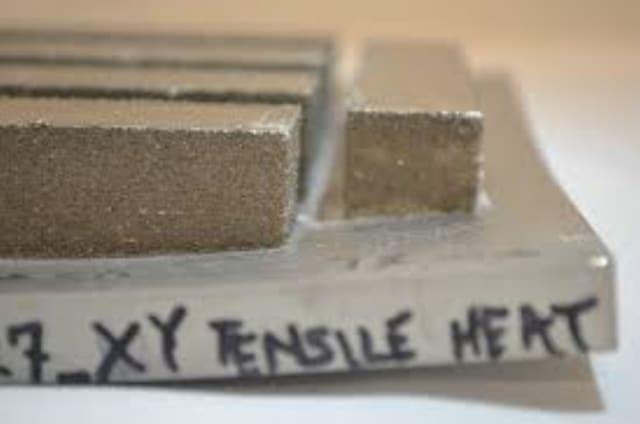
Engineers, scientists, and manufacturing experts around the world are in a frustrating spot when it comes to additive manufacturing (AM).
We have an incredibly powerful technology in our hands, unmatched in its ability to create complex geometries. It can build parts directly from a computer drawing, so the gap between whatās in our minds and whatās in our hands has never been smaller. Think of the cost savings, the labor reduction, the potential empowerment of rural communities. The rewards are tantalizing. But alas, the technology does not yet work quite as it should.
Where Things Stand
Additive manufacturing of metals has nearly achieved mainstream status in industry. Although the technology is still hard to predict, a well-equipped manufacturing facility is now expected to have some AM capability, which is then promptly relegated to niche applications. This unpredictability is primarily due to repeated melting and solidification of metal, which is how metal is fused together in most AM processes. This repeated heating and cooling of metal introduces a host of unpredictable behavior; the part could become distorted or even fracture due to its frequent expansion and contraction. Even when a part is successfully built to the right shape and size, it could have different mechanical properties than one made using conventional subtractive manufacturing; it could be more brittle than expected, or more elastic. In many applications, this is unacceptable.
So, how do manufacturers overcome these complications? Well, the easiest way to get around AMās unpredictability is to just try and see! The trial-and-error approach, however, can take days and cost tens of thousands of dollars for a single part. In the cut-throat world of industrial manufacturing, this seductively intuitive approach is simply too costly.
When trial-and-error wonāt do, engineers often resort to numerical models. In brief, a numerical model is a set of mathematical equations that predicts how a system will behave by solving the relevant physical equations. Have you ever calculated how long it will take you to get someplace, knowing how far your destination is and how fast you expect to drive? Thatās basically a tiny numerical model youāre solving in your head. Engineers use numerical modeling for a plethora of applications, from predicting the outcome of a vehicle collision to optimizing the interior design of an aircraft. Numerical modeling can be applied to AM to predict trouble before it happens.
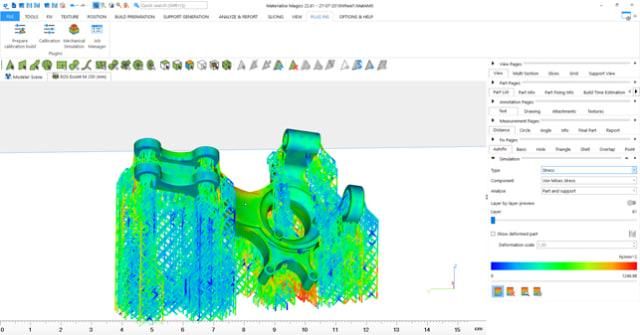
Computational Limitations
AM presents unique challenges to numerical models, however. Unlike a head-on collision, AM consists of multiple highly sophisticated physical phenomena that occur nearly simultaneously, across several orders of magnitude. At the moment a laser comes in contact with metal powder, the powder surface immediately begins to melt, causing its thermal and physical properties to change rapidly. The molten metal behaves like a thick liquid and can flow, on a microscopic scale, in response to changes in temperature and surface tension within (this is known as the Marangoni effect). As the laser travels across the powder, the melt pool follows along while parts of it begin to cool, eventually fusing together to form a solid. Later, when another layer of powder has been deposited on top, this fused solid will be reheated as the overhead powder is melted. In some cases, the fused solid is re-melted itself.
We simply do not have the computational power to model all of these phenomena at once. In other words, our computers are not powerful enough to simulate a process that spans hours by analyzing every single microsecond. Even supercomputers shudder at the thought. To overcome these computational limitations, engineers use empirical relations. Empirical relations are correlations that have been observed through experimentation but are not necessarily backed by theory. Rather than attempting to model every single micro-event, engineers instead prefer to lump their effect into empirical constants. One great example of this is the use of a ālaser penetrationā term.
Read more at ENGINEERING.com