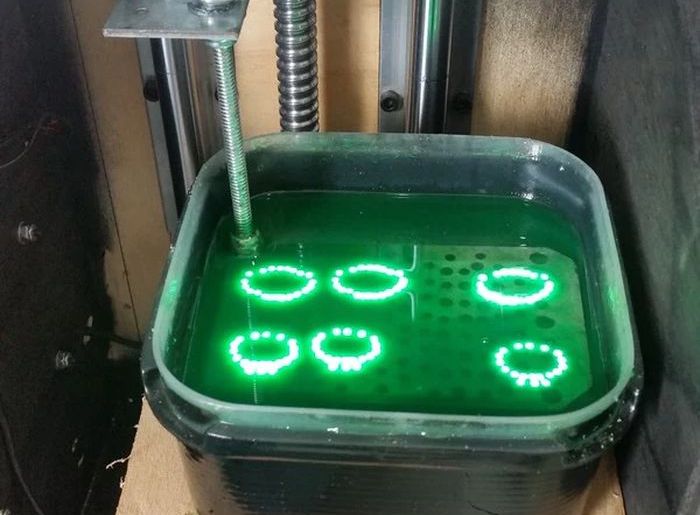
What’s up with top-down resin 3D printing?
We’re all familiar with the “bottom-up” approach that’s pretty much the status quo in the resin 3D printing world. The light engine is snug at the bottom, shooting light through a transparent window at the base of the resin tank to form a solid layer.
The Problem with Bottom-Up Printing
Here’s the snag – the layer doesn’t just bond to the print plate but also to the transparent window. This forces the machine into a slow peeling operation to detach the print from the window. It’s a real time guzzler, causing delays and stretching print durations to lengthy periods.
Some 3D printer manufacturers have tried to sidestep this issue with clever tweaks to reduce peel time. Carbon, for instance, uses a special window that permits oxygen to permeate, averting polymerization at the window surface. Other manufacturers have turned to special window coatings.
The Underused Alternative: Top-Down Printing
But there’s another road less traveled in the industry: top-down 3D printing.
The light engine sits at the top, shining downwards. The resin is held in a tank below, open to the light source—no window, no fuss.
Positioned just under the resin surface is the print plate, set up to have a layer’s worth of resin above for solidification. As the print proceeds, the print plate descends, allowing fresh resin to coat the previous layer.
The absence of a “peel” operation makes these 3D printers blazing fast, like Carbon’s machines, and also mechanically simpler.
A User’s Experience with Top-Down Printing
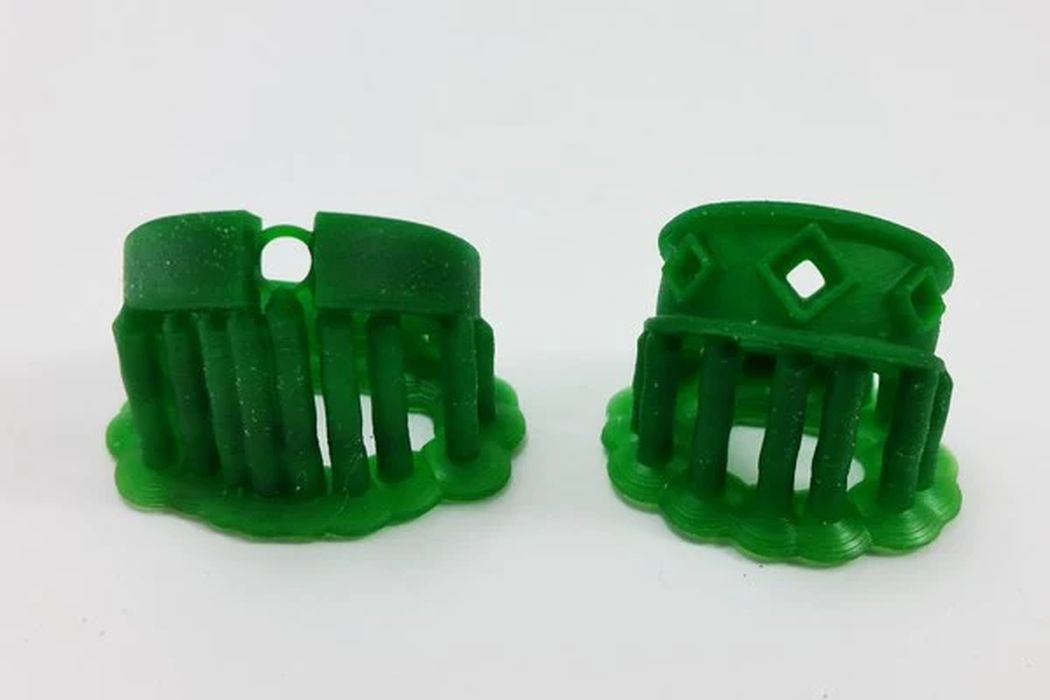
Recently, reader Nicolas Tranchant shared with us a review of such a device made by hobbyist Frédéric Lautré. Tranchant built a kit for this device years ago.
You can delve into Tranchant’s full review of his experience at the link below. He found the kit easy to assemble and the machine’s operating cost significantly lower than the commercial units he’d been using, though the kit machine lacked a bit in the aesthetics department.
Tranchant reports he’s been running this top-down 3D printer successfully for years now.
Why Isn’t Top-Down More Popular?
This left me scratching my head: why hasn’t this approach caught on more?
It’s far simpler than the typical MSLA design, and should churn out parts quicker and cheaper.
As far as I know, the only company that manufactures this type of machine is Australia-based Gizmo 3D Printers, which we’ve covered before. While we haven’t heard much from them recently, they seem to still be making equipment.
Top-Down’s Challenges
I can only see two technical drawbacks to this approach.
First, the top-down method demands a flat and stable resin surface, ensured by gravity. But that also means the machine has to be perfectly level. Any vibration or shifting would ruin a print. However, these seem like solvable problems.
The second challenge, resolution, is a bit stickier. Modern MSLA 3D printers ramp up resolution with each new LCD panel boasting more pixels. A top-down approach, conversely, relies on projection, as the light engine can’t touch the resin. You could use a laser, but that’s pricey, or a DLP-style projection. But the energy from such a projector might be less than what you’d get in an MSLA setup. It’s also unclear whether the resolution of DLP technology is keeping up with LCD panel tech.
The Potential of Top-Down Printing
Despite these hurdles, the top-down approach seems entirely feasible. I’m puzzled why more low-cost 3D printer manufacturers haven’t thought to explore this style of device. In an industry where affordability often takes the cake, top-down machines could find a comfortable niche.
We’ll have to wait and see if this method gets the attention it deserves in the future. Until then, we salute the innovators and tinkerers who aren’t afraid to take the road less traveled in 3D printing technology.
Via Viva Latina, Facebook and Gizmo 3D Printers