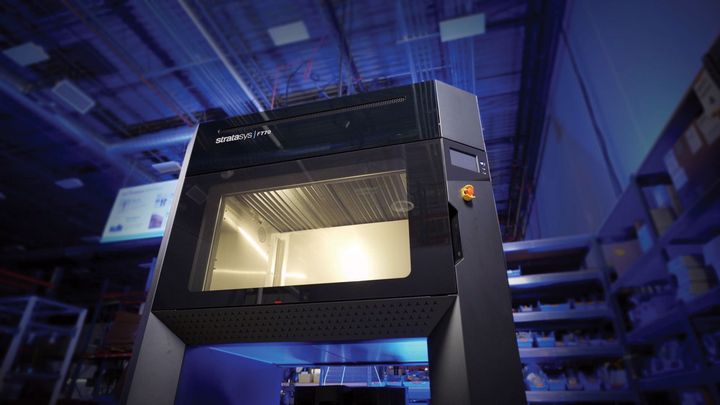
Stratasys announced not one, but THREE new industrial 3D printers today, each very different.
The company has been gently moving towards the manufacturing world in recent years, having experimented with a series of unusual demonstration 3D printers. However, today’s announcement seems to have put the manufacturing strategy into a higher gear.
While 3D printing technology has long been used for prototyping, a number of developments has proven the business model of low-volume manufacturing. This approach fills the gap left open by the expensive tooling costs of injection molding. That technology is only financially feasible if a larger number of units are to be produced. Meanwhile, 3D printers can produce smaller volumes of parts at a consistent and sometimes economic cost.
That’s the target space for the three new 3D printers from Stratasys. These devices are all quite different, and in fact play heavily on several recent corporation acquisitions made by Stratasys.
Stratasys F770
Perhaps the easiest device to understand is the new Stratasys F770 3D printer, which is based on their long-proven FDM technology.
The company already markets a number of FDM devices, so what’s different with the F770?
It’s the size: this machine has a build volume of 372L, and the company says it is the largest build volume for this type of machine available. With Stratasys’ standard heated chamber, it is able to produce parts at a similar or better level of quality than their previous Fortus equipment, but at a larger size.
Stratasys says the longest axis on the F770 is about 1m in length. That’s indeed quite large for an FDM 3D printer, and allows for production of parts larger than would fit in their previously largest device, the Fortus 900mc
Initially the F770 will use only two materials, an ASA and an ABS, combined with their normal soluble support material. This should enable complex geometry prints in those two industrial materials.
Stratasys says the F770 will use 200 cubic inch spools (3.3L or, for ASA, about 3.5kg). This will permit the F770 to run continuously for up to an incredible 140 hours without intervention.
The F770 is also set up to make use of Stratasys’ easy-to-use GrabCAD software for job preparation, but it’s also possible to use the sophisticated Insight system for more direct control of the 3D printing process.
Stratasys has designed the F770 to more easily integrate with factory operations by including an MTConnect feature, as well as an SDK for coding of interfaces to ERPs or MESs.
Finally, they’ve somehow priced the F770 at “under US$100K”; it’s available now for order, and it ships in June.
Stratasys Origin One
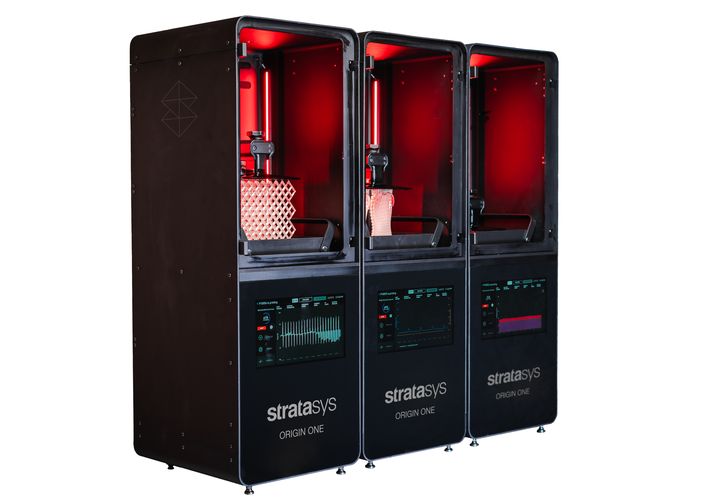
The next 3D printer on the stage is the Origin One. If you haven’t been paying attention, Stratasys acquired San Francisco-based Origin earlier this year.
The Origin One uses the “P3” 3D printing process, which is a DLP-based resin process that makes extreme use of software, sensors and real-time feedback to produce very high-quality 3D prints. “P3” stands for “Programmable PhotoPolymer”, and hints at the nature of their process.
The Stratasys Origin One is not quite the same as the previously announced Origin One that occurred prior to the Stratasys acquisition. In fact, Origin representatives explained that the “new” Origin One contains over 100 technical improvements made by the joint Origin-Stratasys team in only a few months.
The Origin One can reliably produce parts with surface quality equal to that of injection molding, except that you can use any complex geometry. While we’ve seen 3D printers that can produce outstanding surface quality previously, the Origin One can do so at scale. It’s designed for production use, and is targeted for low-volume manufacturing applications.
Stratasys says the system has been used to produce over one million parts since the founding of Origin, demonstrating this capability.
The Origin team has been partnering with a number of major chemical companies to develop custom materials for use in the Origin system. For example, they’ve already produced a fire-retardant material that’s proven quite popular in the aerospace sector, while they have also produced a material that can substitute for aluminum in many applications.
Their strategy is to “unlock” manufacturing applications through the use of specialized materials, and combine that with the ability to mass produce objects with the Origin One hardware.
The Origin One should be of interest to any manufacturer producing end-use products requiring high quality and at low to medium volumes.
Stratasys H350 3D Printer
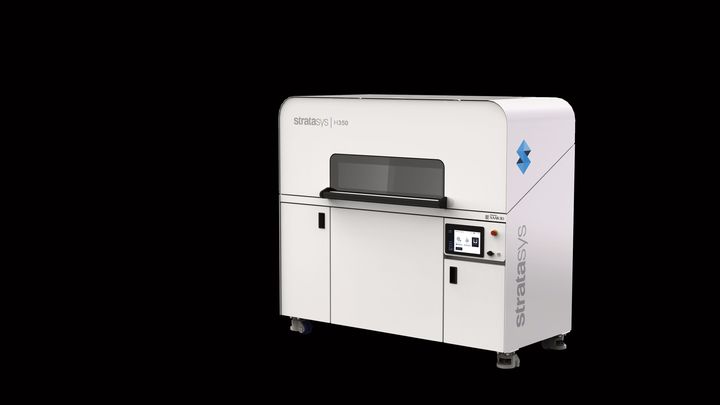
The third 3D printer on the stage today is the unusual H350 device, which is based on Xaar technology. Stratasys has been heavily investing in Xaar for at least two years.
The Xaar process is known as “SAF” or “Selective Absorption Fusion”, and it’s an entirely different 3D printing process from Stratasys’ FDM or Origin’s P3. Instead of filament or resin, SAF uses powder. I reviewed the advantages and disadvantages of SAF earlier this year.
SAF is designed for larger-scale production, and the key is consistency. Stratasys explained that the secret to the SAF process is that all powder manipulation takes place in a single direction, enabling each “particle to have the same experience”. This leads to consistent part quality regardless of the location on the print bed. They call this “homogeneous fusion”.
Stratasys explained that one of the biggest challenges with PBF systems is to produce flat surfaces. With SAF they believe they’ve solved this issue and it is relatively easy to produce parts of this type. They say this is due to their method of heating, which is far less aggressive than that of competing 3D printing processes.
Stratasys has been able to produce hundreds of thousands of parts using the H350, demonstrating the scalability.
They have also tweaked the H350’s design to be more accommodating for use in factory settings. They offer a significant level of individual control flexibility for operations, particularly post-processing. This will allow operators to customize their procedures to ensure the best quality for specific applications.
Another interesting twist is that Stratasys does not make firmware updates mandatory on the H350. While updates are generally desirable, they can often mess up existing finely-tuned processes. This is another way they can accommodate clients.
For cost levels, Stratasys has designed the H350 to minimize manufacturing unit costs through a series of features:
- Print heads are not consumables as they are in other jetting systems
- Only a single fluid is required
- Very high nesting density can be achieved, increasing throughput
- Powder reuse typically requires only 30% fresh powder
Through all these features Stratasys believes the H350 is ideal for low volume production.
Stratasys Production
With these three machines added to the Stratasys lineup it is clear that the company now has a very feasible set of options for low-volume manufacturers:
- Those requiring larger parts can consider the F770
- Those requiring finely-detailed parts can consider the Origin One
- Those requiring larger-scale manufacturing can consider the H350
I believe these machines could permit Stratasys to make a noticeable step into production manufacturing.
Via Stratasys