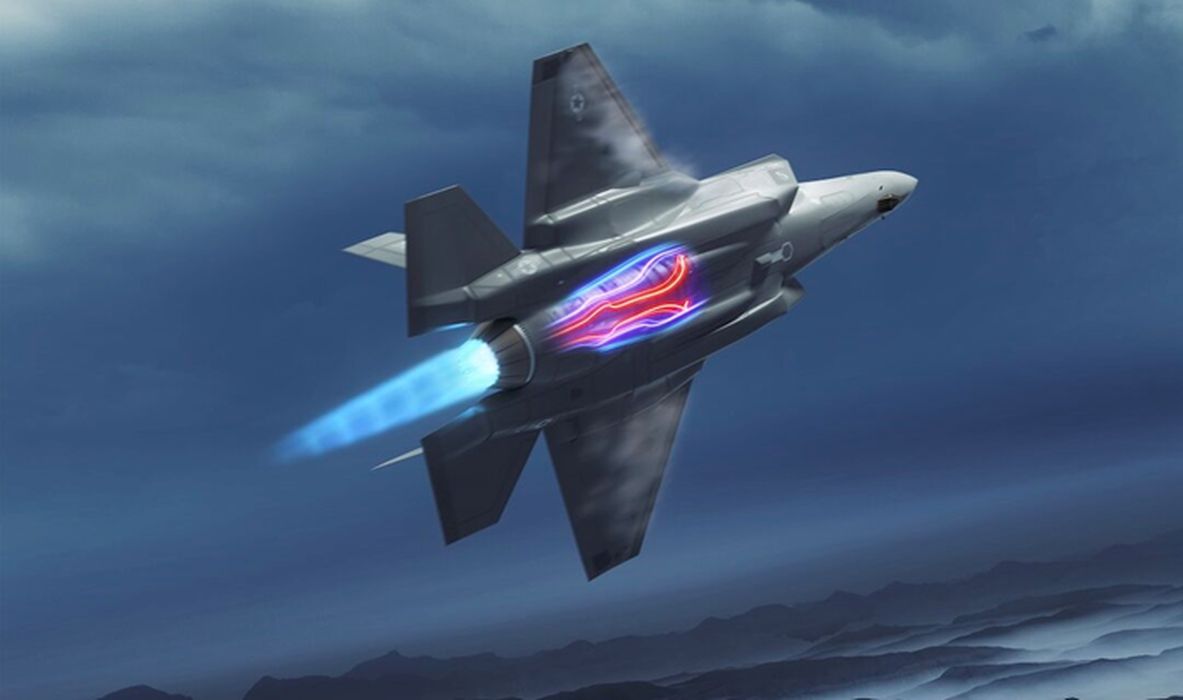
Charles R. Goulding and Preeti Sulibhavi examine the recent boom in jet engine demand and how 3D printing has assisted this growth.
Jet engines are in high demand now. At the end of 2022, the global aircraft engines industry was valued at US$88B, and the market is experiencing strong demand from the Asia Pacific region.
The three leading jet engine manufacturers are GE, Raytheon/Pratt & Whitney, and Rolls Royce.
GE and Raytheon, the worldās largest aerospace and defense company by sales, both reported profits that beat market expectations in the first quarter of 2023. And the International Civil Aviation Organization expects the global airline industry to return to operating profitability by the fourth quarter of 2023, after three consecutive years of incurring losses.
GE
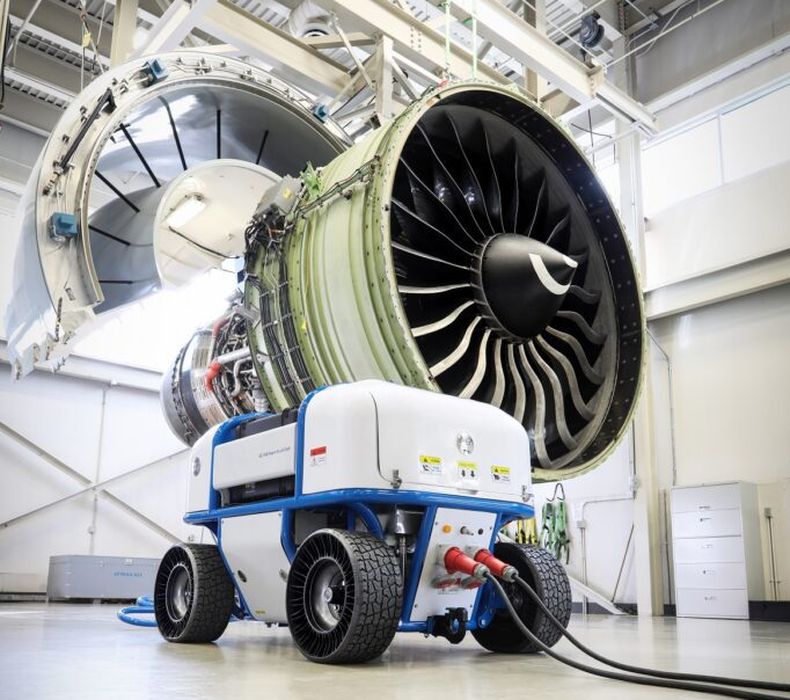
GE is taking advantage of 3D printing technologies. In fact, GEās Avio Aero business develops a Catalyst engine that is in part built with 3D printers and can be used in the Airbus EuroDrone surveillance vehicle.
More importantly, GE is exploring ways to harness data, use AI, automation and 3D printing to find current MRO and supply chain solutions.
Raytheon/Pratt & Whitney
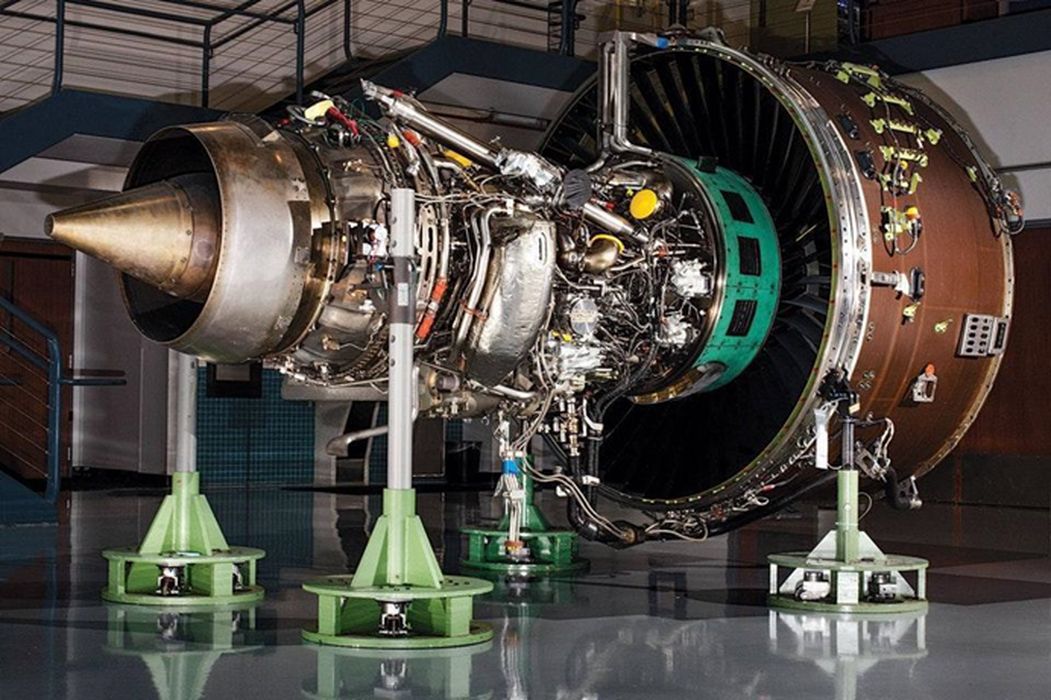
Raytheon/Pratt & Whitney have been making advancements in 3D printing technology for aerospace and defense. Pratt & Whitney and Raytheon have extensive knowledge across various platforms and applications. Raytheon Technologies is a launch participant of President Bidenās AM Forward initiative, a new program encouraging companies to explore the use of additive manufacturing to transform supply chains and drive innovation.
Raytheon Technologiesā commitment includes seeking small-medium-enterprise manufacturersā involvement in over 50% of its requests for quotes on products manufactured using additive technologies, as well as seeking to simplify and accelerate the procurement process of AM parts.
The use of 3D printed components such as fuel nozzles help to increase fuel efficiency and reduce costs at the same time.
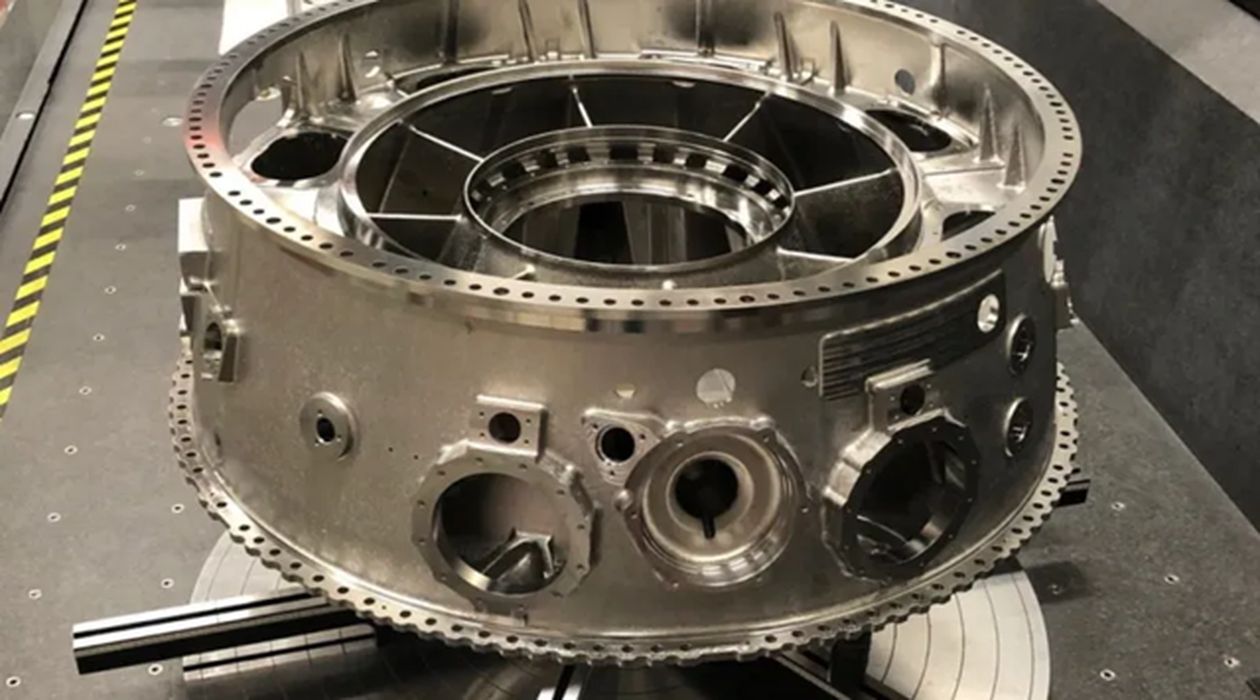
There are more ways in which 3D printing can assist jet engine manufacturers. When OEM parts are in short supply or MRO shops are overburdened, 3D printers can really speed up the whole process to meet increasing demand. MRO shops are responsible for informing engineers on how to update work instructions for a part to be repaired to fit form and function then be returned to the jet engine.
Rolls-Royce has added to their jet engine portfolio by introducing UltraFan. This engine is 25% more fuel-efficient than first generation Trent engines and can help create sustainable air travel.
UltraFanās intermediate compressor case (ICC) was manufactured in part by metal 3D printing techniques. Some of the attaching parts were fabricated via metal 3D printers. GKN Aerospaceās ICC manufacturing process (which was how the 3D printing component was achieve) received support from the Vinnova-funded IntDemo project and the VƤstra Gƶtaland Region in Sweden.
The Research & Development Tax Credit
The now permanent Research and Development (R&D) Tax Credit is available for companies developing new or improved products, processes and/or software.
3D printing can help boost a companyās R&D Tax Credits. Wages for technical employees creating, testing and revising 3D printed prototypes can be included as a percentage of eligible time spent for the R&D Tax Credit. Similarly, when used as a method of improving a process, time spent integrating 3D printing hardware and software counts as an eligible activity. Lastly, when used for modeling and preproduction, the costs of filaments consumed during the development process may also be recovered.
Whether it is used for creating and testing prototypes or for final production, 3D printing is a great indicator that R&D Credit eligible activities are taking place. Companies implementing this technology at any point should consider taking advantage of R&D Tax Credits.
Conclusion
The sky is the limit for future jet engine sales. 3D printing technologies should ride the jet engine wave.