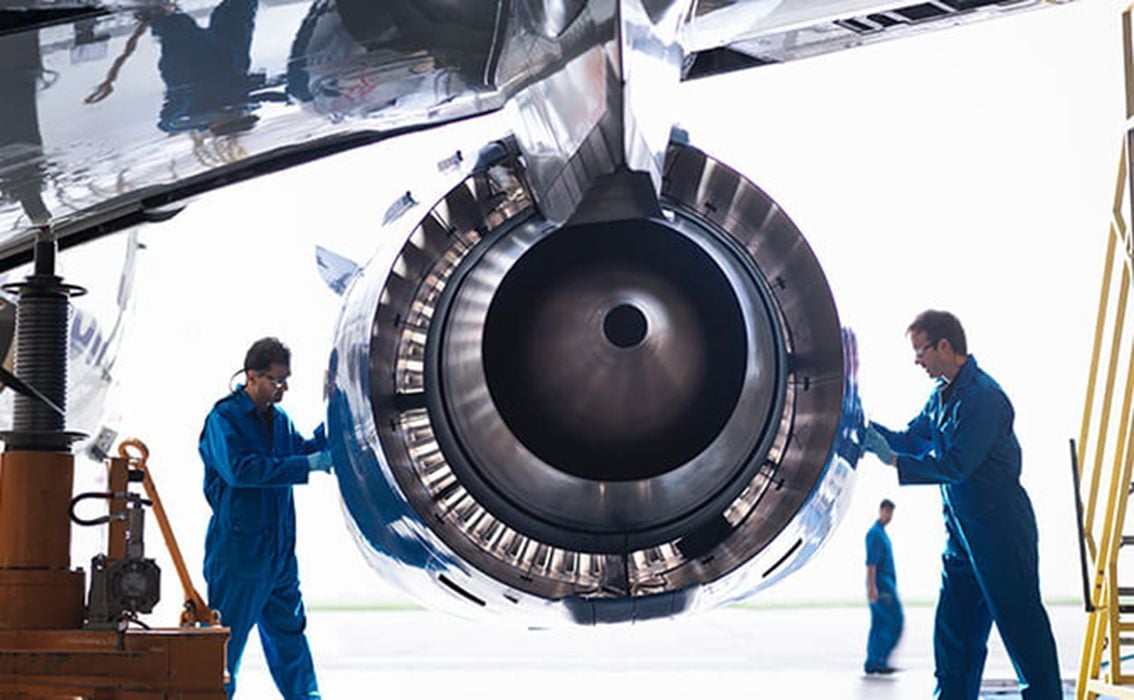
Charles R. Goulding and Preeti Sulibhavi discuss the transformative impact of 3D printing on the aviation Maintenance, Repair, and Overhaul (MRO) industry.
Maintenance, repair and overhaul, or MRO, is the global business segment of maintaining, repairing and operations related to caring for existing aircraft. With the two main original equipment manufacturers (OEMs), airplane manufacturers meaning Airbus and Boeing not able to manufacture the volume needed of new aircraft because of supply chain problems the MRO business is experiencing record sales.Â
Providing quality after-market aircraft replacement parts is a tremendous opportunity for the 3D printing industry.
Need for Genuine Parts
The aircraft component industry is currently in turmoil due to recent instances of counterfeit and defective parts. The aircraft industry needs to ensure that they are providing genuine approved parts.
AOG Technics, a UK company, was recently accused of selling parts with forged certificates and falsified documents. CFM International, a jet-engine manufacturer, whose co-owners are General Electric and Safran, claimed in a British High Court that AOG Technics had been âdeliberate, dishonest and sophisticatedâ in their actions to deceive the market.
In another unfortunate turn of events, in August 2023 Boeing discovered that MAX fuselages built by Spirit AeroSystems (Spirit) had been delivered with improperly drilled holes in the aft pressure bulkhead (the heavy metal dome capping the back end of the passenger cabin that is essential to maintaining cabin pressure).
While not an immediate safety issue, a labor-intensive repair is definitely required for hundreds of MAX airplanes. Boeing CFO, Brian West, has said that because of this, Boeing will revert to a loss position this quarter.
In April 2023, Boeing had found some fittings that attach the MAXâs vertical tail fin were improperly manufactured by a subcontractor to Spirit. That defect cut MAX deliveries to airlines during the peak summer season.
MRO parts are provided by the OEMs and multiple-tier suppliers. The OEMs have ever-increasing 3D printing capabilities.
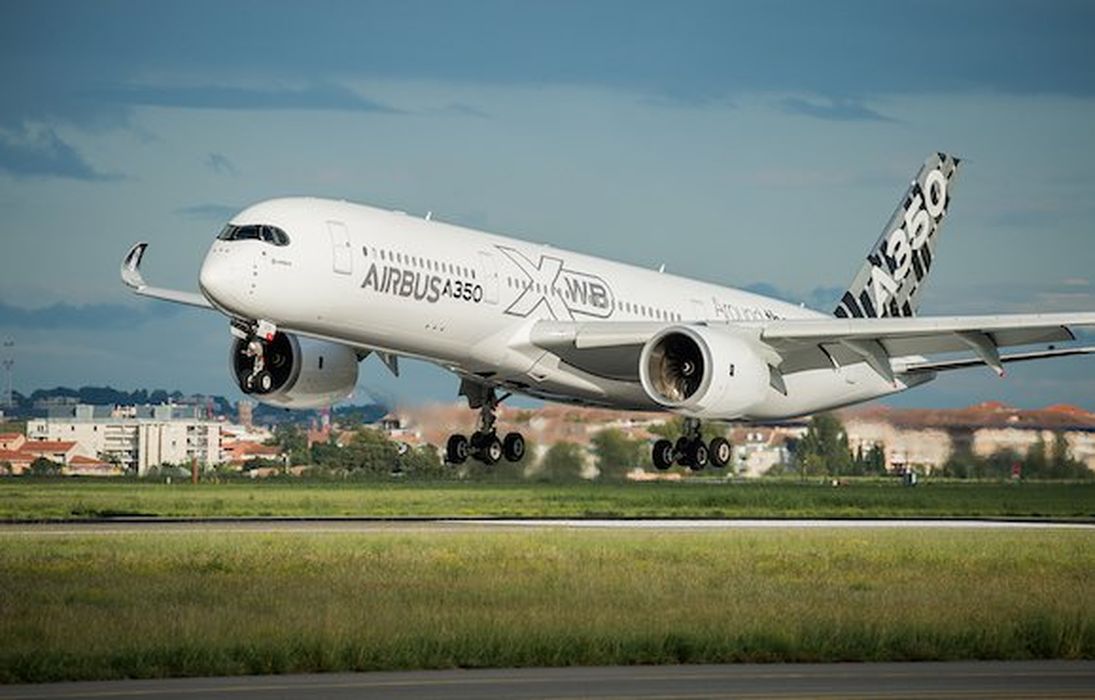
Airbus and Boeing are the largest OEM suppliers with 3D printing experience.
Airbus
Airbus is one of the leaders in aviation that has been integrating 3D printing technology into its products. Airbus is recognized as having over on thousand 3D printed components in the Airbus A350 XWB aircraft.
It has been actively working with Stratasys and Materialise to integrate 3D printed parts into its airline cabins. By using 3D printing, Airbus was able to create bio-inspired panels 15 percent lighter than using conventional production methods. This technology also enables the creation of complex internal support structures, such as lattices inside the panels, without imposing additional manufacturing costs.
Boeing
Boeing is very familiar with utilizing 3D printing technology for aerospace and defense manufacturing capabilities and for fueling further innovation.
Boeing has gone on record stating that 3D printing has lowered lead times and machining time while enabling design enhancements that improve both the efficiency and safety of their parts. 3D printing has help reduce component expenses and has enabled the production of spare parts and replacement parts in the field.
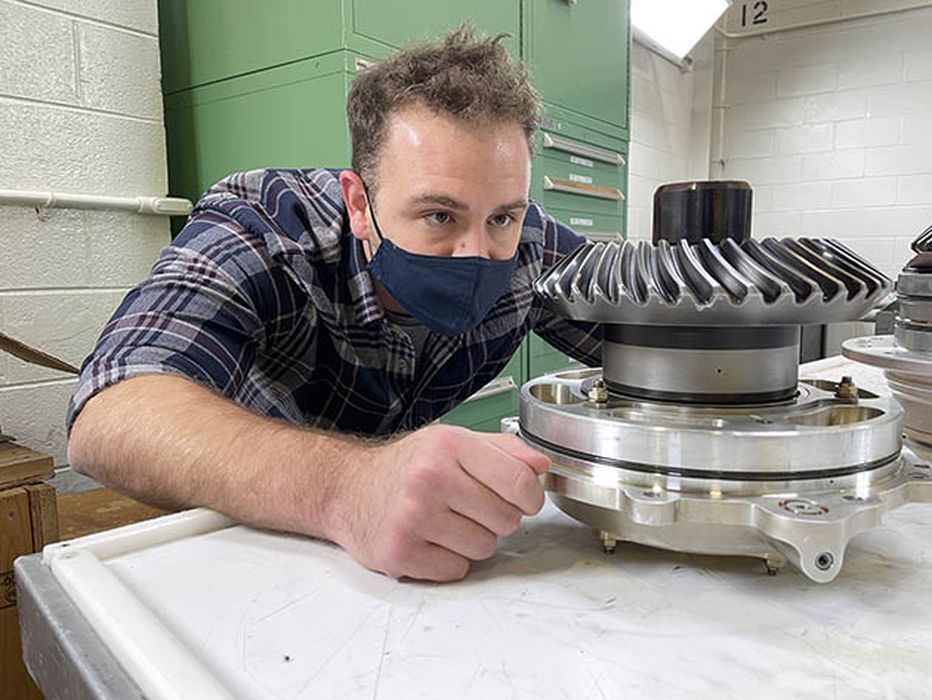
Lockheed System for Quality Parts
Lockheed has a rigorous system to ensure all its external suppliers provide quality parts. This system includes third-party certifications from accredited firms that all parts meet Aerospace Standard (AS) and International Organization for Standardization (ISO) or quality management System (QMS) approvals. If, for any reason, there is a change in standard, Lockheed must be notified in writing 10 days prior. Even manufacturing relocations must be reported to Lockheed.
In 2023, Lockheed produced two large 3D printed titanium domes for a high-pressure tank responsible for holding fuel onboard satellites in orbit. The two domes were created as part of a multi-year development program to create large, high-powered, all-mission capable satellite buses, known as the LM 2100 series.
Rick Ambrose, Executive Vice President of Lockheed Martin Space has stated, âOur largest 3D printed parts to date show weâre committed to a future where we produce satellites twice as fast and at half the cost.â
While the MRO market is dominated by OEMs like Airbus, Boeing, Lockheed, Rolls-Royce, Pratt & Whitney/Raytheon, and GE (as engine parts-makers), there are numerous leading Tier suppliers in the MRO market.
Some of the major non-OEM suppliers with 3D expertise include Heico Corp, Transdigm Group and Lufthansa Group.
Heico Corp
Heico makes the same parts and components as OEMs but at lower cost. Part of this may be attributable to 3D printing. In fact, Victor Mendelson, Founder & CEO of Heico, has said that airlines have âbenefited as a result of having an alternative source of supply both in terms of parts availability and quality and pricing.â
Heico utilizes 3D printers in a few ways. With its Connect Tech capabilities it has an engineering team ready to engage in custom design when âoff-the-shelfâ options do not fit the project. Their manufacturing and testing services include equipment like 3D printers.
The other resource where 3D printers are used is with their 3D PLUS SAS platform. This is a patented technology portfolio that enables stacking heterogeneous active, passive, opto-electronics and MEMS/MOEMS devices in a lightweight, mini package. Thanks to its 3D printers Heico is a global leader in microelectronic products.
Heico is in the process of purchasing Wencor Group for US$2.05 billion to expand its offering of generic aircraft parts.
TransDigm Group
TransDigm is the company responsible for providing airplanes with seatbelt buckles, overhead bin latches, and extruded plastic vents that push the conditioned air into the cabin, in addition to a plethora of valves, pumps, cables and connectors. TransDigmâs product selection also includes lavatory faucets, drain assemblies and door locks. As we have covered, many of these items are great candidates for 3D printing.
A few years ago, TransDigm Group acquired US-based MRO provider, Extant Components Group (Extant). Extant primarily provides various proprietary aftermarket products and MRO services to the aerospace and defense markets. TransDigm should be better positioned to capitalize on MRO growth because of this acquisition.
Lufthansa Group
Lufthansa Technik AG is the MRO unit of the Lufthansa Group that handles MROs as well as the sale of its aviation products and aircraft components to OEMs such as Airbus and Boeing. Lufthansa Technik is using 3D printers for various items in aircrafts including Guide U escape route markings for aircraft interiors. They are photoluminescent (meaning they can glow in the dark in the event of an emergency without electricity) and they are patented and 3D printed.
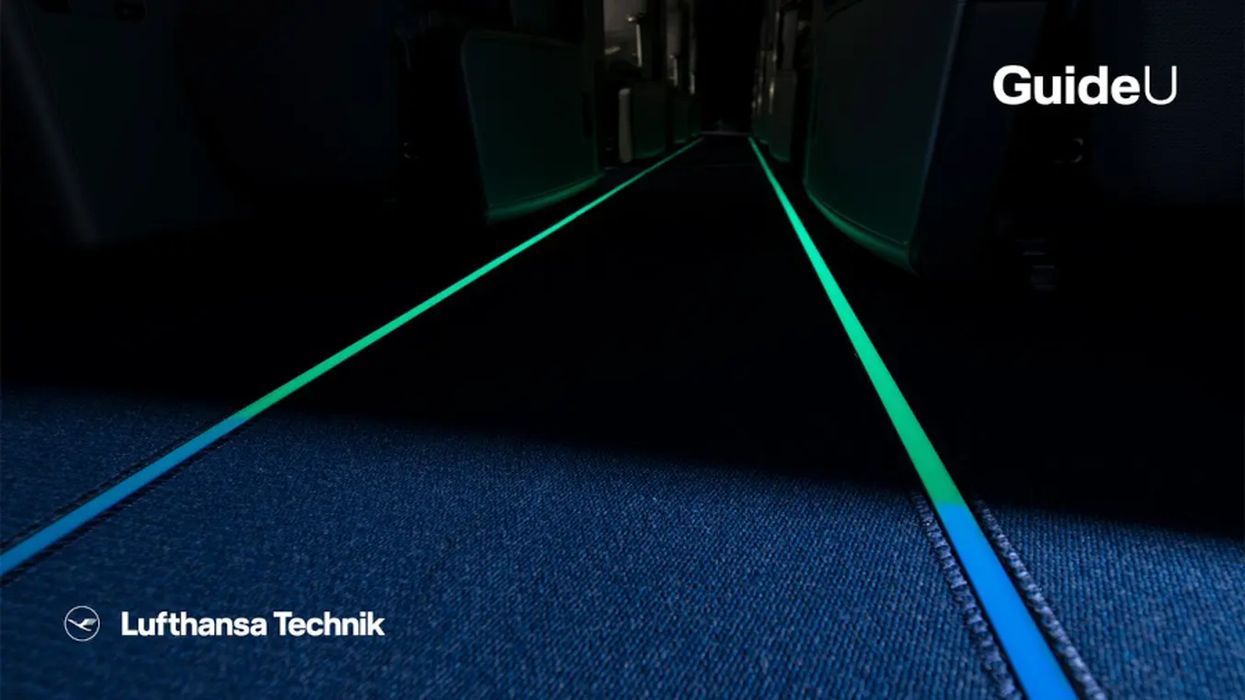
The Research & Development Tax Credit
The now permanent Research and Development (R&D) Tax Credit is available for companies developing new or improved products, processes and/or software.
3D printing innovation can help boost a companyâs R&D Tax Credits. Wages for technical employees creating, testing and revising 3D printed prototypes can be included as a percentage of eligible time spent for the R&D Tax Credit. Similarly, when used as a method of improving a process, time spent integrating 3D printing hardware and software counts as an eligible activity. Lastly, when used for modeling and preproduction, the costs of filaments consumed during the development process may also be recovered.
Whether it is used for creating and testing prototypes or for final production, 3D printing is a great indicator that R&D Credit eligible activities are taking place. Companies implementing this technology at any point should consider taking advantage of R&D Tax Credits.
Conclusion
The high margins in the MRO aftermarket parts business will remind the OEMs how lucrative the aftermarket business is. Likewise, the suppliers will enjoy better margins on proprietary parts than what they obtain from the OEMs. Both enhanced income streams will benefit the 3D printing industry and support further innovation. Â