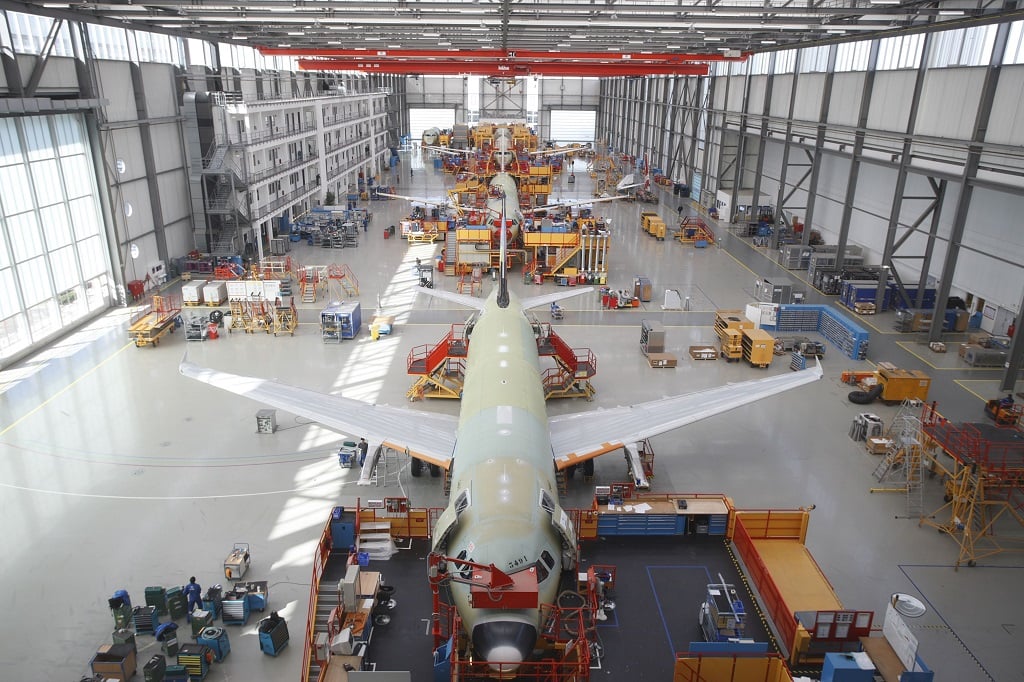
A new contract extension will see more 3D printed parts inside more Airbus cabins.
Stratasys has been 3D printing parts for Airbus for years now. Those parts are now set to reach more types of aircraft. The company explains in a brief announcement today:
“While the initial contract with Stratasys was focused on production parts for the A350, this contract extension expands the range of parts printed for Airbus to include replacement and spare parts for maintenance, repair, and overhaul (MRO) as well as parts for aircraft platforms (such as A300, A330, A340 and A320) in addition to the A350.”
We’ve had many conversations with the Stratasys team over the years about their work in aerospace. They’ve become finely attuned to the needs and wants of that market — what it needs, how it needs it to happen.
Familiarity is an important aspect for a risk-averse manufacturing market like aerospace, where failure can be actually catastrophic. Scott Sevcik, Stratasys’ VP of Aerospace, shared a look inside the long process of additive manufacturing adoption in aerospace in a previous interview, explaining:
“It’s interesting where we are in adoption because everyone is very focused on lightweighting, on topology optimization to create parts we couldn’t produce before — but that’s no one’s first part. That’s never the first thing they do when adopting the technology. You start by introducing as little risk as possible.”
And:
“They could make the same part that had been produced in another technology, whether that was injection molding or stamping, and all that changed was the mold manufacturing process. What we see in adoption is just that: only moving one or two variables at a time. Airbus, with that example, they’ve always had the material [ULTEM 9085], and now they’ve qualified the process and understand what they can do with it, so now they’re starting to entertain new designs.”
Sevcik has also provided more insights into production use for 3D printed parts at Airbus. The contract has been an important one for Stratasys, as end-use parts have been flying for well over half a decade now on the Airbus 350.
Ensuring quality of both materials and process has been key to Stratasys’ work in getting 3D printed parts in the air. In 2017, the company introduced a certification standard for 3D printed ULTEM 9085 aircraft parts. Focus on traceability has also been on the rise throughout operations, as I saw on the ground at Stratasys Direct Manufacturing in a heavily aerospace-focused facility.
And now, expanding the Airbus contract is another significant step forward for Stratasys’ commitment to the aerospace industry.
As the 3D printing industry shuffles around in a year of M&A-driven consolidation and high-profile IPO moves, it’s more important than ever before to establish strong footholds. For Stratasys, this has meant not only acquisitions — including, to date, of Origin and RPS — but now a public doubling down on applications already in focus.
The timing of focus on aerospace is interesting, as the global pandemic has significantly slowed growth in that industry over the last twelve months. This too shall pass, though — and Stratasys wants to be there when it does. The company closes out today’s announcement by noting:
“Stratasys is an established leader in aerospace, including 3D printing solutions for flight parts, tooling and prototyping. The company’s industrial FDM systems and materials provide the performance and manufacturing repeatability valued by space, commercial aviation and military customers. As it recovers from pandemic slowdowns, the aviation industry is expected to increasingly turn to additive manufacturing for strong yet lighter weight parts and consolidated assemblies, while digital inventory of 3D-printable spare parts promises to make MRO operations more agile and cost effective.”
Via Stratasys