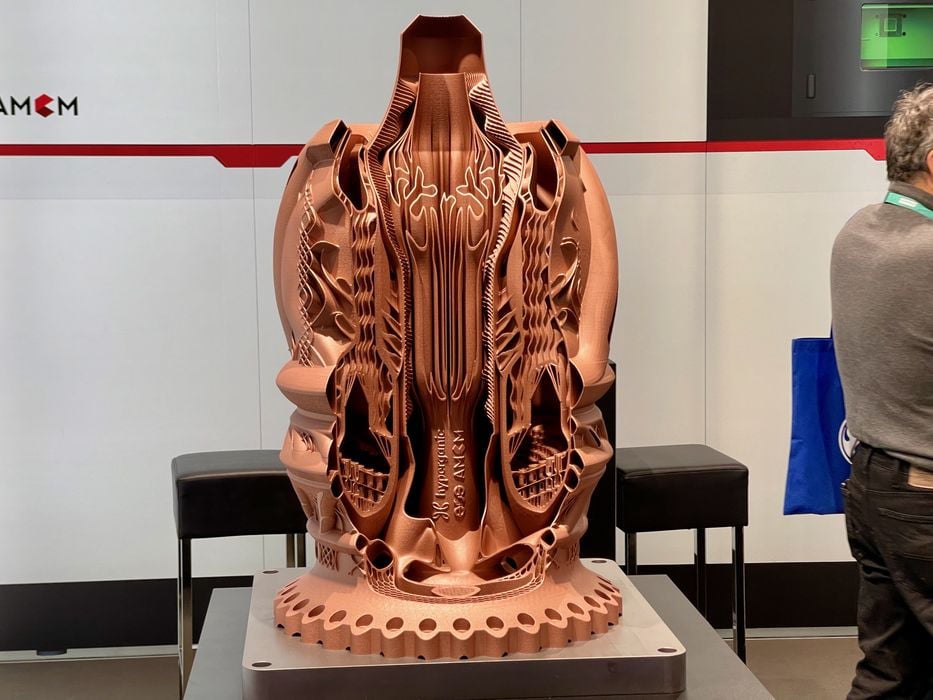
This week’s selection is the astonishing Aerospike rocket engine by Hyperganic.
If this item looks familiar, it should, as we featured it last May as the “Most Complex 3D Printed Part”.
At last week’s Formnext we had the opportunity to view this 3D print up close, and it was so impressive we had no choice than to select it as our design of the week.
It’s a rocket engine, but it may not look like one. That’s because it’s an aerospike engine, which is quite different from conventional rockets that use an “engine bell”. The bell is used to corral expanding gas and direct it outward. However, in an aerospike engine the expanding gas is outside and pushes against a “spike” to create the force. The advantage is that engine bells must be sized for the outside air pressure, meaning you need two different engines for launch and in-orbit use. An aerospike engine can work at any air pressure.
Needless to say, to design an aerospike engine that actually works effectively is an astonishingly complex matter requiring advanced fluid dynamics and other disciplines. This is why we haven’t seen this style of engine frequently used.
A complex geometry demands complex software to design to 3D model, and that’s what was undertaken by Hyperganic. Their AI-based CAD tool was able to successfully design this aerospike engine. They explain:
“It was engineered completely in Hyperganic Core using advanced software algorithms and has never seen a single piece of manual CAD. It’s likely the most complex AM part ever produced — it broke all conventional workflows.”
The resulting design was 3D printed by specialists at AMCM, who used a modified EOS metal 3D printer with a much larger build volume.
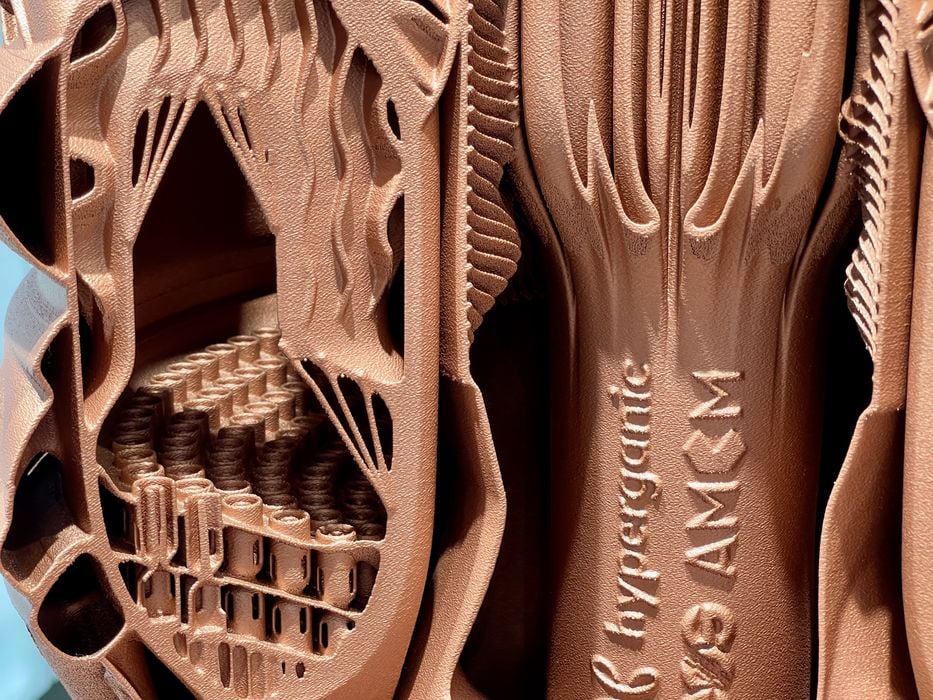
The rocket is printed in copper, and surely is also one of the largest copper objects ever 3D printed as well.
In the design you’ll notice a huge number of internal channels — the print is actually a cutaway version to show you the inside. These are required because the expanding gas surrounding the engine is terrifically hot. In fact, the hotter the gas, the more efficient the rocket. You want hot!
The trouble is that heat could break down the engine, and so the channels are used to cool the metal before it melts. These must be extraordinary efficient, as the engine must also be extremely lightweight.
It’s an incredibly impressive design, and it was quite an experience to see this 3D print in person. In time, it will become one of the milestones in the history of 3D printing.
While the aerospike engine is perhaps the most complex 3D print ever made to date, it is actually only one of a series of even more complex designs that will come in the future as designers leverage the power of additive manufacturing technology.
Via Hyperganic
It’s only impressive if it works.