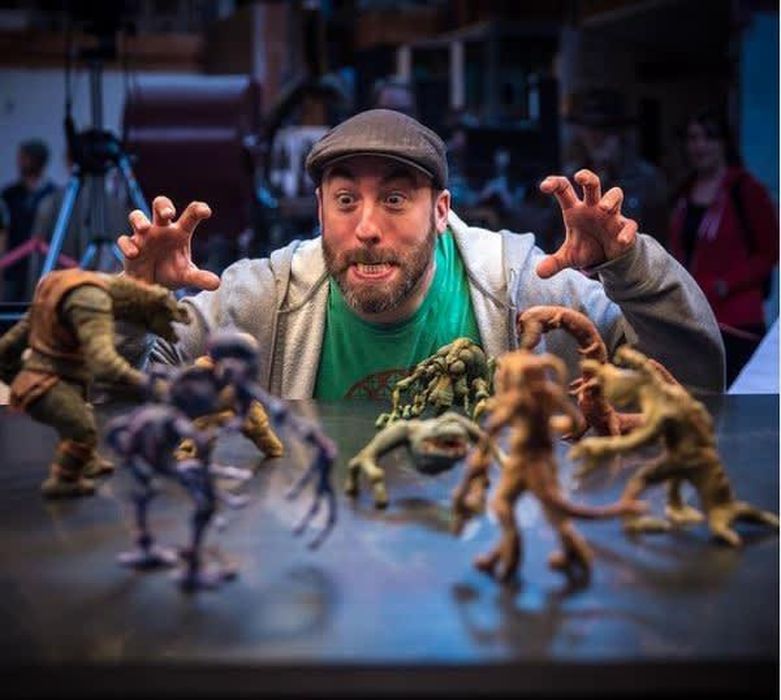
From 3D printers to CNC mills, Thingergy’s Frank Ippolito delves into the manufacturing processes behind filmmaking.
The world of engineering and manufacturing is broad. We’re all well aware of the vast need for things to get made, and humans have been doing it for quite some time. While many of us are quite privy to how things are made, there are some markets that are often still shrouded in mystery … like Hollywood.
The world of filmmaking has changed over the last century, with the inclusion of new camera technologies and computer-generated imagery. In fact, many of the CAD skills that engineers possess can often translate to computer animation and rendering that many studios utilize. Autodesk, for instance, lives in both the CAD/CAM world (with Fusion 360, Inventor, and PowerMill) and the animation world (with Maya).
While technology has continued to improve and expand, sometimes there is still a need for actual props, tactile costumes, and physical sets in films. As the film industry has progressed, we’re beginning to see the marrying of both the digital and physical worlds to create the most lifelike scenes possible.
That’s where Frank Ippolito, owner and operator of Thingergy Inc. , steps in.
Physical Props in a Digital World
Thingergy is a full-service specialty costume, props, FX makeup, and “maker of things” company. Ippolito explained, “Our versatility of ‘making things’ ranges from 10-foot-tall statues of video game characters to flying flame-throwing dragons to hordes of costumes for movies and television.” The company’s core business is primarily TV, movies, and video game companies, including Ubisoft, EA, Star Wars, HBO, Netflix, and many others.
“What we actually do could be anything at any given moment and constantly changes from day to day,” Ippolito continued. “Part of the shop could be casting body parts for a horror gag. Another part of the shop could be welding a 15-foot-tall aluminum frame for a statue, while someone else might be sewing custom fabric we made into the biggest pair of cargo pants you have ever seen.”
Ippolito’s team thrives on creating something new and has a saying in its shop: “This isn’t the first time we have done something we’ve never done before.” But spending time and money on building physical props and wardrobe begs the question of why it’s needed in our ever-expanding digital toolbox. While there are still some uncanny valley challenges when creating realistic digital people, arguably most things can be created in a digital environment.
“Practical effects help create realism between performers and their surroundings,” Ippolito explained. “CGI can elevate that experience to bring that performance outside of what practical applications can’t physically do. Better technology leads to better practical effects and computer-added effects—together, the movie and TV industry is just going to keep blurring that line of reality. One of the biggest conflicts you hear in our industry, special effects and movies/TV, is the use of advanced technology. Sometimes people have a hard time adapting to the change of how movies are done now with CGI and new tech. We understand things change and embrace technology and old-school techniques here at Thingergy.”
Read more at ENGINEERING.com