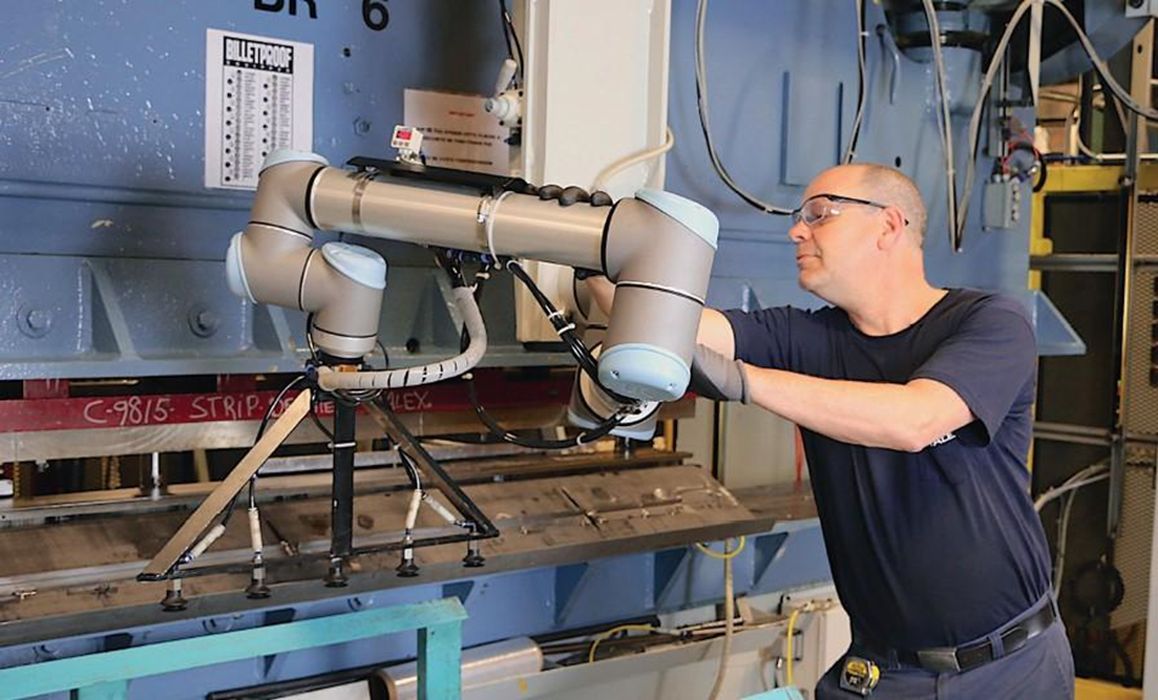
Charles R. Goulding and Preeti Sulibhavi suggest 3D printing could greatly aid the progress of cobots.
Cobots or collaborative robots have been enjoying increasing sales growth related to labor shortages, rising labor costs and the drive for automation. In 2021, the cobot market saw a 40% growth in sales and most analysts predict that by 2026 the cobot industry will be valued at over US$2B.
Destaco, which was originally the Detroit Stamping Company is a business unit of Dover Corporation (Dover) and has been a long-standing manufacturer of end-of-arm affecters, long before the robot age.
In fact, Destaco was an existing business unit of Dover when I joined the company in 1977, over 40 years ago. The new cobot tooling portfolio includes the following tools:
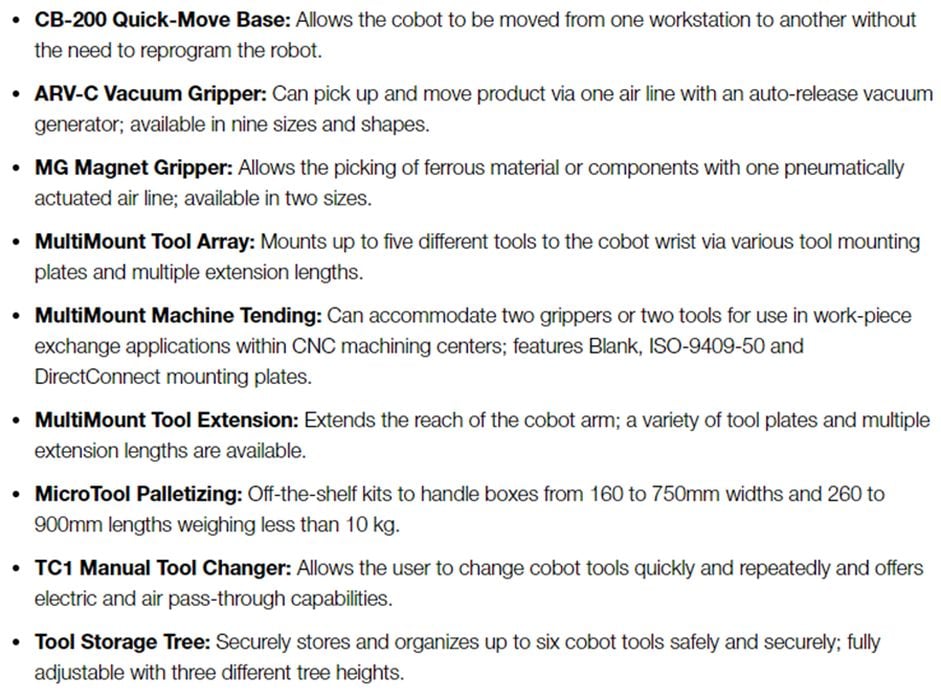
We have previously written about the synergy between cobots and 3D printing. The more cobot tooling that is available increases cobot utility and increases the demand for cobots.
Destaco’s portfolio of cobot tooling for applications employs small payload cobots. The tooling is designed for gripping, palletizing, machine tending, tool changing, and tool extension applications up to 10 kg payloads.
Destaco offers kits that feature user-selected accessories, along with the hardware and tools needed for installation. The tooling is compatible with cobots that have an ISO 9409-1-50-4-M6 end-of-arm mounting pattern. Blank robot and tool plates are offered for users who want to use their own mounting patterns.
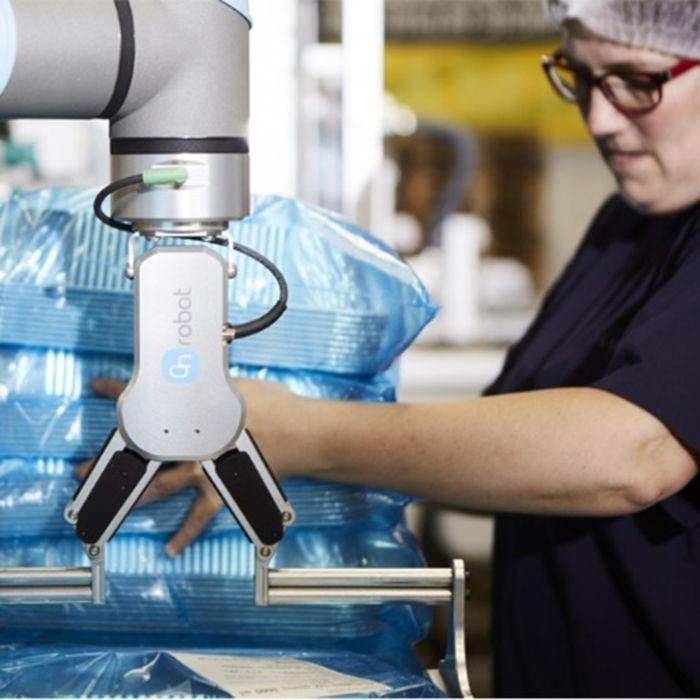
It is inherently obvious that 3D printing is a good fit for cobot design and development. End-effectors for cobots are a perfect 3D printed application. It has been utilized in various verticals including the food, manufacturing, hospitality, and healthcare industries.
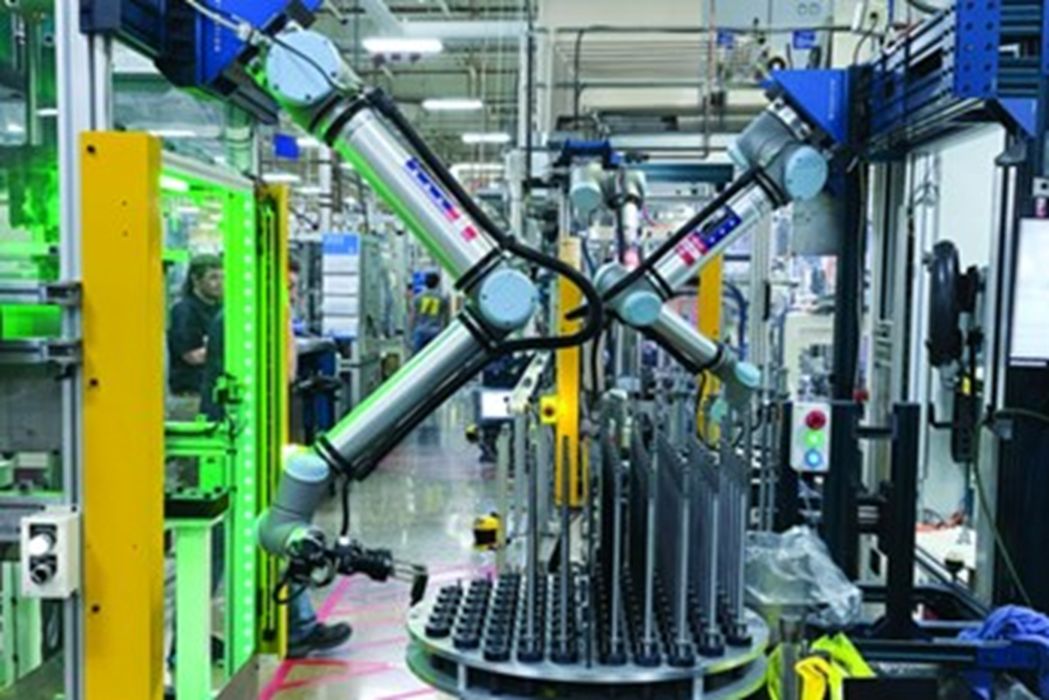
Cobots and 3D printing working together to automate a Thyssenkrupp Bilstein plant in Ohio [Source: Additive Manufacturing]
At Thyssenkrupp Bilstein’s, Hamilton, Ohio production plant, the facility’s piston rod and valve cell illustrate how cobots and 3D printers are working together to automate the manufacturing industry. 3D printers are fabricating the hardware that is vital to proper cobot functioning, and the cobots are doing the work of humans, who can now focus on more higher-level tasks.
The Research & Development Tax Credit
The now permanent Research and Development (R&D) Tax Credit is available for companies developing new or improved products, processes and/or software.
3D printing can help boost a company’s R&D Tax Credits. Wages for technical employees creating, testing and revising 3D printed prototypes can be included as a percentage of eligible time spent for the R&D Tax Credit. Similarly, when used as a method of improving a process, time spent integrating 3D printing hardware and software counts as an eligible activity. Lastly, when used for modeling and preproduction, the costs of filaments consumed during the development process may also be recovered.
Whether it is used for creating and testing prototypes or for final production, 3D printing is a great indicator that R&D Credit eligible activities are taking place. Companies implementing this technology at any point should consider taking advantage of R&D Tax Credits.
Conclusion
It’s nice to see a long-time metal stamping company grow by innovating to help the robot industry to further its growth.