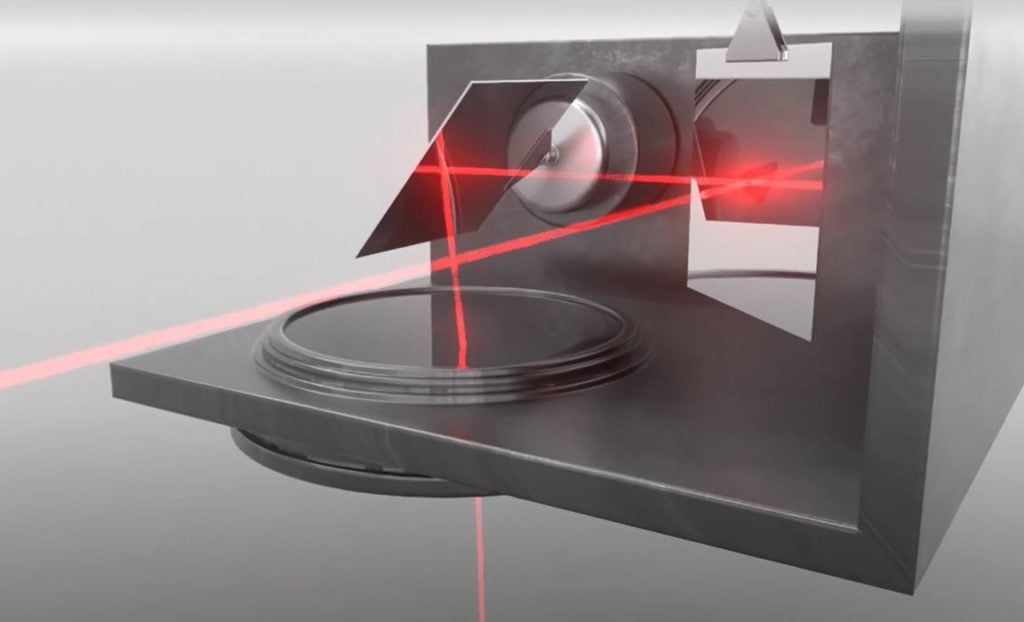
Tecnica provided an interesting explanation of a common issue in SLS 3D printers, and their unique solution.
The SLS 3D printing process should, at first, seem pretty straightforward: a laser selectively fuses thermoplastic particles on a flat bed, layer-by-layer. Easy, correct?
Not so fast. Itās actually quite a bit more involved, even though the job of delivering a precise amount of energy to a given spot on the bed should be a simple thing to do.
Donāt you just sweep the laser across the bed to accomplish this?
Not exactly. Lasers are expensive and heavy components, and it is generally impractical to build a mechanism that can precisely tilt an entire laser, particularly at the speeds necessary to build a part in a reasonable time.
Instead most SLS machines use a galvanometric solution. In this approach the laser is fixed in place, and its beam strikes a tilting mirror. The mirror can easily redirect the beam to any portion of the print surface, and do so quickly.
Is that the answer? Yes, it is for many 3D printer manufacturers, but there are issues.
One major problem is that as the mirror tilts, the shape of the illuminated area on the print surface (the ālaser dotā) becomes elliptical. You can try this yourself by pointing a light at a flat surface, measuring the lighted area, and the measuring again when the light is tilted.
As the area of the laser dot enlarges, the amount of energy per area decreases. In other words, it would take longer to melt the thermoplastic. This means that the print parameters must account for this unexpected energy drop at the extremes of the build chamber.
Tecnica has a wonderful video showing this problem with an animation:
Of note is the laser dot cross-section and the uneven energy intensity map. You can see how the laser dot changes in shape as the print proceeds, and how the energy varies across the print surface. That can lead to improperly formed parts, or parts with inconsistent strength.
Tecniaās solution is rather interesting. They wanted to ensure the beam hits the print surface with a consistently-sized laser dot, yet at the same time avoid moving the laser itself.
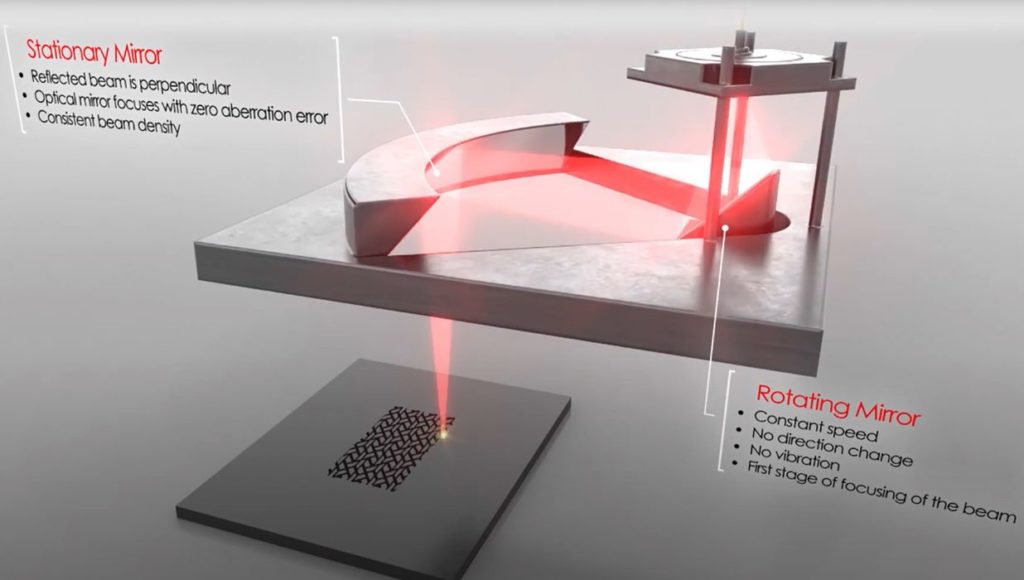
Their approach was to design a uniquely-shaped curved mirror. The laser sends a beam to a simple rotating flat mirror that redirects light energy across the curved mirror. The curved mirror directs the beam to all portions of the print surface and ensures the laser dot is consistently sized. This means a consistent amount of energy is delivered to each part of the print surface, regardless of location.
Watch this video to see how it works:
That approach certainly works, and should result in better SLS 3D printed parts.
The one issue I see with the Tecnica approach is that the specialty curved mirrors may be expensive to produce. They would also be designed for a particular build volume, meaning if a larger machine were required, itās likely a new mirror would have to be produced. That could also raise costs, as a single mirror style could not be mass produced for all the equipment.
Nevertheless, Tecnica has an interesting solution to a persistent SLS 3D printing problem.
Via Tecnica