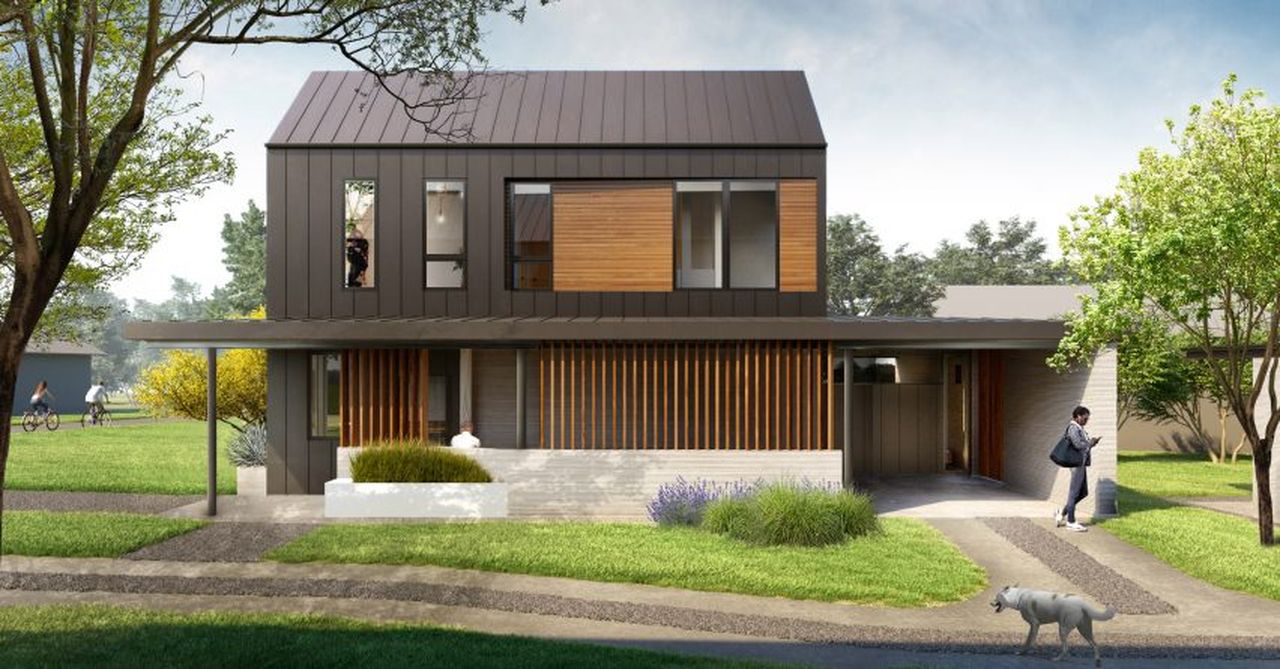
Charles R. Goulding and Preeti Sulibhavi explore the ongoing construction of wood homes in hurricane prone coastal areas and the advantage of 3D printed homes.
Surprisingly, builders in Florida’s hurricane-prone coastal communities are still constructing wood stick-built homes. This is occurring despite climatic events such as Hurricane Ian, which devastated southwest Florida in 2022.
While concrete construction may seem the obvious choice for durability, wood frames remain popular due to significant cost savings and faster build times. However, wood is clearly more vulnerable during major storms.
Structures made with 3D printing show great promise for storm resilience. The layered printing process creates continuity within the walls, adding strength. Geometric shapes like curves and angles can also be incorporated to improve structural integrity.
Perhaps most importantly, 3D printing enables forms not feasible with traditional techniques. This includes reinforced concrete printed in wood frame-like structures with interior lattice supports. Such “concrete canvases” provide the moldability of wood with reinforced concrete toughness.
Hybrid designs take this further by integrating wood and steel rods within the concrete printing process. The result is resilient concrete infused with thermal insulation, preserving wood’s advantage for energy efficiency.
3D printing also speeds construction, with some homes fully printed in just days. And less labor and reduced material waste make it cheaper per square foot compared to conventional building.
Yet why aren’t 3D-printed homes sprouting up across hurricane hot zones already? The technology faces barriers to rapid mass adoption. The 3D printing industry needs to do a better job communicating the advantages of 3D printed buildings. Restrictive codes often lag behind innovations as well.
Still, pioneers are showing whatās achievable, and awareness is growing. After Hurricane Michael in 2018, global housing nonprofit New Story partnered with construction technologies company ICON to 3D print initial homes in Texas as affordable model hurricane-resistant residences. Their success helped change local building codes in Austin.
New Story and ICON are now working with the coastal Florida county of Manatee on resilient and low-cost printed prototype homes. Other innovators like Florida startup Kamp Kover are also commercializing resilient 3D-printed panels for storm protection. Perhaps most promising is Palari Homes – a Florida startup using 3D printing to build entire turnkey residences. Just founded last year, Palari recently announced their first community of 3D-printed homes planned near Tampa. The company utilizes a proprietary concrete composite mix reinforced with layers of steel cable. Their fully-printed homes can reportedly withstand 250 mph winds – well beyond what current codes require.
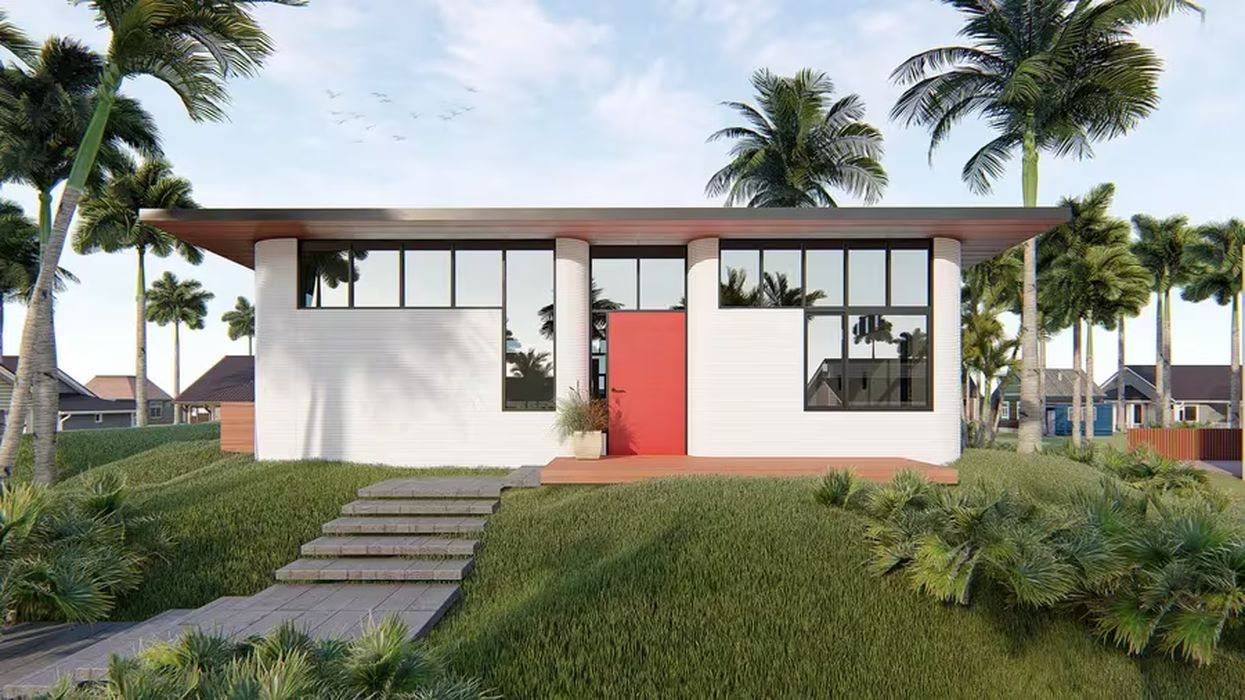
Such examples make it clear 3D printing has crossed a tipping point from novelty to a viable pathway for resilient and cost-effective, real-world housing. Florida builders considering wood frames today would do well to also examine alternatives offered by additive manufacturing. The Sunshine Stateās growing cluster of construction technology startups is set to accelerate 3D printingās adoption.
The Research & Development Tax Credit
The now permanent Research & Development Tax Credit (R&D) Tax Credit is available for companies developing new or improved products, processes and/ or software.
3D printing can help boost a company’s R&D Tax Credits. Wages for technical employees creating, testing and revising 3D printed prototypes can be included as a percentage of eligible time spent for the R&D Tax Credit. Similarly, when used as a method of improving a process, time spent integrating 3D printing hardware and software counts as an eligible activity. Lastly, when used for modeling and preproduction, the costs of filaments consumed during the development process may also be recovered.
Whether it is used for creating and testing prototypes or for final production, 3D printing is a great indicator that R&D Credit eligible activities are taking place. Companies implementing this technology at any point should consider taking advantage of R&D Tax Credits.
Conclusion
With thoughtful designs leveraging new materials science, thereās no longer a need to choose between affordability, rapid rebuilding after storms, and robustness. As Florida re-envisions resilient coastal living for the era of climate change, 3D printing provides an essential tool to ensure growing communities can stand up to what nature throws their way.