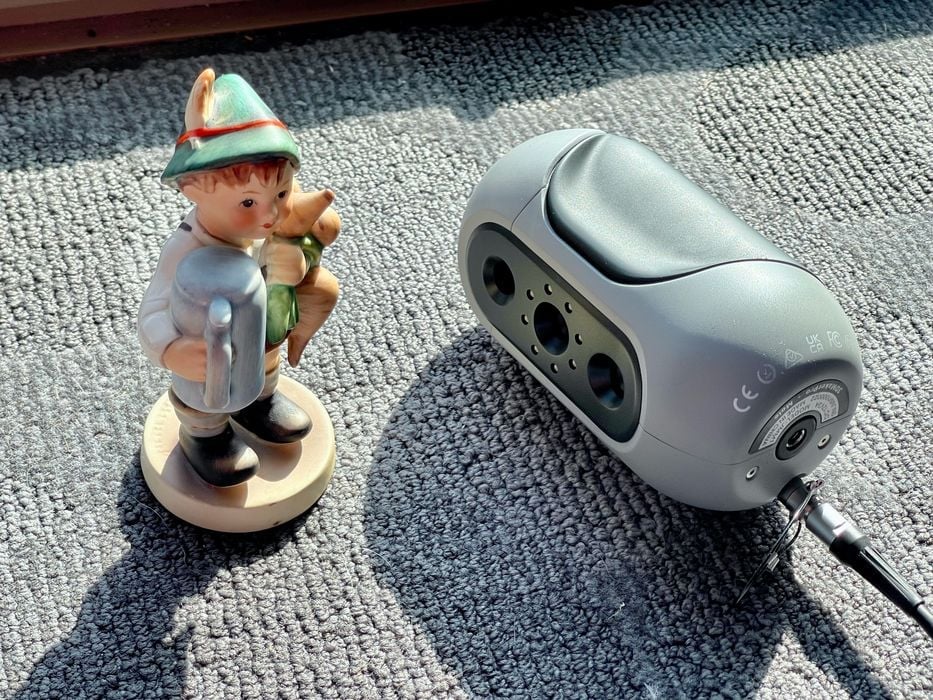
Our look at the new Mole 3D scanner continues with operations and alignment.
This is part two of a three part series, please read parts one and three.
Mole 3D Scanner Operations
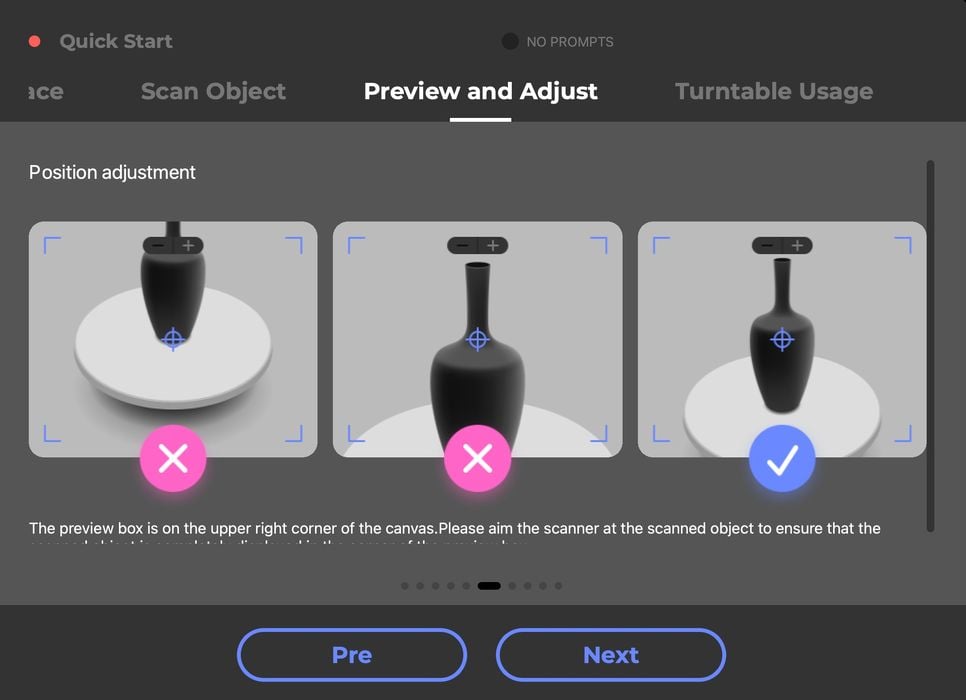
The Mole has two basic operational modes: handheld and turntable, which you would choose depending on the nature of the subject.
For example, if the subject is a small item that would fit on the turntable, youâd use that mode. On the other hand, if your object is bigger, the handheld mode would be more useful.
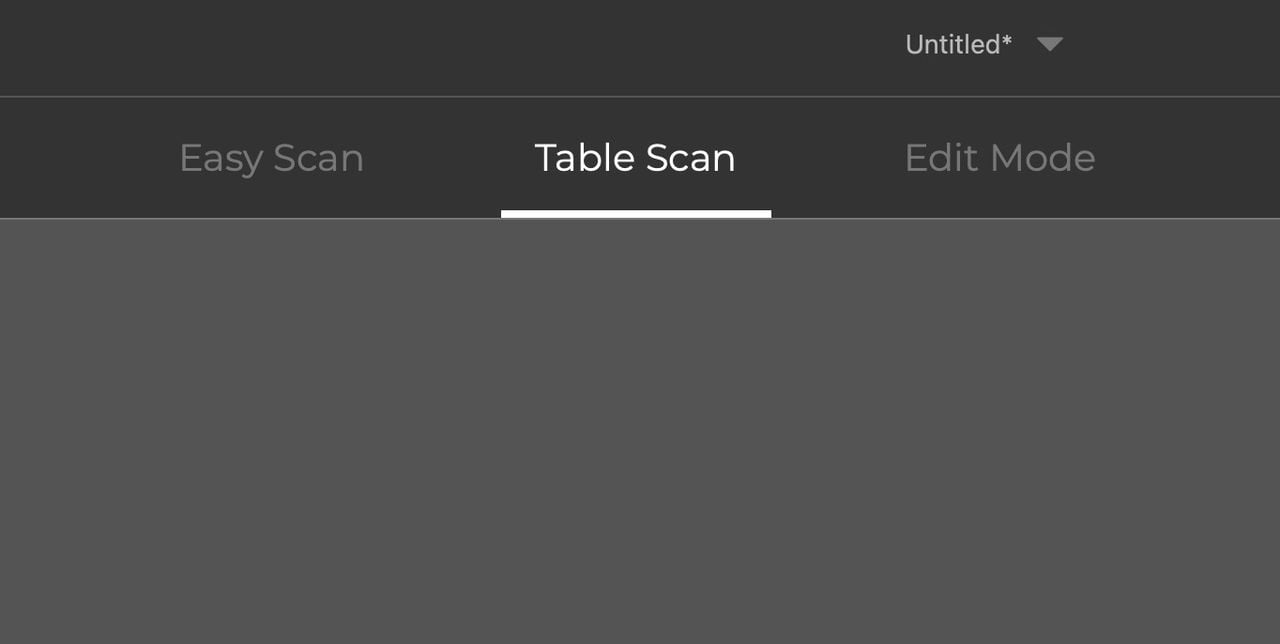
Unfortunately, these modes are not quite as clear as Iâve portrayed them. JMStudio calls them âEasy Scanâ and âTable Scanâ. âEasy Scanâ is handheld mode, and âTable Scanâ is turntable mode.
The 3D scanning workflow used by the Mole more-or-less follows our basic âTen Steps of 3D Scanningâ. Our previous story describes these in detail, but in point form they are:
- Calibrate
- Scan
- Scan again
- Align
- Fusion
- Meshing
- Texturing
- Editing
- Simplification
- Export
In a sentence, the scans collect point clouds of the object in 3D space. These are then âfusedâ into surfaces, which are transformed into meshes (STL, OBJ or 3MF), and then textured before finally exporting the file for use in other applications.
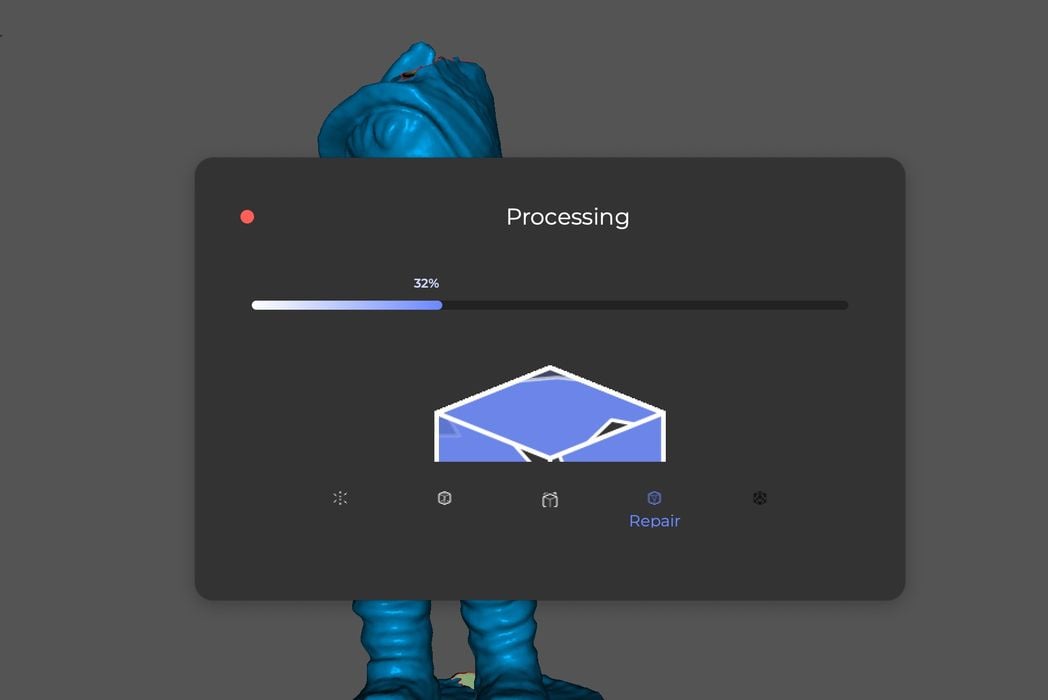
Itâs quite important to understand these steps before you begin using JMStudio, because the software doesnât always make it clear which step youâre on and what happens next. However, once you do understand the workflow and 3DMakerproâs terminology, itâs pretty easy to get through it with JMStudio.
The handheld mode is easiest to understand opposite the workflow: you perform the scan, then process it to produce the meshed object.
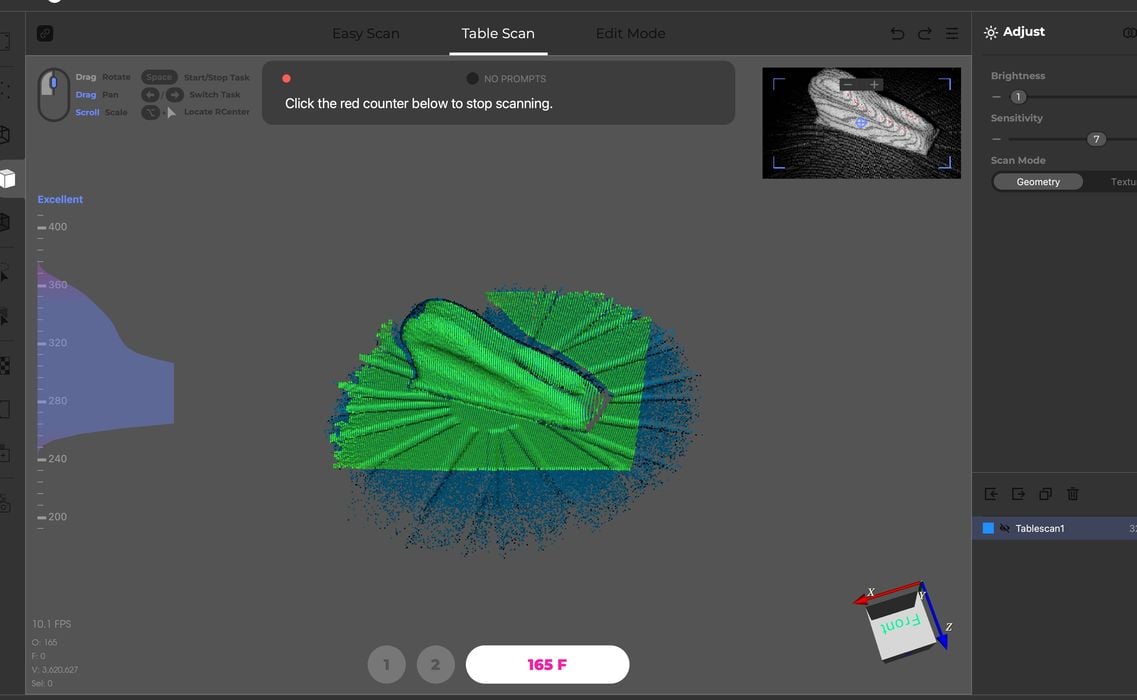
The turntable mode is at first a bit confusing, and thatâs because 3DMakerpro is trying to make things easier later in the process. The problem theyâre solving is that when in turntable mode, you always end up scanning the object â and the turntable itself.
The turntable must be removed from the 3D model because itâs not required. Normally this would require a bit of editing to clip it out, but JMStudio can do this automatically.
Hereâs how it works: when in turntable mode, JMStudio presents you with a mysterious âInitialâ button. What youâre supposed to do is remove your object from the turntable, and hit that Initial button. The scanner then scans the empty turntable â so that it âknowsâ where the turntable is located. Then the next step is to place the scanning subject back on the turntable and hit âScanâ. This captures the point cloud for the object AND the turntable surface.
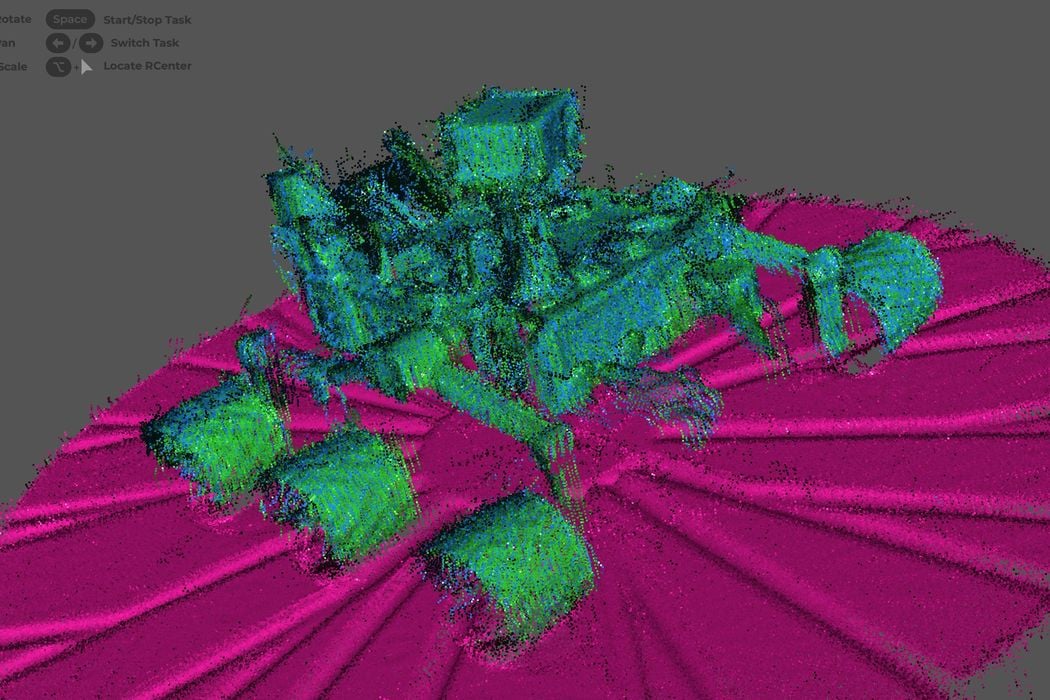
However, when the scan is processed, the software can automatically remove the turntable surface because it knows all about it from the âinitialâ. In fact, the turntable surface shows up in a different color in the scan because it is âselectedâ. Itâs often just a simple matter of âdeletingâ it with a keystroke.
This is a pretty useful feature, but the problem is that this sequence isnât explained well and the software doesnât really help you understand whatâs happening. However, once you know how this works, itâs very easy to do.
Turntable mode is relatively easy to execute, because the turntable performs all the action â the operator just presses buttons.
Meanwhile, handheld mode requires a bit more expertise. The scanner must be moved precisely around the subject, all while keeping the subject in frame. In addition, you canât move too quickly, or the Mole will lose its place in 3D space and youâll receive the dreaded âlost trackingâ message.
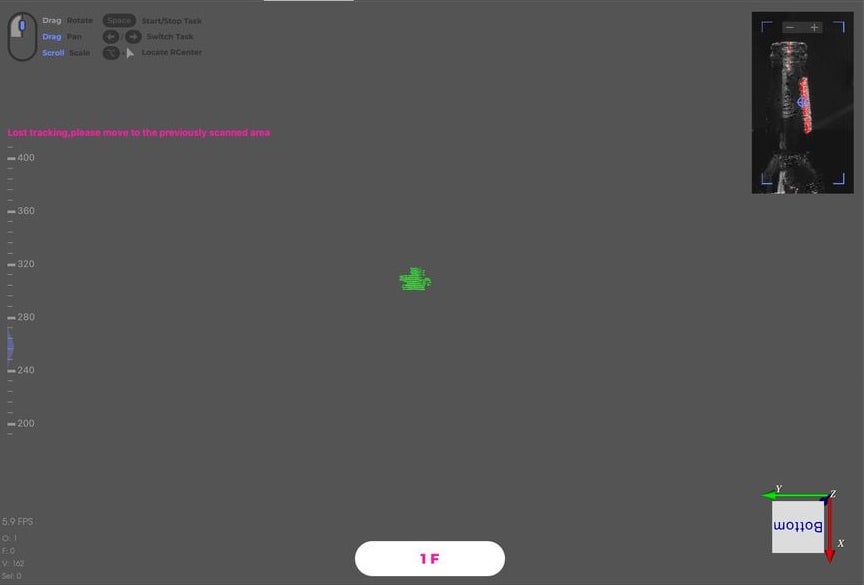
Some 3D scanning systems stop the scan when tracking is lost. However, the Mole has a pretty good method of re-establishing tracking. After receiving the lost tracking message, you slowly move the scannerâs view back to a point previously scanned, and it almost always picks up where it left off.
I found this feature to be essential in making it easy to use the Mole, because I frequently lost tracking. One reason for my aiming issues is that the odd round structure of the Mole makes it somewhat difficult to aim by hand.
Normally handheld scanners have a kind of âpistolâ design where you can intuitively point the device at the subject. However, the Mole is completely round and itâs very hard to tell where it is pointing at any moment.
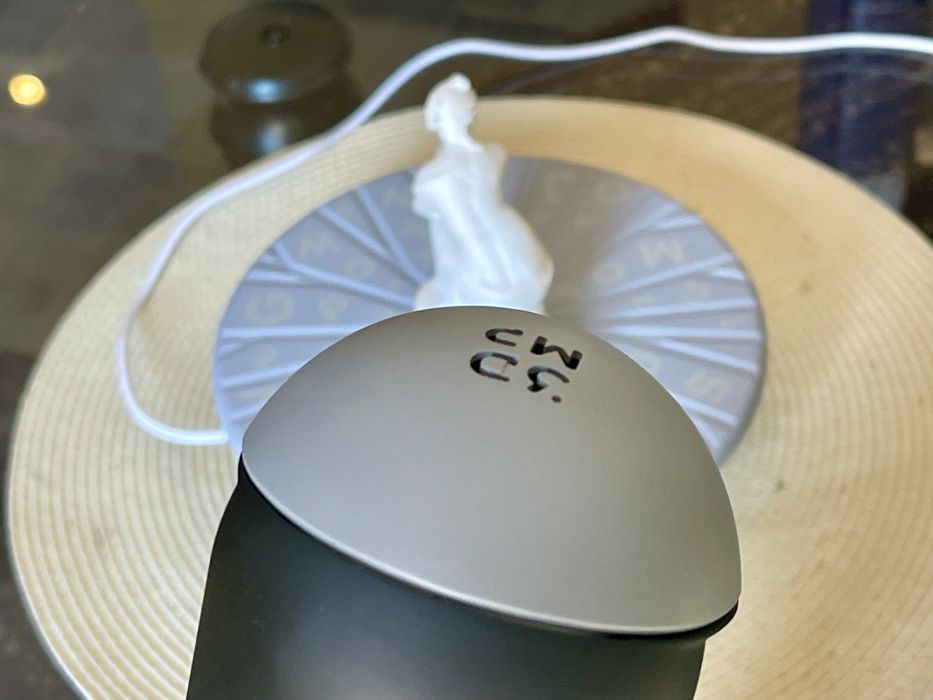
There isnât even any markings on the top of the Mole to clearly indicate where the aim is pointing.
I found the best practice for scanning movement was to keep eyes on the PC screen where the preview image is shown. It takes a bit of hand-eye coordination, but soon youâll get the hang of moving the Mole properly. I found that the act of scanning would get easier each time I performed one.
Iâm told that other versions of the Mole will have the ability to attach a smartphone to the back of the Mole and allow a âdirectâ view of the scene on the smartphone. This would be significantly easier to use, but I was not able to test this mode with my Mole.
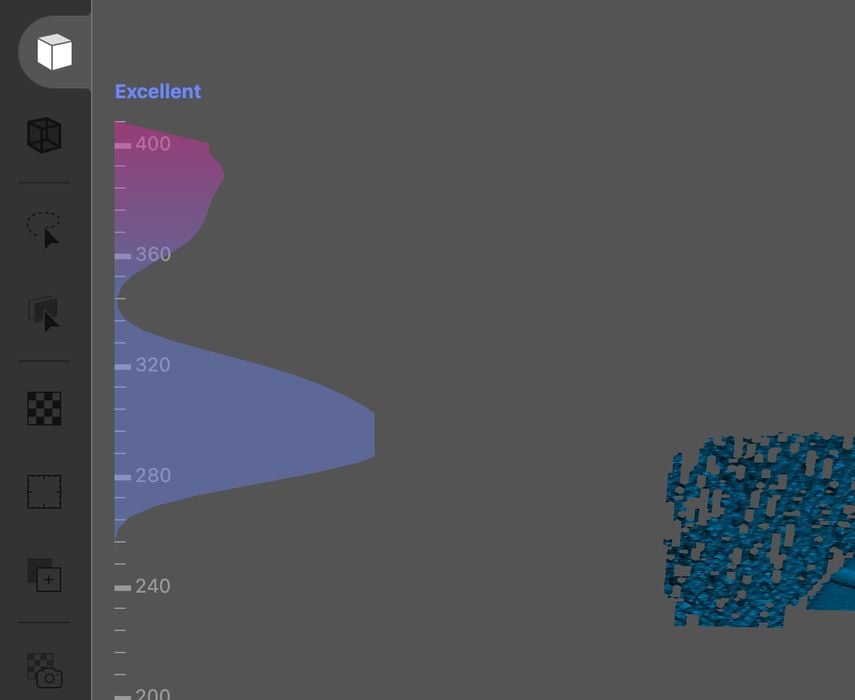
When scanning, JMStudio shows a graph of the current distance between the subject and the scanner. The game is to ensure you are within the âgoodâ range. This is because the scanning process is essentially the act of sweeping a virtual cube across all surfaces of the subject. That cube is at a particular distance from the scanner, and the graph can help you manage that distance.
Mole 3D Scanner Alignment
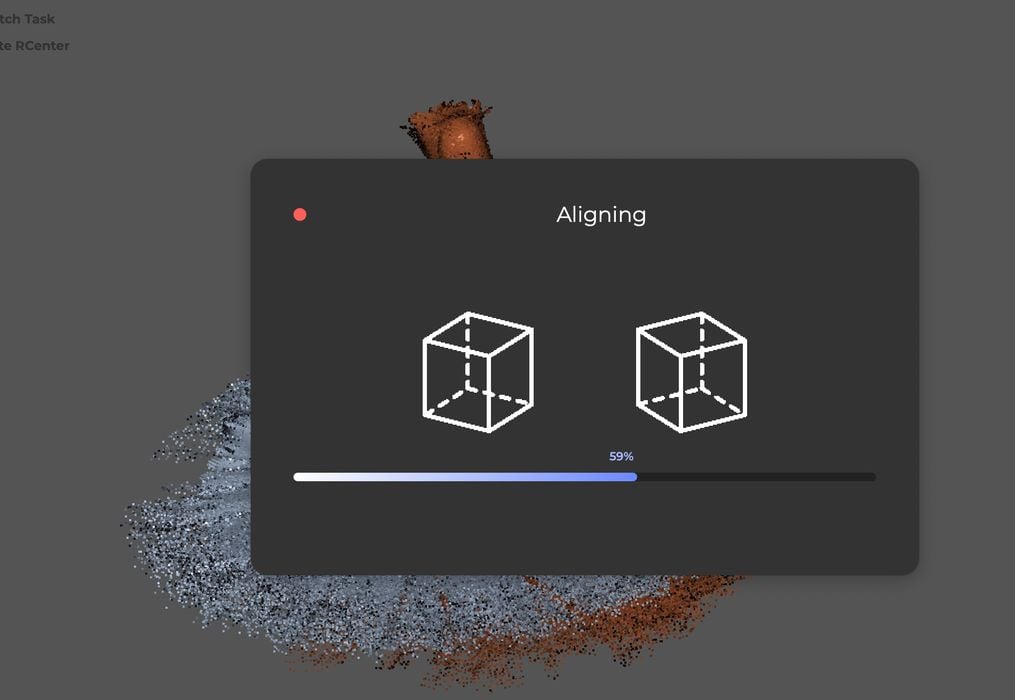
One of the most important features in the software is âalignmentâ. This enables you to capture all sides of an object.
For example, say youâre scanning a bottle. While you might have captured most of the bottle, you didnât capture the bottom of the bottle because it was hidden against the floor or turntable.
The solution to this dilemma is called âalignmentâ. The idea is that you take two different 3D scans, each with different orientations. In the case of the bottle, youâd perform a second 3D scan with the bottle on its side, thus exposing the bottom.
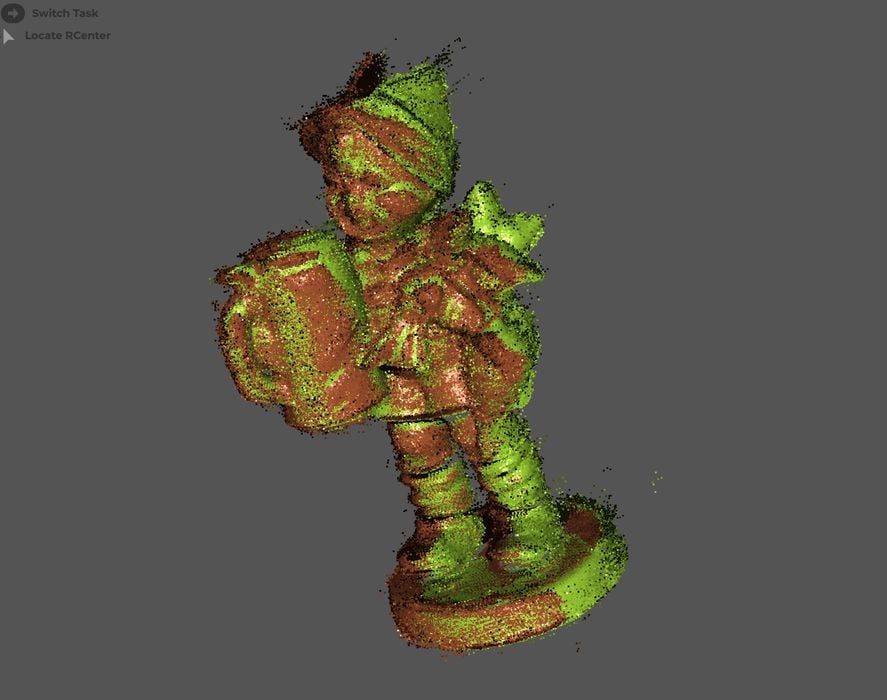
Alignment is pretty easy in JMStudio, and there are two ways to align.
The first, and easiest method is âautomaticâ. This procedure has the software attempting to figure out how the two scans can fit together. I presume this is done by rotating the scans around until they are âcloseâ.
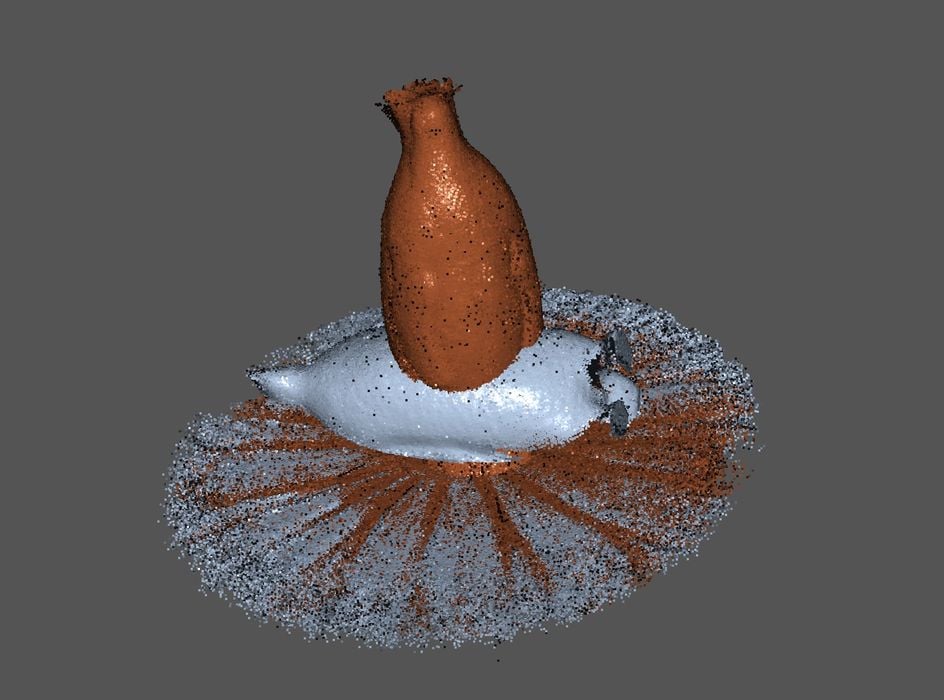
I found the automatic alignment procedure would usually work, but sometimes not. It seemed to depend on the geometry of the subject, with more complex and incomplete scans tending to fail. By the way, an alignment failure is always interesting to observe, as it is usually a wild mashup of your subject.
Should the automatic alignment fail, there is a manual mode.
To manually align scans, you select two scans, which are displayed side-by-side. Then you create âalignment pointsâ by pressing the â+â button.
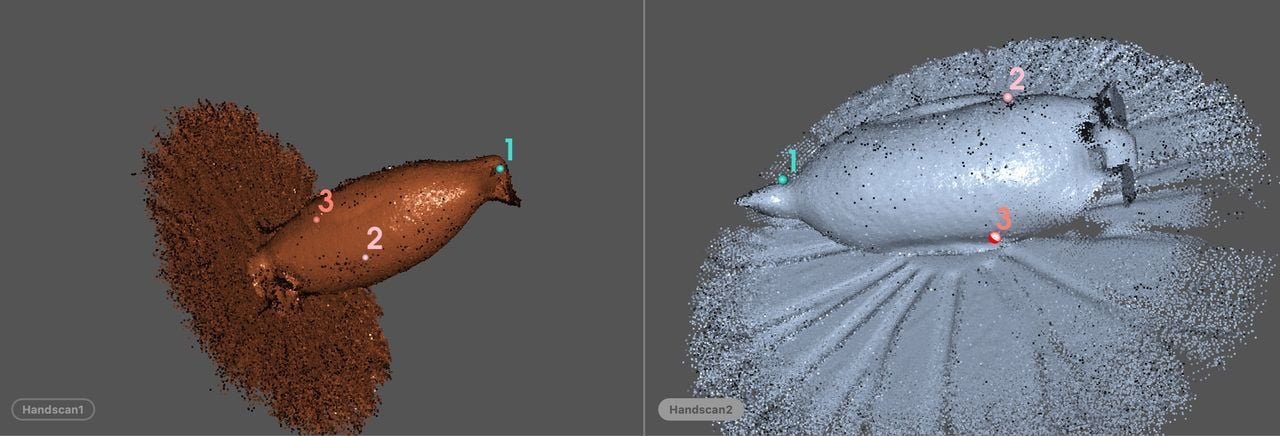
The alignment points appear on both scans, and are numbered 1, 2 and 3. Your job is to move the points on each scan so that they are in the corresponding positions. For example, if scanning a sculpture of a dog, point 1 might be placed on the left front heel of each scan. Point 2 might be placed on the tail of each scan, and point 3 could be on the nose.
These three point locations in 3D space provide a strong hint to JMStudio of how the two scans might be placed together â or, âalignedâ. The software then overlaps the two point clouds and can then process them into a single 3D model including both top and bottom of the subject.
An important tip for alignment is to attempt to capture as much geometry as possible for each scan. Itâs too easy to think, âno problem, that portion will be scanned next timeâ. Except that you might miss it because itâs hard for human brains to keep track of geometry when itâs rotated.
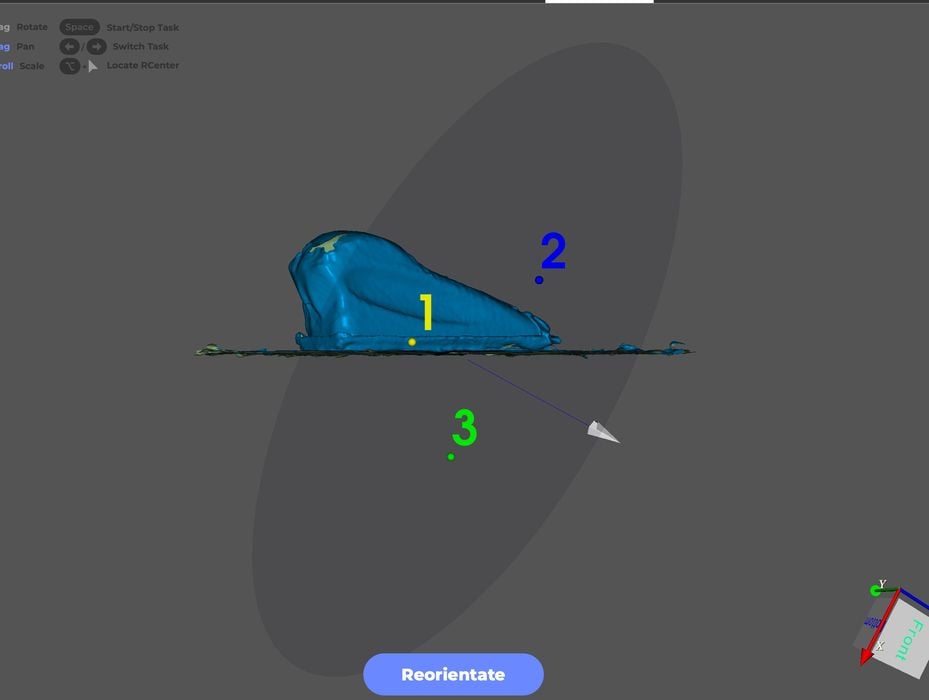
After âfusionâ, the resulting 3D model can be edited, meshed, repaired and exported.
One step that I found confusing was the texturing step. Usually in 3D scanning of this type, the scanner would occasionally capture some full color frames of the subject from different angles. Then later on these would be projected onto the 3D model, thus applying a color texture to the surface.
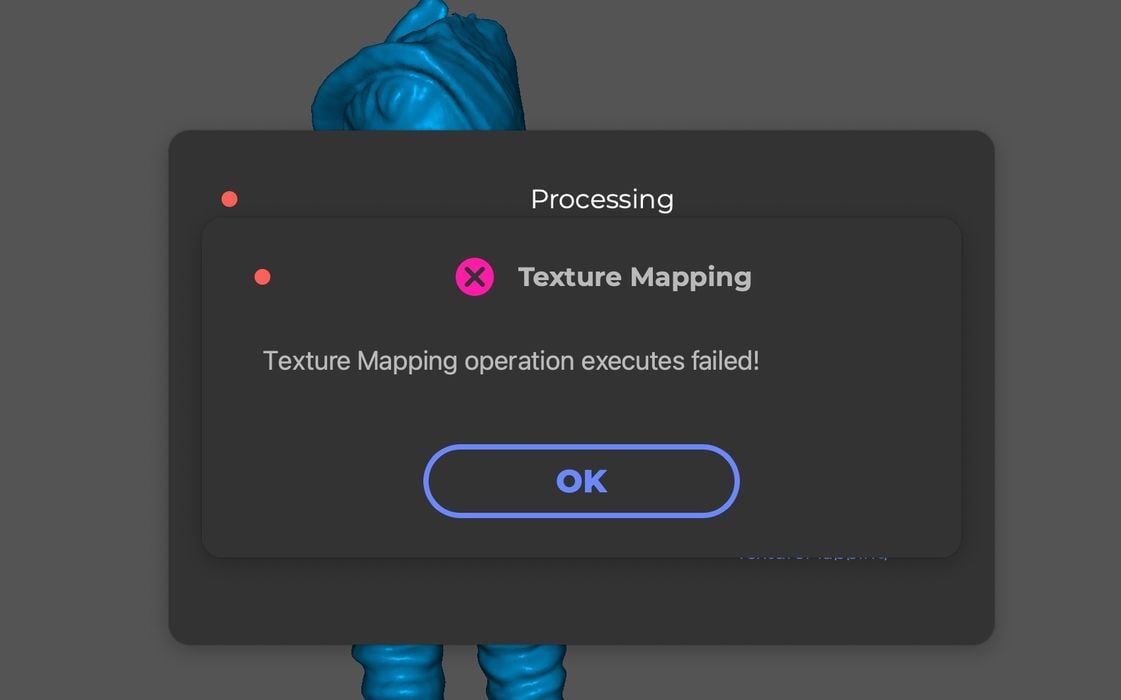
While JMStudio seemed to have a texturing option, I could never get it to work. Later, 3DMakerpro explained that the particular Mole system involved does not do texturing as that is an optional additional feature. This means that the low-cost Mole is not able to capture full color textures, but is excellent for geometry captures.
This is part two of a three part series, please read parts one and three.
Via 3DMakerpro