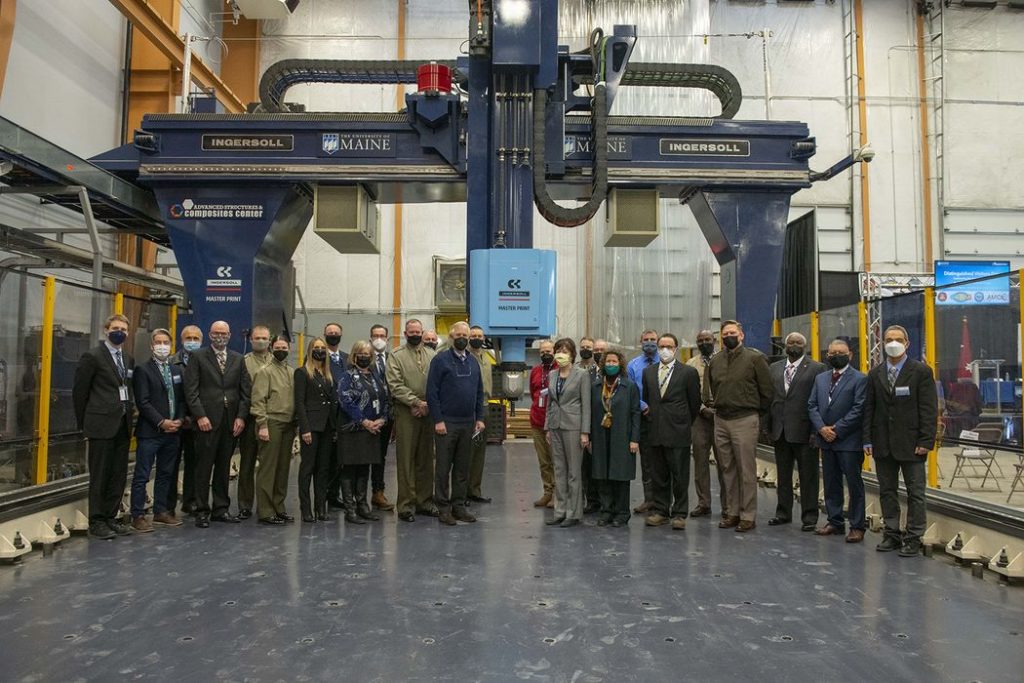
The University of Maine’s Composites Center designed and 3D printed what appears to be the largest ships ever produced with the technology.
This particular research center has been active in this area for some time. In 2019 the center undertook the production of “3Dirigo”, then the world’s largest 3D printed boat. The printing of 3Dirigo, a prototype patrol vessel, took only 48 hours, far less than conventional manufacturing processes.
This vessel is 25’ (7.6m) in length, and demonstrated the possibility of this new approach to shipbuilding.
Last month the center once again announced a breakthrough, 3D printing not just one, but two prototype military vessels, working with the US Marine Corps Systems Command.
The first and larger of the two 3D printed vessels is apparently capable of moving standard 20’ shipping containers from ship to shore. This vessel is said to be twice the length of the original 3Dirigo, so about 50’ (15.2m).
The second vessel produced is a landing craft, capable of moving “a Marine rifle-squad with organic equipment and three days of supplies,” and is smaller than the first vessel.
Why is this development notable? Apparently it takes more than a year to build a landing craft using traditional approaches, while the University of Maine researchers were able to leverage 3D printing technology and other approaches to complete the landing craft in only a single month.
I strongly suspect that the ships’ designs were able to gain from the ability to 3D print the entire structure in one piece: this eliminates the need for connectors, bolts, lugs, and could also provide pre-designed conduit channels wherever required. It’s not just that the 3D printing can operate 24/7, other techniques can also speed up production.
This is a significant development, as it shows it is indeed possible to highly leverage 3D printing for larger-scale shipbuilding and gain a cost and time advantage. It’s very possible this technology could be commercialized in the near future.
If commercialized, we could then see an avalanche of unusual ship designs as many of the normal geometry and production constraints would be gone.
Another possibility is a dramatic scaling up of the technology. As you can see from the image at top, the 3D printing mechanism is quite large, but apparently able to scale by merely extending the axes to the required dimensions.
If it’s possible to produce smaller ships more quickly, then how about larger vessels?
Finally, you may be wondering why there are no images of these two new ships. The University of Maine declined to publish them, presumably because they are military prototypes, and therefore it is not appropriate to show them.