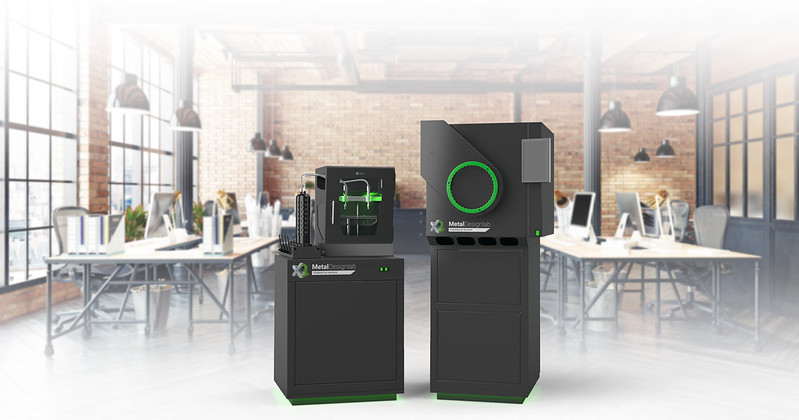
There’s a new office-friendly metal 3D printing system on the market as ExOne and Rapidia introduce the Metal Designlab 3D printer and X1F furnace.
Office-Friendly Metal 3D Printing
The appeal of metal 3D printing in an office environment lies in speed and convenience. Designers, researchers, and others who require relatively quick access to new parts can create them in their own offices. To work in such a setting, near or even on a workstation, 3D printers must be safe to operate, materials easy to handle, and sintering solutions convenient for a small footprint.
To date, “office-friendly metal 3D printing” generally means one of two solutions: Desktop Metal or Markforged. Desktop Metal’s original Studio System and the Markforged Metal X came to market in 2017.
Today, though, those systems are faced with a new direct competitor: ExOne.
Well-known for binder jetting technologies working with sand and metal materials, ExOne has historically been targeting industry. Some of their 3D printing offerings are a bit smaller in size, but until today ExOne equipment wouldn’t be a go-to for, for example, an office setting. Now, thanks to an exclusive partnership, a new launch is set to bring another metal 3D printing offering to the table — or, as it were, to the office desk.
Rapidia Metal 3D Printing
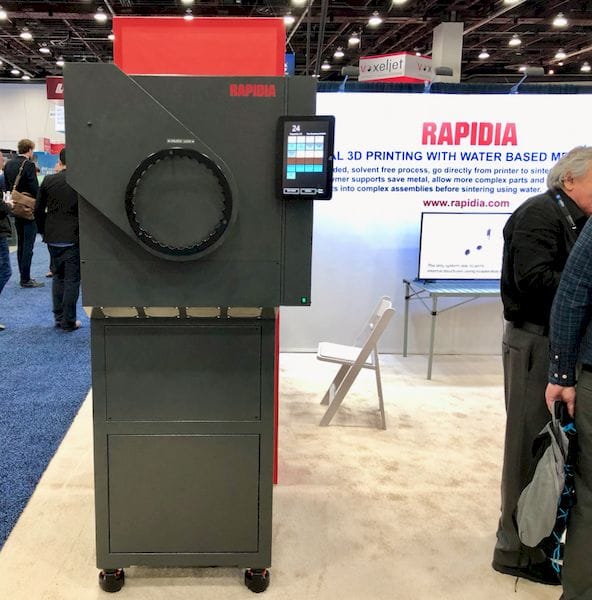
Two years ago, Vancouver-based Rapidia unveiled an interesting metal 3D printing technology.
That two-step process — that is, only 3D printing and sintering, with no middle step for debinding — was quite intriguing. It seemed that Rapidia was the first to successfully introduce such a system. They are no longer the only ones, though, as just last week Desktop Metal introduced the Studio System 2 as a two-step metal 3D printing solution. Hot on the heels of that announcement, though, we have the first update in quite some time from Rapidia.
The announcement explains:
“Under terms of this strategic partnership, ExOne has a right of first refusal for majority ownership of Rapidia, and Gelbart will now become a technology advisor to ExOne.”
And:
“Rapidia’s two-step 3D printing technology, developed over several years and first revealed in 2019, was the first to allow water-bound metal and ceramic parts to go directly from a printer into a furnace without a debinding step. The efficiency is made possible by HydroFuse, an innovative water-based paste containing metal or ceramic powders, which does not require debinding before final sintering. Two materials are currently offered: 17-4PH and 316L stainless steels, with other metals and ceramics to follow soon.”
While for example in Desktop Metal’s two-step process, the debinding becomes thermal rather than chemical, Rapidia’s technology uses HydroFuse paste. This, they explain, “replaces 98% of the binder with water, which evaporates while printing,” a technology that “also removes the limitation on maximum part thickness.” This is in contrast to what the release notes is a general limitation to 5-10mm part thickness with other bound metal 3D printing processes: “The new ExOne Metal Designlab can print 100% solid metal of any thickness.”
ExOne x Rapidia
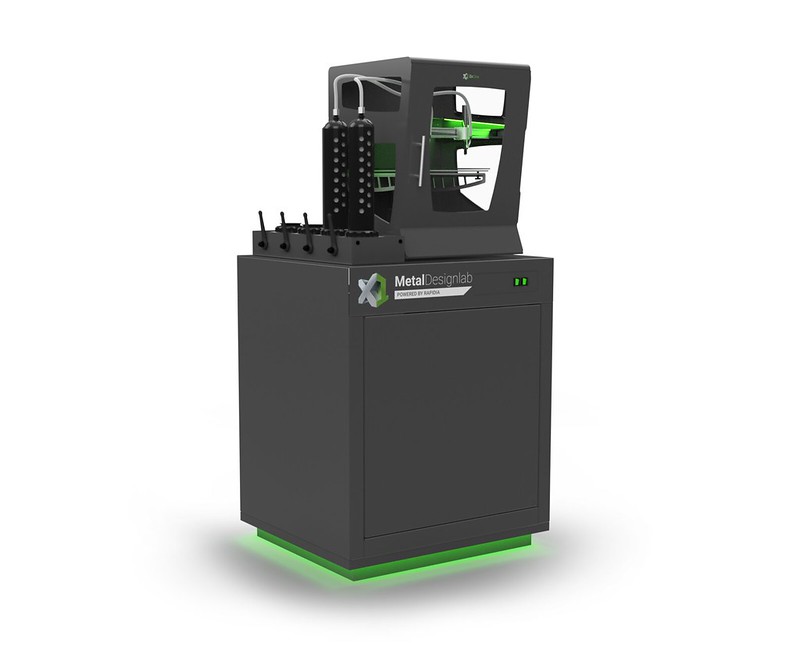
With the coming together of ExOne and Rapidia for this launch, Rapidia’s technology gains access to extensive ExOne market resources. As Rapidia’s Gelbart explains:
“We set out to develop a simple, environmentally friendly system that creates the toughest, most intricate parts overnight. Today, we’re excited to leverage ExOne’s global marketing and sales team to help customers around the world enjoy the benefits of our revolutionary technology. I also expect a lot of innovation to come from combining the deep technical knowledge of both companies. Now, users can 3D print complex parts today without any thickness limitations for solid parts and produce high-strength parts overnight.”
ExOne CEO John Hartner adds:
“We are delighted to partner with the visionary Dan Gelbart and the Rapidia technology team to offer the new ExOne Metal Designlab and X1F furnace. This technology is a true time-saving innovation that complements ExOne’s portfolio. Now, researchers, educators, and industrial designers will be able to bypass days of waiting and produce high-quality parts without the limitations faced by parts that require traditional debinding.”
The new solution is available today for orders; deliveries of the 3D printer and furnace are expected in Q2 2021. Further developments are also on the way. The release explains:
“The ExOne and Rapidia teams are collaborating on system and process enhancements to offer this true Print Today, Parts Tomorrow to the marketplace, with more innovations expected. The new X1F advanced furnace, with about 10 liters of usable volume, will also be offered across ExOne’s binder jet lineup, where it is an ideal complement to the Innovent+ or InnoventPro 3L or 5L printers.”
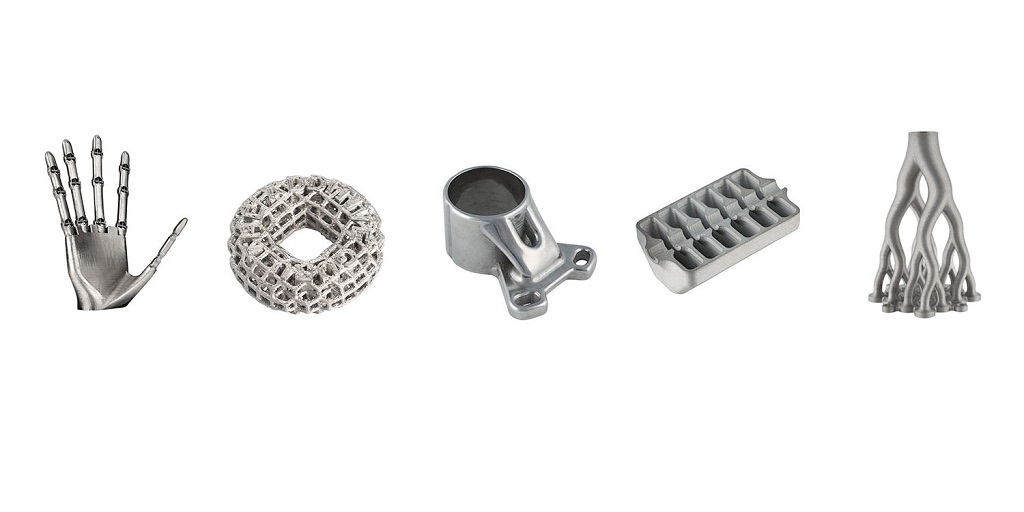
A few other points of interest from the Metal Designlab site indicate as well:
- By eliminating 98% of the binders, we also eliminate debinding odors in the office. Our process has no solvents, no fumes, no odors or no need to dispose of waste polymer.
- Limited need for hydrogen or forming gas. Metal Designlab sinters some common metals, such as 316L, without any need for hydrogen or forming gas. It just uses a small amount of welding grade Argon, which is available anywhere at a fraction of the cost of other sintering gasses. Next to the metal, gas is the second largest expense in a sinter-based system.
- The X1F advanced furnace by Rapidia is fully automated, safe and easy to install. Powered by a 60A single-phase receptacle and sized to fit through an office door, it is designed from the ground up to be truly office-friendly. The furnace software comes pre-loaded with sintering profiles; just select a material and press start. A thick walled retort ensures thermal uniformity over the full temperature range, with a peak temperature of 1400 °C.
Some system specs include:
- Resolution: Coarse (0.6 mm nozzle) and Fine (0.4 mm nozzle). Other sizes available.
- Build envelope: X: 200 mm Y: 280 mm Z: 150 mm
- Caution: Parts approaching the full build envelope size may exhibit distortion during sintering
- Printing speed: Over 40 cc (2.4 cubic inch) per hour with coarse (0.6 mm) nozzle
This partnership and introduction is certainly intriguing — a bold move from ExOne and Rapidia that should give us another “one to watch” as 2021 continues.
Via ExOne