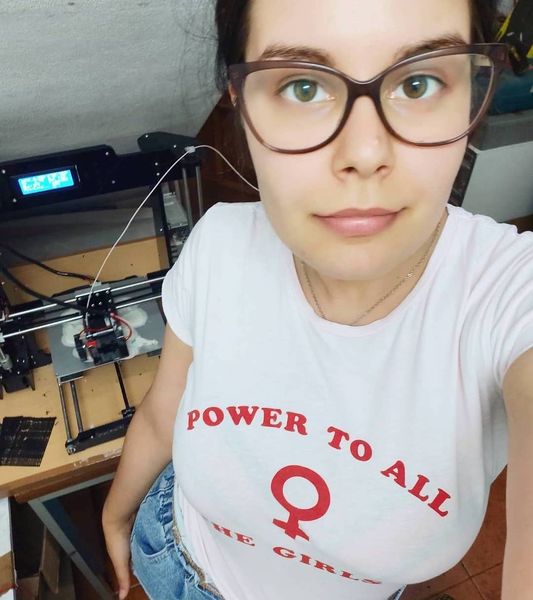
We had a chance to interview Susana Marques, a fashion designer who has been using a number of 3D printers to develop functional and attractive fabrics.
This is Part One of a two-part series. Be sure to read Part Two.
In this part, Marques, only 24, relates her background and how she got started into her long journey to develop practical methods for producing wearable 3D printed fashions.
After hearing her story and seeing countless examples of her work, I think she’s really on to something that few others have been able to achieve. She is able to produce functional — and beautiful — fabrics that can be used to make clothing, which she does.
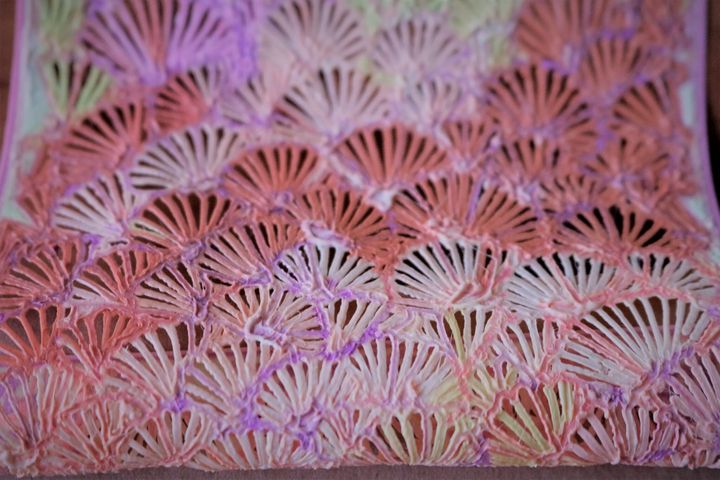
Fabbaloo: Can you tell us about yourself? Where are you from and what is your background?
Susana Marques: “I was born and raised in a small village in the district of Braga, Portugal. Amid a family with a very closed mentality and in which no member of my family followed studies, neither did the majority finish obligation education, even the youngest ones. My mother, as well as most of my aunts, are textile workers in small knits factories that they produce for fast fashion. I was growing up with my cousins inside my uncles’ factory, I often slept in the knitwear baskets, spent the day playing with the remains of the patterns of the pieces, took all the scraps and made clothes for the baby toys, for barbies, my uncle would let us cut labels and as we grew up we would separate the pieces that came out of the cutting and sewing machines…
At 5/6 years old, my godparents gave me a sewing machine toy to play with, but it worked, it was blue and white, it had a pedal and everything, super cute and opened the doors for me to create more elaborate clothing for my barbies. I then attached the pieces of fabric half sewn, half pinned, then learned to sew them by hand. Around 8 years old I started to sketch and to say I was going to be a stylist.
It was when at 14 I started to unsew my clothes to understand the patterning, and my parents gave me a portable sewing machine. The sewing machine arrived and my mother, who worked for a lifetime in the textile sector, said: ‘now, sit down and do it!’, she didn’t even teach me how to put the thread in a needle. It also figures up my education and way of doing things, no one taught me anything, they put it in front of me and it was ‘now make it work with the resources you have’, there is a very Portuguese word for that is ‘desenrascanço’: I have to know how to do all the things by my own and self-teach.
At that time, I was already organizing a folder full of sketches and designing clothes for my aunts to send to the seamstress. I started making clothes for myself at special times or because the clothes in the stores were very boring compared to what I created. And I started making special dresses for my friends too. At the age of 16, I signed up to present a collection of my own at fashion shows in my county’s ‘fashion week’, I got to know the whole process of creating a collection, it was an incredible experience. I performed there for 3 consecutive years.
At 18, I entered the degree in Fashion Design and then the path was already beginning to be defined. As you can see so far, I have no connection or training in technology and my entire ‘career’ has always been focused on fashion design, the arts, always surrounded by drawings, painting, sewing … very far from my current world.”
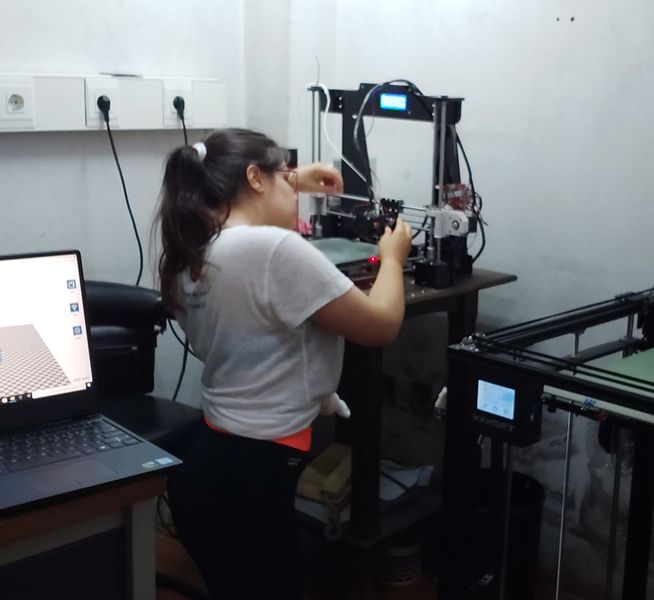
Fabbaloo: When did you get into 3D printing, and how did that happen?
Susana Marques: “In 2017 I started my master’s degree, and in one of the subjects we were asked to develop a collection, while the teachers passed the guidelines, we were told some options that we could use, including the possibility of partnering with a FabLab, where we could use 3D printers, laser cutting machines and other technologies to give an innovative factor to our collections.
But at our disposal this type of technology was unprecedented at our university so I was excited and at the same time I wrote 3D printing on Google, and I ended up looking for trendy 3D printing too, after about 5 minutes I immediately said I wanted to use the technology in my collection.
I knew absolutely nothing about 3D printing, about printers, what it was, I was having the first contact with technology at that time and I was fascinated. However, I realized that it would be something that would take a lot of time and effort on my part. At the time I envisioned it to be soon used in accessories or even to create the trims of the collection, something that would give a different touch to my work but would not go much beyond that.
After that day, I came home and started researching technology every day, subscribing to newsletters, searching more and more about the subject, but the truth is that I was completely lost in this new world. A professor from the university, who ended up becoming my advisor, took a class in which she introduced me to the SketchUp 3D modeling program so that I would have some basic notions and be able to start working on something, taking into account that I advanced with the idea of wanting to use technology in my collection.
About six months passed, I started to know a lot of things theoretically, but in practice the truth is that I had never been in front of even a 3D printer. The university was also unable to provide any, so they made a connection with another department for me to use a printer that was falling apart and always crowded with engineering students. So, I decided to order at Gearbest, I bought an ANET A8 for 120 euros.
As soon as the printer arrived and had to be assembled, I set to work. I realized that in the end I still didn’t know anything about the technology, and I had a lot of difficulties.
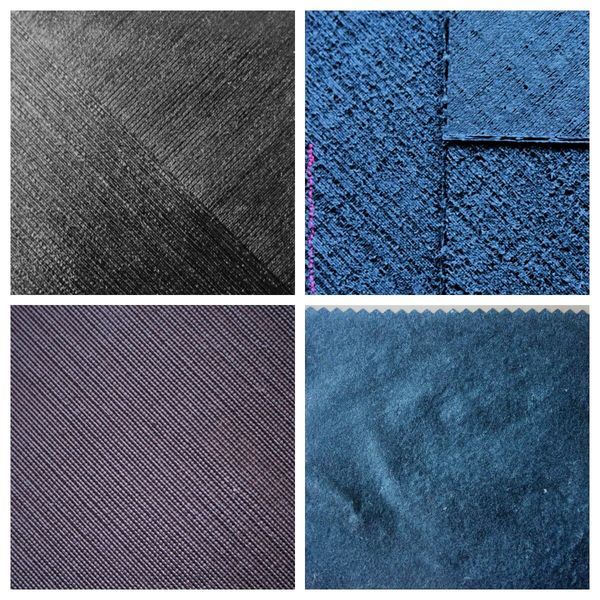
At that time, having Iris Van Herpen as an idol and venerating Danit Peleg for our similarity of path, I sat in front of the printer with all the background I had acquired in theory and started to follow a few steps that I had already read about what some designers had done.
My first experiences were through rigid interconnected modules, as many people still do today, a little based on the work of Janne Kyttanen and several other designers who followed this line. I entered platforms like Thingiverse and downloaded some of these meshes. I already had tried to print these chain-mails at the university with the printer practically falling apart, and the result was completely unfeasible.
So I tried to reproduce it again on my printer, in ABS and PLA, after finally understanding the definitions and learning to deal with the material, these first modules came out well, I was super excited to see the first products coming out of the printer. However, it only satisfied me for a day or two, at that very moment I realized that it was completely unfeasible from the point of view of use and would never leave the conceptual field, in addition to having several limitations of comfort and applicability.
It was at that moment that I decided to start testing the flexible filaments, especially those of Recreus, which at the time was one seen by all designers as a solution to implement in fashion, and I finally started doing some tests with Filaflex.
I started to get very flexible samples, very similar to conventional fabrics, I used 82A and 95A shore materials, and I was super excited to see that the fabrics I printed were thinner and more malleable than anything I had ever seen on the Internet.
These samples that I made, I showed only to one teacher (the one who became my advisor) and was the only person I trusted at the time, as well as the director of the university’s textile department, both were my pillars throughout that route.
To apply to the collection, which had been the beginning of all of my research, I printed a PLA dress that ended up despite about 8 kg due to my lack of knowledge both in terms of materials and structures, limitations and everything else that involves 3D printing. I also printed a shirt entirely in Filaflex on a tulle base, at that time I was also experimenting with printing on fabrics.
As soon as I dispatched the pieces for the collection, I very quickly felt again that it was not enough, it was a good thing without a doubt, however it was very far from matching what would be a suitable clothing for everyday life, in that sense I started looking for filaments even more flexible that could provide another level of comfort and deepen the development of structures that resemble conventional textiles, it was when I started using the Recreus 70A and then used the Makeshaper 60A which was discontinued afterwards, and I was able to test only 200g.
With each passing day I wanted fabrics that were more elastic, more comfortable and more suitable for everyday use, but I quickly realized that the market was very limited, both in terms of printers and materials, and there was no offer for what I was looking for. It was then I decided to gather all the money I could to acquire a Filastruder, and at that moment I could start producing my own filaments, testing even lower hardnesses that forums said were impossible to use. I was also able to finally recycle all the waste that I had saved from my printer and was never able to throw it away.
From then on it was always more fun because I started assembling and disassembling the printer, making changes, I stopped using only the black and white filament and started to play with color, as at the time I couldn’t buy spools of several colors and I also thought that the colors that the brands offer were very limited, I started to create my own dyeing method, to create a way to build my garments, to test the increasingly flexible filaments and new structures. Every day was a new adventure.
As soon as I plunged into this world head on, between mid 2018 and 2019 I wrote my dissertation on the application of additive manufacturing in the fashion industry. My biggest limitation was perhaps a help in many moments, the fact that I was working completely alone, with no one around me who knew practically what a printer was, without any support from even the university, and depositing all my money & savings in research, made my life revolve around this, but at the same time have an endless commitment because I was 100% in it, and without help. If I could buy filaments I would never have started making my own; if I had any chance to buy the colors, I wouldn’t have figured out how to dye.
Of course, it always cost me a lot not to have someone to advise me, to teach how to work on the programs and to have to discover everything on my own, just as I would like to spend my very little money on things like other girls my age instead of extruders, nozzles and pieces for research, besides that whenever it was necessary to move forward, saving cents to finally be able to buy was demotivating and counterproductive.”
This is Part One of a two-part series. Be sure to read Part Two.