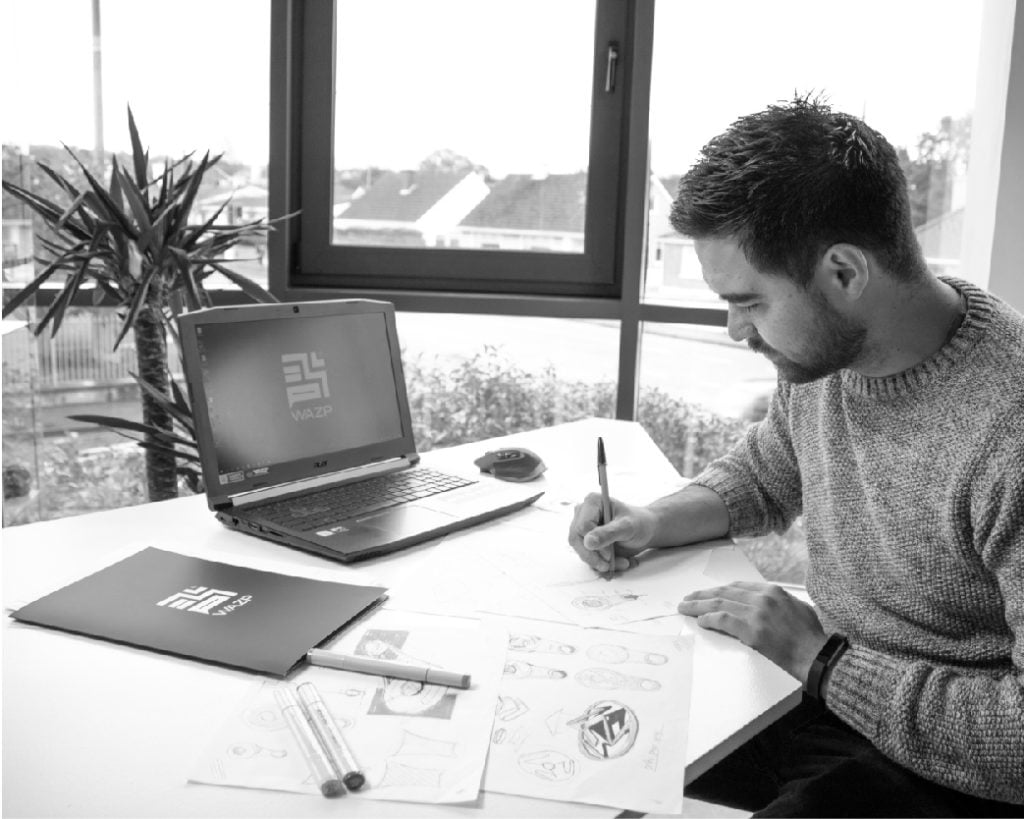
I had the opportunity to get to know WAZP and the big 3D printing and digitization ideas arising from this small Irish company.
In County Kerry, WAZP has been working toward a global end-to-end supply chain solution. While it seems that supply chain is all we’re talking about in additive manufacturing these days, it’s certainly not a new conversation for the team at WAZP.
To get in on that conversation, I caught up with Stephen Barry-Hannon, Marketing Communications Specialist.
WAZP
Founded in 2015, the company is focused on the power of digital solutions. They offer a succinct summary:
“The company was founded in 2015 by Shane Hassett and Mariana Kobal with a mission to refine the capabilities of Additive Manufacturing and create a Supply Chain as a Service that brings this endeavor to businesses globally and at scale.”
That mission of supply chain as a service brings in, unsurprisingly, additive manufacturing. But, Barry-Hannon was clear, the company is “not just 3D printing” — appropriately, the technology is “a tool” for the company. The focal point isn’t 3D printing: it’s digital supply chain.
But what does that actually mean? WAZP offers several key services to ‘transform digital content into physical products’ via 3D printing across a “global network of production facilities and partnerships with the leading technology and service providers in Europe, Asia Pacific and North America,” as the company describes.
Among WAZP service offerings are:
- Product development
- Product implementation
- Additive manufacturing
- Including post-processing: blasting, surface smoothing and polishing, surface dyeing, and surface coating
“Customers come to us and may just have a sketch,” Barry-Hannon explained. “Our design team will design it, optimize it, and manufacturing it using the latest 3D printing technology using near-shore manufacturing.”
The in-house WAZP design team is a standout for the company. At 12 employees, WAZP is by no means a huge operation — but it is mighty. The design team will work with a customer at every step of design to manufacture.
“We can print in the tens to tens of thousands very quickly. We can cater to massive corporations and very, very small businesses,” Barry-Hannon continued. “This has been very helpful for companies often being quoted minimum orders of thousands.”
Low-volume manufacture is of course one of the hallmarks of 3D printing, and WAZP is connecting the dots there — at every step.
“When we say end-to-end, we mean it. We’ll do design all the way through market-ready,” Barry-Hannon added. “We will process, post-process, package: anything it needs to be market-ready.”
To date, the biggest client for WAZP’s services has been IKEA. The team created a hand as a decorative piece; Barry-Hannon describes it as “probably one of the most distributed 3D printed products out there.” On a consumer level, that may just be true; IKEA is a huge operation and the hand was sold on three continents — and sold out within the first week of launch in the US.
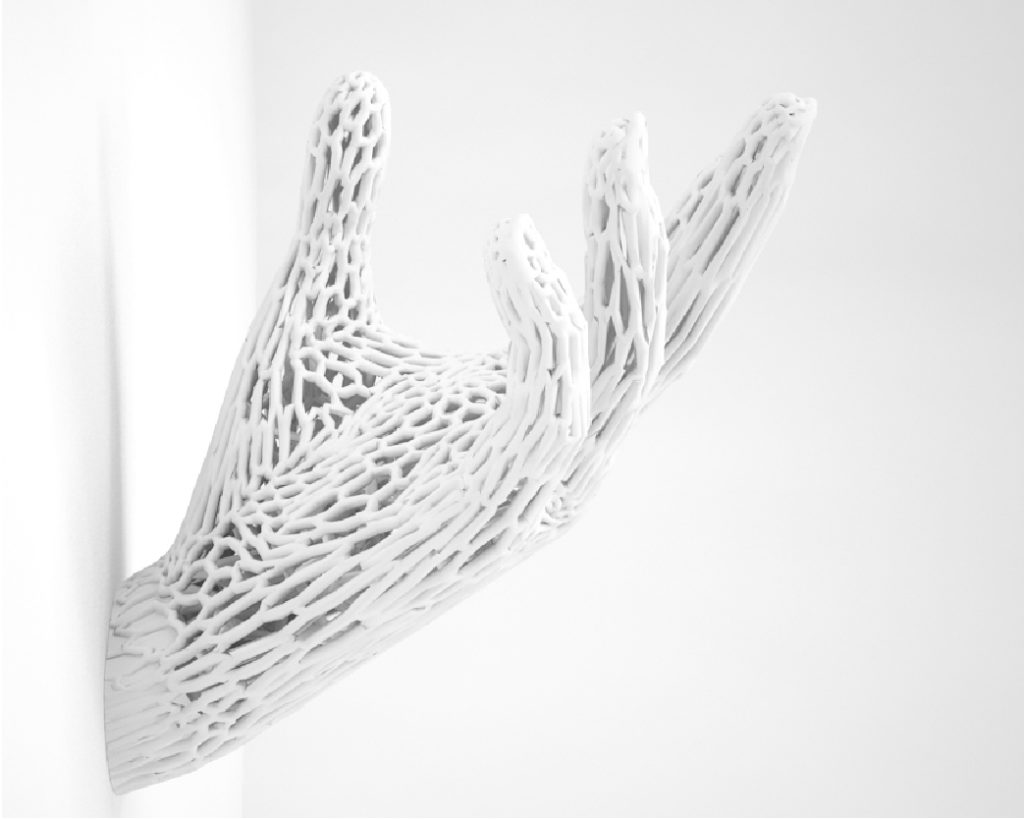
Sustainability
From IKEA to a new eyewear launch, every project that WAZP has something in common beyond advanced technology and a digital supply chain: it’s done with sustainability in mind.
“Sustainability is a major, major, major thing for us at every step of the process,” Barry-Hannon emphasized.
This comes into play in a few ways. First, the company tries to use “as little material as possible.” Leveraging the lightweighting capabilities of 3D printing, less material can be used as compared to traditional designs, helping clients reduce their material needs.
Material reuse is also key. WAZP ‘got their hands on’ material that had been used and was set to be disposed of — but “we did our research and were able to rejuvenate it to match what would be needed,” Barry-Hannon noted. One product for IKEA, in fact, used 100% reused material.
Reducing waste comes hugely into play, and Barry-Hannon highlighted an impressive company fact:
“We have reduced manufacturing process waste to less than 2%, compared to traditional manufacturing that can be up to 90%.”
Further on sustainability, we return to the near-shore manufacturing model. This “takes out the need for air and freight, to an extent,” Barry-Hannon said, adding that one customer switching to their services took off 2,000 kilometers of on-road freight need. Work like this can “reduce countless tons per year of CO2 emissions.”
Also reduced in WAZP’s digital approach to manufacturing is the actual production step. With a new eyewear product, there are fewer than 10 production steps. This compares to “between 44 and 73 production steps” for traditional acetate glasses.
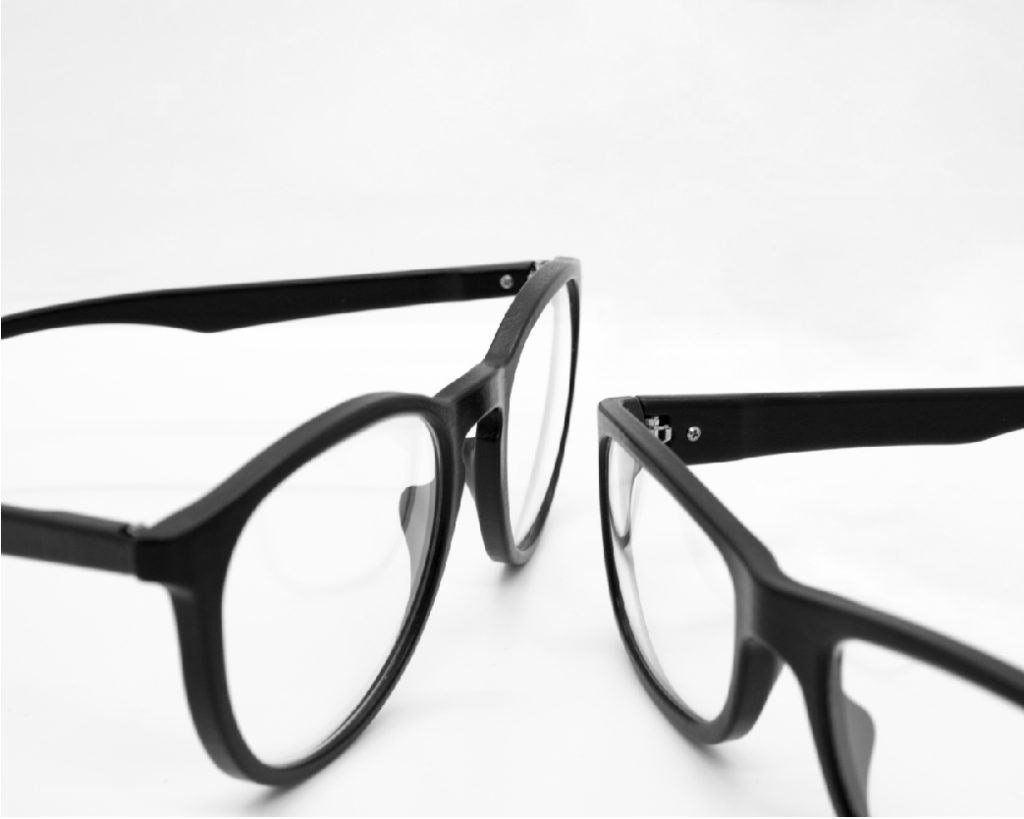
On top of all this is, of course, digital inventory. Cutting warehousing needs and physical stock is a major focus for digital manufacturing, where new parts can be 3D printed quickly as needed.
WAZP SPARK
This month, WAZP also launched a new service: SPARK. This, Barry-Hannon told me in our chat ahead of launch, is a solutions-driven solution.
Co-Founder and COO Mariana Kobal explained in the announcement:
“SPARK is a scalable platform that gives an opportunity to choose ready off-the-shelf solutions suitable for different applications. We are delighted to start this initiative and aim to continuously expand the range and portfolio of solutions.”
Currently, SPARK includes three collections: connectors, locking mechanisms, and housings.
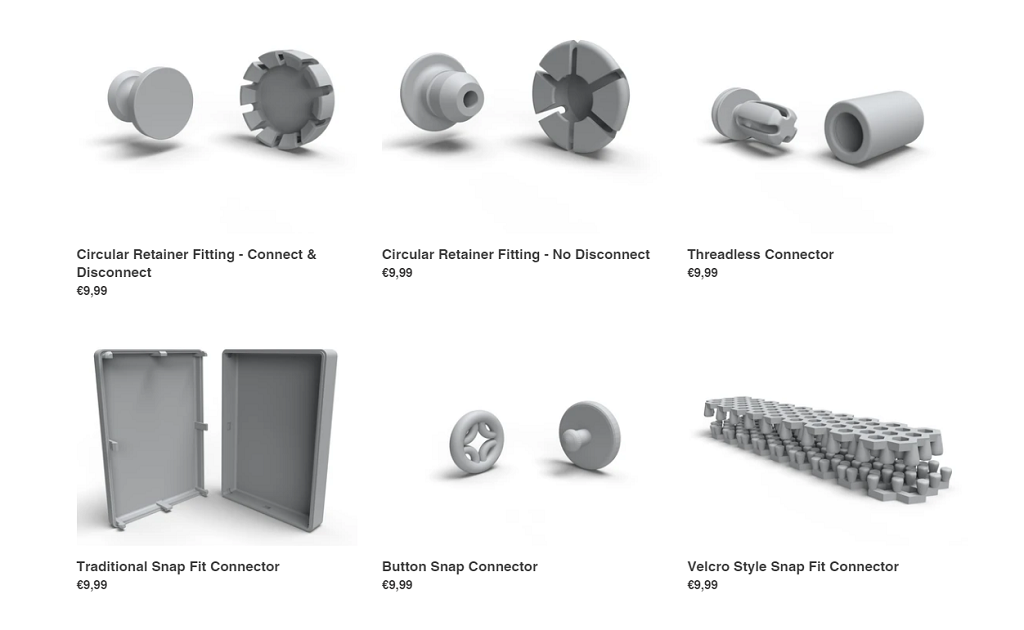
Designs available from SPARK can all be customized to fit exact needs. Starting from an existing design expedites the development.
“We work with so many different projects, and have created designs that can do many things: threading mechanisms, lattice structures, all these different solutions. So we put them on a platform and are pricing low to get products quicker to market,” Barry-Hannon said.
Education
In addition to supply chain, another oft-appearing idea these days is the skills shortage in STEM areas and particularly in specialized areas like additive manufacturing. WAZP is putting their knowledge to use in helping to inspire and offer opportunity to the next generation.
WAZP works each year with student work placements, as the company is “always keen to give people a chance.” They have also worked with area institutions like Trinity College Dublin, which tapped WAZP’s expertise in 3D printing an intake manifold. This year, WAZP is working with Galway and the Mayo Institute of Technology through which their design team is mentoring students in industrial design courses.
“Our community here in Ireland really helped WAZP get off the ground, so we always want to give back. A big thing for us is to encourage young people to pursue careers in STEM,” Barry-Hannon said.
Via WAZP and WAZP SPARK