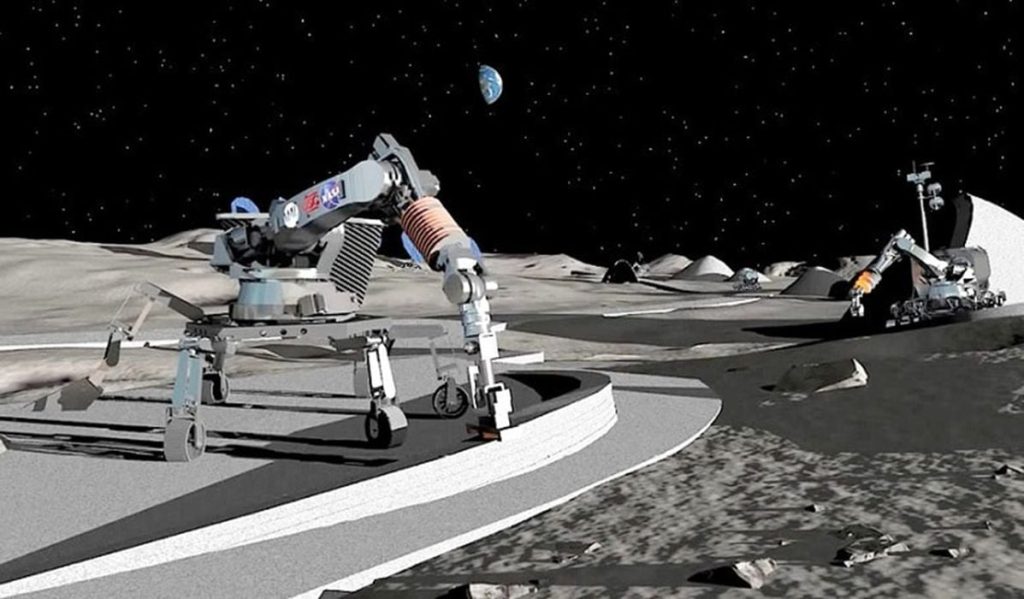
Charles R. Goulding and Preeti Sulibhavi review a webinar focusing on use of additive manufacturing in space applications.
On Thursday, November 10, 2022, the Additive Manufacturing (AM) Coalition held a forum titled, “The Use of Additive Manufacturing in Space.” The webinar featured industry experts including:
- Mr. Foster Ferguson, Global Director, Aerospace, Stratasys
- Dr. Ken Savin, Chief Scientific Officer, Redwire Space
- Dr. Matt Gratias, Director of Government Business Development, Relativity Space
Each of the companies that the speakers represented are worth noting.
Redwire Space
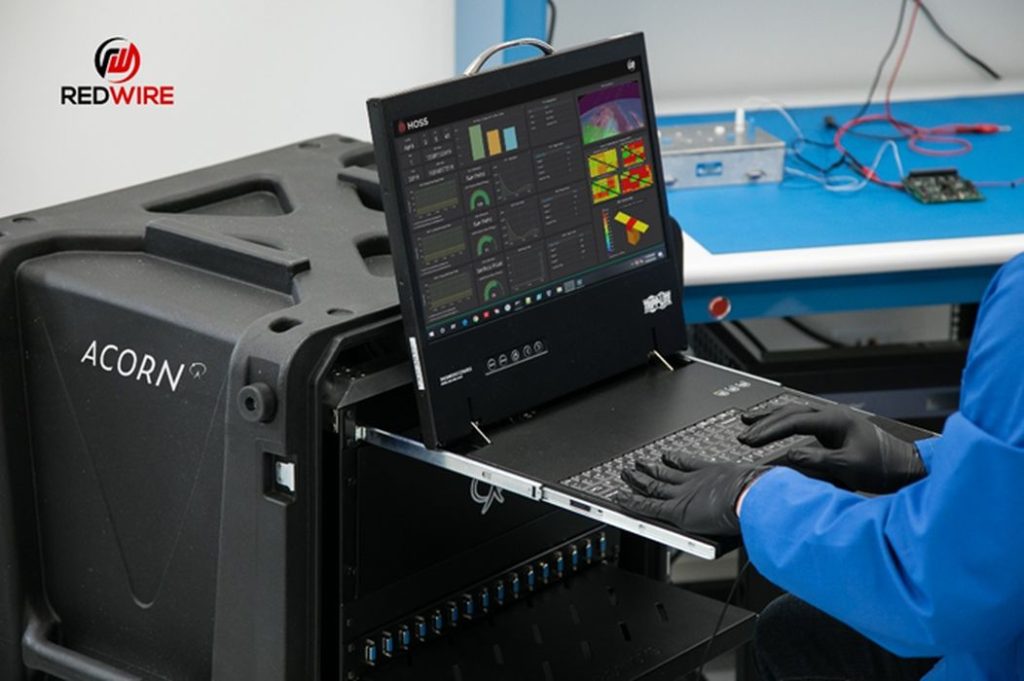
Redwire provides critical capabilities that enable complex space missions including civil, commercial, and national security missions.
Some of Redwire’s projects include space commercialization, digitally-engineering spacecraft, on-orbit servicing, assembly and manufacturing, advanced sensors and components, and space domain awareness and resiliency.
Dr. Savin discussed the work his team is doing in terms of 3D printing. Redwire manufacturers products in space as well. These are for items that cannot be produced in the earth’s atmosphere such as a micro G, which is a loop of metal and dipped into sugar water that creates a unique object that can only be created in a zero gravity environment. Makerspace is used for this application.
Bioprinting in space has certain advantages. The images are 3D due to the lack of gravity flattening the structures. This creates opportunities for tissue printing for organs or tissue therapy that can have pharma applications and model development as well. The level of detail that Savin’s team gets in space is not possible on earth. This means that Redwire has ISS payloads that include 3D printers and bio-fabrication facilities (for 3D printing tissue with bioinks) as well.
Redwire also utilizes metal 3D printers for repairing spacecraft parts in space instead of waiting for parts from earth to reach the craft in time.
Relativity Space
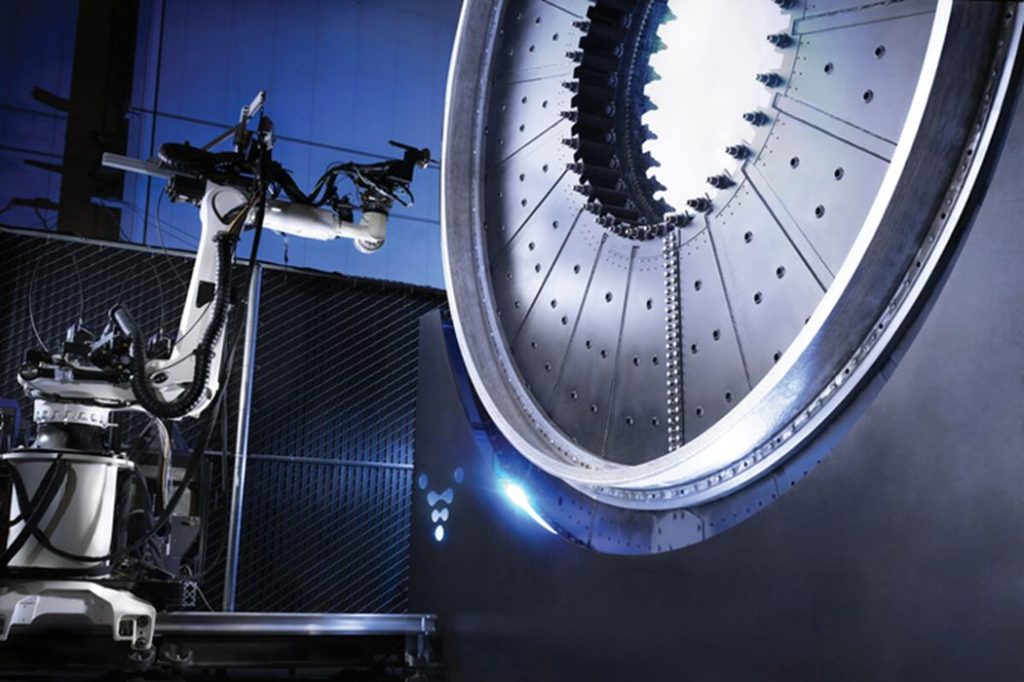
Relativity Space is a company dedicated to tackling unstructured data challenges. Matt Gratias discussed how Relativity is using 3D printing to design, build and fly entirely 3D printed rockets. Terran 1 is a rocket that is entirely 3D printed by Relativity. Relativity’s “Stargate” platform allows for scalable autonomous platforms that shift physical complexities in 3D printing into design complexities. Stargate also requires fewer parts and can accommodate unprecedented build volumes.
The flexibility of having a large-scale AM platform in space is a priceless resource as many teams do not know what they may or may need or encounter during their space mission.
Stratasys
And, of course, there is Stratasys, an industry leader with US$600M plus in revenue, that needs no introduction. Mr. Ferguson, Global Director, Aerospace at Stratasys covered how AM has grown in the aerospace industry, from rapid prototyping to jig & fixtures.
Then, as polymers got more advanced, tooling direct print flight parts became possible. Now Stratasys is providing main parts in some of the major space crafts. Considerations for 3D printing space components include extreme conditions (heat and cold) among other items. Stratasys has been successful in reducing the number of parts required for aerospace parts as well as the time it takes to produce them in addition to the cost.
Mr. Ferguson discussed certain proprietary materials such as what they developed for fiber optic routing components. Stratasys has used 3D printing to produce space vehicles that will carry cargo to replenish supplies at the International Space Station (ISS). Stratasys is proud to be working with Blue Origin on its current and future projects.
The Research & Development Tax Credit
The now permanent Research and Development (R&D) Tax Credit is available for companies developing new or improved products, processes and/or software.
3D printing can help boost a company’s R&D Tax Credits. Wages for technical employees creating, testing and revising 3D printed prototypes can be included as a percentage of eligible time spent for the R&D Tax Credit. Similarly, when used as a method of improving a process, time spent integrating 3D printing hardware and software counts as an eligible activity. Lastly, when used for modeling and preproduction, the costs of filaments consumed during the development process may also be recovered.
Whether it is used for creating and testing prototypes or for final production, 3D printing is a great indicator that R&D Credit eligible activities are taking place. Companies implementing this technology at any point should consider taking advantage of R&D Tax Credits.
Conclusion
The webinar provided great insight into the developments of 3D printing in space. Particularly the use of the zero-gravity environment to 3D print unique metal parts and bioprint tissues as well.