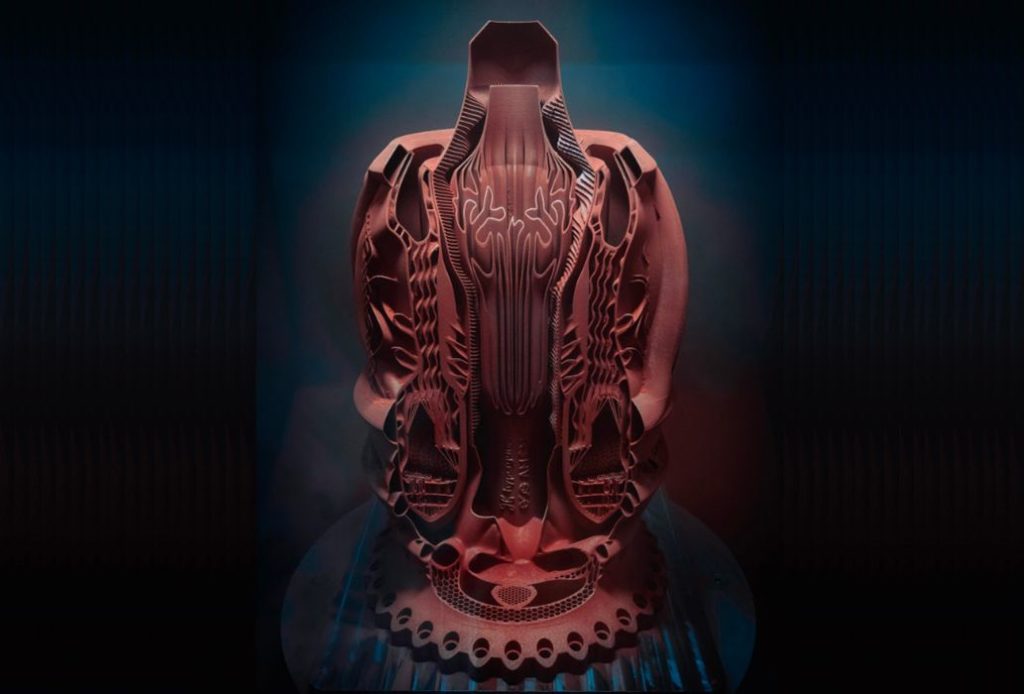
Hyperganic may have produced the most complex model ever 3D printed, a revolutionary aerospace engine.
You may not have heard of Hyperganic; it’s a German startup focusing on AI-based engineering, where the complexities of massive 3D models are handled automatically by software. Their tool is Hyperganic Core. CEO Lin Kayser explains:
“It’s not a magic box. You have to teach the software how to build certain types of objects. But instead of creating one object, like you do in traditional CAD tools, you design an algorithm. This algorithm can then, depending on the input, create lots of different objects and explore a large design space. You can add digital evolution, evaluate results based on their performance and let the best ones influence the next generation.”
And that’s what Hyperganic did to produce the aerospike engine shown above.
What’s an aerospike engine? It’s a very different form of rocket engine. You are probably familiar with the typical rocket engine, which has a large “bell” on the bottom to capture expanding gas and generate upward force. These have been used for many decades, but there is a more efficient design: the aerospike.
Instead of a bell, the aerospike engine simply has a “spike” and the expanding gas surrounds it. As the gas expands, it pushes on the spike to generate forward thrust. This design is said to be as much as 20% more efficient than typical bell designs. It also automatically adjusts for altitude: bell engines require differently sized bells for different air pressures. Large bells are used in the vacuum of space, while smaller bells are used deep in the atmosphere. This is because there’s no air to push back on the expanding gas in space. The aerospike works the same regardless of external air pressure.
Why isn’t everyone using aerospike engines in that case? It turns out they are pathologically complex to design, as the spike part would always overheat. NASA attempted to design an aerospike system in the 1980s and 1990s, but gave up because they could not overcome the complexity.
This was the task taken on by Hyperganic.
It’s a vastly more complex problem than you might imagine because such an engine must be extensively tested and optimized. In other words, you aren’t just making one; you are making a series of iterative changes to the design and building many of them.
Hyperganic seems to have solved this problem. Kayser explains how it was done:
“What my partner Josie created over the past year, is a completely algorithmic model for a wide variety of aerospike designs. Within minutes we can create almost any engine design imaginable, including injector heads, advanced heat transfer systems and complex combustion chamber geometries, different thrust levels and different sizes. Our customers can now quickly iterate and come up with the best designs. An iteration only takes a few minutes.”
In other words, they built an aerospike vending machine. Push some buttons, get an engine. Different every time.
That’s an incredibly powerful capability, and also one that demonstrates how the future of additive manufacturing may unfold.
Imagine a world where every object is, at its core, an algorithm. Bolts, furniture, appliances, rocket engines, or whatever, are all systems where a request with some parameters generates the precise object required.
I think this is why they call their system “Hyperganic Core”.
Via Hyperganic