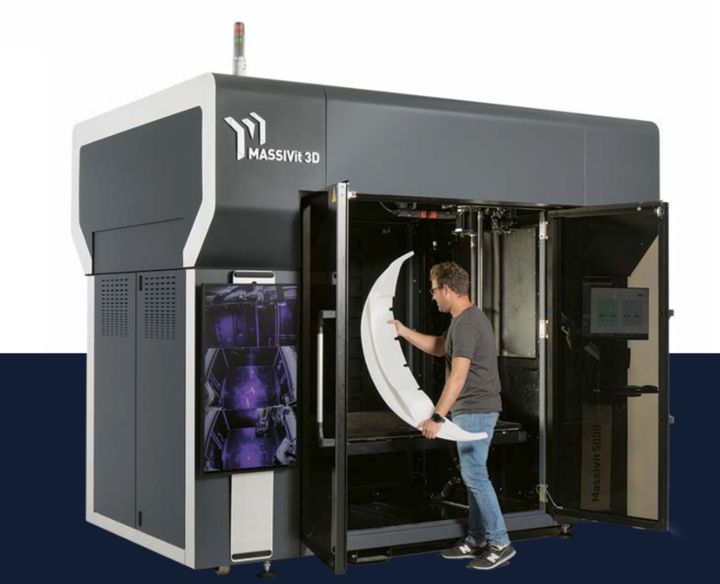
Massivit announced a new and very large 3D printer, the Massivit 5000.
The Israeli company has rapidly built quite a business servicing the large-format 3D printing market with their increasingly huge machines.
Each of their machines makes use of a unique 3D printing process they call āGel Dispensing Printingā, or āGDPā.
GDP is a thermoset process, unlike the familiar thermoplastic process used in SLS and FFF processes. Thermoset reactions are used in the SLA process where liquid photopolymer resin is fused by exposure to strong light energy.
However, instead of using a photopolymer liquid like SLA, Massivitās GDP process uses a photopolymer gel. This provides a number of interesting advantages.
As it emerges from the deposition toolhead, the gel maintains its shape. This allows it to be cured by strong UV lights that bathe the entire build chamber continuously. The process can 3D print objects as much as 30X faster than conventional 3D printing processes.
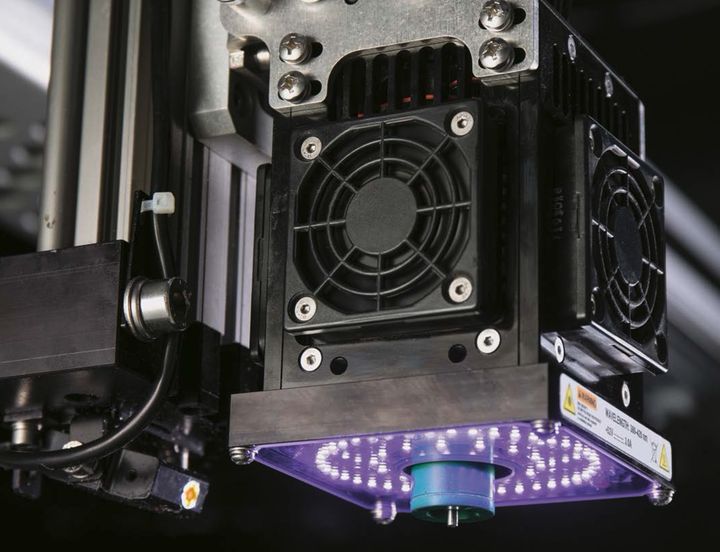
GDP also has the interesting property of near instant solidification, which makes it similar to filament extrusion: overhangs are easily handled, and apparently itās quite rare to require support structures when using GDP.
By using larger nozzle sizes, Massivit can enable very rapid production of large objects. While it is possible to 3D print larger objects using other 3D printing processes, it takes a very long time, sometimes measured in days or even weeks. However, the rapid speed of GDP changes the equation significantly and huge prints become practical.
This capability has enabled different industries to make use of 3D printing for larger items. Massivit lists some of them:
- 3D signage
- Large advertising display items
- Movie props
- Theatrical scene elements
- Amusement park structures
But the premier application seems to be what Massivit calls āFull Scale Prototypingā. This is a practice in which a big item, such as an entire automobile, is prototyped at 1:1 scale by producing several large parts.
They cited an example where a client produced an entire vehicle for display at the SEMA show, with 16 full-size parts produced in only 10 days. Thatās pretty incredible.
Another very interesting example is industrial casting. Massivitās process for producing large molds is to first 3D print a hollow structure with a thin skin. They then apply a layer of epoxy resin to the interior through a rotational process. Finally, the remainder of the interior is injected with a thermoplastic such as ABS. This produces a very rigid and large-sized mold ready for repeated casting.
Massivit 5000
The new machine is able to perform all of the above but with some powerful new features. Massivitās large-scale devices, the 1800, 1800 Pro and now 5000, all have a build volume of 1450 x 1110 x 1800 mm.
The new Massivit 5000 contains two deposition heads, rather than the one on the 1800s (although the 1800 Pro can be upgraded to two). These are independent toolheads that can, for example, be used to build two different objects in the same print job.
The big difference is that the 5000 can have different materials in each toolhead. Currently Massivit offers three different materials, Dimengel 90, 100 and the new 110. The 110 material is compatible with the 5000ās new āHDā feature.
HD, or high definition, 3D printing on the Massivit 5000 is a way to shrink the layer sizes to only 0.5mm in order to obtain a much smoother finish. Normally such enormous objects donāt require significant resolution because the layers are usually not noticeable at that scale, but in some cases smooth surfaces are more desirable. Now thatās possible with the HD feature.
Thereās also a new āFastā printing mode that allows layers up to 1.5mm in size, which should speed up prints significantly at the cost of some surface quality.
The Massivit 5000 also includes a three-camera AI system that keeps watch on the print head to ensure it is cleaned anytime it begins to collect stray gel. This increases part quality and print reliability.
Massivit has also made some interesting changes to their slicing software. Thereās now an auto-orientation feature that instantly re-orients imported 3D models to the optimum setup for GDP printing.
Another fascinating feature in the software is āMold Modeā. This allows a 3D mold model to be automatically generated from any positive 3D model, and should be of interest to any client performing industrial casting.
The Massivit 5000 seems to have incorporated a number of changes from their client baseās feedback, and that should make it a much easier machine to operate as well as being more productive.
Via Massivit