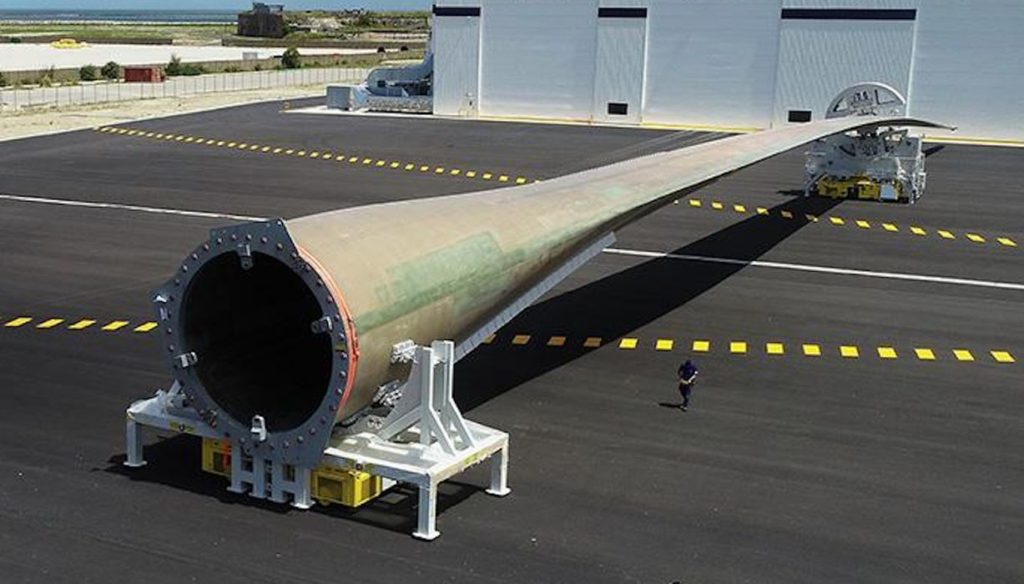
An announcement from GE Renewable energy describes a partnership with voxeljet and Fraunhofer IGCV to efficiently produce wind turbines.
Renewable energy has become a technology with dramatically increasing use, and a key component of that sector is wind energy. Wind energy is harvested through turbines that spin as the wind passes by, but thereās one problem.
The most efficient wind turbines are those with the largest blades. The large blades require large towers ā otherwise the blade tips would strike the ground. In other words, future wind turbines are best made at huge scales.
That poses a problem.
Building these enormous parts in traditional factories means they must be transported to the build site. Often the build sites are located where wind flow is optimal, which are typically in odd locations not near the factory and sometimes without proper road access.
Transport of the large parts also means traversing the roadway network, and there are significant dimensional constraints. Sometimes this means large items have to be split into multiple components that are assembled on site, and also requiring additional transportation costs.
For an industry working towards lowered emissions, this doesnāt sound like a success story.
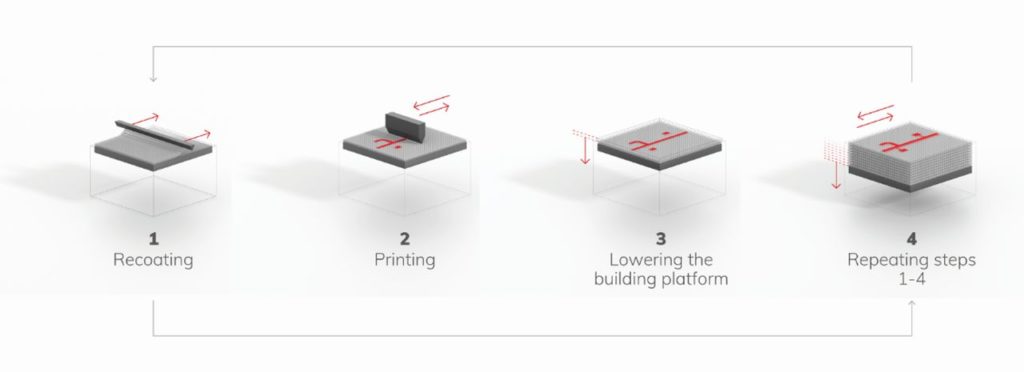
The new concept is to produce the larger parts directly on the build site. voxeljet equipment will produce a sand print, which will become the mold for a massive casting. GE Renewable Energy said some parts could be as large as 9.5m (31ft) in length. They said:
āThe Advance Casting Cell (ACC) 3D printer under development will benefit from financial support from the German Federal Ministry for Economic Affairs and Energy and will be capable of printing molds to cast components for the nacelle2 of the GE Haliade-X that can each weigh more than 60 metric tons, reducing the time it takes to produce this pattern and mold from ten weeks or more to just two weeks.ā

voxeljet will be developing a much larger 3D printer to take on this role, but that should not be an issue because their binder jet process is easily scalable. However, the company has never built a device of that size yet. Currently their largest device is the massive VX4000, which has a build volume of 4000 x 2000 x 1000 mm. Itās about the size of a small house.
But the hypothetical āVX10000ā will be significantly larger.
The intention is to erect the new 3D printer near the build site, and then produce casts for the up-to 60 tonne turbine parts.
GE Renewable Energy Senior Additive Design Engineer Juan Pablo Cilia said:
āThe 3D printed molds will bring many benefits including improved casting quality through improved surface finish, part accuracy and consistency. Furthermore, sand binder jet molds or additive molds provide cost savings by reducing machining time and other material costs due to optimized design. This unprecedented production technology will be a game changer for production efficiency allowing localized manufacturing in high cost countries, a key benefit for our customers looking to maximize the local economic development benefits of offshore wind.ā
I expect the method here will be to erect the 3D printer in a shipping port, where the turbine parts will be cast and then moved directly onto ships to take them offshore to the build site. This means the 3D printer and casting operation need be set up only once in a region, as it could serve a large offshore area by sea transport.
voxeljet CEO Dr. Ingo Ederer said:
āWhile offsite on-demand 3D printing provides many benefits for small quantities of cast parts, running a 3D printing system on-site leverages the technology to its fullest capacity. Given the demand for offshore wind turbines, that will help a lot to fulfill project schedules and high market demands. With our productive āBinder-Jettingā technology in combination with our experience in large format industrial 3D printing, we are serving customers in the foundry industry for over 20 years. It is our mission to bring 3D printing into true industrial manufacturing and we are therefore very excited to be part of this groundbreaking project.ā
This is a very good move for voxeljet, because the operation will make offshore wind energy construction more efficient and more eco-friendly. Itās also a long-term move as the demand for wind energy will only grow in the future, and any āport factoryā they equip will be busy for many years.
First trials of the system are expected early next year.
Via voxeljet and GE Renewable Energy