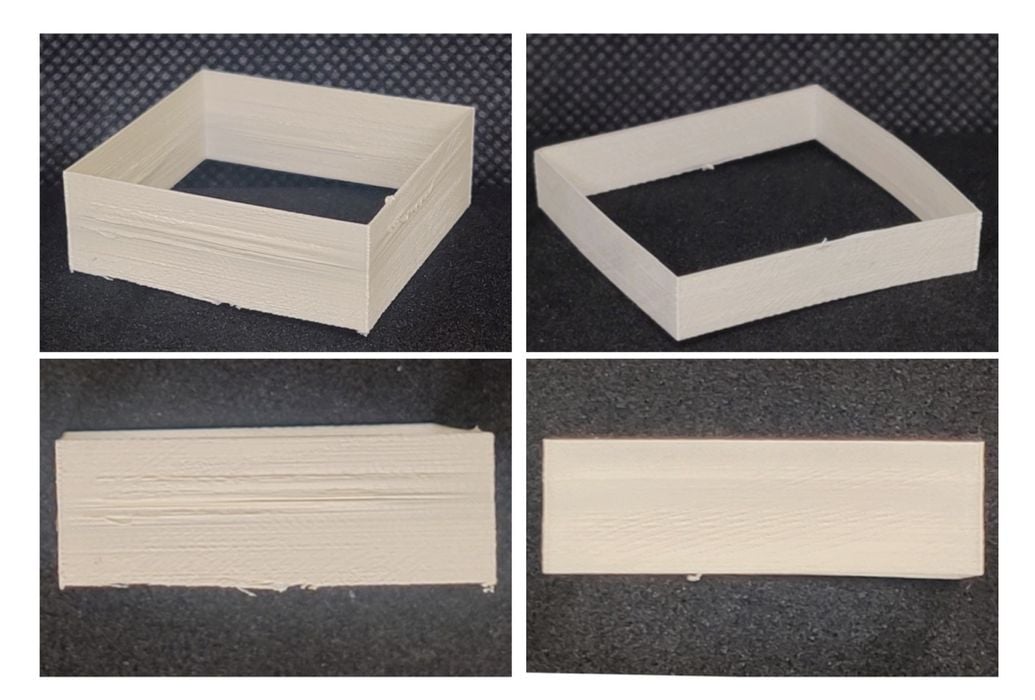
Researchers have developed a framework for continuously tuning flow control on FFF 3D printers.
Flow control is one of the most important factors that determine the quality of a print. However, in basic 3D printing configurations itās set once for the entire job. That opens up the possibility of variable flow rates ā often because the input filament is not of a consistent diameter and other factors.
Some more advanced 3D printers use a layer by layer method to control flow rates. For example, a fresh layer can be scanned and compared to the expected results, and the flow rate would be adjusted for the next layer.
That approach is better, but not optimal. Here the researchers have developed a novel framework that can adjust flow rates based on sensor readings on a continuous basis throughout an entire print job.
How is this done? They are using an approach they call āFCPā, or āForce Controlled Printingā. This involves the installation of a force sensor on the extruder that can reveal the amount of force taking place in real time. Their algorithm then uses this data to adjust extrusion. They explain:
āIn Force Controlled Printing (FCP) for FFF, a sensor is installed in the extruder assembly to measure the force applied onto the filament while extruding it through the nozzle during printing. Unlike the conventional approach, where the filament driver speed is predefined, in FCP the driver speed is continuously adapted by a controller to maintain the measured driving force at a desired and constant reference value. The printing performance of this technique strongly depends on the controllerās performance. PID controllers can be used for this application, but only a well-tuned PID controller will properly regulate the extrusion process while dealing with external disturbances.ā
The data is run through a Bayesian Optimization process, which is a mathematical approach for optimizing compute-heavy functions, particularly where only data points are input. Thatās precisely the case here, as the force sensor provides intermittent data during the print job.
This flowchart explains the workflow that is executed during print operations:

Does this approach work? At top you can see an example of their FCP-FFF process, with a clear difference between the before (left) and after (right) samples.
They were able to test the method multiple times and subsequent measurements showed that the flow rate error had a āsignificant reductionā.
This is very good news for FFF 3D printing. It means that it would be possible implement this approach on inexpensive desktop 3D printers, as it requires only the introduction of a new sensor. Some equipment already has such sensors.
The rest of the method is just software that could be implemented in the firmware of the machines. This could be a way to dramatically increase the print quality on almost all FFF 3D printers.
Via ArXiv (PDF)