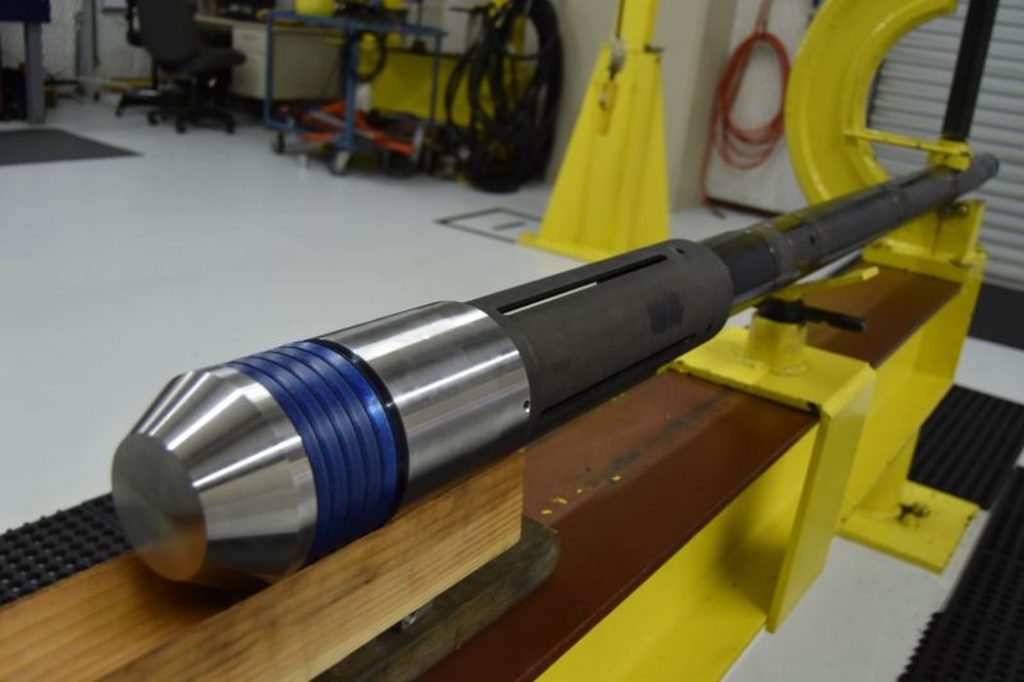
Engineering a 3D printed component that can take the heat and corrosive chemicals in a geothermal well.
There are sources of geothermal energy beneath the surface of the entire planetābut very few locations that are actually suitable to tap into that energy to power electrical plants or heat homes. And once an accessible source is identified, the challenges continue: the machinery used to tap into that energy source needs to be able to stand up to extreme temperatures, nearly indestructible rocks, high pressure and corrosive chemicals.
One company, Downhole Emerging Technologies (DET), has turned to additive manufacturing (AM) to create solutions. The company recently of the American-Made Geothermal Manufacturing Competition, sponsored by the U.S. Department of Energy (DOE), for their innovative Diamond ETIP (Extreme Temperature Isolation Packer).
A packer is a mechanical device that is deployed and retrieved by wireline into a geothermal well to isolate specific zones of the well. It can be deformed to accurately fit the shape of the wellāand is a key technology for harnessing geothermal power. But the packer needs to be able to withstand the extreme temperatures within the well.
Existing packer technologies in the industry have been adapted from the oil and gas sectors, which use rubber and plastics. These parts fall short in three ways: they arenāt rated for the heat in a geothermal well that can often exceed 200 degrees Celsius, they tend not to last more than a year and they are not easily deployed or retrieved. In addition, these components can be expensive.
DET set out to create a metal packer that could be easily deployed and retrieved. āWe came up with a very intricate, crazy design that simply cannot be machined,ā said Ken Havlinek, CEO of Downhole Emerging Technologies. āBut it can be printed.ā
DETās packer is shaped like a large bracelet with features that allow it to deform, precisely and rapidly, into the shape required to create a seal in the mine shaft. Because of the complex internal features of the deviceāitās not just a hollow ringāit could not be machined, molded or extruded using traditional manufacturing methods because of the complex internal features of the device.
But while conventional manufacturing methods werenāt suitable, DET found that 3D printing technologies were up to the task. Downhole partnered with Protolabs, a digital manufacturing specialist company, to print the part. In fact, the component was the largest Inconel largest Inconel additively manufactured part Protolabs has created to date.
One component of the packer is called the setting tool, which applies the force to deform the packer in order to set it in position or retract it. DET wanted to use as little energy as possible to set the packer in place as well as unset and retract the deviceāthe smaller the amount of force required the better. Additive manufacturing allowed DETās engineers to reduce the forces needed.
In fact, because existing setting tool systems could not generate the force needed to set a metal packer, DET originally set out to make its own custom setting tool that could apply the extremely high force that was required. However, the company started using additive manufacturing to create prototypes and iterate the design to reduce the amount of force the tool needed. Through this process the company landed on a design that applied force efficiently enough to enable the use of existing commercially available setting tool systems. According to Havlinek, reaching that point freed the company from having to do extensive work to design its own setting system: DET could now use setting tools that are already on the market.
āOnce we started envisioning a solution that additive manufacturing could reach, it really opened the door to us getting very creative and finding ideas that allow this device to perform far better than it would have if we stuck with traditional manufacturing methods,ā said Havlinek. āWe designed it so it takes less force to compress it and stretch it while maintaining the exact same deformation and performance.ā
One of the benefits of 3D printing that was of particular benefit was the fast turnaround time in creating and iterating prototypes. āAdditive manufacturing can often turn a drawing into a prototype a lot faster than a machine shop can,ā said Havlinek. āThat was a really nice feature when youāre up against a tight time frame, on top o the fact that additive manufacturing can create parts that simply canāt be made any other way.ā
DET determined that stainless metals would be the best option for the packer. āAny underground environment that’s going to be involved in either oil and gas or now geothermal is going to have chemicals that corrode and do a pretty good job of destroying a lot of materials, including most metals,ā said Havlinek. For that reason, the Diamond ETIP usesĀ 17-4 PH stainless steel alloy, which has a high tensile strength and withstands corrosive effects up to high temperatures better than conventional stainless steel. The packer also uses Inconel and other nickel-based alloys, which are also corrosion-resistant. These alloys are all commonly used in additive manufacturing.
Read the rest at ENGINEERING.com