
Charles R. Goulding, Ryan Donley and Preeti Sulibhavi discuss Nippon Steel’s recent acquisition of U.S. Steel.
Nippon Steel, Japan’s largest steelmaker announced an agreement to acquire a United States steel producer, U.S. Steel, in a US$14 billion deal. The companies will be combining their extensive histories and technological capabilities that will vault the venture into the worldâs second-largest steelmaker. U.S. Steel considered other suitors such as Cleveland-Cliffs, ArcelorMittal, and Nucor but Nippon outbid the domestic steel giants with their US$14 billion cash deal to secure the 122-year-old steelmaker. The transaction will close with U.S. Steel retaining its name, brand, and headquarters in Pittsburgh, PA. The deal is being met with opposition but, U.S. Steel has been falling behind and Nippon brings a plethora of resources and management capabilities that will significantly improve steel production, technology, and overall operations.
U.S. Steel has been at the forefront of innovation in the steel industry with cutting-edge manufacturing capabilities and commitments to energy efficiency that is synchronous with the decarbonization and sustainability goals of Nippon Steel. The commitment and investment to clean energy applications bodes well with the added boost of the Inflation Reduction Act (IRA) incentives that will subsidize the investments made in the especially energy-intensive steel industry.
Steel materials are no strangers to the 3D printing industry. In fact, Army vehicles, like infantry carriers and tanks, have numerous functions that need to be maintained, and a damaged part may leave a vehicle disabled for months waiting for a replacement part. Putting 3D printers in the field to fabricate replacement parts is becoming an increasingly popular workaround.
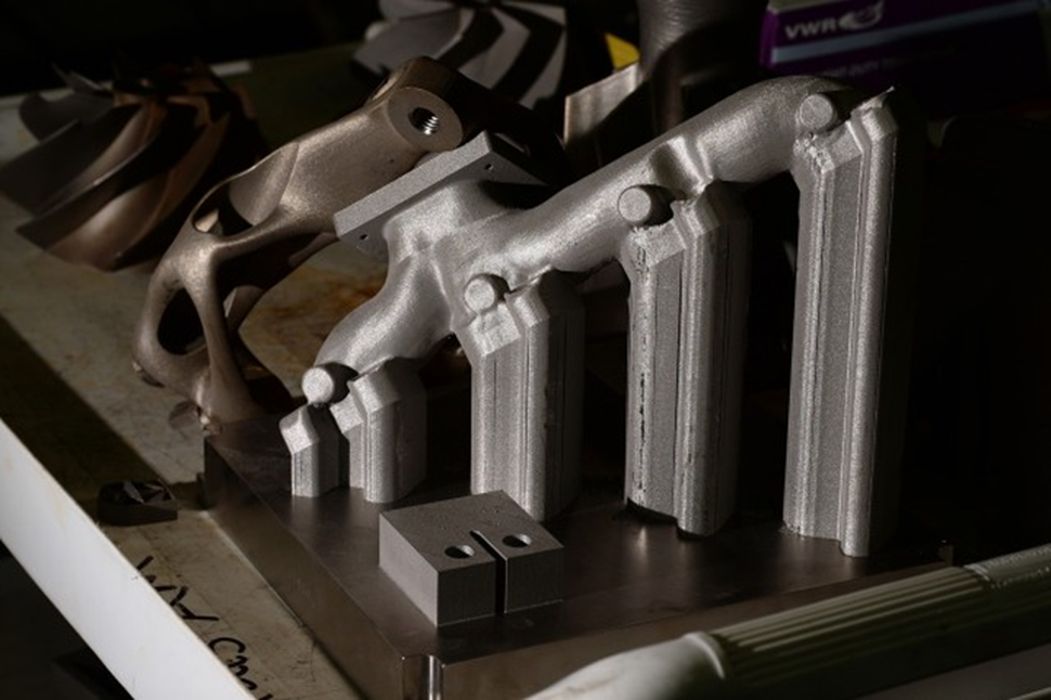
Scientists at the Army Research Laboratory are responding to this by exploring new ways to print durable steel parts on-demand, with feedstock more than 50 percent stronger than whatâs commercially available, said Brandon McWilliams, ARL manufacturing and technology branch team lead.
For McWilliams, the Armyâs 3D printing strategy is twofold: sustainment or how to supply soldiersâ parts for legacy systems, and the ability to print parts for future systems.
In traditional steel manufacturing, the material is âsubtractedâ from a chunk of metal or object. In metal 3D printing it is a process of adding layer upon layer of steel to form an object. Nippon Steel is often one of Japanâs leading patent filers and has an extensive laboratory organization.
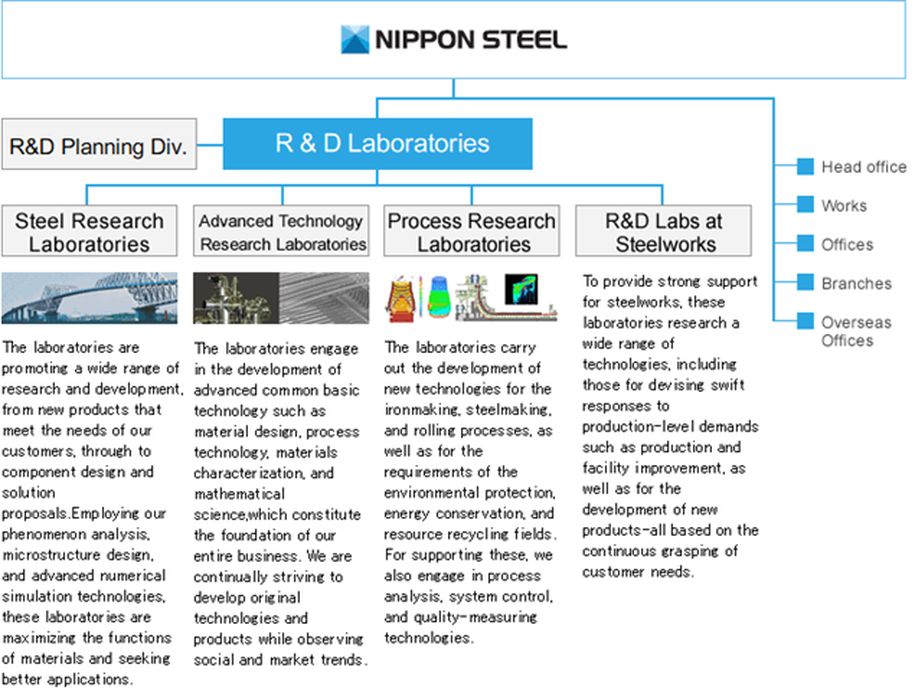
Both U.S. Steel and Nippon bring together highly advanced manufacturing capabilities as they invest and progress their research and development to support the evolution of steel production.
The Research & Development Tax Credit
The now permanent Research and Development (R&D) Tax Credit is available for companies developing new or improved products, processes and/or software.
3D printing can help boost a companyâs R&D Tax Credits. Wages for technical employees creating, testing and revising 3D printed prototypes can be included as a percentage of eligible time spent for the R&D Tax Credit. Similarly, when used as a method of improving a process, time spent integrating 3D printing hardware and software counts as an eligible activity. Lastly, when used for modeling and preproduction, the costs of filaments consumed during the development process may also be recovered.
Whether it is used for creating and testing prototypes or for final production, 3D printing is a great indicator that R&D Credit eligible activities are taking place. Companies implementing this technology at any point should consider taking advantage of R&D Tax Credits.
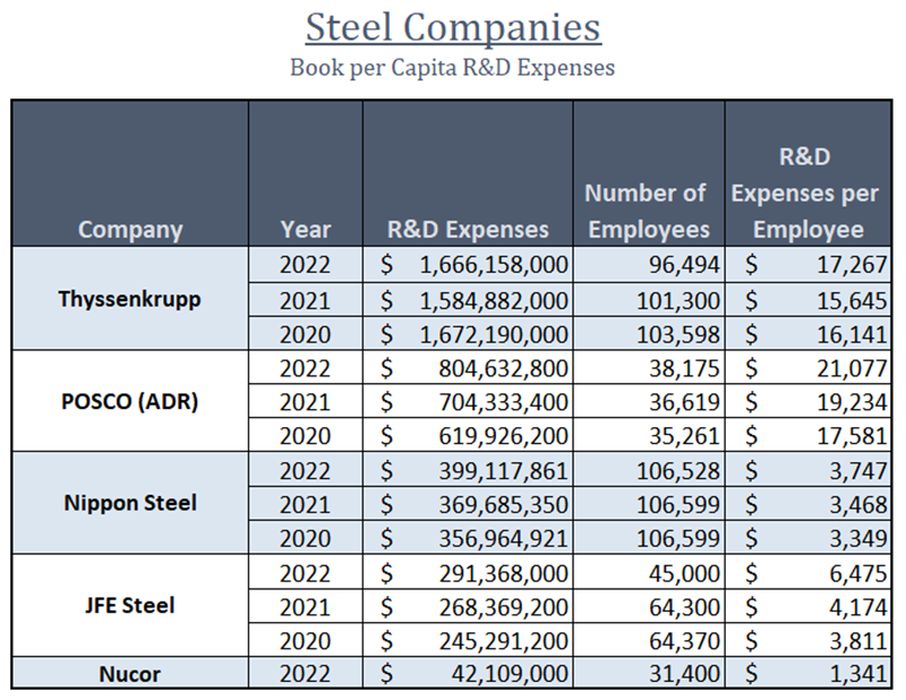
Conclusion
The acquisition of U.S. Steel by Nippon is a tremendous development for the industry. It could advance metal 3D printing innovation as well.