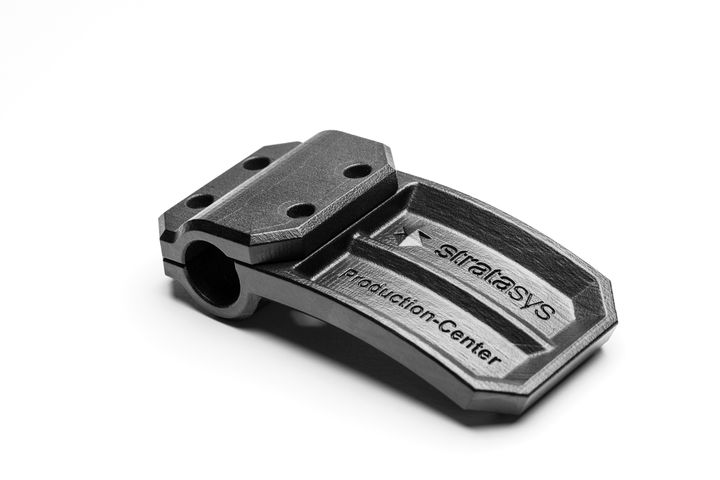
I’ve been thinking about Stratasys’ new SAF 3D printing process.
“SAF” stands for “Selective Absorption Fusion”, a trademarked term that refers to the method used in their new H Series of 3D printers to be released later this year.
In the 1980s Stratasys was the originator of the most popular 3D printing process used today, FFF, or as it is known under Stratasys’ trademarked name, FDM. For most of the company’s existence they exclusively marketed FDM equipment. However, upon the merger with Objet in 2012, they also marketed Objet’s equipment, which uses PolyJet technology.
Now the company is about to release the third major 3D printing process, SAF, according to information released by the company today.
How SAF Works
SAF is a powder-based 3D printing process, and so adopts many of the advantages and disadvantages of other powder-based 3D printing processes like SLS. However, while SLS uses a laser to selectively fuse polymer particles, SAF does something entirely different.
There are two main features of SAF. First, there is “Big Wave”, a method of uniformly depositing a flat layer of fresh powder. While there are no images of the system available yet, it seems that Big Wave uses a counter-rotating roller. It’s not clear whether the roller simply mashes the powder down to a flat orientation, or another approach, such as using electrostatic force to carry powder on the roller. I’m guessing it’s the former, as that is a simpler approach.
The second feature is the use of “HAF”, which is a fluid that exhibits high energy absorption. The idea here is that the flat powder layer will be selectively “printed” with drops of HAF by sweeping a set of industrial piezoelectric printheads across the powder bed.
But then you just have a wet bed, so what happens next?
SAF’s next step is to sweep a powerful infrared light source over the wet bed. HAF then quickly absorbs the energy and heats up. The heat is sufficient to melt nearby polymer particles, causing the selected regions to fuse.
At this point you have pretty much the same story as you’d find in SLS: selectively fused layers that gradually build into a complete object.
SAF Advantages and Disadvantages
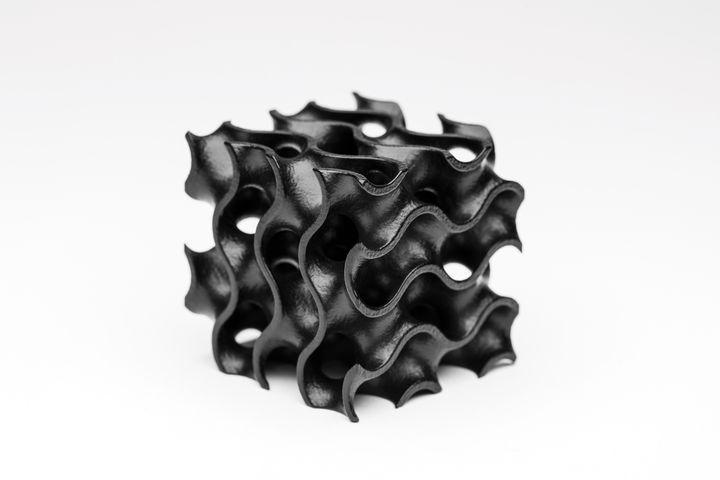
Every 3D printing process has advantages and disadvantages. That’s why it’s best to have several different technologies at hand, so that you can choose the right tool for the job. Let’s take a look at SAF.
No Support Required
Any powder process doesn’t require the use of annoying support structures because the surrounding powder supports loose elements or overhangs. This will significantly lower the total cost of unit production as compared with other processes that do require support removal.
Thermal Control
The SAF heating process takes place in a single step per layer, meaning it is far easier to control the thermal conditions of fusing. That should correspond to reliable operation and parts of consistent quality.
Scalability
Because of the nature of SAF, it should be relatively easy to scale it up. This means to create bigger build volumes, you’d need only add more heaters and printheads, which has already been proven possible on industrial 2D equipment.
Powder Enclosure
Like resin 3D printers, there is the danger of encapsulating loose powder inside a part when it is designed incorrectly. SAF users will have to include “drain holes” when necessary.
Polymer Only
The heat potential of HAF is likely too low to consider for use with metals, so SAF is probably going to be a polymer-only process. However, there’s still a massive market for such equipment.
“Tetris-ing”
Because of the lack of need for support materials, it will be possible in SAF to “Tetris” in as many parts in three dimensions as possible. This would not be a “one layer of parts only” technology; you can jam parts into a build volume as tightly as you can fit.
Simplicity
Thermal control aside, the process seems very simple, and thus effects like warping should be easily accounted for. This also means the SAF systems should be relatively reliable and able to run for long periods continuously.
Fast Production
The production speed for parts should be quite fast because:
- HAF deposition will occur very quickly for each layer
- Heating of each layer is simultaneous
- Only a single layer is heated at a time, allowing other layers to cool
- Big Wave is likely quick, too
This is quite different from HP’s MJF process, where build chambers require some time to cool down because they are heated overall and there is less surface area to radiate heat. SAF should be more easily scalable.
Inexpensive?
Based on all of the above, it’s likely the cost of a SAF part should be relatively low. However, the actual end-user cost remains to be seen as Stratasys hasn’t released pricing or even a description of the equipment yet.
Finally, it seems very clear that Stratasys is directly targeting industrial production with SAF. They have apparently spent “10 years” developing the technology (with Xaar), and in that time we’ve seen them explore a number of different approaches to get into that market. With SAF, it sounds like they’ve found the key that should open the door.
Via Stratasys
This sounds very similar to the High Speed Sintering (HSS) technology developed at the University of Sheffield. Did Stratasys license it?
https://www.rapidmade.com/rapidmade-blog/2014/8/6/university-of-sheffield-touts-breakthrough-in-high-speed-sintering-hss
Hi Jon! Please see our other article today highlighting how this technology was created with Xaar, which was the company formed around that HSS technology: https://www.fabbaloo.com/news/stratasys-introduces-its-latest-production-focused-3d-printing-line
It looks like they are the same. The inventor, Professor Neil Hopkinson, has worked with several UK Universities (at least Sheffield, Nottingham, and Loughborough). He then joined Xaar.
It’s good to see this technology coming to fruition. It certainly sounded interesting when I first read about it, but then it went quiet.